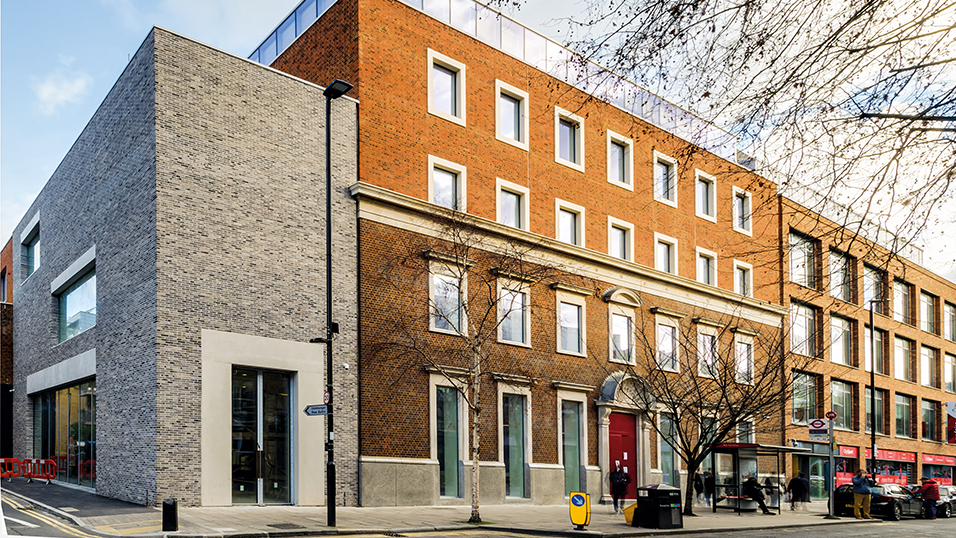
Making a beautiful new office from two decrepit buildings is no mean feat. But both developer and contractor insist the pain was worth the gain, reports Kristina Smith.
Once a bank HQ and gin distillery, the new Technique building in London’s Clerkenwell is now a high-quality office space, light and airy with environmental credentials to die for. Walking round site, it is impossible to imagine how this dream environment emerged from the scenes revealed in construction photos from the two-year build.
As Graham Construction project manager Jamie Tombs talks though some of the issues he and his team have dealt with, he frequently punctuates his account with “but it was worth it”. And he genuinely means it. Because what he and developer General Projects share is a love of buildings and building technology – which is at the heart of this rebirth.
Technique building – project team
Client: General Projects
Contractor: Graham Construction
Architect: Buckley Gray Yeoman
Structural engineer: Heyne Tillett Steel
Gross development value: £80m
Construction cost: £20m
Form of contract: JCT Design and Build
Programme (on site): January 2020 to February 2022
Key specialist contractors:
Piling: GSS Piling
M&E: Michael Nugent
CLT/glulam frame and steel structure: B&K
Lifts: Stannah
Glazing and curtain walling: Anglian Architectural
“We wanted to use what was there,” says General Projects’ development director Frederic Schwass. “To celebrate what’s there and to extend it.” So, the existing concrete has been sandblasted to expose the aggregate, with missing lumps and formwork joins now features to be admired.
By using a combination of cross-laminated timber (CLT) and glulam for the third and fourth floors of the building, General Projects has boosted the floor area to 74,000 sq ft of top-notch space with 5,000 sq ft of small, affordable units in the basement. The timber members are left exposed, lightly whitewashed, promising biophilic benefits to workers on the upper floors – as do the blue-green roofs around the stepped-in upper floors.
CLT and glulam also worked wonders for the building’s sustainability, with the timber embodying around half the carbon that a steel frame would, according to structural engineer Heyne Tillett Steel (HTS). Occupiers won’t look at less than BREEAM Excellent, says Schwass.
There is a downside to timber frame though: the cost of construction insurance, which Schwass says is 2.5 times higher than for steel or concrete. And the frame did require a little help from steel just here and there.
Who gets the risk?
