The Digital Construction Awards attracted 170-plus entries this year, 85 of which have been shortlisted. Here, we detail the finalists for the Digital Innovation in Health, Safety and Wellbeing award.
This category recognises the use of digitalisation, digital methodologies and technologies to enhance health, safety and wellbeing among workers on construction projects.
Six entries made the shortlist.
Countess of Chester Hospital | Dalkia Engineering/Hilti Corporation
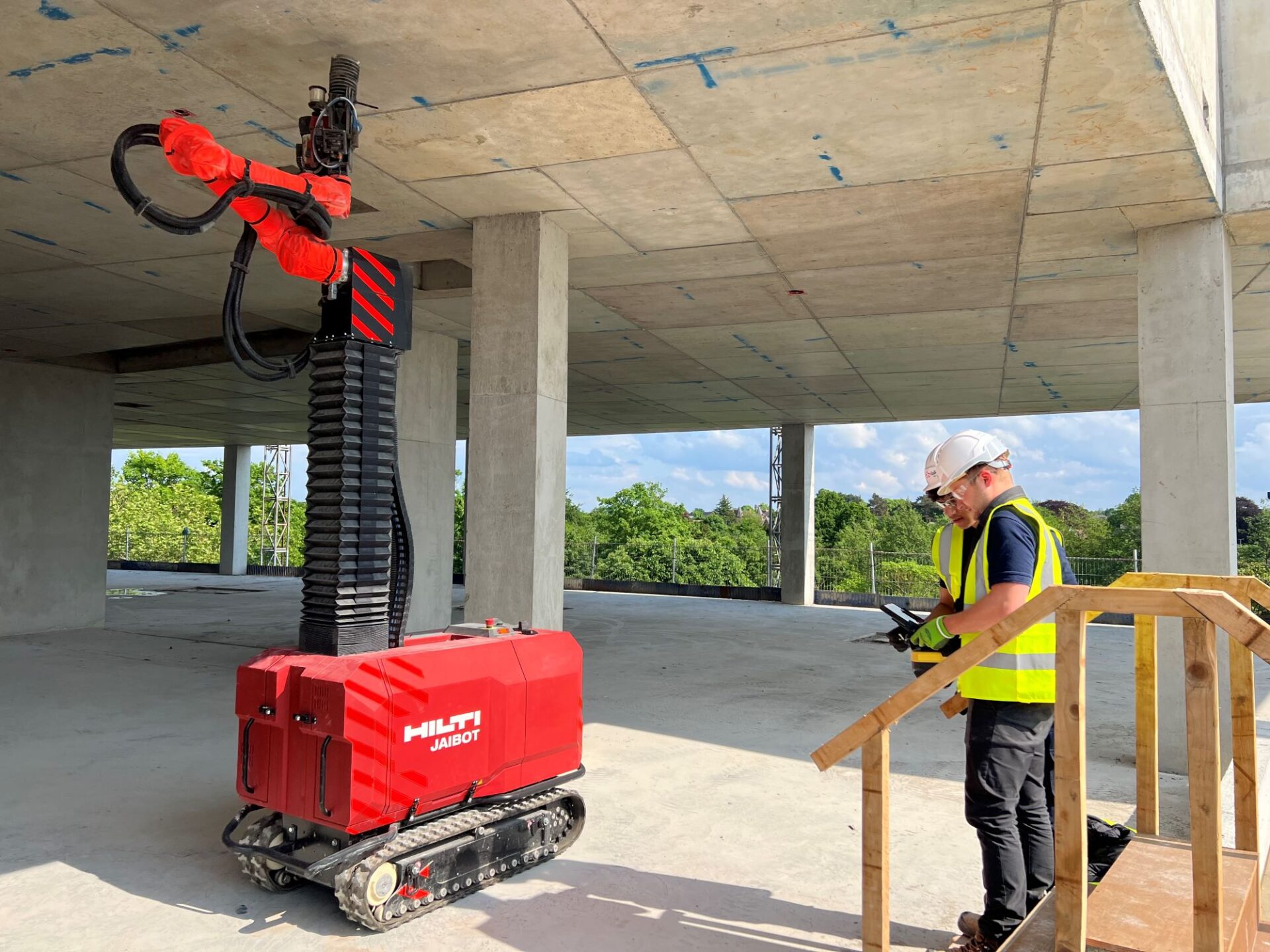
Faced with the complex demands of a largescale MEP installation at the Countess of Chester Hospital, Dalkia Engineering sought to overcome the inefficiencies and safety risks of traditional drilling and setting out methods. Working under a tight programme and near live hospital wards, the company identified automation as key to minimising disruption, enhancing accuracy and improving worker safety.
