New digital surveillance technology is proving its worth in improving concrete quality assurance, as well as advancing safety and sustainability, writes Mott MacDonald’s Sudarshan Srinivasan.
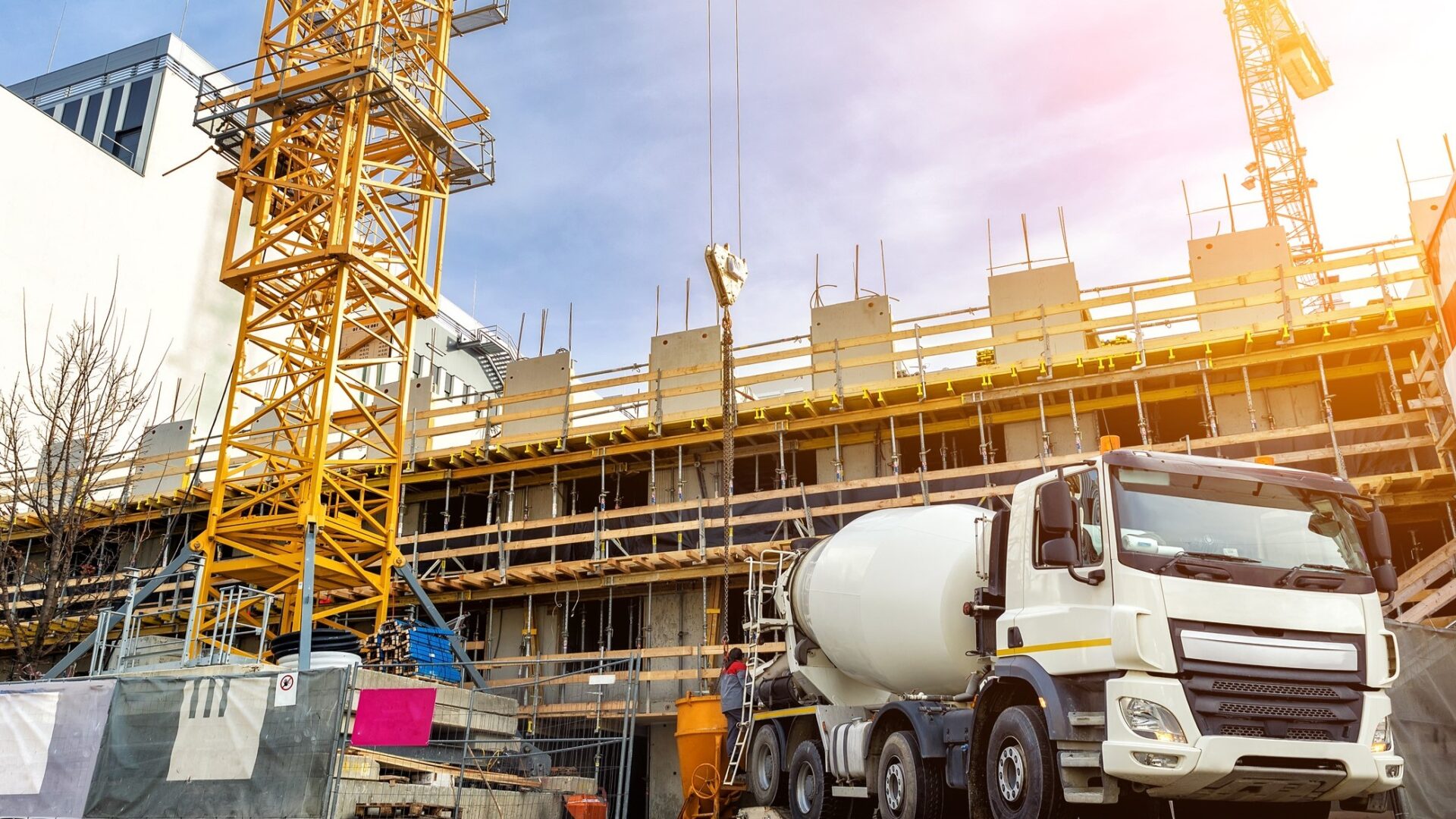
Cutting 1,500 tonnes of carbon from just one element of a major construction project through technology might seem too good to be true. However, new digital solutions in the concrete sector can deliver that – and more.
This headline-grabbing carbon reduction was achieved by using a concrete delivery truck with equipment to provide real-time consistency and temperature monitoring during the delivery of 20,000 cu m of concrete.
