The Digital Construction Awards attracted more than 140 entries, 62 of which have been shortlisted. Here we detail the shortlist for the Best Application of Technology.
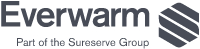
This category, sponsored by Everwarm, recognises the application of a specific technology. The category focuses on how technology has been applied to a particular challenge or solved a specific problem.
This category proved exceptionally popular with entrants, so rather than a shortlist of six, eight entries made the cut.
The likes of Kier Construction, McAvoy Group, L Lynch, Faithful + Gould and Travis Perkins have secured a place on the shortlist
Building a smart estate for Manchester Foundation Trust | BIS Consult with Manchester University NHS Foundation Trust, Morta, Esri UK and Concerto
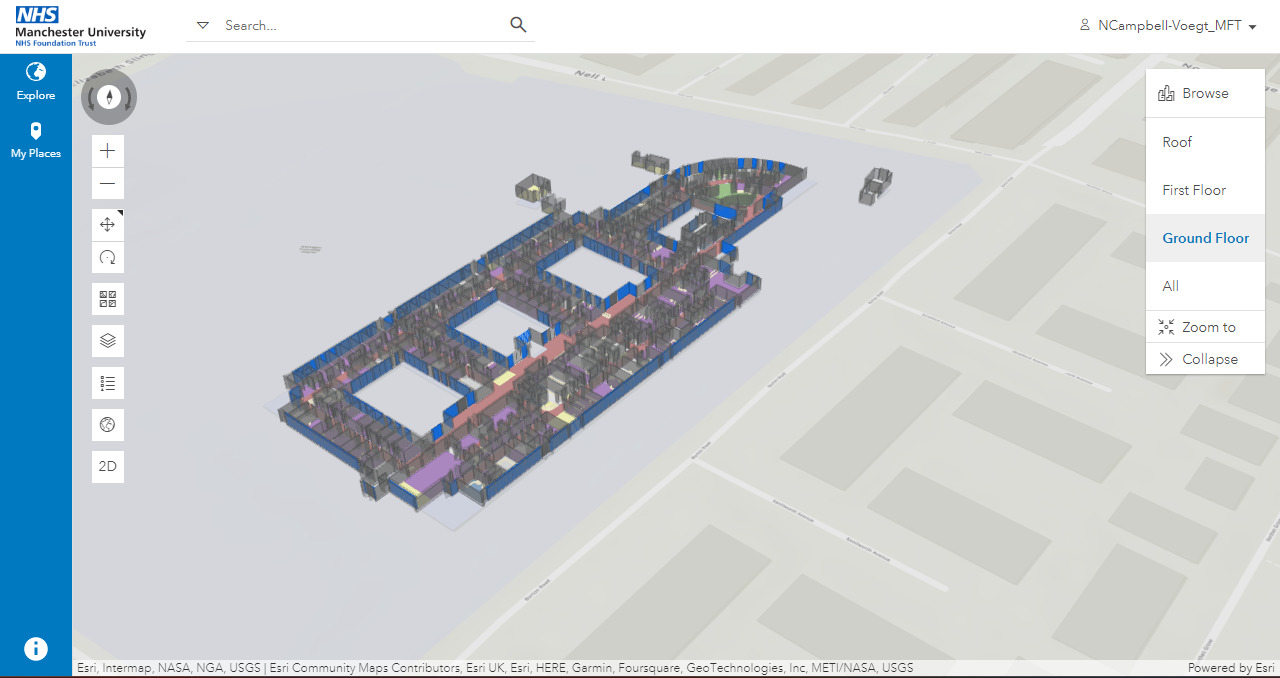
For Manchester Foundation Trust, the issue of data fragmentation and a heavy reliance on manual data processing was reducing efficiency across project delivery, asset operation and maintenance activities. It was creating a lack of transparency, reducing collaboration between different teams and departments, and most importantly reducing trust and confidence to make effective decisions.
The trust has more than 80 managed properties across an area spanning from Liverpool to the Peak District, including hospitals, community health centres and administrative space, as well as hundreds of off-campus facilities through which it delivers critical health services.
BIS Consult set about unlocking the value of the trust’s estates data and creating a single view of the truth. Rather than following traditional approaches of large data migration and IT transformation programmes, BIS Consult took a different approach: it set out to retain and integrate the existing systems and data, to optimise the value of what was already in place, while introducing new tools for data integration, validation and visualisation.
BIS Consult’s approach involved the capture of data on a daily basis from the trust’s legacy CAFM system, Concerto, to an Azure database hosted by the trust.
The consultancy then used the Morta platform to digitise processes previously managed in spreadsheets and word documents, with a connected and customisable information hub.
BIS Consult then turned to the Esri UK ArcGIS geospatial mapping platform to create maps of the estate and geo-locate the data.
