The coronavirus field hospitals presented a construction challenge like nothing before. Will Mann talks to the project managers on three of the hospitals, starting with Dragon’s Heart in Cardiff, where Mott MacDonald led a team including events specialist ES Global.
The Principality Stadium in Cardiff normally provides the backdrop to Welsh rugby internationals. In March, it was picked as the venue for a different kind of test – as one of the ‘field hospitals’ which were hastily being constructed for coronavirus patients around the UK.
Dragon’s Heart, the name chosen for the facility, was unusual in requiring construction of a tented area inside the stadium to accommodate the clinical facilities. Its construction team was unusual too. Consulting engineer Mott MacDonald led the project team and gave the contractor job to a non-construction firm, events specialist ES Global.
Related
Ciaran Willcocks, project director at Mott MacDonald, takes up the story: “We got the phone call at 3pm on Sunday 29 March. Over the next 12 hours, we pulled together the project team and the supply chain for the project. We were on site at 8am on Monday morning the next day with ES Global as contractor and architect BDP.
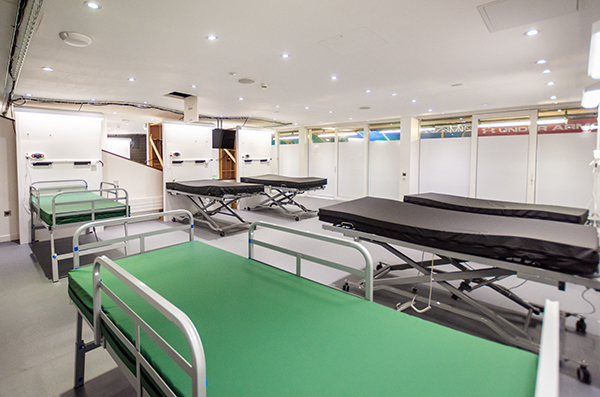
Project team
Project managers: Mott MacDonald, Archus
Main contractor: ES Global
Architect: BDP
Structural engineer: Momentum
M&E engineer: Hoare Lea
Tent installation: Nine Yards
“On that Monday, we talked through the project with various stakeholders, including the Welsh government and NHS Wales. We agreed that by the end of that day, a decision had to be made on the scope of the hospital so work could get underway the next day. The CEO of NHS Wales gave the go-ahead at 6pm.
“We took that as formal confirmation and mobilised the team to start work the next morning, Tuesday 31 March. We received our letter of authority on Friday 3 April. NHS Wales deserves credit for making the decision on the spot and issuing a substantial letter of credit to a contractor they’d never heard of before – ES Global – to the tune of £2m.”
But Willcocks was confident the events contractor could deliver, having worked with ES Global on the shooting venue for London 2012 at Greenwich Park and the velodrome at the 2018 Asian Games in Jakarta, Indonesia.
“The major difference with Dragon’s Heart was constructing the tented overlay space, which was not a require-ment at other hospitals like ExCeL.
“This falls within the purview of ES Global, but not the traditional construction contractor. We’ve had to source one of the biggest tents in Europe for Dragon’s Heart, and construction contractors wouldn’t have the contacts and knowledge for that job.”
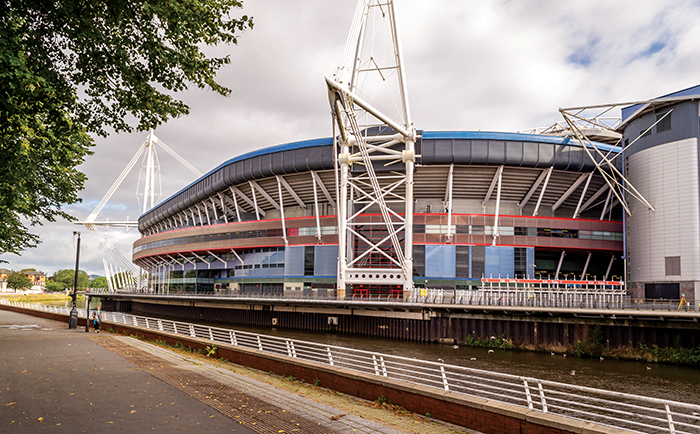
Jeff Burke, owner of ES Global, explains the company’s approach: “Our mobilisation plan went hand in hand with the design; one depended on the other. We mocked up three or four possible tent layouts on the pitch first; we needed to understand how different arrangements could work depending on what products were available in the market the next day.
“This is a pragmatic approach which we’re very used to, and it ensures we can deliver projects quickly, rather than being delayed waiting for a specific bit of kit.”