Following rigorous evaluation by its in-house digital engineering team, Dalkia adopted the Hilti Jaibot – a robotic drilling system that integrates directly with BIM. The Jaibot automates drilling based on pre-modelled fixing locations, eliminating human error and drastically reducing manual handling and work at height.
The solution was implemented in collaboration with main contractor Integrated Health Projects (IHP), a joint venture between Vinci Building and Sir Robert McAlpine, and supported by Hilti’s technical team to ensure seamless deployment.
The results were transformative. Drilling time was reduced by 40%, rework fell by 95%, and costs dropped by 20% compared to traditional methods. Safety was markedly improved: Jaibot’s operation reduced exposure to dust and vibration, and eliminated risky manual tasks. The cleaner, quieter process also benefited patient wellbeing during nearby live operations. Dalkia achieved a 100% safety score for its installation, and the approach has since been rolled out across its UK business.
The project exemplifies how digital construction methods can deliver measurable gains in productivity, safety and sustainability.
Electricity Transmission Substation site visits | AtkinsRéalis
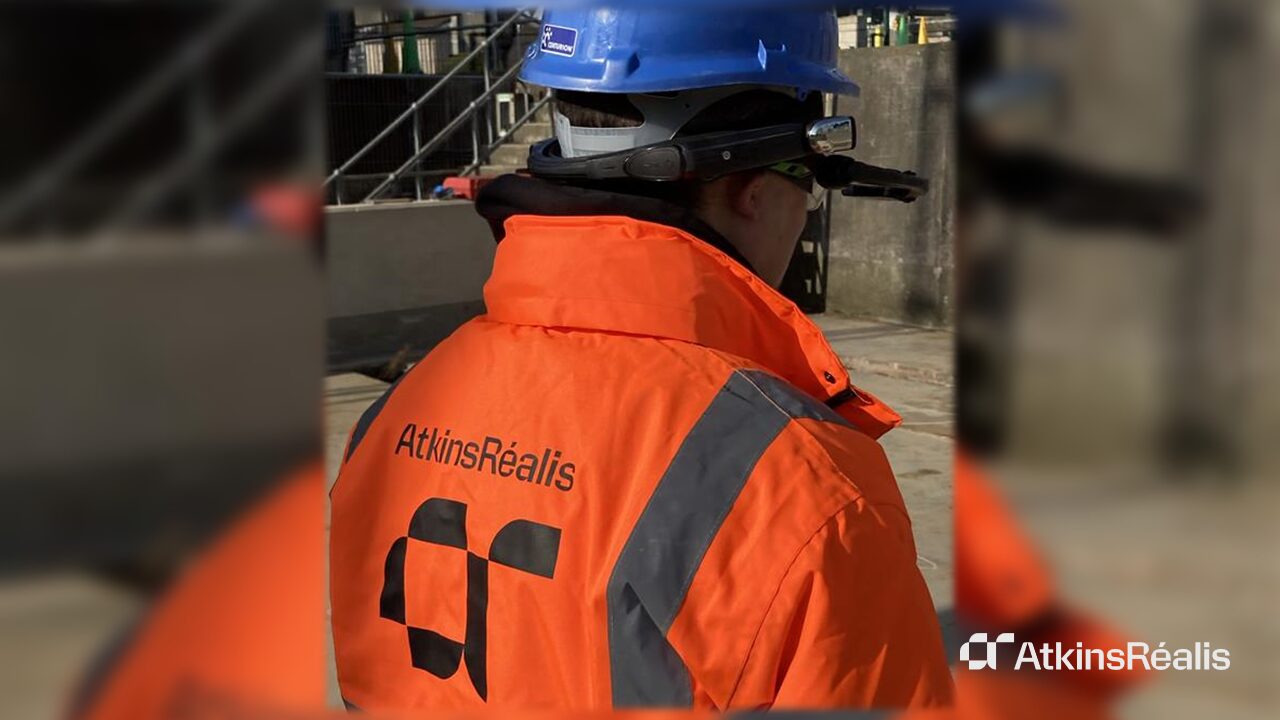
As part of its work on UK electricity transmission infrastructure, AtkinsRéalis identified significant health, safety and efficiency challenges in traditional substation site visits. These included the risk of exposure to live electrical environments, extensive travel for subject-matter experts, and limited ability for international colleagues and stakeholders to understand site conditions via static 2D drawings.