Component tracking in complex supply chains: HMP Millsike | Kier with PCE, Ministry of Justice and Ynomia
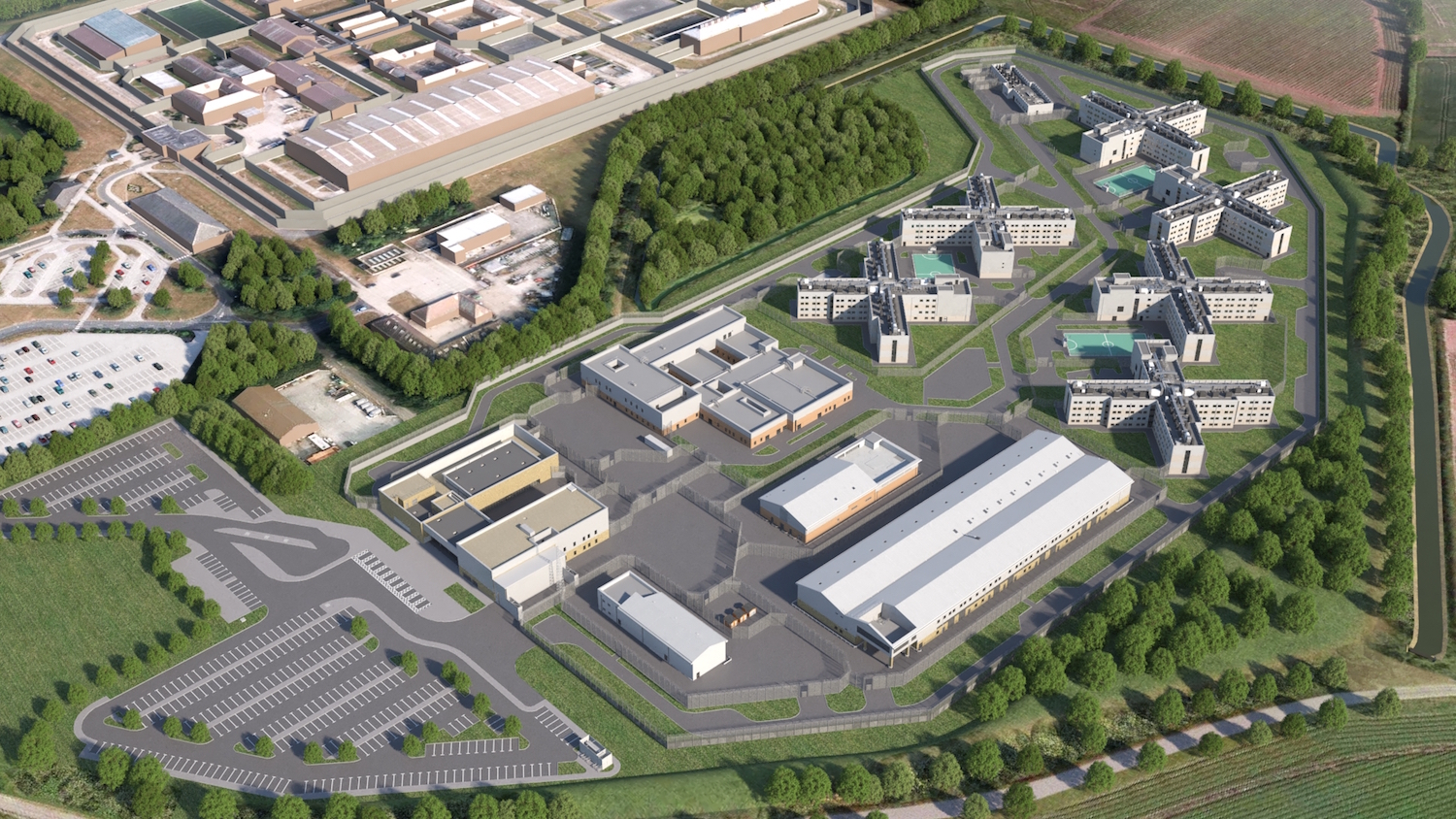
Kier is constructing the £400m HMP Millsike prison in East Yorkshire for the Ministry of Justice.
The prison will feature 14,550 precast concrete units and circa 90,000 subcomponents, which are being manufactured in nine factories across the UK and Ireland. Kier required fast and accurate component tracking across the project.
On the HMP Five Wells project, Kier had used Dalux for quality assurance across six factory sites, tracking the status of components being produced by each of the three suppliers. AT Millsike, Kier chose Ynomia to build on this success, making direct use of data gathered through Dalux and other tools.
The Ynomia workflow relies on bluetooth light energy tags on components moving past beacons to trigger milestones. This also makes direct links to the data sources Kier already uses: it automatically monitors ViewPoint for design progression of components and Dalux for installation checks. It provides a live perspective on a component’s journey, from design to installation, visualised through a digital twin, with no extra work required.
