The Digital Construction Awards attracted over 170 entries this year, 85 of which have been shortlisted. Here, we detail the finalists for the Digital Innovation in Productivity award.
This category recognises the use of digitalisation, digital methodologies and/or technologies to enhance the productivity of construction workers on a project or projects.
Seven entries have made the shortlist.
Electricity Transmission Substation Site Visits | AtkinsRéalis
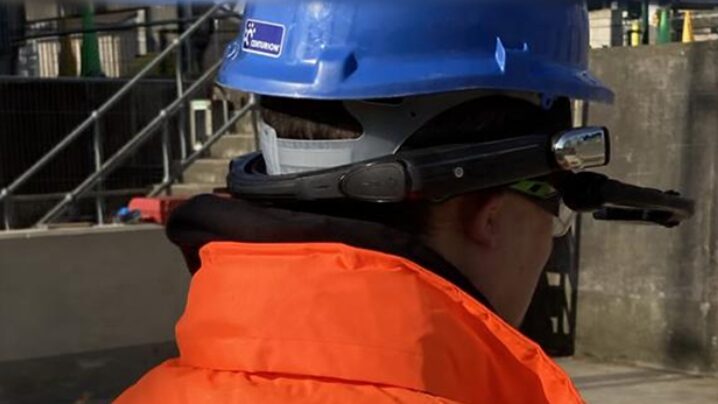
Significant volumes of substations and network upgrades are required to achieve net-zero targets efficiently and cost-effectively. AtkinsRéalis’s design process involves visiting substations to gather onsite details to develop appropriate solutions.
However, this approach comes with several challenges, including health and safety considerations around electrical risks of substations, remote locations requiring overnight stays, difficulties in interpreting 1960s hand-drawn as-built drawings, and discussions with stakeholders who have never visited the site, among other issues.
To overcome these obstacles, AtkinsRéalis identified two technologies, namely the GoPro MAX camera, which captures 360-degree photos and videos, and the RealWear Navigator assisted reality headset.
During previous site visits, teams captured photographs and videos using mobile phones, creating large datasets that lacked broader context, including only specific site sections within each frame, making them hard to refer to later.
AtkinsRéalis trialled GoPro MAX on standard substation visits. One person attached the camera to their helmet for hands-free data capture, allowing them to focus on the visit and hazards. Initial users were substation engineering SMEs, which had to prioritise site engineering assessments, rather than optimally capturing suitable footage.
While 360-degree footage creates valuable ‘virtual sites’, it prevents live contributions from those not on site. This is where RealWear Navigator enables livestreams from the wearer’s perspective to Microsoft Teams, allowing many to attend the site virtually, and all participants can discuss with each other while referring to the livestreams.