Though not the first project on site, Technique was the first project the developer won, after it was set up in 2016 with a mission to breathe new life into ageing buildings. Had General Projects not been approached by the owners – private investors based in London – the two 1960s buildings could very likely have been razed to the ground.
“Knocking a building down is miles easier, miles quicker but you won’t have the same characteristics,” comments Tombs.
One of the thorniest issues for General Projects and Graham in agreeing a contract back in 2019 was how to apportion the risk of working with an existing structure. “One of the biggest issues is always structural risk, and how much the contractor is willing to accept,” says Schwass. On Technique, Graham was able to shoulder the risk, but only after carrying out extensive investigation work to assess the state of the frame, which is steel wrapped in concrete.
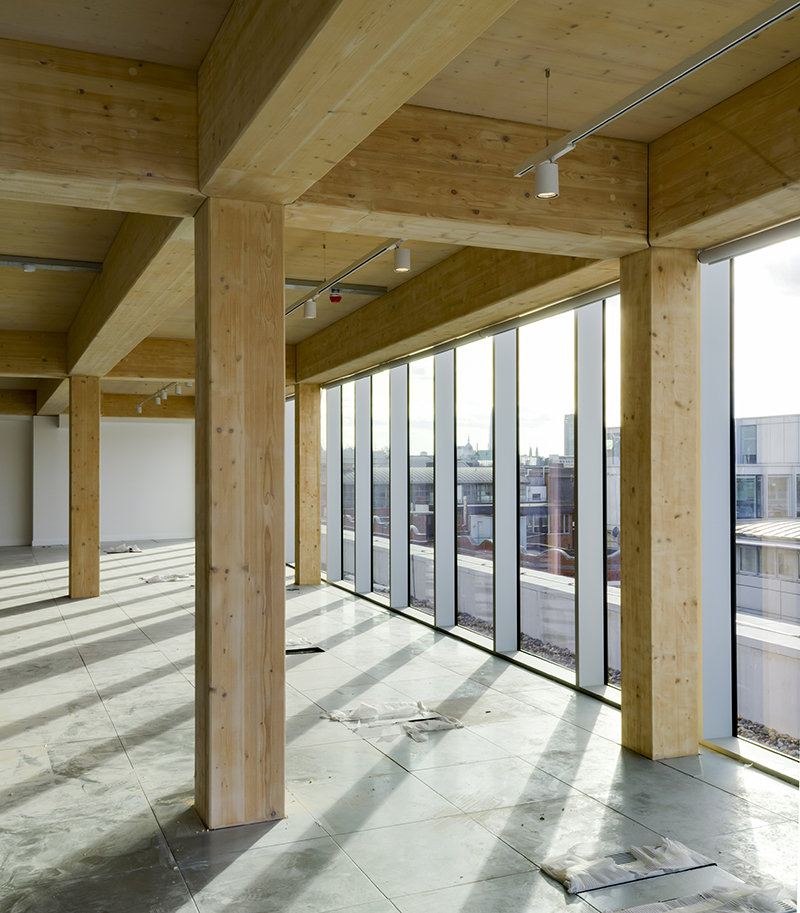
“Some of the steels inside the frame were not strong enough,” says Tombs. “HTS had made assumptions on the size of the columns based on previous history and drawings, but we had to open them up to see what was there and what we needed to do to take the CLT and glulam frame.”
The buildings sit on an ‘L’ shaped plot, with the ex-bank HQ fronting Goswell Road and the old distillery – which has also been a printworks – running perpendicular to it along Pear Tree Street. The corner spot, once a pub that was bombed during the Second World War, was a car park.
