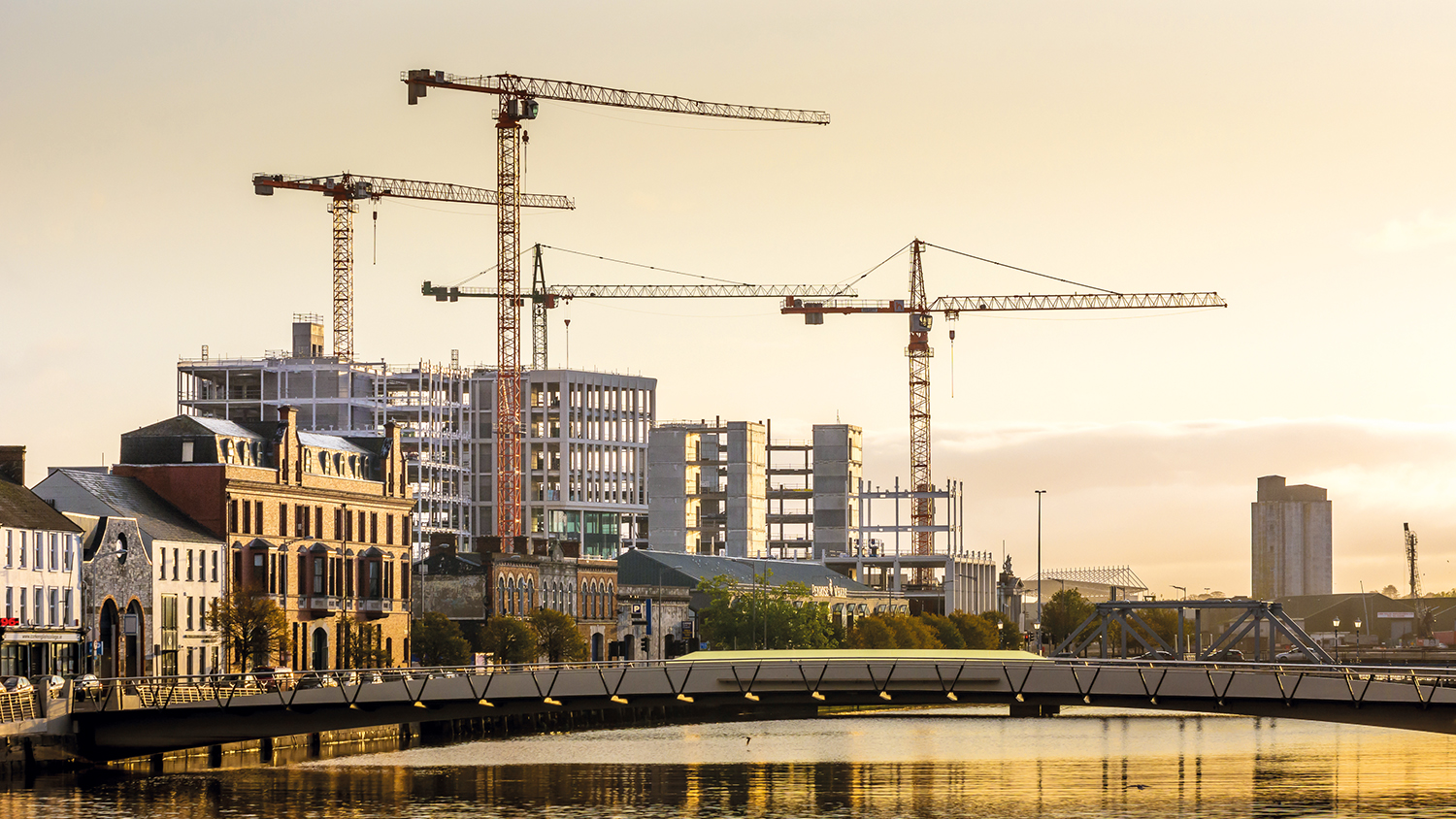
After last month’s spotlight on MMC in Australia, Rod Sweet looks at a new CIOB report on the building method’s prospects in Ireland.