The deployment of this digital technology has improved the way projects are delivered and created new methods of communicating and optimising design development.
innDex and FM Conway
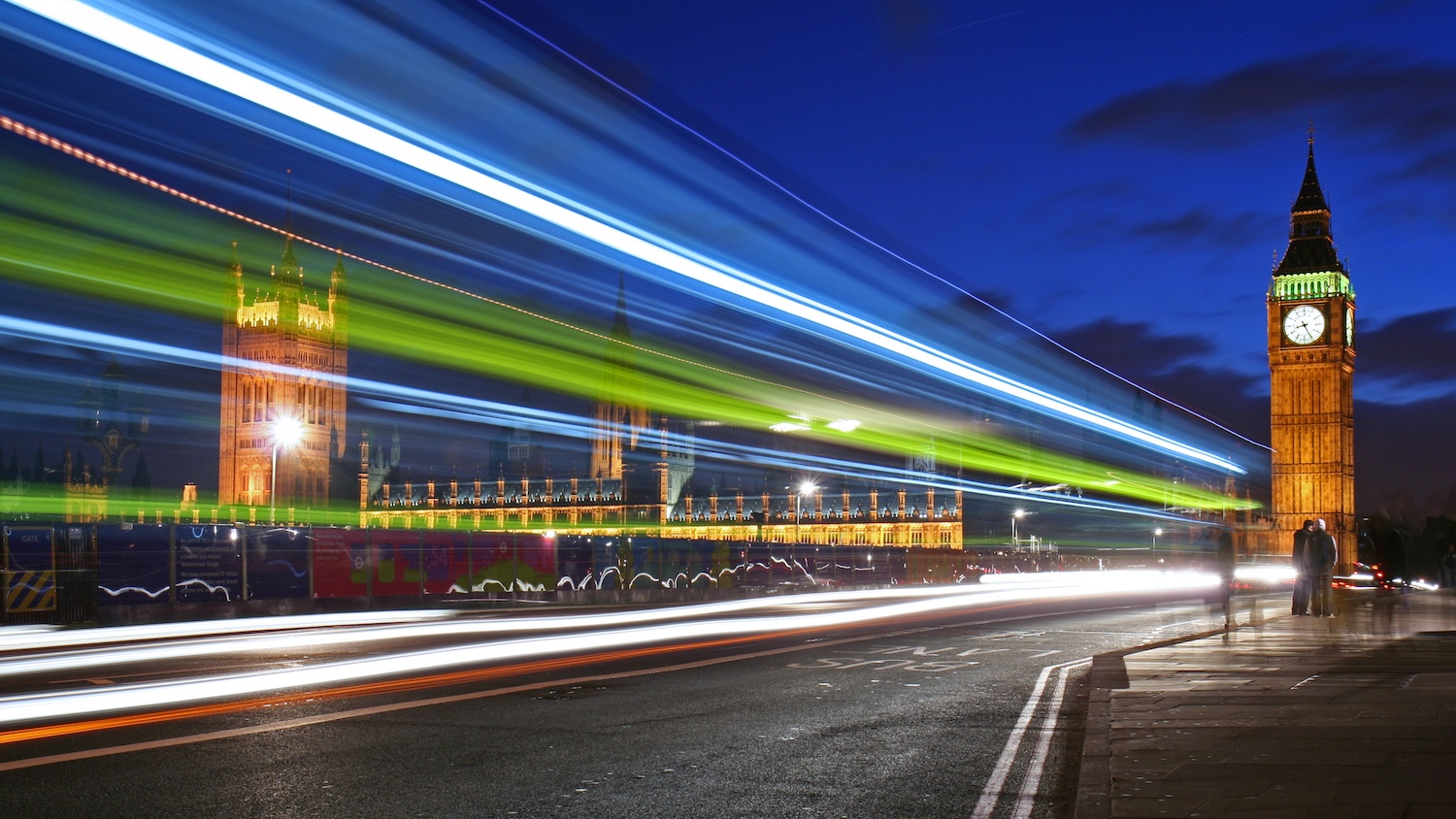
FM Conway and innDex have revolutionised digital asset management on Westminster City Council’s multi-million pound bridges and highway structures programme, an ambitious framework running until 2026. Covering numerous ageing assets, the programme required innovative solutions to address legacy systems, fragmented documentation, and safety bottlenecks, particularly with site inductions, inspections, and permit workflows.
Faced with inefficiencies and compliance risks, FM Conway partnered with innDex to develop a comprehensive digital platform. The digital inductions tool alone has slashed onboarding time by 83%, saving more than £6,000 in paperwork and allowing workers to complete safety protocols en route to site. Daily briefings, toolbox talks and progress updates are now managed through the innDex app, improving clarity and cutting site delays by around 15 hours per week.
The suite also includes an inspection tool that tracks asset conditions using environmental data and route-mapping, while a centralised permits system ensures real-time approvals and role-specific compliance. Fleet and equipment checks are automated to enhance reliability and cut carbon emissions. FM Conway is now piloting camera analytics to optimise maintenance schedules by tracking asset usage.
A single digital hub consolidates workforce training records, timesheets and site access logs, allowing real-time monitoring and transparent audit trails. With more than 147,000 photos logged, visual documentation strengthens accountability and supports proactive maintenance.
The platform has not only improved safety, efficiency and sustainability across multiple sites, but provided Westminster City Council with enhanced oversight, futureproofing long-term asset management across the borough.