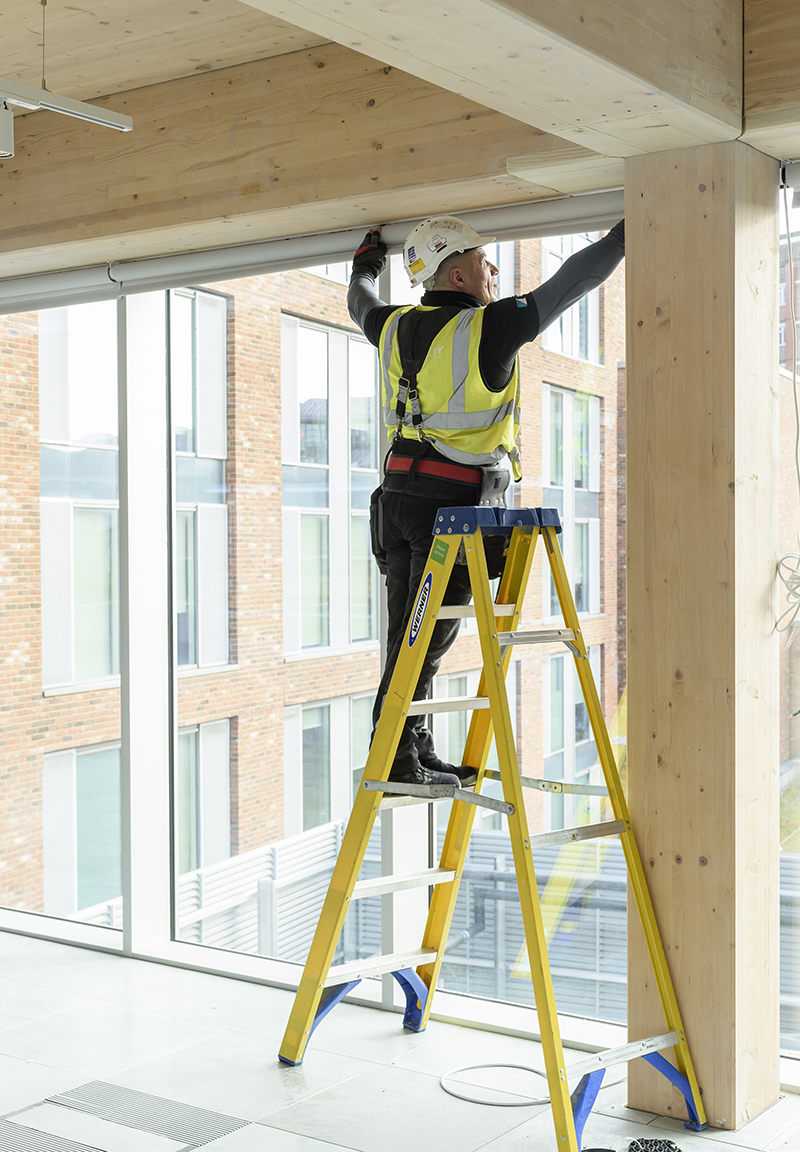
The two buildings had been joined together after a fashion, but the Technique project sees a new, three-storey concrete-framed linking lobby built on the corner plot, the footprint extended in two areas with steel frame structures, and two new timber-framed storeys added to the top of both buildings. That may sound relatively straightforward, but it wasn’t. There was demolition, repair, structural modifications, old and new and some interesting materials. “This project is a tricky one,” says Tombs, who has over 40 years’ construction experience. “It has everything.”
If Tombs had to pinpoint the biggest technical challenge, it would be the forensic work required to protect the existing building as the structural changes were made to it, he says: “It’s understanding what you are going to do to the building and how that’s going to affect the building. If you have to cut out a column that’s 80 tonnes, how do you support it and replace it with a load-bearing structure?”
It was the position of the new lift shaft that required the removal of that 80-tonne column and a large portion of the pile cap below it, with loads transferred onto a goal post frame. “That required extensive temporary works,” says Tombs.
Before that operation, Graham had to remove some of the buildings’ load while adding foundation support. With structural investigations done and preliminary sums tightened up, Graham started work from the top and bottom simultaneously, with mini piling in the basement. Meanwhile demolition of some of the upper floors was underway to create a level base for the CLT frame. Floor screeds were removed throughout to make way for lighter precast planks on the lower floors.