To address these challenges, AtkinsRéalis deployed two digital tools: the GoPro MAX 360-degree camera, and RealWear Navigator assisted reality headsets. The GoPro enabled hands-free, full-site visual capture, creating ‘virtual site’ walkthroughs. These were embedded into the company’s CIRRUSinsite geospatial platform, allowing users to navigate site footage via map coordinates, reducing the need for return visits and providing context for hard-to-interpret 1960s drawings.
The RealWear headsets provided live, first-person site visits via Microsoft Teams, enabling subject matter experts and global colleagues to participate remotely, give real-time input, and eliminate the need for travel or overnight stays.
Combined, the tools reduced the number of people physically on site, improving safety while increasing productivity.
The impact has been substantial. In 2024 alone, AtkinsRéalis recorded savings of approximately 45,000kg of carbon, 3,000 working hours and £185,000 in costs on electricity transmission project delivery. Teams now host virtual walk-downs to brief stakeholders and accelerate design understanding. Graduate engineers are empowered as ‘digital champions’, optimising data capture and expanding digital delivery culture.
By adopting cross-sector tools and applying them innovatively to high-risk, geographically dispersed infrastructure work, AtkinsRéalis has transformed its approach to substation design and delivery.
T2 Baggage Programme | Heathrow/Aecom
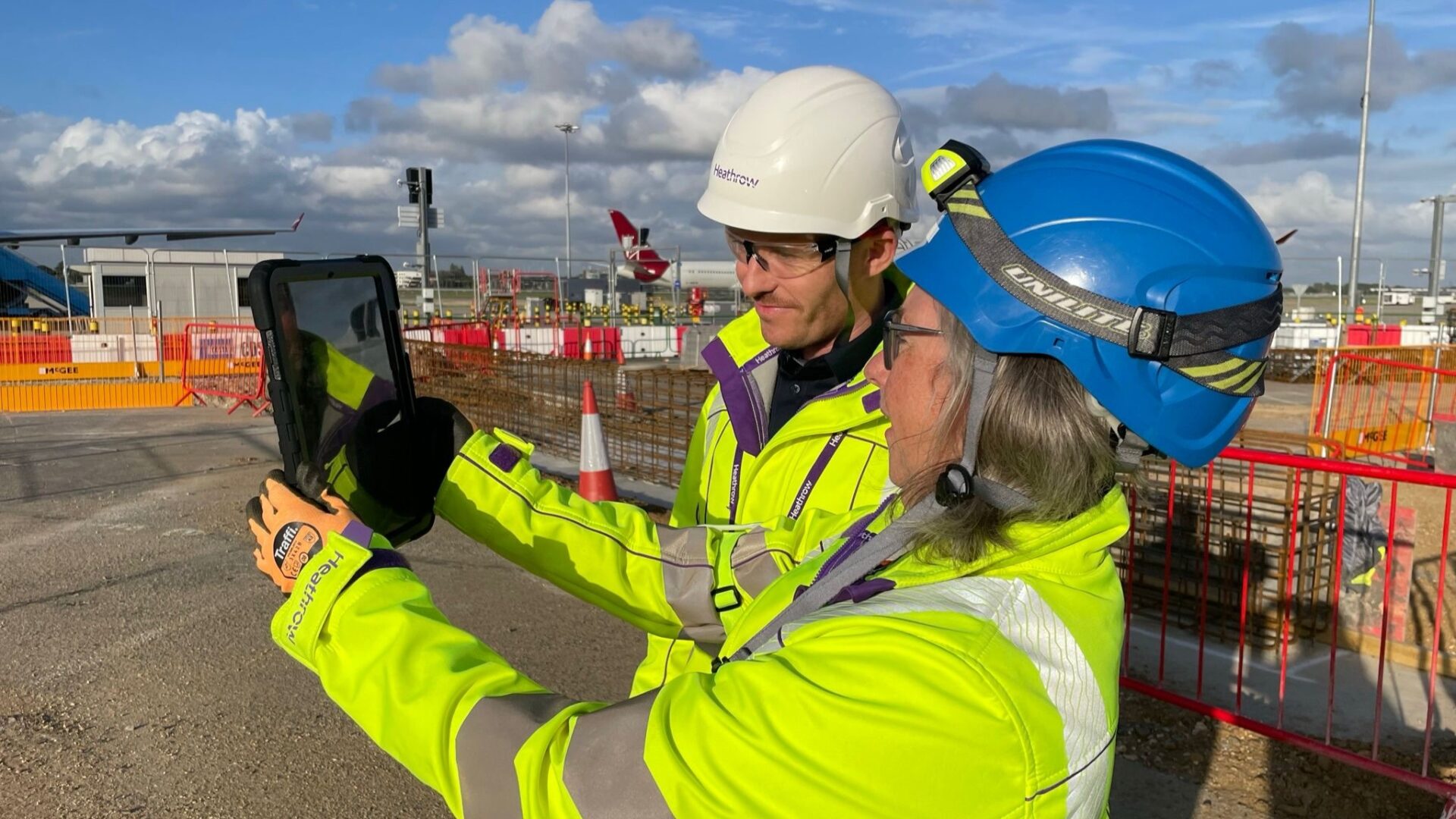
At Heathrow Airport, the Terminal 2 Baggage Programme (T2BP) presented a complex design and safety challenge: coordinating 21 interlinked projects across multiple design organisations, all operating in a live airport environment. The traditional approach – managing design risks via disparate Excel sheets – proved inefficient and error-prone.
Aecom, in partnership with Heathrow and software provider Gamma AR, pioneered a digital safety-in-design methodology using Autodesk Construction Cloud, supported by Power BI dashboards and integrated 3D BIM models. This innovation replaced manual risk registers with a standardised, live digital platform. Design risks are now geolocated within federated 3D models and accessible in real-time, including via augmented reality tools on site.
The system streamlines compliance with CDM 2015 regulations and aligns with PAS 1192:6. It enables real-time collaboration between designers, contractors, and stakeholders, improving design engagement, buildability, and health and safety outcomes.
Statistically, the benefits are significant. During RIBA Stage 4, the platform helped eliminate 40 risks through design, with only 25 risks remaining for the construction phase, and 44 risks assigned to long-term operational use to support the future health and safety file.
The solution has been mandated by Heathrow across all capital programmes and adopted by Aecom globally. It represents a major shift from reactive to proactive health and safety design practices, driving digital transformation across infrastructure delivery.