Modular solution
The design and construction planning were necessarily condensed, a process that would normally take two years completing in five days, Willcocks explains. Where possible, modular construction was used.
“Most of the units are temporary plug and play, including air-handling units, chillers, scaffolding and tents. We used a standard 2m x 1m panel to build all headboards and bed partitions, and we’ve installed 6,000 of those on the site.
In numbers: Dragon’s Heart Hospital
- 2,000 – maximum bed capacity
- 15,000 sq m – area of medical overlay tent
- 300km of cabling
- 80 tonne – weight of main oxygen tank
- 14,000 sq m of flooring
- 10MW of extra generator capacity
“The biggest tent measures 150m by 50m and there are also four smaller tents, roughly 150m by 24m, and three around the edges, each about 100m by 10m each. Altogether, that is 15,000 sq m – around eight times the size of the Glastonbury main stage.
“These were assembled using a 100-tonne crane, plus an army of skilled operatives at pitch level, then a single cherry picker put the final bolts in. There was almost zero working at height.”
However, the M&E provided a major technical challenge, Willcocks says.
“There are no M&E connections whatsoever under the pitch so we had to bring in our own – water, waste, oxygen, power, heat, cooling. We’ve installed 10MW of generators inside the stadium –enough to power 15,000 homes – on top of the stadium’s existing 3.3MW of capacity. All this kit stands on scaffolding around the covered tented area on the edge of the pitch. There are also hundreds of cables and pipes feeding into the hospital, including water pipes 10 inches thick.

“Oxygen has been the limiting supply factor – valves, terminals, fitters are all in national shortage, and most of all, the main oxygen control panel. We’ve put in an 80-tonne main supply tank and a 40-tonne ancillary oxygen tank.
“A massive amount of brand-new ducting has been put into place. Installing the air handling was a major challenge. We fabricated these huge steel ducts, 3m x 3m in diameter, which had to be ‘flown’ over the tents and suspended from the stadium roof.”
Dragon’s Heart also makes use of space under the stands, Willcocks explains.
“The concourses under the stands have been converted into wards, and we had to board off the vomitories with acoustic panels, then connect ductwork into this area so we could create a temperature-controlled space.
“The home and away dressing rooms serve as office spaces, the waste compactor room has been converted into a lead-lined CT scanner room and fully functional blood laboratory, the press box is used for project management meetings and I used the police cell when I had to make a private call.”
Social distancing strategy
Bringing together a site workforce of over 1,000 and delivering the work within a tight timeframe while maintaining social distancing protocols has been a challenge, admits Willcocks.
“Finding the skills needed in those numbers was difficult. We’ve worked 24/7 using a shift pattern but we couldn’t fill night shifts for some of the work packages like fit-out – some 1,500 beds needed to be wired.
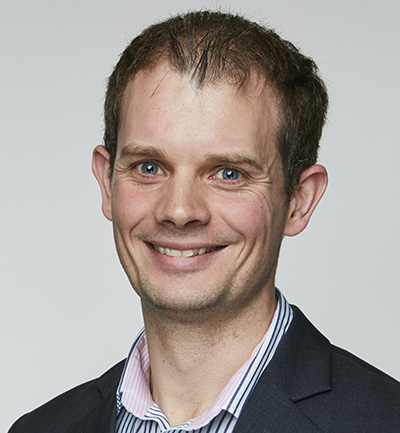
“We’ve installed enough generators inside the stadium to power 15,000 homes.”
Ciaran Willcocks, Mott MacDonald
“The social distancing puts an extra layer of complexity and anxiety on everything, but people got used to it. With fit-out, we had electricians, pipe fitters, carpenters and plumbers all working in the same spaces – but also separated. And then this is complicated further when the army arrives to put the beds together hot on the heels of the final fit out.”
He says the site workers were “mostly” happy with the safeguarding measures.
“Clear communication from the NHS clinicians on site helped. We took workers’ temperatures every morning, had handwashing facilities everywhere, washed their clothes whenever they required it. We fed them 24/7 using a catering company that normally does rock concerts. We also opened up four hotels nearby where many of them are staying.”
Dragon’s Heart became an operational hospital on 21 April, with the first 300 beds in the stadium concourses. A further 1,200 in the stadium bowl opened on 8 May, though total potential capacity is 2,000, Willcocks adds.
“Nobody was happy that this needed to be built, but we’re glad to have been a part of it. It is one of the most interesting and gratifying engineering challenges I’ve ever had to work on.”