National Rehabilitation Centre | IHP (Vinci Building/Sir Robert McAlpine)/Buildots
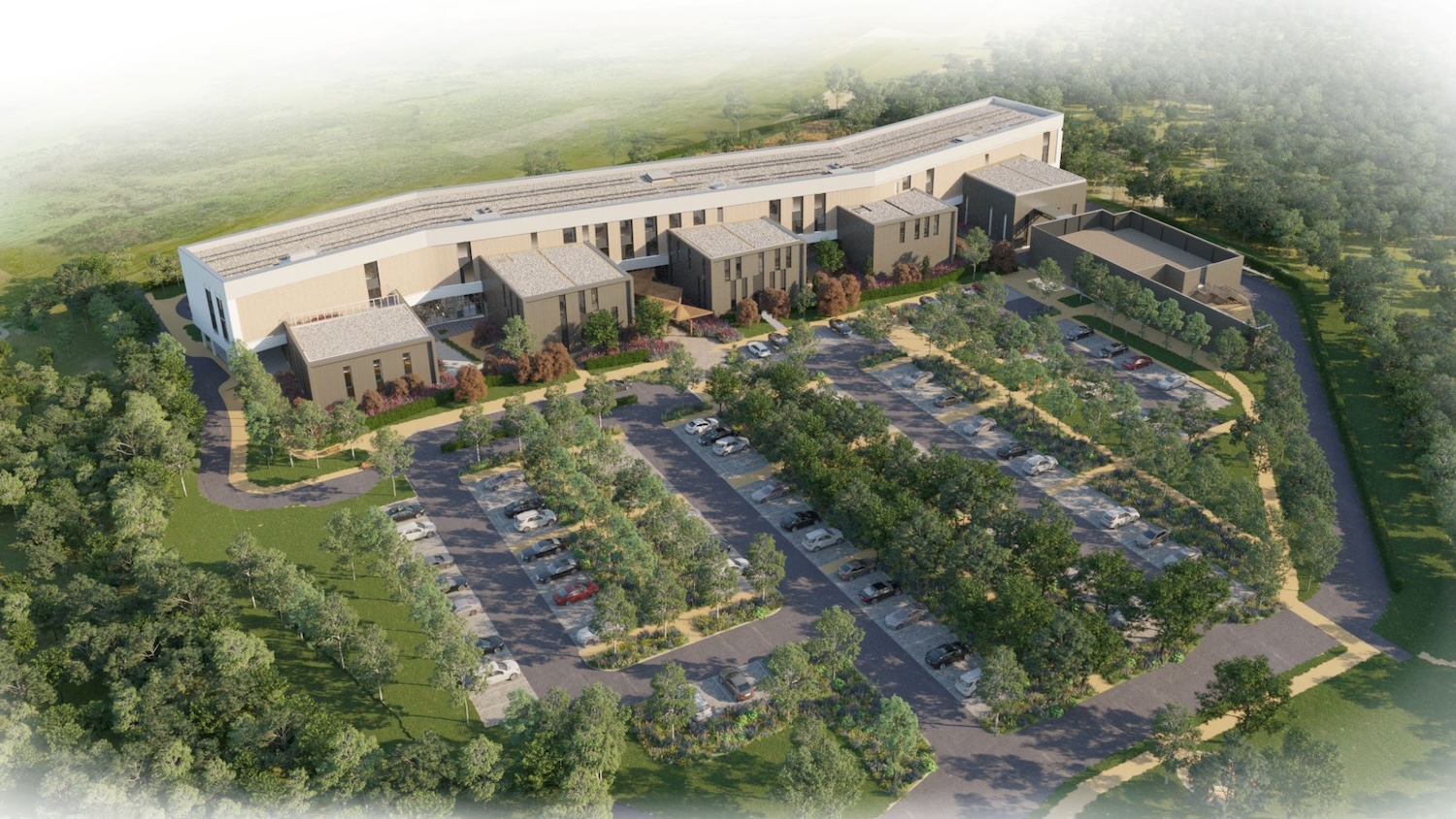
The National Rehabilitation Centre (NRC) project is a landmark initiative being designed and constructed by Integrated Health Projects (IHP), the Sir Robert McAlpine (SRM) and Vinci Buildings JV, for Nottingham University Hospitals NHS Trust. With a £105m investment, this ambitious project is set to deliver a state-of-the-art, energy-efficient facility with 70 beds, as part of the government’s New Hospital Programme later this year.
Traditional construction management often faces inefficiencies, causing budget overruns and missed deadlines. In contrast, the NRC project is distinguished by a digital solution that enabled simultaneous progress monitoring, delay prediction and workforce planning. This approach not only facilitated collaborative decision-making with the supply chain, it also ensured a seamless fit-out sequence.
By tracking workforce numbers on site using biometric turnstile data from Datascope and integrating it with AI-powered progress tracking and delay predictions from Buildots, the digital solution allowed the NRC project team to identify the root causes of bottlenecks through continuous review of past performance. It also accelerated activities by making proactive workforce adjustments, preventing cascading schedule impacts.