Just a few months into the project, Kier has already saved around £250,000 from better control of casts in component supply, while also saving a significant number of hours in managing and administering the project. Indeed, Kier has fewer staff managing and administering HMP Millsike than the HMP Five Wells project.
Designing in efficiencies: how augmented reality has streamlined the design process | McAvoy Group with Korec Group
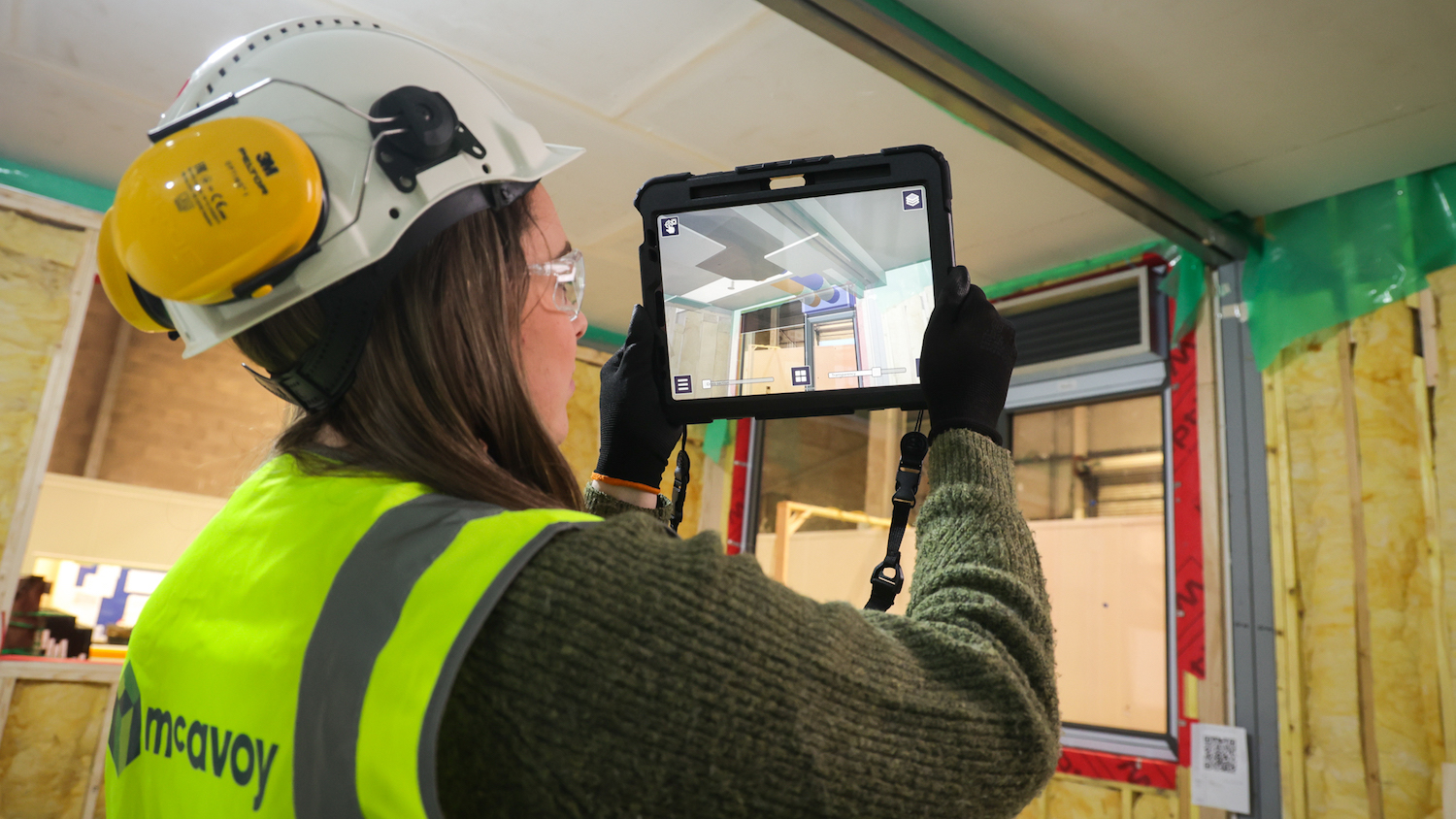
McAvoy Group needed a solution that could verify the design data from the 3D BIM model in a live build environment, enabling the business to make more accurate decisions based on real-time data.
The contractor chose the Trimble Connect AR solution (from Korec Group) as it enables the 3D data to be brought onto the factory floor and sites, where users can then overlay the 3D models with the actual build to verify the installation of the build.
Using AR, McAvoy can visually compare the virtual model of a building with the actual build to verify design information, ensure correct installation of packages – specifically M&E.