Laing O’Rourke e-RAMS
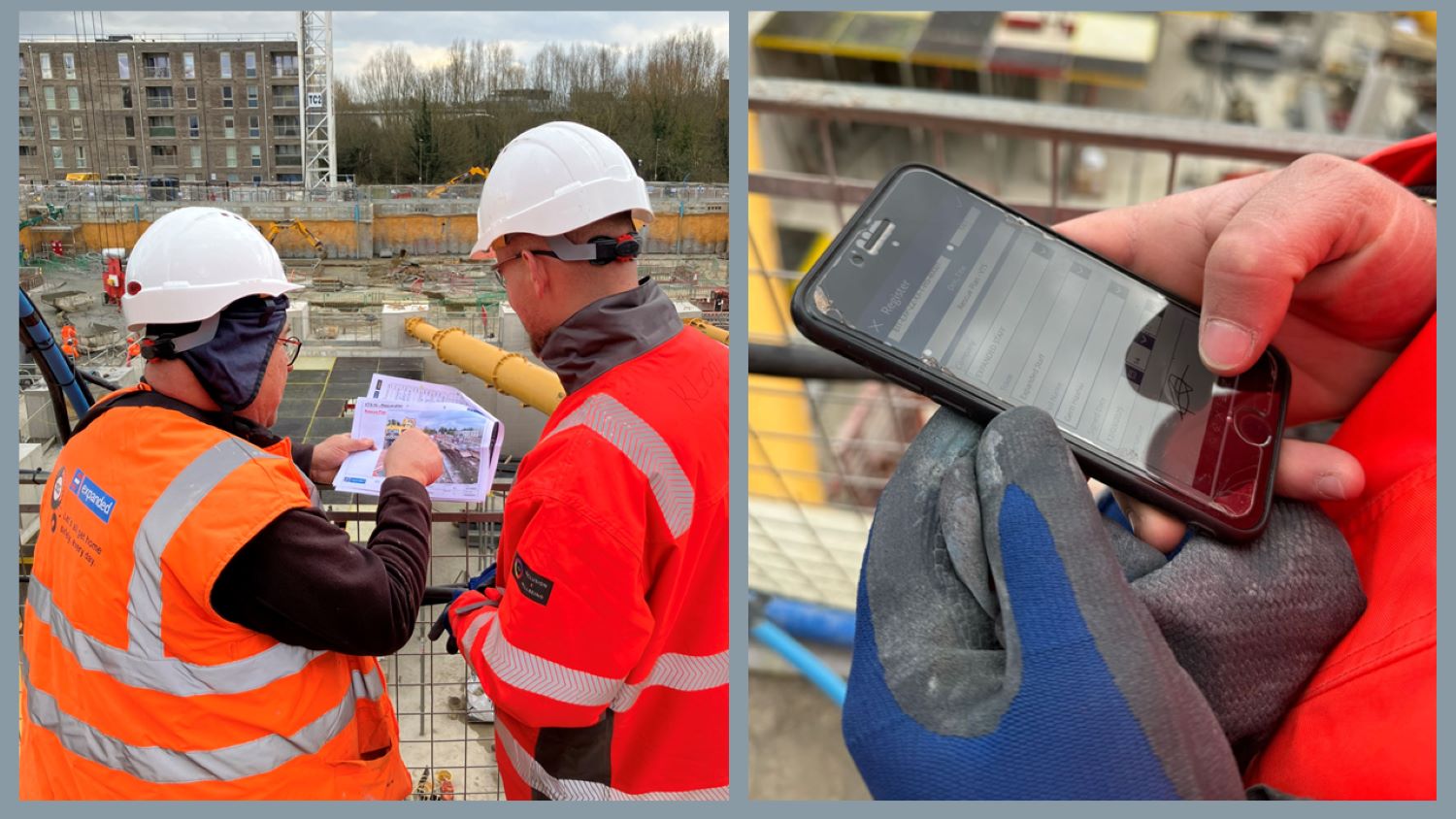
Laing O’Rourke, along with its subsidiaries Expanded Structures, Expanded Geotechnical, Crown House Technologies and Vetter, has transformed RAMS (Risk Assessment Method Statement) compliance with its bespoke e-RAMS solution.
Developed in-house using Microsoft Power Apps and integrated with Asite, Azure SQL and Power BI, the system replaces inefficient, paper-based processes with an automated, cloud-based platform that ensures real-time visibility of worker briefings and compliance data.
Traditional RAMS systems suffered from poor revision control, fragmented records and time-consuming audits. The e-RAMS solution eliminates these issues by providing live updates, digital acknowledgements and a visual traffic-light system to identify compliance gaps. Workers are automatically added to the RAMS matrix via turnstile entry, and site managers can instantly verify briefing status, even overcoming language barriers through visual cues.