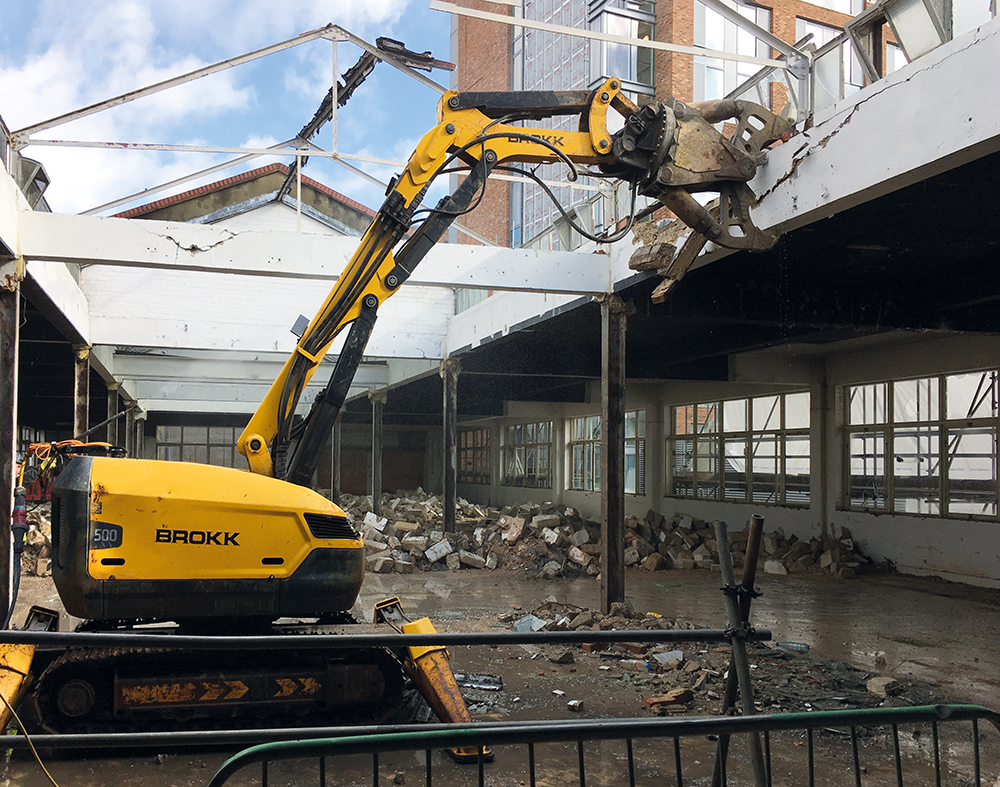
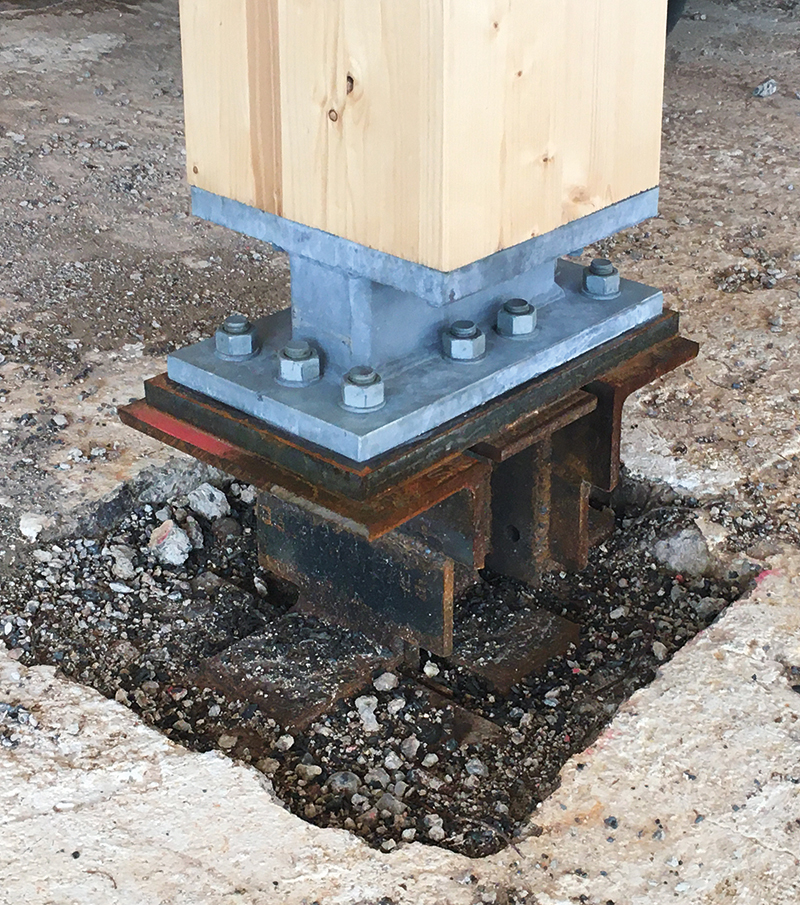
There are also new piles for the lobby, which has a jaw-dropping two-storey gallery above, requiring the sacrifice of 800 sq ft of lettable space. “In creating an interesting space, we lose the value of the floor space, but it adds value to the rent of the whole floor,” explains Schwass.
In Clerkenwell, where creative and tech firms rub shoulders, buildings need some arty ‘wows’. So, parts of the lobby are clad in tiles made from volcanic ash from Mount Etna and designed by Amsterdam-based Formafantasma, design darlings of the moment. The tiling, which adorns parts of the reception area, showcases the craft of the tilers too, who worked from a picture only.