McAvoy is also able to track, resolve and manage issues using AR. These issues can be detected early in the design process while the building is under construction in the factory – resulting in a more cost-effective process and better quality control.
Furthermore, AR has enabled McAvoy to improve its internal communications with operatives and subcontractors. The firm can communicate the location of services and any design requirement quickly and accurately through the AR software.
Finally, by using AR, McAvoy can report any design changes in the factory or on site back to the design team for approvals and updating the BIM models for handover. This allows McAvoy to improve its golden thread of information with all records remaining up to date throughout the project lifecycle.
Digital Thumbs Up | L Lynch with Safety Shield Global
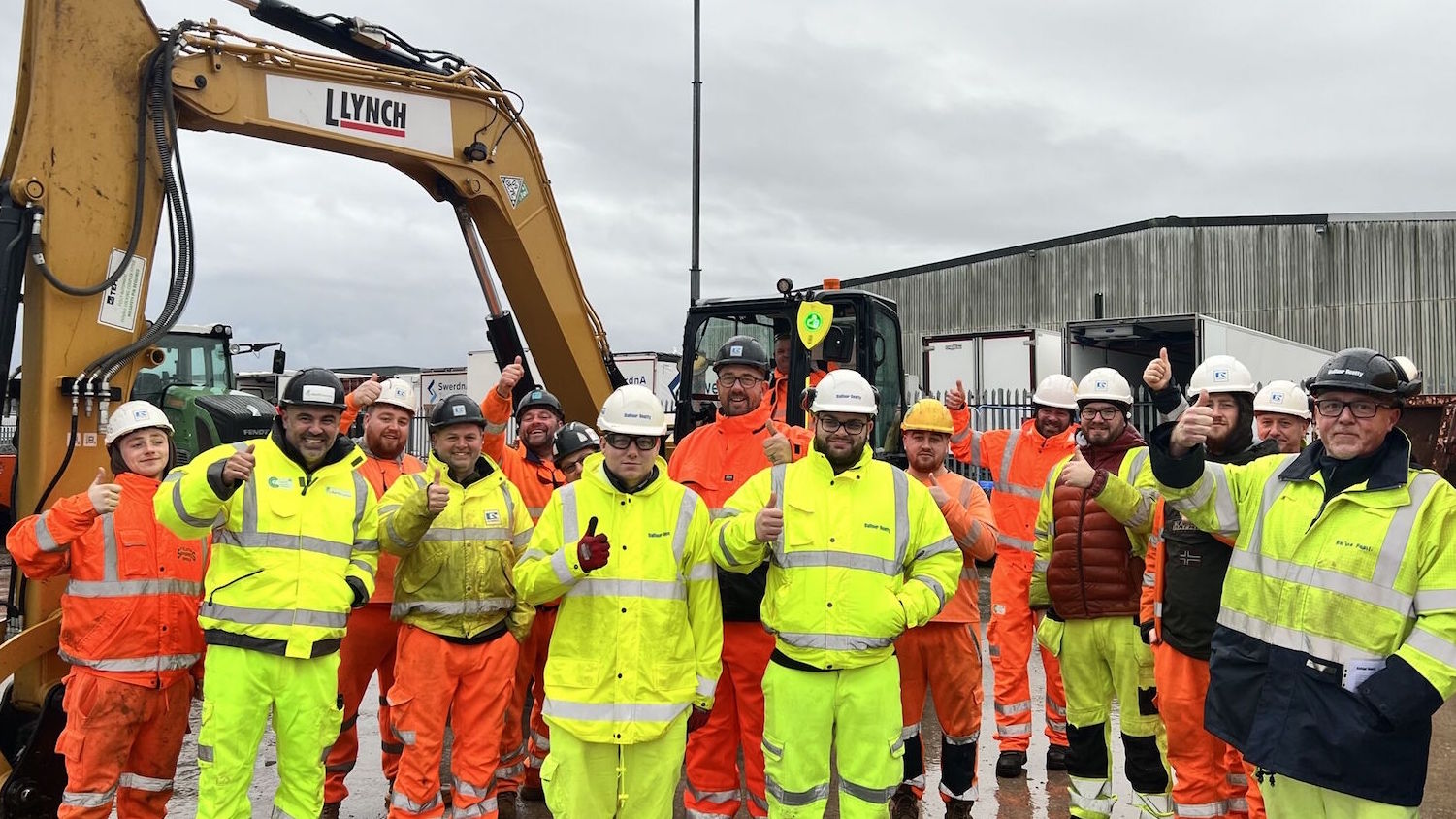
Collaborating with Safety Shield Global, L Lynch has digitalised the established, industry-known safety procedure: Thumbs Up.