Deployed in February 2024 across a project with 800 personnel, e-RAMS cut administrative time for site managers by more than 80%, saving eight hours weekly or 416 hours annually, which equates to £16,640 saved per site over a year. Audit durations dropped from three days to half a day, saving £5,000 per audit. Staffing requirements for compliance monitoring were reduced by 60%. Workforce briefing accuracy rose from 75% to 98%. Safety non-compliance incidents decreased by 30%. Data errors fell by 85%.
The flexibility and low-code architecture of e-RAMS make it scalable across future projects, enabling continuous improvement without costly redevelopment. Built with end-user input from across the supply chain, the tool is practical, robust and already reshaping safety culture across Laing O’Rourke sites.
Moata Safe by Design | Mott MacDonald
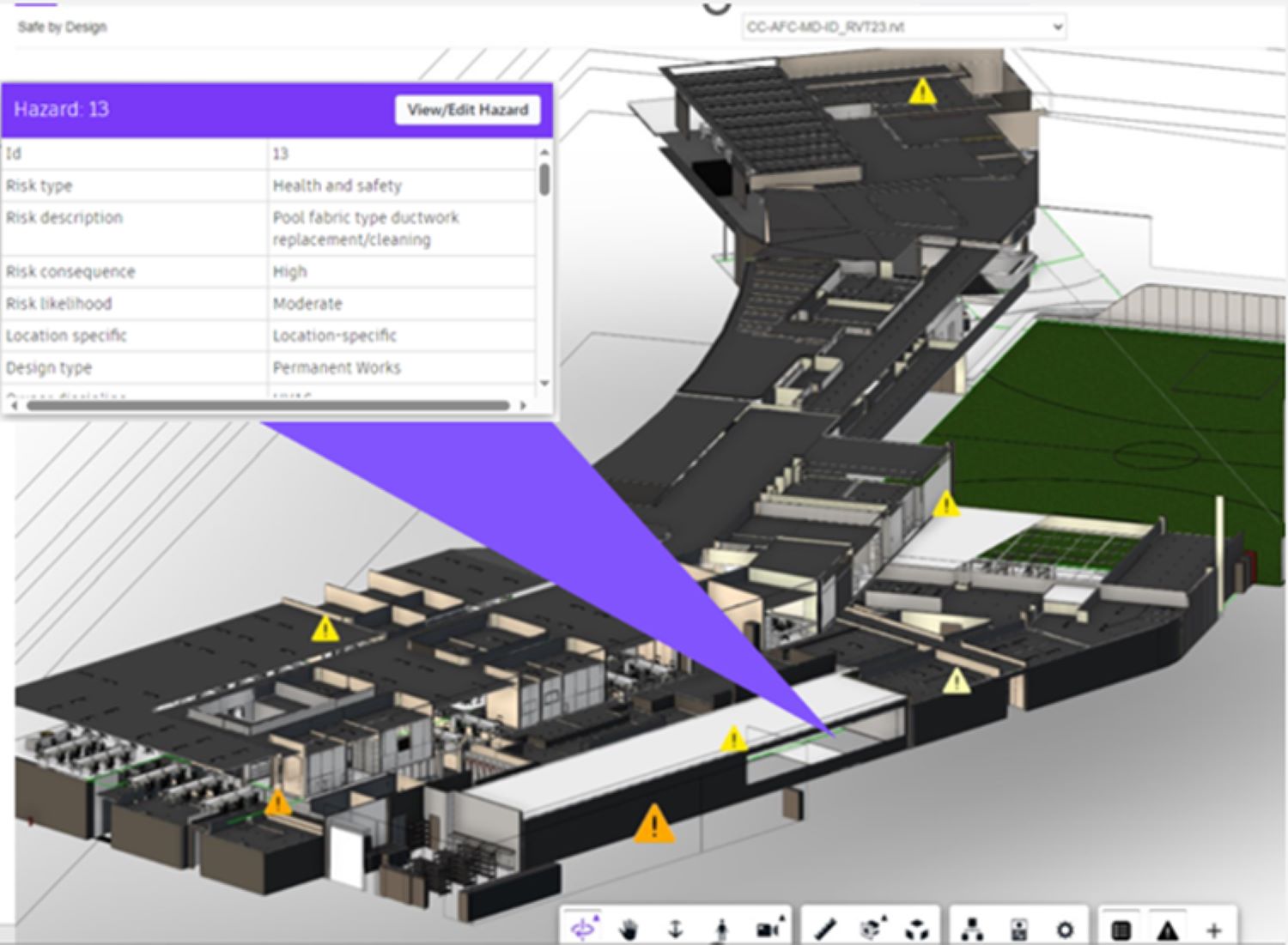
Mott MacDonald developed Moata Safe by Design (MSbD) to address a global health and safety challenge: how to ensure hazard elimination and knowledge sharing across 2,000+ projects in 150 countries. Traditional tools, like Excel-based design risk registers, were siloed, inconsistent and inefficient. MSbD replaces these with a geo-spatial, 3D model-integrated digital platform that facilitates proactive hazard management throughout a project’s lifecycle.