Mott MacDonald also worked with the contractor and concrete supplier on the project to use technology that undertook digital slump monitoring, replacing waste intensive manual tests. The combination of these digital solutions was key to reducing load rejection that, in turn, made the carbon savings possible.
While not every project is of this scale, this technology and others aimed at providing surveillance for concrete during the production, delivery and placement stages could soon benefit schemes of all sizes.
A wide range of digital technologies such as sensors, data acquisition systems, data analysis and decision-making tools are being implemented in large infrastructure projects. However, there are challenges to be addressed to improve the accuracy, reliability, integration and acceptance of the digital methods as an alternative to the conventional and manual techniques.
Manual testing drawbacks
Digital surveillance refers to real-time data acquisition, storage and analysis of the properties of concrete. At the production and delivery stage of concrete, a significant amount of manual testing is undertaken by contractors to ensure its quality.
It is time-consuming and expensive to implement this manual testing, especially on large construction projects where high volumes of concrete pours need to be controlled and monitored. The basic properties of constituent materials, for example moisture content of aggregates, mix design parameters and batch records, are usually monitored in real-time at the ready-mix concrete batching plant.
However, the crucial fresh concrete parameters, such as slump and temperature, are measured manually for each load of concrete at the production plant and at the site delivery point.
As well as the technicians being required to monitor multiple pours taking place at the same time, it is also very disruptive with waiting time required to check compliance. Plus, if the concrete is rejected there will be wastage, potential delays to the pour and a risk of cold-joint defects.
In-transit monitoring
Established research on the rheological properties of concrete on measuring yield stress and plastic viscosity has been transformed to develop an automated in-transit concrete monitoring system.
GCP Applied Technologies’ VERIFI system and Sika’s CiDRA SmartHatch are examples of in-transit management systems that use on-truck sensors and proprietary algorithms to measure key properties of the concrete.
These systems provide real-time monitoring of concrete consistency and temperature, with advanced features such as remote access of data linking to batching plant records for controlled water or admixture addition and extrapolating the data to predict the performance of the new mix.
Curing checks
Concrete strength development is another construction stage where digital innovation is disrupting conventional methods.
Strength following a concrete pour is predicted by measuring the temperature of the placed concrete to determine its maturity, which is a function of temperature and time. This process can be undertaken remotely using temperature data collected using sensors placed within the concrete element.
Preliminary laboratory work is required to establish a relationship between strength and maturity but, once calibrated, the data from the sensor can be used to calculate the strength. These sensors work by sending the data wirelessly to an internet-based cloud storage platform, enabling remote access through an online web portal.
