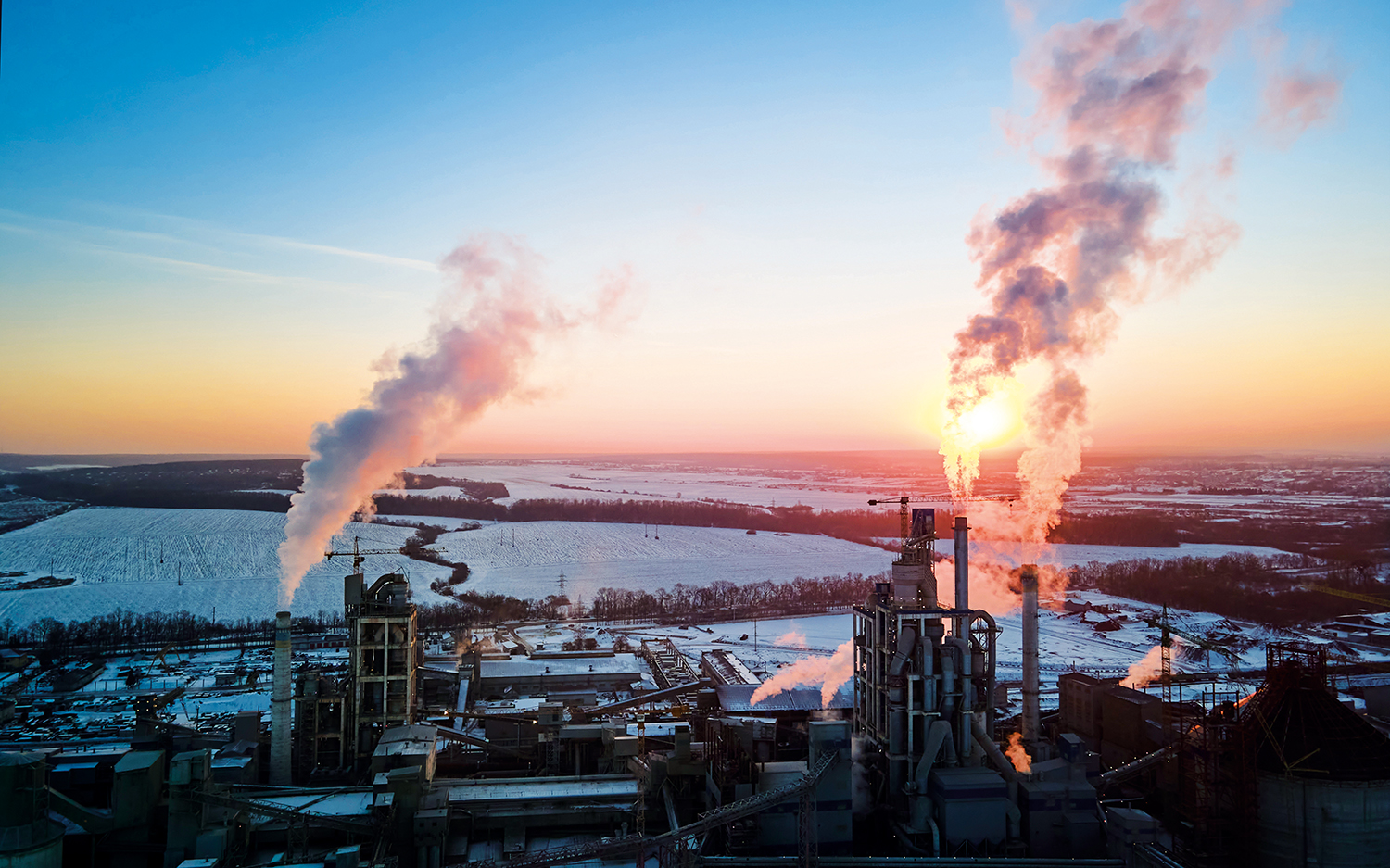
We know that timber sequesters carbon. Can concrete do the same? Kristina Smith meets the materials scientists trying to make it happen.