An internal review of Lynch’s health and safety processes and procedures revealed improvements in the Thumbs Up procedure. Lynch recognised that in poor visibility, such as during winter months when there are fewer daylight hours or poor weather conditions, a thumbs up from an operator could be misinterpreted by site personnel. Moreover, Lynch appreciated that not all individuals attending sites have received the Thumbs Up or Red Zone training.
To counter these challenges, Lynch collaborated with leading plant safety technology company Safety Shield Global to digitalise the Thumbs Up procedure.
When a site user wants to approach the machine, they give a thumbs up gesture from a safe distance to the operator. Once the operator has seen the thumbs up signal, they will bring the machine to a controlled stop.
The operator then presses a button in the cab that triggers the LED sign to change from a red No Entry to a green Thumbs Up. This is accompanied by an audible message from an inbuilt speaker saying: “Thumbs Up accepted, approach with caution.” At the same time, on a 360-degree excavator, the controls are disabled and made safe for the approaching person.
This then allows the site personnel a safe way to approach the machine without any doubt they have been seen.
Lynch has installed the Digital Thumbs Up on 300 machines on sites nationwide.
Heathrow Airport – water leak detection solution | Ramtech with Mace, Heathrow Airport and Wingate
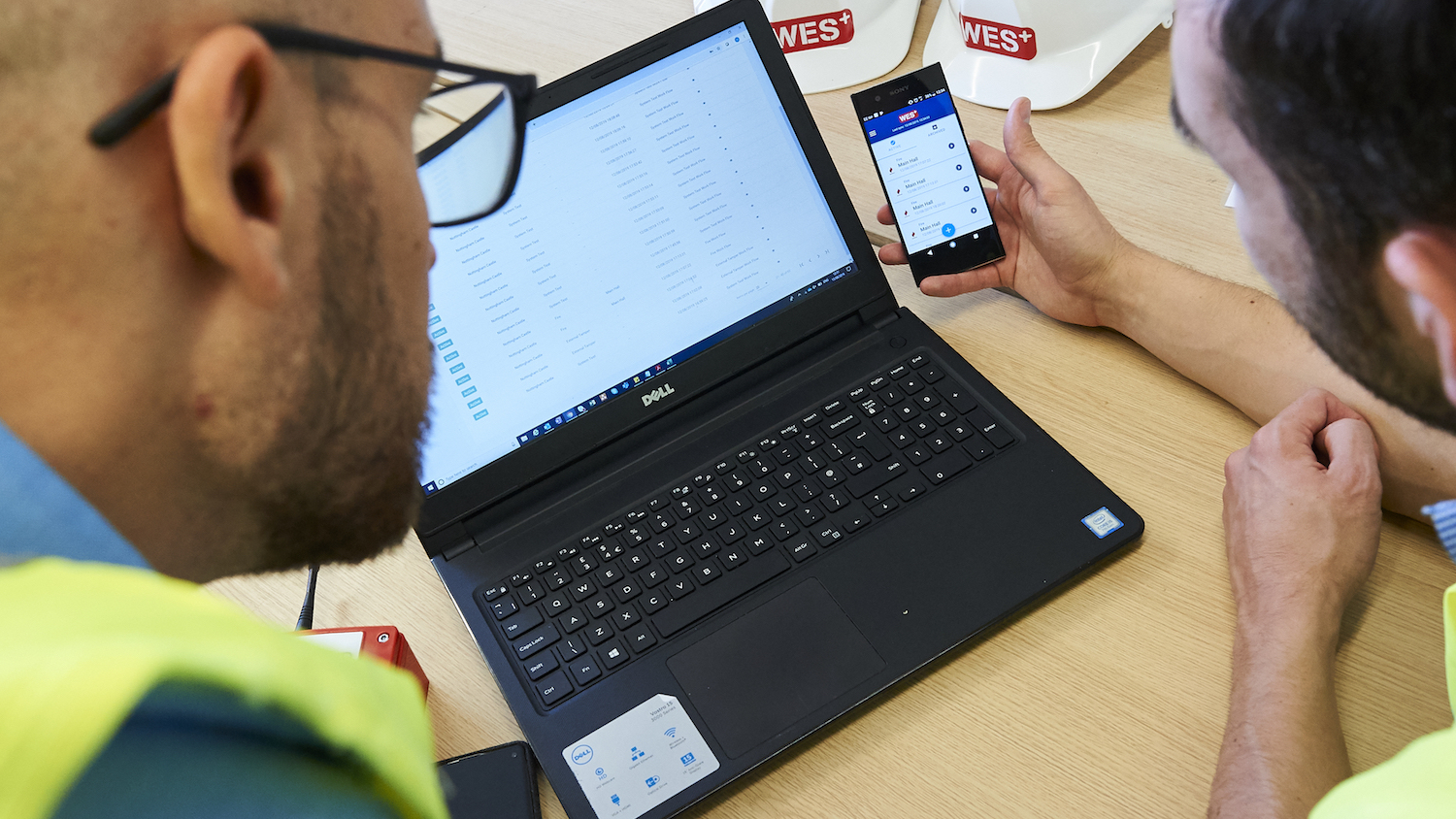
While fire is responsible for the largest insurance losses in construction, escape of water is still the most common – and most costly – for construction project teams.