Productivity benefits
One key benefit of the technology is that greater understanding of the concrete maturity enables formwork to be undertaken at the earliest possible point.
There are other benefits too. The extended monitoring of concrete maturity from the sensors can also support the reduction of concrete cube sampling for identity testing. This is made possible by comparing the database of seven and 28-day maturity index for concrete with standard cube strength results. This approach provides confidence about using digital maturity monitoring systems for concrete compressive strength compliance.
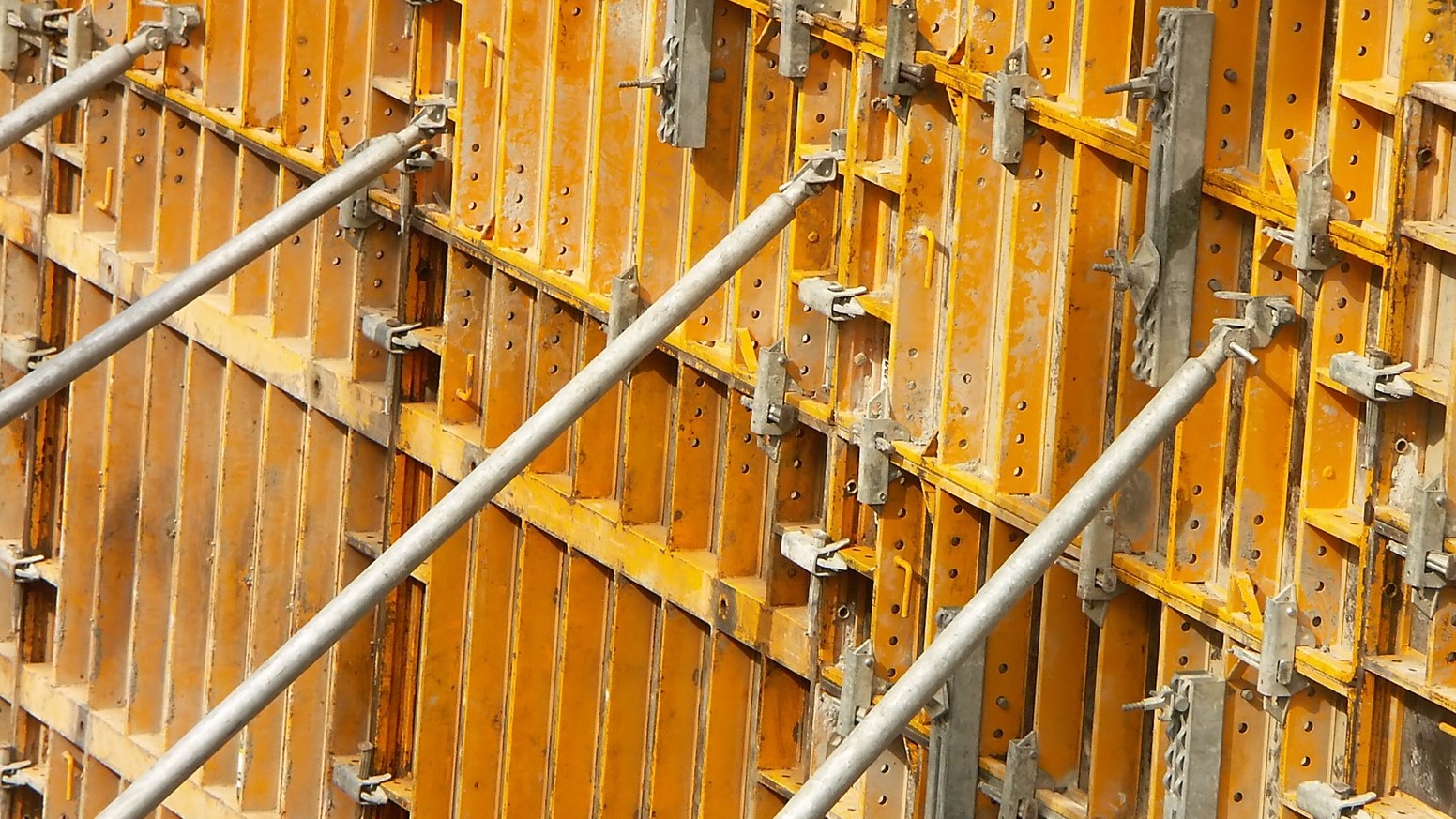
In addition, the technology allows for early detection of issues related to the pour, which is critical to quality assurance and achieving the design life of the structure.
Such systems can be used to check the compliance of thermal plan requirements in mass pours, monitor core temperature of concrete and identify risks of thermal cracking in hot and cold weather conditions. The temperature and maturity data provides certainty that larger pour volumes or bigger pour lifts, which aids the pace of construction, are not impacting on quality.
When it comes to the long-term durability of the concrete, the sensors also provide data that assists with assurance that the risks have been minimised.
As an example, sensors showing excessive temperatures can point to delayed ettringite formation during the first stages of cement hydration, which in the longer term can result in a deterioration mechanism that causes cracking and spalling. Temperature monitoring during the curing phase means that action can be taken to ensure specification limits are not exceeded.
Operational monitoring
Concrete resistance to reinforcement corrosion is one of the crucial parameters that impact the long-term durability of concrete and can be monitored by using corrosion sensors, such as anode-ladder sensors.
This technology monitors the progression of deterioration in the concrete cover zone, which can be extrapolated to estimate the timeline for the initiation of reinforcement corrosion.
Real-time digital surveillance of concrete durability using corrosion sensors in critical locations of the structure can aid in predictive repair and maintenance of an asset.
Future development
The last decade has seen a rapid increase in the range and capability for concrete surveillance technology and that pace of change looks set to be just the start.
Recent advances in digital technology, cloud computing and artificial intelligence create the potential to integrate different monitoring modules to a common platform to improve decision-making at every stage. If these technologies are applied at production, construction and operational stages, concrete structures can give clients real-time insight into performance over the whole life of the asset.
This capability will enable clients to build more sustainable and durable structures that are constructed and managed more efficiently than has been possible in the past. Nonetheless, having a clear understanding of how to interpret and analyse the data provided at each of these stages will be key to gaining full insights into asset performance.
Sudarshan Srinivasan is a principal materials engineer at Mott MacDonald.