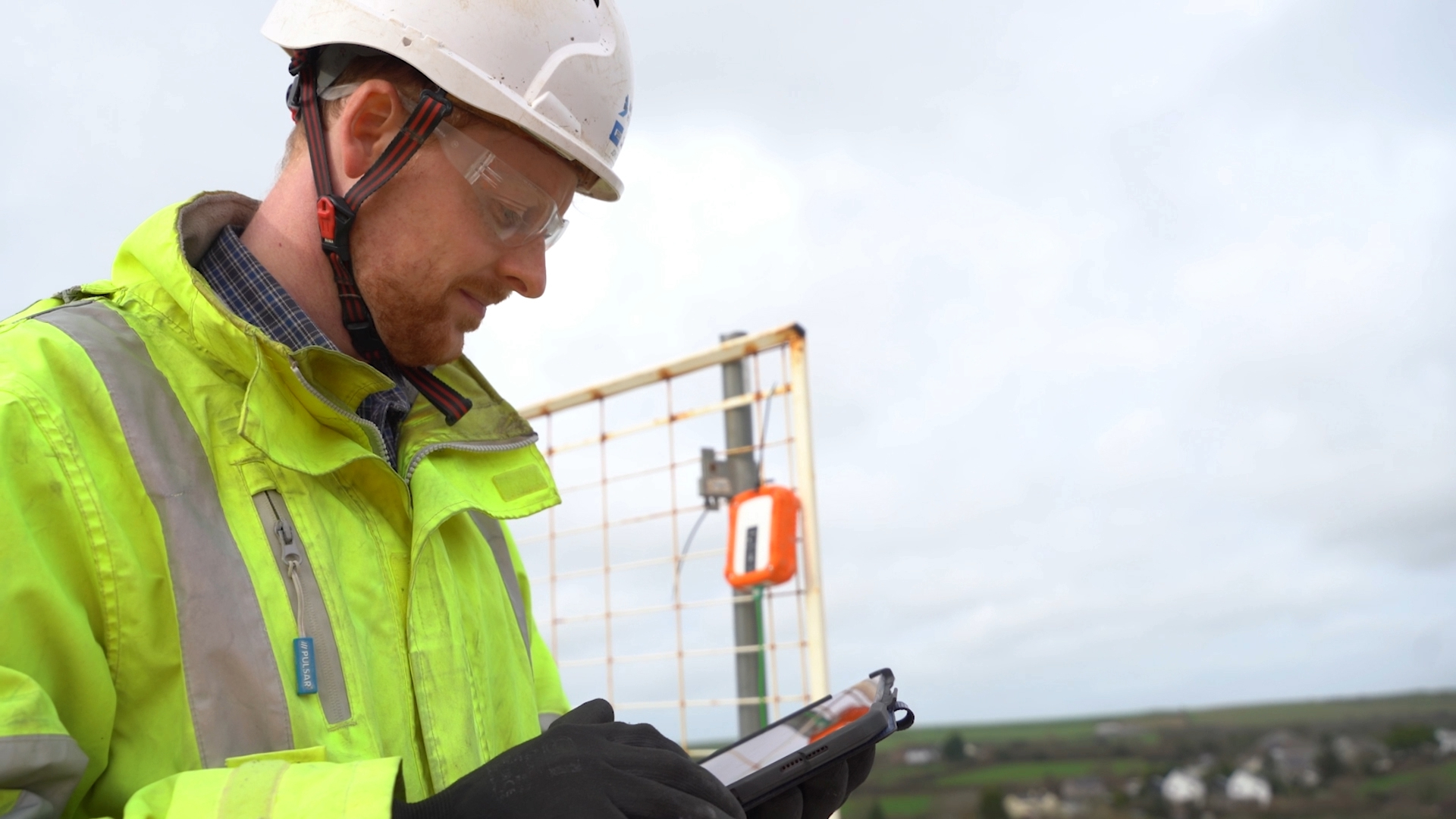
Concrete sensor technology has helped Costain reduce striking times by a third and lower its carbon footprint, the engineering company claims.
Materials engineers have been using concrete sensors to monitor the strength and temperature of setting concrete, which resulted in time and efficiency savings, Costain said. It also helped reduce the quantity of materials used.
One project used the sensors for more than 80 different pours and structures, eliminating the need to conduct destructive testing of approximately 500 strike cubes.
How the sensors work
The Gaia 200 sensors, manufactured by Maturix, send real-time temperature and strength data wirelessly to engineers, temporary works designers and other specialist contractors. Each sensor is the size of a smartphone.
This information helps contractors make faster and more informed decisions, such as when to remove the formwork following a concrete pour, for example.
Concrete pours are traditionally tested by physically removing cube samples to be examined under lab conditions, with a typical pour requiring around six cubes.
The ability to record readings directly and accurately from sensors means these tests are no longer necessary.
Comments
Comments are closed.
No offence, but we were doing this at Balfour Beatty over ten years ago at Whitechapel station. Strike, curing and loading times using concrete with 80% GGBS.
Sir Robert McAlpine were doing this when casting the lids of the caissons on Cormorant field gravity oil platform, high PFA content concrete. 1976.
Previous comments just going to show how slow the industry adopts change and best practice. Like sustainable drainage (SuDS), being well-known and in use for at least 25 years, yet still not business-as-usual.