Ramtech’s water leak detection solution (WLDS) offers an automatic, 24/7 monitoring solution. It integrates with Ramtech’s existing wireless fire detection WES platform, creating a EN54-25 compliant fire and escape of water solution
The WLDS works by detecting if moisture reaches the various nodes along the technology’s detection tapes or cables. It then sends an alert via data when combined with Ramtech’s cloud-based REACT platform, used by personnel to raise alerts on-site.
Mace and Wingate used the technology at Heathrow to protect the airport terminals undergoing construction work. The work involved the removal and replacement of dilapidated water pipe valves in Terminal 4.
This was a high-risk project as the existing system was around three decades old, but still formed part of a major live site.
Nine water detection units were used across eight plant rooms. The system was a logical choice for Mace, with the team having worked with similar products in the oil and gas industry, but never in construction. This was the first time working with a Ramtech product, through Wingate.
Mace intends to use the WLDS in a similar capacity for Terminal 5 operations.
Local ID | Faithful + Gould
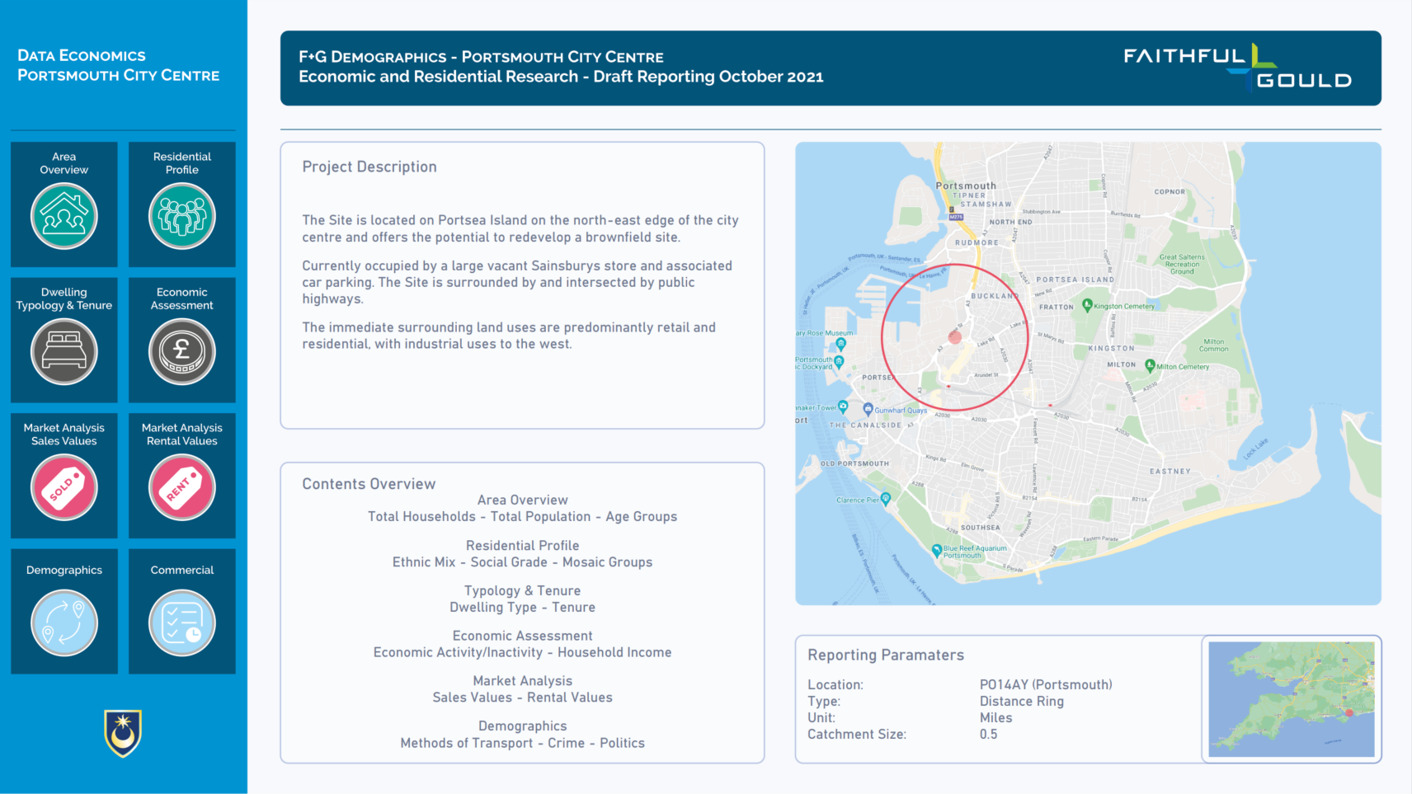
Created in-house by teams in London and Bangalore, Faithful + Gould’s Local ID tool gives developers and local authorities the power to leverage a wide range of data so that they can analyse, improve and optimise their housing developments (including associated infrastructure) and investment.