To enhance the administration of lookahead planning and thereby improve the efficiency of the process, AI-powered assistants were used to automatically capture key issues and actions in daily logs.
For example, Microsoft Copilot was used to automatically interpret discussions, generate action lists and assign responsibilities, ensuring that no actions, commitments or discussions were overlooked. These changes led to a 75% reduction in time spent on administrative tasks, amounting to six to eight hours per week.
This approach not only enabled the NRC project to mitigate five weeks of potential delays, thereby preventing losses exceeding £1m, but also established a new standard for data-driven construction planning.
Prefabricated partitions on high-rise residential projects | KOPE AI/Saint-Gobain Intewall
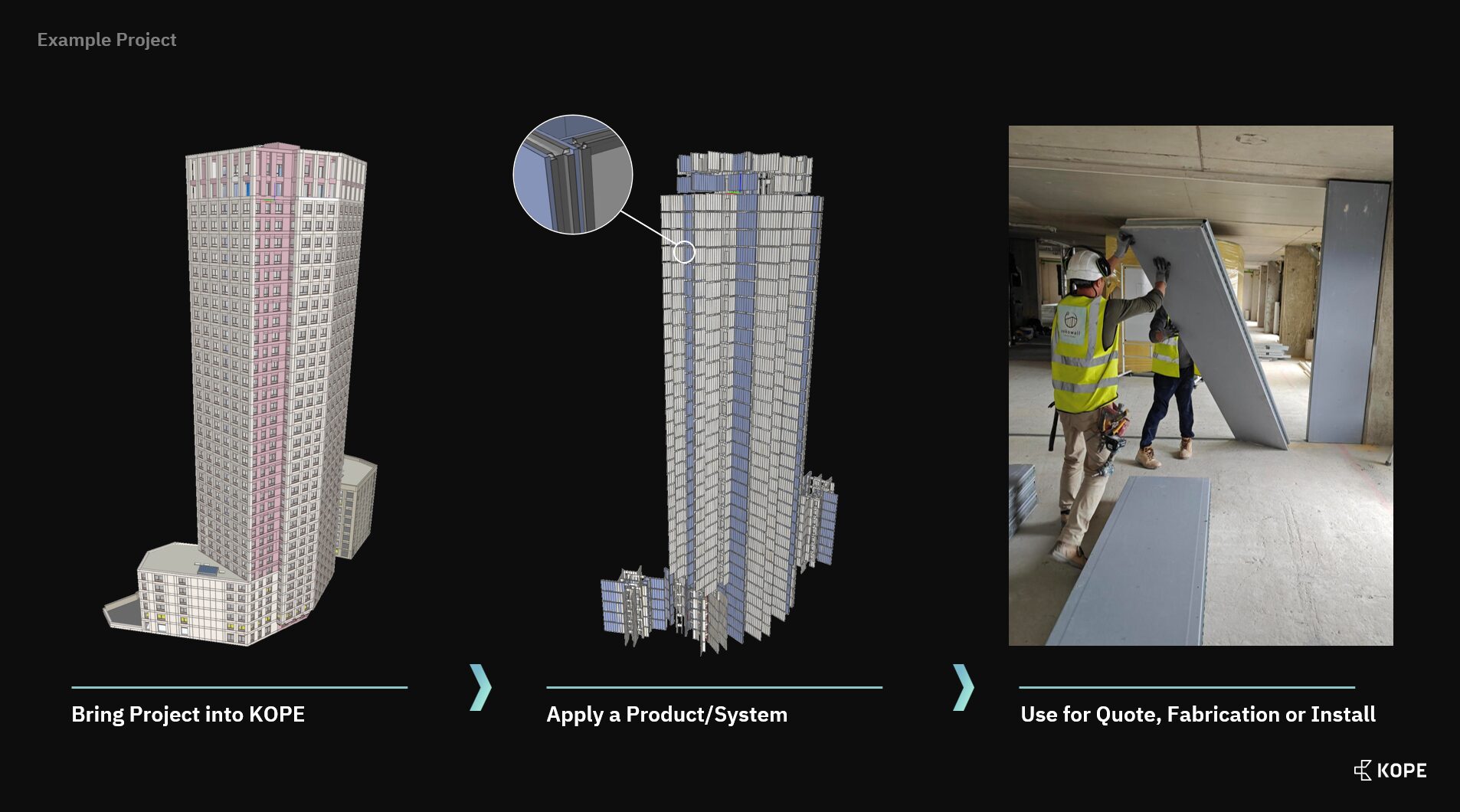
Traditional methods for assessing the feasibility and suitability of Saint-Gobain’s InteWall prefabricated partition systems have usually been costly, time-consuming and labour-intensive, typically taking several days per project floor.