Whatever concrete decarbonisation roadmap you look at, carbon capture usage and storage (CCUS) accounts for a big piece of the pie.
In the UK, where producers have already done some of the easier carbon reduction work, CCUS will account for around 60% of carbon savings by 2050, according to the Mineral Products Association’s (MPA) decarbonisation roadmap, which it published in 2020.
Perhaps the most obvious form of CCUS for cement production sees carbon dioxide (CO2) removed from flue gases and then stored in an underground depository. Heidelberg Materials is doing this on a large scale at its Brevik cement plant in Norway, perhaps as soon as 2025, with a carbon capture and storage plant partly funded by the Norwegian government.
Combined with Norway’s plentiful renewable energy supply, this will result in what Heidelberg is calling “the world’s first carbon captured net zero cement”.
Locking CO2 into cement
But there is another way: to somehow lock some of the CO2 emitted from cement production into the concrete itself. This is an idea being pursued by scientists and startups around the world through a variety of technologies, in varying stages of development. These range from carbon curing to producing supplementary cementitious materials (SCMs) to creating aggregates.
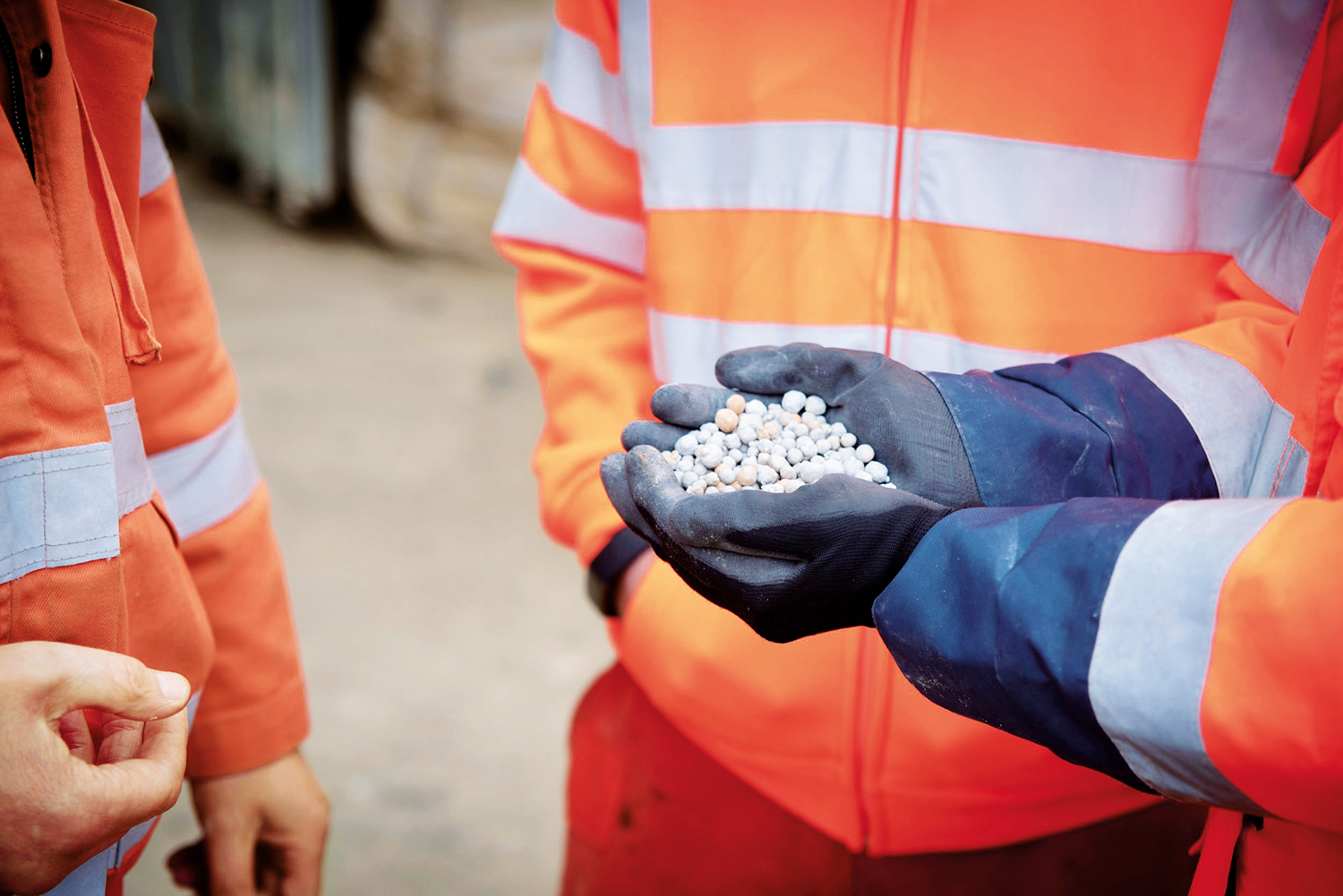
Contractors and their supply chains should be paying close attention to such technologies, suggests Marta Sjögren, co-CEO and co-founder of Nordic-Dutch startup Paebbl which has ambitious plans to create a portfolio of products that store carbon, starting with SCMs.