Demographic data, for instance, can improve the placement of new housing estates, schools and GP surgeries, easing the pressure on local infrastructure. Knowing the incomes, lifestyles and needs of the locality allows developers to turn generic plans into bespoke solutions, making them more targeted and efficient, which in turn can tilt the business case in favour of development.
Local ID also provides statistics around modes of transport, which can help in making crucial decisions regarding transport infrastructure in localities.
In its initial stage, the tool comprised a PowerBI front-end with Excel as the underlying database.
Upon successfully demonstrating the functionality, Faithful + Gould realised a more stable environment was needed to host the data so the tool could be scalable and sustainable. Considering the volume and complexity of the data, and the intended usage in future, Faithful + Gould decided to use Azure Data Factory for data ingestion, storage and carrying out analysis using AI & machine learning.
Since its soft launch, it has been used on major schemes, including the current Portsmouth City Centre regeneration scheme and on a new estate in the London Borough of Enfield.
Plymouth City Council’s new crematorium The Park | Kier
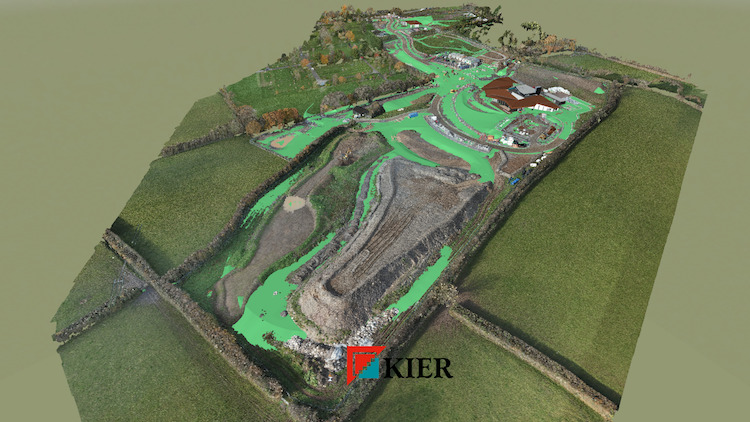
Using drone surveying, point clouds, and data-driven earthworks quantification, Kier Construction optimised construction efficiency, accuracy and sustainability on the Plymouth Crematorium for Plymouth City Council.
Drone surveying captured high-resolution aerial imagery, which was processed into detailed point clouds for 3D models. These models facilitated terrain analysis, obstacle identification, and efficient earthworks planning.
The drone surveying significantly accelerated the data collection process compared to traditional methods, allowing the project to commence more quickly and adhere to strict deadlines. The increased accuracy and precision of the data reduced the need for rework and minimised disputes, ultimately leading to cost savings.
High-resolution cameras and LiDAR sensors mounted on the drones generated accurate and detailed 3D models of the site, enabling the construction team to make informed decisions during the design and construction phases. The data quality also minimised the risk of errors and inconsistencies, ensuring a higher-quality final product.
The integration of drone-generated data with BIM systems facilitated more efficient collaboration between architects, engineers, and contractors. Access to a comprehensive digital representation of the construction site improved communication, reduced the risk of misunderstandings, and streamlined decision-making among stakeholders.
Using drones reduced the need for manual labour in hazardous surveying conditions, enhancing on-site safety. Additionally, the technology contributed to the project’s sustainability goals by minimising rework, waste and the environmental impact of construction activities.