In addition, late-stage design phases frequently excluded the possibility of adopting offsite solutions without significant redesign. This conventional approach increased the demand for bespoke components, inflated manufacturing costs and elevated project risk.
Saint-Gobain recognised an urgent need for a rapid, digitally-driven solution capable of quickly and accurately evaluating the viability of prefabrication within established designs. The primary challenge was to minimise bespoke manufacturing requirements without substantial impacts to existing designs, ensuring that off-site prefabrication could remain competitive and viable even at advanced design stages.
Software company KOPE AI worked with Saint-Gobain to create a bespoke product configuration platform that allows teams to quickly evaluate the suitability of InteWall’s partition system on existing project design models.
This product streamlines decision-making, reduces costs, minimises onsite waste by up to 92%, and significantly increases the standardisation and productivity of offsite manufacturing methods.
By digitally encoding the InteWall panel logic and placement strategies, the product was better aligned with manufacturing realities, enhancing the overall project productivity and enabling Saint-Gobain to offer a more competitive, sustainable and efficient solution.
Skyline Cockpit
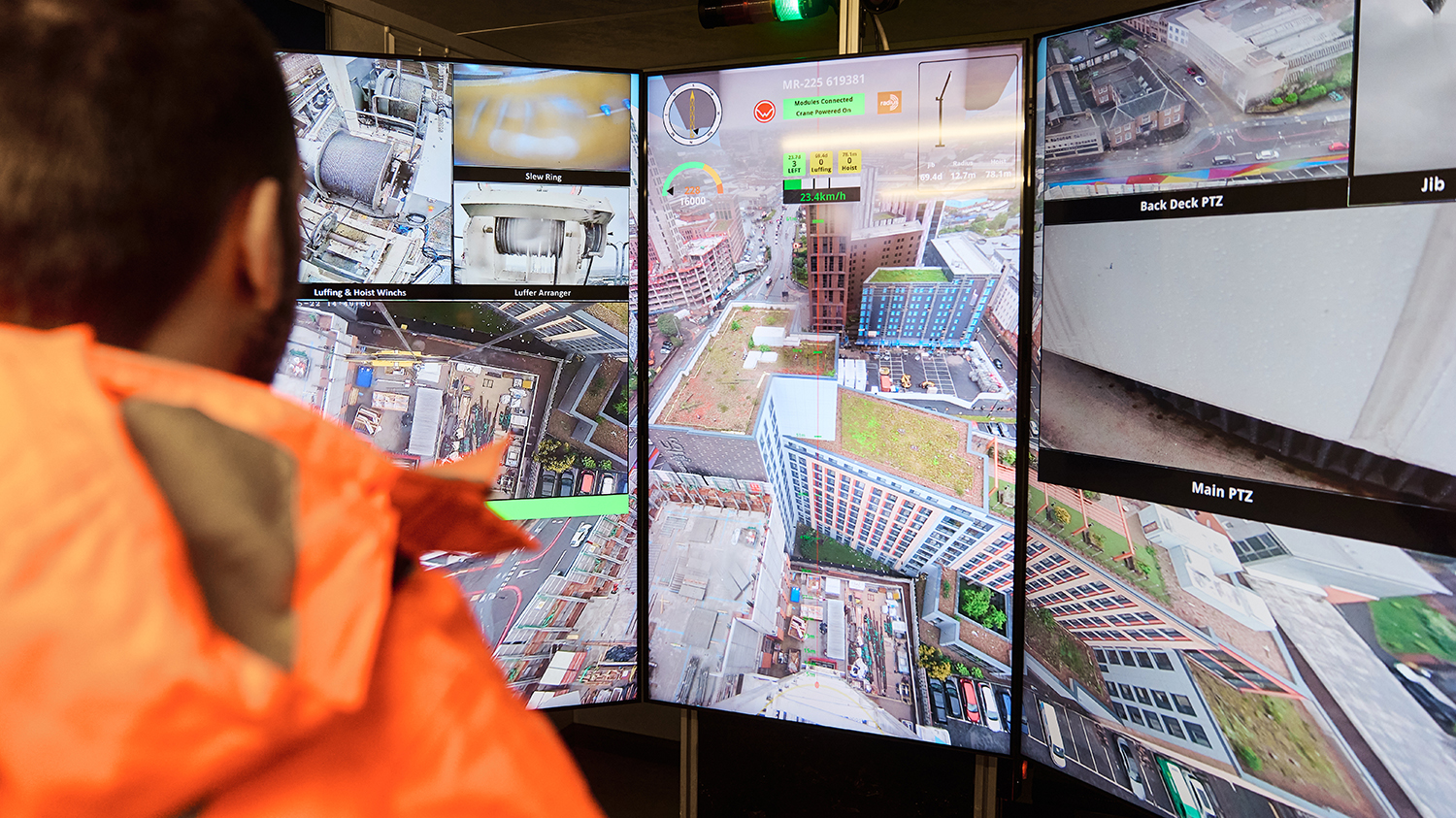
Traditionally, tower crane operators sit dozens of metres in the air, battling limited visibility, unpredictable weather and high-risk conditions. Skyline Cockpit flips that on its head.