The bricklayers are also to be admired. In a move agreed by the planning authority at the 11th hour, General Projects specified StoneCycling bricks, hand-thrown in the Netherlands from recycled materials. The tolerance on the bricks was huge, says Tombs, but no one would know, looking at the wall now.
Strengthening works to the existing frame took a variety of forms. Some columns were stripped of concrete so that steel plates could be added before the concrete was replaced; some gained additional rebar; a few were wrapped in carbon fibre with a concrete-coloured grout applied on top.
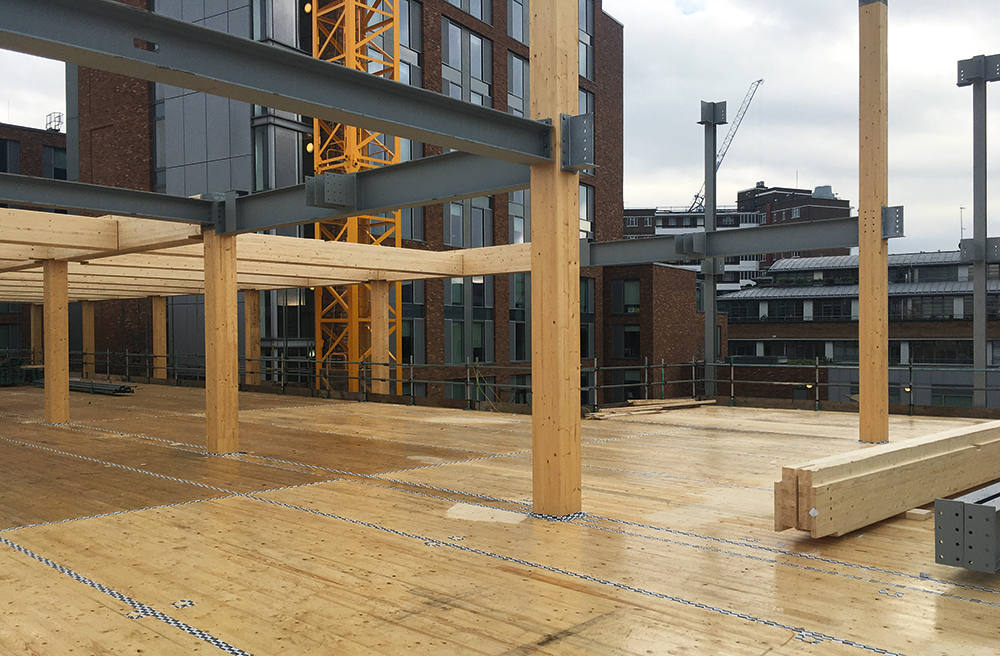
The design of the timber frame, which Graham subcontracted to specialist B&K along with the steel frame for the extended areas, wasn’t plain sailing either. When B&K did the detailed design and calculations, it discovered that a few of the members were not strong enough; they had to be beefed up with steel, which was then encased in timber.