“Contractors should be thinking about how they can use this opportunity,” she says. “Carbon avoidance [or offset] credits are not very well known about because they’ve just started. But they could be a way to boost margins.”
Sjögren cites CarbonCure in North America which pays a proportion of its carbon credits to concrete companies. Paebbl will be looking at a similar system when it starts selling its technology.
Carbon curing
CarbonCure, founded in Nova Scotia in 2012, is further ahead in commercial terms than many of the others in this arena.
Its technology, which can be retrofitted onto existing concrete plants, sees CO2 injected under pressure into concrete wagons where it reacts with the concrete to form calcium carbonate and hence becomes permanently embedded. This increases the concrete’s compressive strength which means that cement content in a mix can be reduced, according to CarbonCure.
CarbonCure says its process saves between 7 and 11kg of CO2 per cu m of concrete produced. That isn’t a huge amount, but it all adds up. CarbonCure’s website tells us its technology has saved 126,130 tonnes of carbon over the past year.
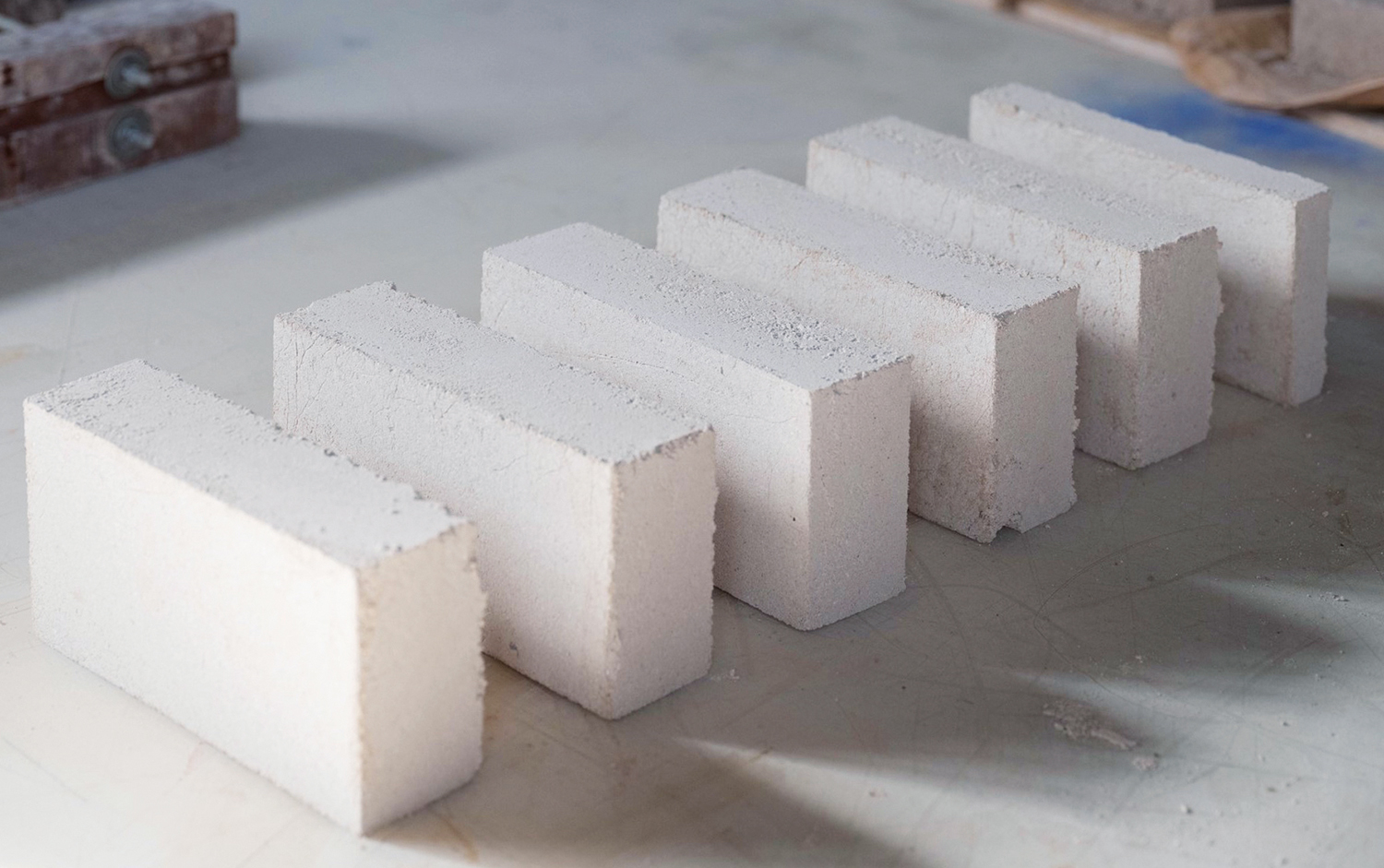
Another established company that uses carbon curing is Solidia. Its process combines its own low carbon SCM and carbon curing in a special chamber to create precast elements which Solidia says can reduce their carbon footprint by up to 50%. The company is creating its first plant at its Texas headquarters.
Canadian firm CarbiCrete deploys slag rather than portland cement in its precast concrete and again cures it in a special chamber with CO2. Carbicrete, which piloted its technology in 2018, says that the result is carbon negative concrete blocks, some of which are already being manufactured by Patio Drummond in Quebec.
UK company Carbon8, which was founded in 2010 and came out of the University of Greenwich, has developed technology to lock carbon into the aggregates used in concrete.