With a multi-angle camera system, operators get a panoramic view from the ground of every essential angle: from the trolley winch to the hook and load line, eliminating the need to squint through a tiny window.
Skyline Cockpit’s cutting-edge software stitches visuals into a single, intuitive display, layering in augmented reality to anticipate exact landing spots in real time. Real-time alerts, safety warnings and weather-based adjustments turn crane operation from guesswork into precision.
The system can be retrofitted to existing tower cranes. Unlike fully automated solutions that require new machinery, Skyline Cockpit upgrades traditional cranes, making remote operation accessible without massive capital investment. It also allows one operator to manage multiple cranes, addressing the labour shortage without impacting efficiency.
Skyline Cockpit’s first UK deployment took place in partnership with Winvic and Radius Group at the Crown Place Birmingham project, a 33-storey student accommodation development.
The process came with challenges, including crane operators being initially sceptical about moving from the cab to the ground and regulatory compliance (remote operation in a live construction site required close collaboration with site safety teams). However, once the crane operators experienced the improved visibility, ergonomic set-up and reduced fatigue, adoption accelerated.
Skyline Cockpit also worked alongside Winvic to ensure seamless integration with existing workflows to ensure regulatory compliance.
After a 12-week trial, Winvic kept the system on site, reporting a 10% increase in crane efficiency.
SmartWaste Scan | Cielo Costa/BRE Group
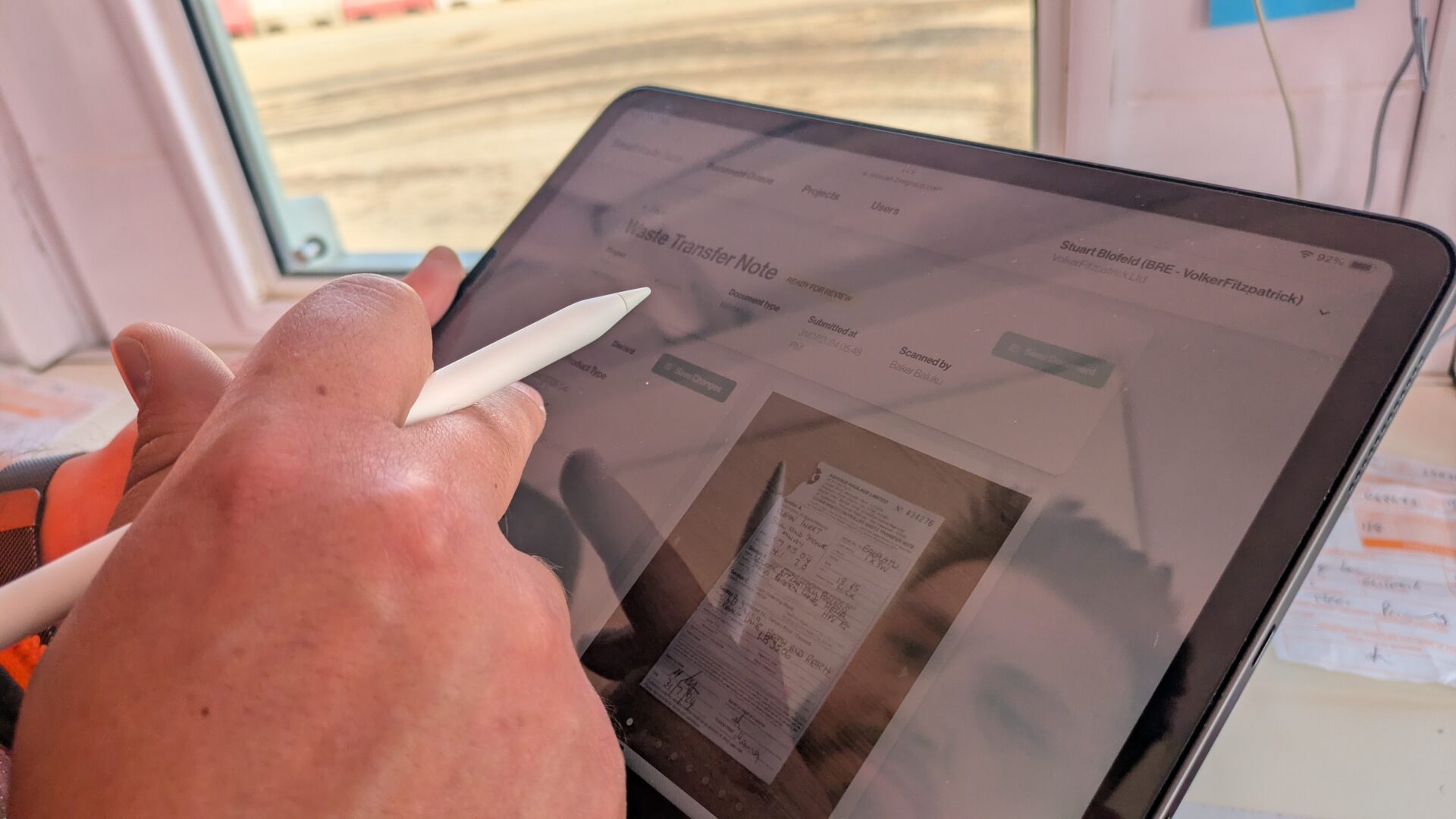