With modifications made to the top of the existing columns to create connections, B&K installed the frame in 12 weeks. “It was just like a big Meccano set,” says Tombs. While B&K did its Meccano, M&E specialist Michael Nugent was busy on a 3D puzzle. General Projects wanted clean lines for the upper floors, which meant drilling holes through the existing steel beams. “Extensive design work was required so the frame could take the penetrations,” says Tombs, with Michael Nugent creating a model in Revit.
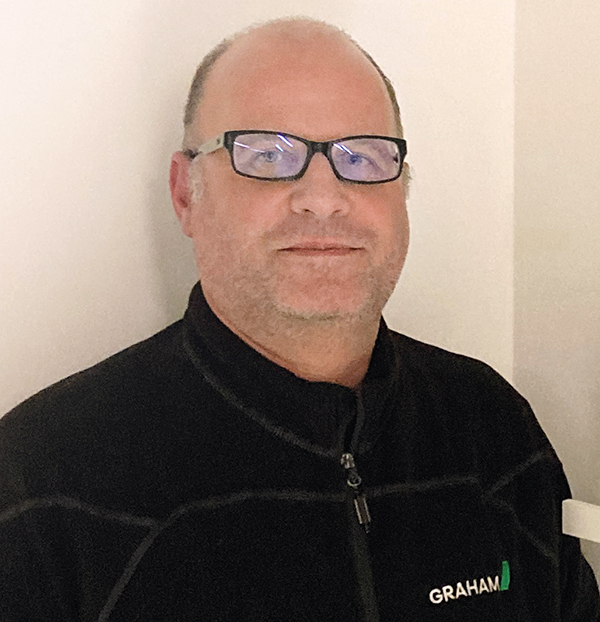
Construction manager CV: Jamie Tombs, Graham Construction
If there’s one vital ingredient for a complex refurbishment like Technique, it’s experience. Fortunately, Graham Construction’s project manager Jamie Tombs has it in spades.
He began his construction career with Bovis in 1988, gaining bachelor’s and master’s degrees while working. After 10 years with Bovis, he went on to work for several main contractors, mostly on commercial projects, and has been with Graham since 2018.
Tombs is delighted that his daughter is following in his footsteps, having just started an apprenticeship in construction.
Heating and air conditioning for the upper floors is housed in a plenum, which makes the space more flexible too, explains Schwass. Achieving air-tightness for the plenum was another challenge, says Tombs, requiring patience and many smoke tests before all the gaps were found and plugged.
Ready for tenants
Technique’s technical hurdles were complemented with some logistic and community ones too. The risk of Brexit impacts meant Graham had to bring in its final CLT and glulam consignment early, causing a storage headache. For General Projects, the project had a very long gestation period as it worked to keep its residential neighbours happy. Tombs says relations with neighbours have been good. Graham has kept them informed of what’s happening when, stuck to agreements such as limiting noisy works to two hours with two-hour breaks, and modified the agreed closure of Pear Tree Street so residents could use it in the evenings.
Having happy neighbours has helped General Projects secure later planning consent for two roof terraces on the upper floor among the blue-green roofs. Post-pandemic, outside spaces are ultra-desirable. There are also outside terraces at the back of the building on the second floor and basement levels, where the removal of part of the floor above has delivered a small courtyard and natural light for the affordable units.