Carbon8 uses its accelerated carbonation technology (ACT) to combine wastes from industries such as cement, energy from waste, paper and pulp, steel and biomass with CO2 to produce an aggregate which it calls CircaBuild.
Lightweight aggregate
Carbon8 has developed its solution so that it can be accommodated in a container which can then be easily transported and installed at an industrial site.
Its first commercial deployment began in summer last year at Vicat’s Montalieu cement plant in southern France, capturing CO2 from the plant’s flue gas and using it to convert cement bypass dust into lightweight aggregate which could then be used in concrete block production.
Last year CCP Building Products used CircaBuild with its Greenbloc technology, which uses a non-portland cement binder, to produce trial concrete blocks. According to CCP, which is part of SigmaRoc, the blocks produced are carbon negative, accounting for 110% less carbon than one made with 100% ordinary portland cement and with the possibility of increasing that to 125%.
Carbon8 announced it will also run a pilot project at an energy-from-waste plant in Duiven in the Netherlands. Aggregate produced from fly ash waste will be turned into aggregate which will then be tested for compliance with construction industry standards.
Paebbl and UK startup Seratech are at the beginning of their development journeys. Their technologies are somewhat similar, involving the combination of olivine – a naturally occurring magnesium iron silicate – with carbon dioxide.
Founded in 2021, Paebbl and its backers see the commercial potential of investing in this field. Its first step is developing a process to combine CO2 with olivine to create a silica-enriched magnesium carbonate which can be used as an SCM.
Magnesium silicates
The magnesium silicates in the olivine react with carbon dioxide under a pressure of 50 to 100 bars at a temperature of between 100 and 200 deg C, which would be provided through renewable energy, says Sjögren.