SmartWaste is an all-in-one platform that helps companies to efficiently track and report carbon emissions, waste, material usage and energy consumption. What was needed was to bring SmartWaste even closer to the day-to-day reality of the construction site, which is where SmartWaste Scan came in.
Using AI, SmartWaste Scan removes the need for inefficient and laborious manual data entry processes, cutting costs and time for users. With just a photograph of a waste ticket or material delivery note, SmartWaste Scan uses optical character recognition and machine learning to extract and verify data from such documentation, improving operational efficiency and compliance in the process.
The automation of these processes removes the risk of human error while bringing waste reporting under one platform. It also provides a standardised route to maintaining oversight of subcontractors.
Contractors and subcontractors can submit a wider range of carbon data on the updated platform, including Scope 3 carbon emissions data alongside SmartWaste’s existing carbon reporting capabilities and full duty of care tracking.
SmartWaste Scan is a web application that can be accessed from anywhere with a network connection, including a smartphone or from a laptop.
There were challenges along the way. Initially, the AI struggled to extract data accurately from the paper forms. To crack this, Cielo Costa trained machine learning models extensively and then tested three different solutions against each other, which resulted in a significant uplift in accuracy.
Six existing SmartWaste customers have already worked with SmartWaste Scan and achieved savings in every case as well as more accurate measurement and increased visibility ease of communication with main contractors.