MSbD incorporates live integration with platforms such as Autodesk Construction Cloud and iTwin, enabling real-time model visualisation and location-specific hazard tagging. Its AI-powered Risk Assist Tool uses historical project data to predict design risks and suggest mitigations, supporting early-stage design decisions. Crucially, AI recommendations are subject to human validation, ensuring rigour and accountability.
A key differentiator is the platform’s ability to harmonise terminology using Uniclass coding, enabling international consistency while allowing region-specific outputs. It has been piloted on live projects since July 2024, with positive client feedback and strong user adoption thanks to streamlined workflows.
The system offers full auditability, project-specific dashboards and a portfolio view. This has transformed risk visibility, improved compliance and reduced design-related incidents. Knowledge is no longer siloed – designers can instantly see how peers worldwide addressed similar risks, from bridges in the UK to aqueducts in Bangkok. MSbD boosts quality, reduces rework, enhances legal compliance and, ultimately, helps save lives across global infrastructure projects.
Signal Operator Rostering System | Flannery Plant
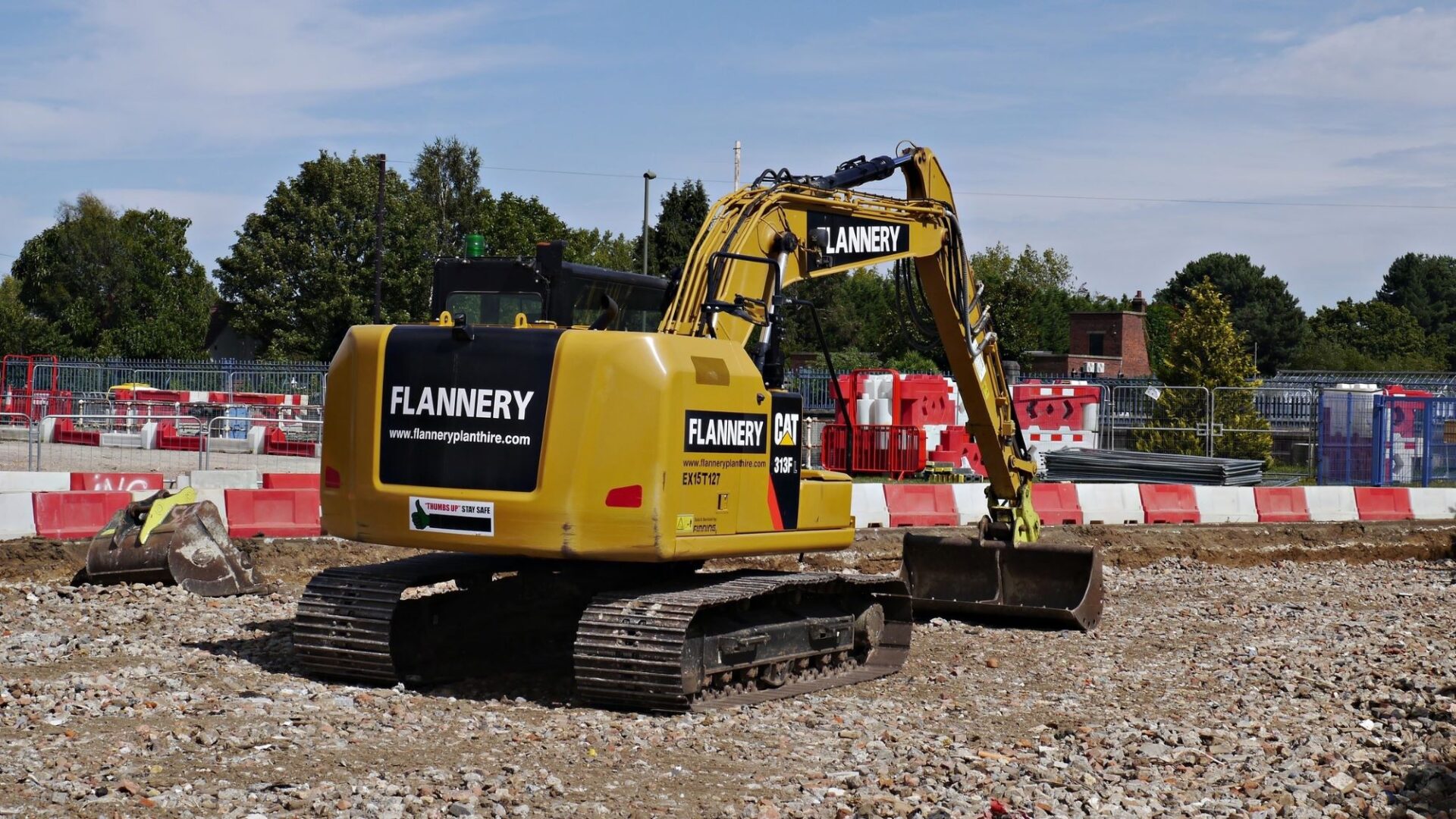
Plant hirer Flannery has transformed workforce management in the construction industry with the roll-out of its Signal Operator Rostering System, a digital platform that automates compliance, fatigue monitoring and operator scheduling. Developed in collaboration with Signal Software and piloted on BAM UK’s Environment Agency Incident Response projects, the system integrates in real-time with the NOCN database via a live API, ensuring only accredited plant operators are rostered.