When CM visited site in early February, Schwass was hoping that there would soon be news of a tenant for the building. Practical completion was planned for the end of the month, with Graham inviting General Projects’ landscaping and IT contractors in to work in parallel with them, rather than after handover as was programmed.
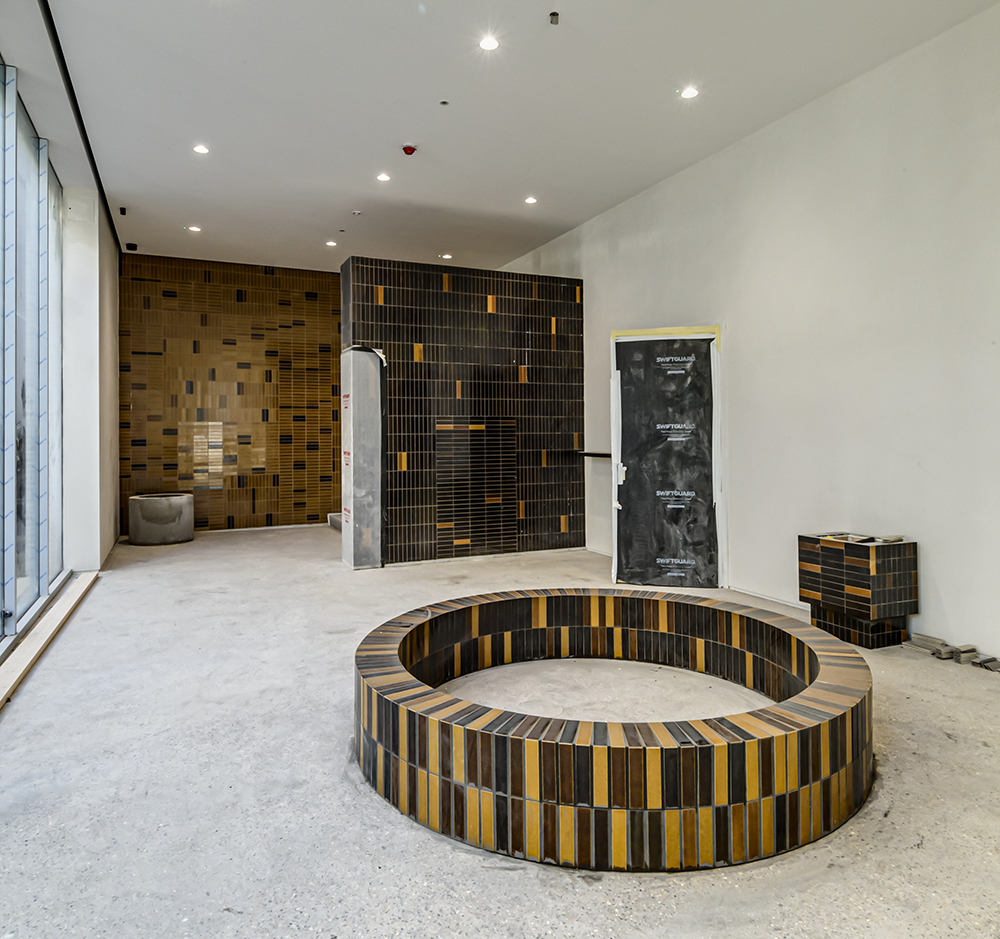
The project has run longer than planned, in part due to Covid absences and disruption which caused four weeks’ delay. There have been additional works too. The original programme was 20 months, but it has stretched to 24.
For Schwass, quality is everything and this goes for the building’s owners too. “Given that they are looking to hold onto it for a long time, the most important thing for our client and for us is that we get a beautiful building that it is high quality,” he says. “There are too many developers who only care about returns. I personally would never develop or manage a building that I would not stand for or be proud of.”
Comments
Comments are closed.
A most impressive story in every aspect. I don’t underestimate the challenges that were encountered and the work that must have gone into overcoming and managing them.
The successful relationship between Client, Architect and Contractor shines through. The supply chain relationship must have been vital to the success. This is real Building!