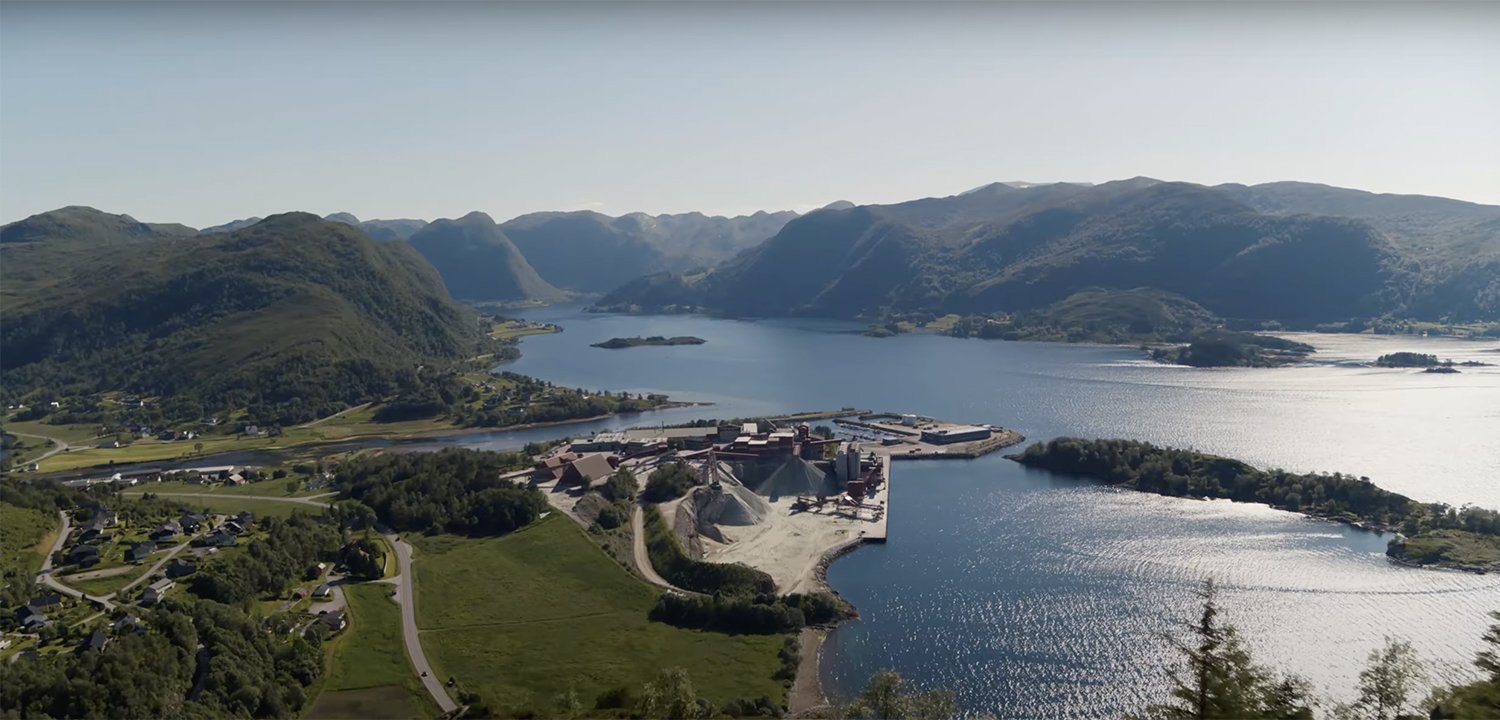
“So far, we have shown that it can be used in all non-structural concrete classes and in a couple of structural classes, from early results,” says Sjögren. “We hope to develop it for
all classes in a couple of years.”
Paebbl’s November 2023 news was that it had stepped up its processing from the laboratory to a 500-litre batch production unit. Its next step would be to scale up 10 or 20 times to create a continuous plant by the end of 2024 with the goal of producing a first-of-a-kind (FOAK) commercial plant by 2027 or 2028.