WholeHouse | Travis Perkins
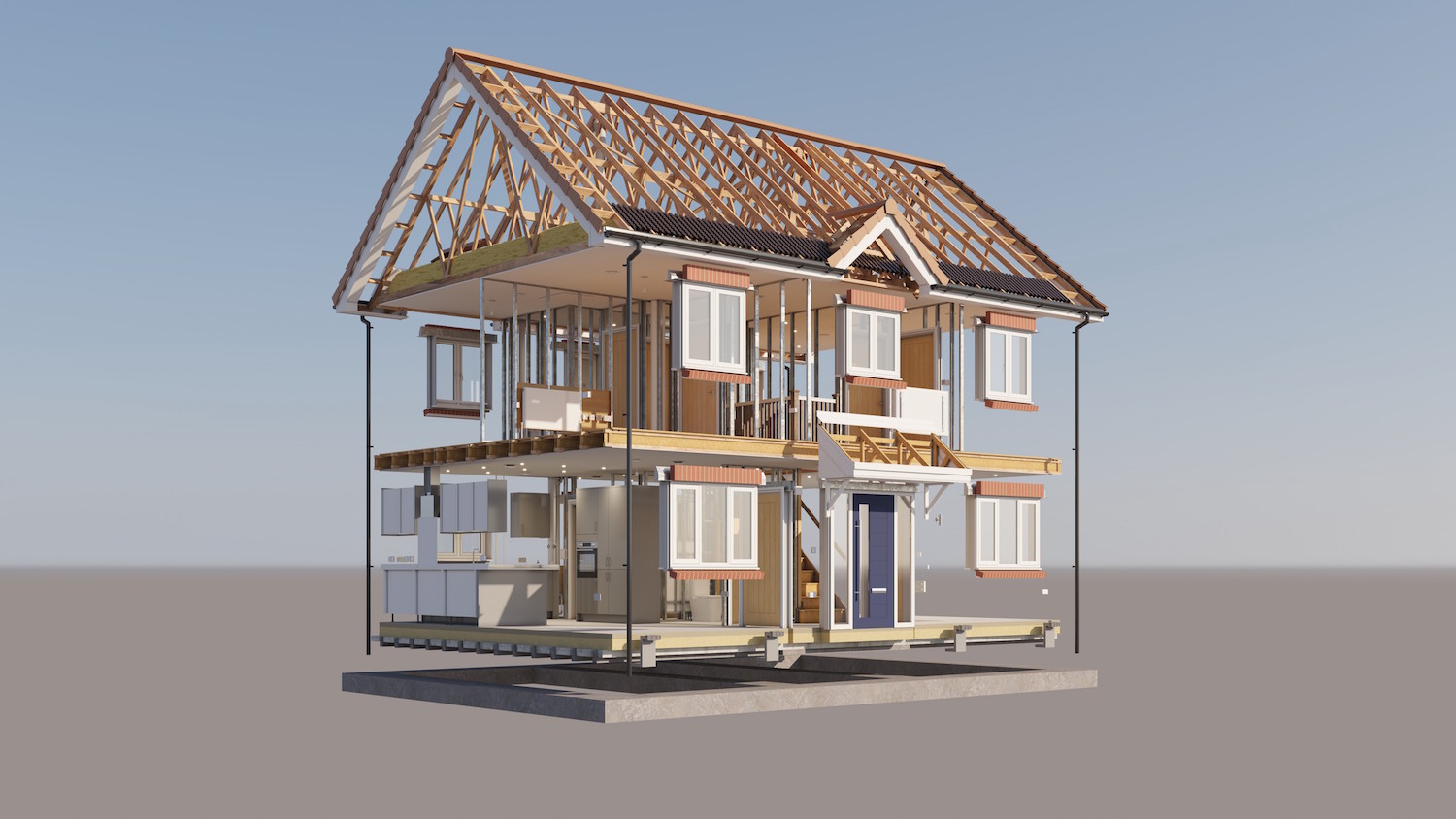
WholeHouse is Travis Perkins’ BIM-style design and costing platform for housebuilders building up to 250 units a year.
Using the platform, housebuilders can visualise in 3D their designs of plots and developments. These can be adapted, personalised and tailored to customer requirements.
WholeHouse generates designs, material schedules, detailed construction and marketing materials needed to plan, cost and build projects at the click of a button. WholeHouse allows housebuilders to create a house type from over half a billion coordinated, tried-and-tested designs.
Information is embedded in the models, down to details like the colour of brickwork, different roof types, verge types, windows, door frames, porches, and gutters. Furthermore, component prices update in real-time as different components are added to the design, so informed costing decisions can be made.
Designs are also checked and reviewed by an industry-leading and expert supplier panel and are fully compliant with industry standards and latest regulations.
WholeHouse can supply housebuilders with an entire set of drawing sheets, up to 200 pages of construction details and a full bill of all the items needed to build a property in under an hour.
Celebrate with the best
The winners of the Best Application of Technology category, alongside the victors of the other 11 categories, will be revealed at the awards dinner on 4 July at the Brewery in London.
You can join them by booking your places at the awards. There is an early bird discount for those who book tables before 5pm on 19 May.
The Digital Construction Awards celebrate best practice and reward innovation in the application of BIM and digital technology in the built environment sector.
The awards are run by Digital Construction Week, the Chartered Institute of Building, and Construction Management and BIMplus.
Awards sponsors include the Association for Project Safety, BIMcollab, Bluebeam, Everwarm, Graitec, nima, Procore, Revizto and Sir Robert McAlpine.
Don’t miss out on BIM and digital construction news: sign up to receive the BIMplus newsletter.
The post Digital Construction Awards 2023 shortlist: Best Application of Technology appeared first on BIM+.