The challenge for Flannery was managing a large operator workforce and fleet safely and efficiently across multiple sites, while navigating complex compliance demands. Manual processes had proven vulnerable to human error, inefficiencies and risks. A strategic R&D process followed – including workflow mapping, stakeholder consultation, and technical scoping – to create a bespoke solution for the sector.
Key features include automated fatigue tracking using real-time working hours, digital timesheets, and machinery assignment tools, all accessible via a mobile interface. The system also offers machine usage tracking and automated maintenance logging.
The benefits are already evident. Rostering accuracy and certification compliance have improved significantly, administrative workload has been cut by 30%, and safety incidents have reduced by 15%. Transparent compliance reporting has improved client relationships and enabled more effective audits.
Despite initial resistance and integration challenges, targeted training and iterative updates ensured successful adoption. The system is now mandated across all of BAM’s northern projects, with potential for wider industry uptake.
The platform marks a step-change in digital safety and workforce management, enhancing collaboration and delivering scalable, measurable improvements across the construction sector.
Celebrate with the best
The winners will be revealed at the gala dinner on 1 July at the Brewery in London.
You can join the shortlisted entrants by booking your seats at the awards.
The Digital Construction Awards are organised by Digital Construction Week, Construction Management and the Chartered Institute of Building. The first sponsor to be announced is Bluebeam.
To find out more about the Awards, visit digitalconstructionawards.co.uk.
Generative artificial intelligence was used to help with the creation of this article. All content in the article was sourced, checked and verified by our editorial team before publication.