Willmott Dixon in partnership with Nialli and Ascentae
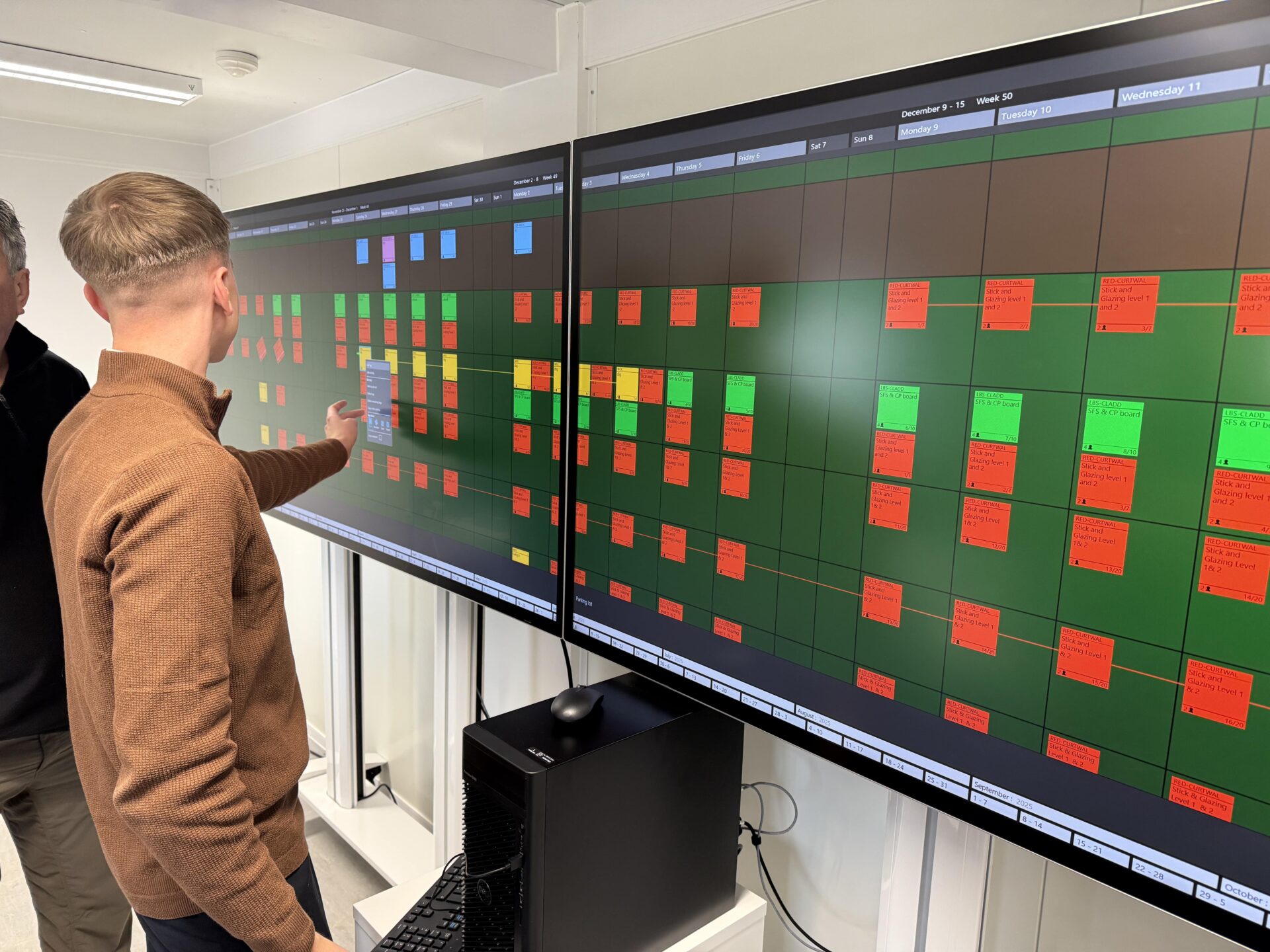
Willmott Dixon has set a new standard in digital construction planning through the seamless integration of the Nialli Visual Planner and Jupiter 21:9 ultrawide interactive displays.
This transformation has dramatically increased project efficiency, improving percentage plan completion from 40% to 72%, reducing variance issues by 30% and halving project errors, leading to substantial cost savings.
Unlike other solutions that require complete process overhauls, Willmot Dixon’s approach balances traditional best practices with cutting-edge technology, ensuring intuitive adoption and tangible productivity gains.
Enhancing stakeholder collaboration and enabling real-time data-driven decision-making has fundamentally reshaped how projects are planned and executed. The collaborative planning methodology ensures that projects stay on time and within budget while fostering stronger supply chain relationships and boosting overall business performance.
By successfully bridging the gap between analogue and digital processes, Willmott Dixon has created a scalable, industry-leading solution that will continue to drive productivity and innovation within the business, with wide-reaching benefits across their supply chain.
Improved visibility, collaboration, and valuable data have enabled Willmott Dixon to execute regional and national projects more effectively.
Celebrate with the best
The winners will be revealed at the gala dinner on 1 July at the Brewery in London.
You can join the shortlisted entrants by booking your seats at the awards.
The Digital Construction Awards are organised by Digital Construction Week, Construction Management and the Chartered Institute of Building. The first sponsor to be announced is Bluebeam.
To find out more about the Awards, visit digitalconstructionawards.co.uk.