The process currently works with almost pure CO2. “Between 80 and 100%, the performance is pretty stable across the board,” reports Sjögren.
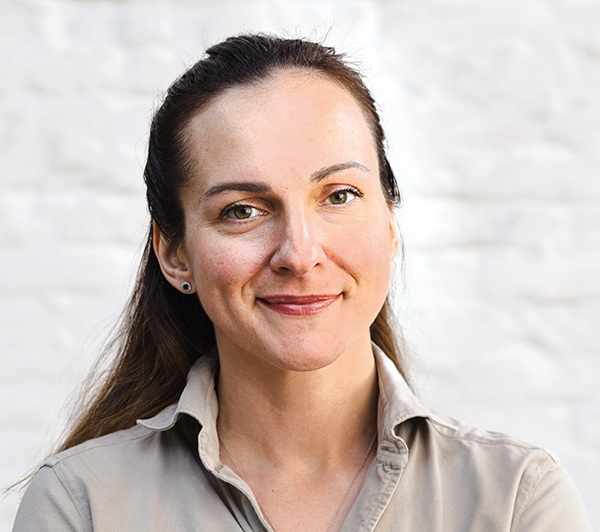
“Contractors should be thinking about how they can use this opportunity.”
Paebbl is working with SeaO2, which captures and purifies CO2 from the sea. “Our goal is to prove it works even with these low efficiency sources of CO2. If you prove economics work at this level, it definitely works with flue gas,” says Sjögren. After that, Paebbl will turn to flue gases from waste incineration plants which contain a high proportion of CO2.
The Seratech process also sees the combination of olivine and CO2 but is designed to work with any flue gases containing 10% or more CO2. Unlike Paebbl’s process, Seratech’s patent-pending system sees the resulting silica and magnesium carbonate separated.
Net-zero carbon concrete
The silica can be used as an SCM, with a mix which sees around 35% of portland cement replaced, performing similarly to a standard 40MPa concrete. At just over 35%, concrete produced with the SCM would become net-zero carbon, says Seratech CEO Sam Draper. The company plans to publish a life cycle assessment later this year.
Paebbl is about to tender for the delivery of its first pilot facility, a plant that will run continuously, sequestering 100 to 200 tonnes a year. Assuming that it can raise the necessary funding for the build, that could be up and running by mid-2024.
Meanwhile, Seratech has been working on trials to deploy the magnesium carbonate produced in the process in bricks. It says they only need to be baked at 60 deg C – as opposed to over 1,200 deg C for conventional clay bricks – before being left to cure at ambient temperature for up to two weeks.
“We have done some standard tests on strengths and durability of the bricks, which are all looking good,” says Draper. “We are continuing to refine the mix design to optimise performance and how you cure them.”
Now the goal is to create partnerships with brick and block manufacturers, Draper says: “This product could be used within existing technology, which is a key selling point of magnesium carbonate bricks. You don’t need to make any modification of the plants; you can run it through the same process. That’s what’s really big for us.”
Too much risk
With these companies and many others working on sequestering carbon into concrete, bricks and other materials, these technologies could provide a useful contribution to the CCUS element of the net zero journey. However, in the UK there are some big barriers to the adoption of such technologies.
At a very basic level, there is the issue of standards. There’s a reason why the US is adopting these technologies faster. “Here in Europe, we have been ‘recipe based’ for 30 years longer than the US In EU. But, as of 2025 we are moving to performance-based standards which will be a huge change,” says Sjögren.
In the UK, although BS 8500 was updated in November 2023 to allow lower carbon concretes to be specified, it is still largely recipe based rather than performance based, as are other related standards. It is possible to deviate – but that is expensive and time-consuming.
Market forces won’t be enough, warns Hannah Durden, managing director of CNZW Developments, who advises on the adoption of new low-carbon materials and carbon neutrality.
“There needs to be legislation forcing clients to specify more eco or carbon-friendly materials from government. We need to tax carbon emissions – look at how the EU’s emissions trading scheme is beginning to affect the cement and concrete industry. Wholesale adoption won’t happen without this,” she says.