A new report published by CIOB and TASC, an economic and social think-tank in Ireland, has examined the barriers to modern methods of construction (MMC) in the country.
Its author, Dr Robert Sweeney, said expanding MMC would get houses built faster and help Ireland achieve its carbon emission targets. The report, Modern Methods of Construction: Barriers and benefits for Irish housing, calls for a concerted effort by the Irish government to change various policies to promote MMC.
“It would result in considerably less waste than conventional construction methods, enable construction to be carried out more quickly and would reduce disruption such as noise and truck traffic in local neighbourhoods,” he said.
In Ireland as in the UK, MMC is an umbrella term that includes a spectrum of approaches, from 3D volumetric modular or 2D panelised pre-manufacturing at one end, to technologically assisted conventional construction at the other.
This report uses ‘MMC’ and ‘offsite manufacturing’ interchangeably. It’s based on interviews with 30 people working in construction, two-thirds of them in the private sector – a mix of contractors, architects and manufacturers – and about a third from local authorities.
What’s holding it back?
The supposed benefits of MMC are by now familiar: speed of delivery and better quality assurance are the most often cited. But the barriers the report reveals are as multifaceted and systemic in Ireland as they are in the UK, where problems have afflicted several modular builders.
Five policy changes that could prime the MMC pump
- The government should review height restrictions for timber frame buildings, currently set at 10m.
- The report urges government to include MMC components in building regulations and their accompanying Technical Guidance Documents to prevent manufacturers having repeatedly to test and prove their systems for each application.
- The government should consider raising taxes on concrete for its embodied carbon content.
- Local authorities should build more social housing directly to shape that market more toward MMC.
- The government should develop MMC-friendly procurement models.
Most of the barriers stem from the basic problem of weak and unstable demand. Factories are expensive to build, equip and staff, and the money spent on them won’t be recouped if their production lines sit idle for even some of the time.
When it comes to private housing, demand for factory-made houses falls at the first hurdle because the major banks won’t offer mortgages for modular homes, the report finds.
One manufacturer described the lengths it went to to try and engage their banker. First the bank demanded a certificate of completion. Then it demanded the house be fixed to the foundation. Then it required a 60-year guarantee.
The manufacturer met each demand but the bank still said no, the report said. Funding for big modular developments is tricky as well, because manufacturers will typically ask for up to 60% of the total cost up front, the report found, whereas in conventional projects banks release project funding in more gradual stages.
Insurance presents difficulties, too. After the 2017 Grenfell catastrophe, insurance is very expensive for MMC manufacturers because actuarial data on the risks of MMC is skimpy and skewed toward disaster. MMC makes insurers especially jumpy about professional indemnity insurance for designers after Grenfell.
Vagaries of planning
Difficulties with financing led the report to conclude that public housing may be better for MMC, since local authorities can in theory build independently of market forces.
But local authorities are beholden to planning rules, and a number of interviewees said the vagaries of Ireland’s planning system impedes the take-up of MMC.
The uncertainty in the MMC market means that delays in planning, which can amount to years, leave social housing developers at risk if the manufacturer who helped them work up their plans is unable to deliver when permission is finally granted.
And the report notes that switching manufacturers at the last minute is not straightforward. Perhaps the biggest barrier to MMC in Ireland and elsewhere is the lack of standard designs for social housing.
The manufacturing business model needs a high degree of standardisation. As Henry Ford quipped, customers could have his Model T in any colour they liked so long as it was black.
One MMC manufacturer complained of the huge variety of designs among local authorities for social housing.
Leaps ahead
Big private housebuilders like Glenveagh and Cairn Homes were leaps ahead in this respect, the manufacturer said. They give architects strict guidelines on internal dimensions.
“So if the government adopted a similar approach to what the private entities like Glenveagh and like Cairn Homes do in really locking in design standards and not budging from them, and saying, right here’s our modular house, we have two styles and we have two grades, Grade A and Grade B.
“Now modular manufacturers, there’s three years worth of it in front of you, man up, invest and start delivering,” the manufacturer said.
Faced with these difficulties, it’s no wonder the MMC manufacturing market in Ireland is immature, as the report finds, with a limited number of firms trying to make a go of it.