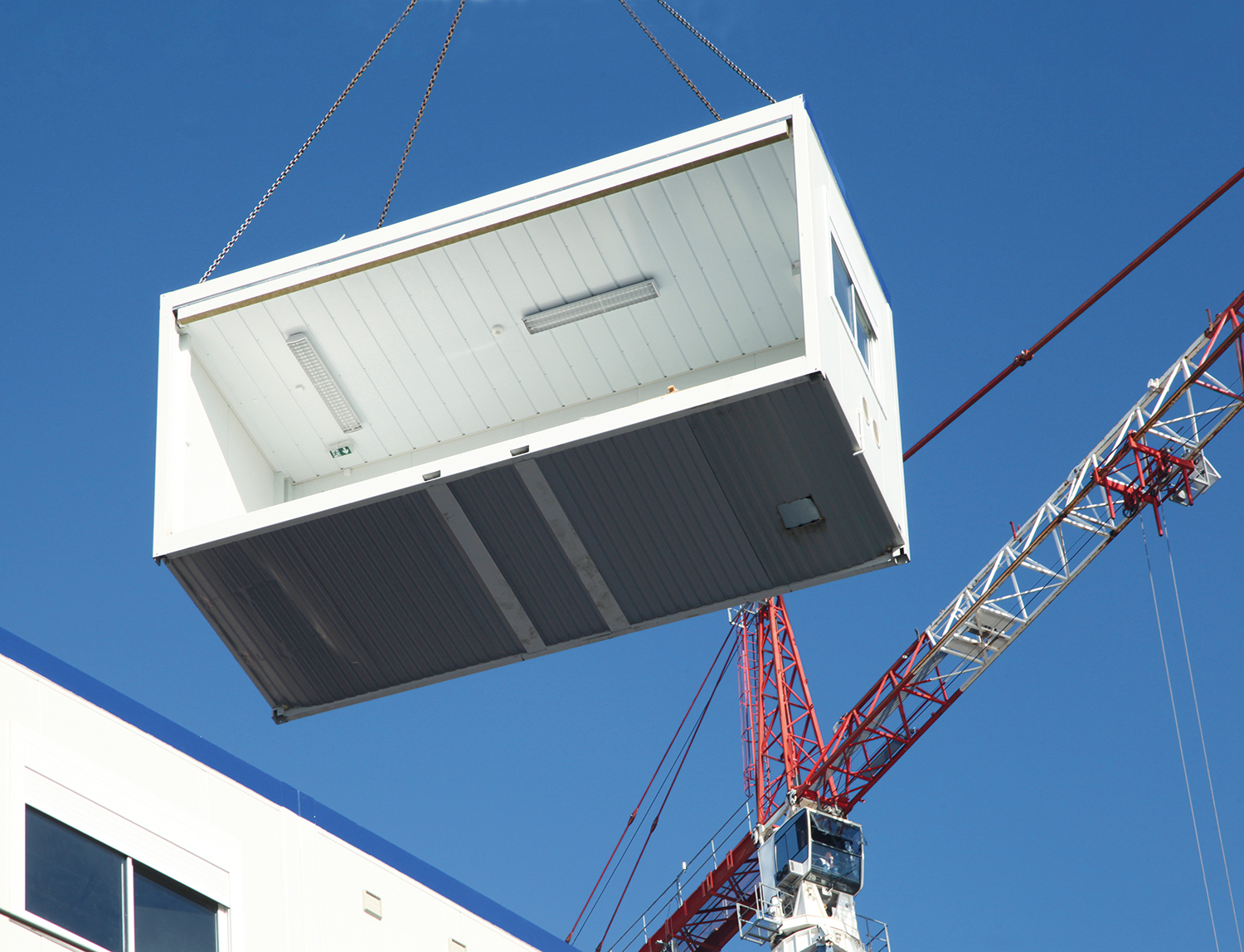
Is modular housing finally about to go mainstream – or remain a niche player? Kristina Smith speaks to trade body Make UK Modular and other industry players.
Depending on who you talk to, modular housing is either “the unsung success story of the construction industry” or “on a bit of a knife edge”.
The former view is that of Steve Cole, director of Make UK Modular, which represents seven modular housing manufacturers. The latter comes from David Johnson, director of preconstruction at Volumetric Building Companies (VBC).
According to Make UK Modular, which is part of manufacturing trade body Make UK, 3,300 modular homes were built in the UK in 2022. And it says that its members are on track to produce 10,000 homes a year by 2025. Between them, those members (see box) account for over 70% of the UK’s modular housing market.
VBC, founded in Philadelphia in 2009, is a new entrant to the UK market which is looking to expand further in the US and in Europe. Having recently purchased Polish steel modular company Polcom and the assets of failed US modular builder Katerra, it hopes to work in a variety of sectors in the UK, including build-to-rent, affordable housing and student accommodation.
Into administration
Johnson’s more cautious view of the wider industry is well informed. He was preconstruction director at Caledonian Modular until March 2022 when it went into administration, shocking many. Andy Smith, also ex-Caledonian, now heads up VBC in the UK. “We went into administration with the largest order book that an MMC company had secured, £300m with well-established clients,” Smith recalls.
But Caledonian suffered because it was underfinanced, he says.
Make UK Modular members
Ilke Homes
Legal & General Modular Homes
TopHat
Laing O’Rourke
Vision Modular Systems
Stelling Properties
M-AR Offsite
“There was a massive drive for revenue generation that led to corners being cut in terms of getting product signed off and ready for manufacture, and rushing through the manufacturing process and not delivering it very well on site. That was an individual business failure rather than a sector failure.”
Getting the right volume of work is a tricky business for modular suppliers. Too little and you can’t pay the bills. Too much, and standards can start to slip.
In May 2022, Urban Splash Modular, a joint venture between Urban Splash, Sekisui House and Homes England, went into administration. A report into the failure cited underutilisation of the manufacturing facility and design issues as the main factors leading to the company’s demise.
Deep pockets are a must for anyone wanting to make it in modular in the UK. VBC has the backing of private equity company Pimco. The likes of Legal and General, Ilke and TopHat are also well financed and investing significantly, while forecasting returns in the longer term.
The case for modular
There are lots of reasons why it could make sense to use modular to increase our housebuilding output. Make UK Modular’s latest report, Who Will be the Builders?, published in March 2023, focuses on how building more modular houses could help counter labour shortages.
Modular homes require fewer people to build them, and the workforce can be drawn from a more diverse pool since it doesn’t require people to be able to move from site to site, following the work.
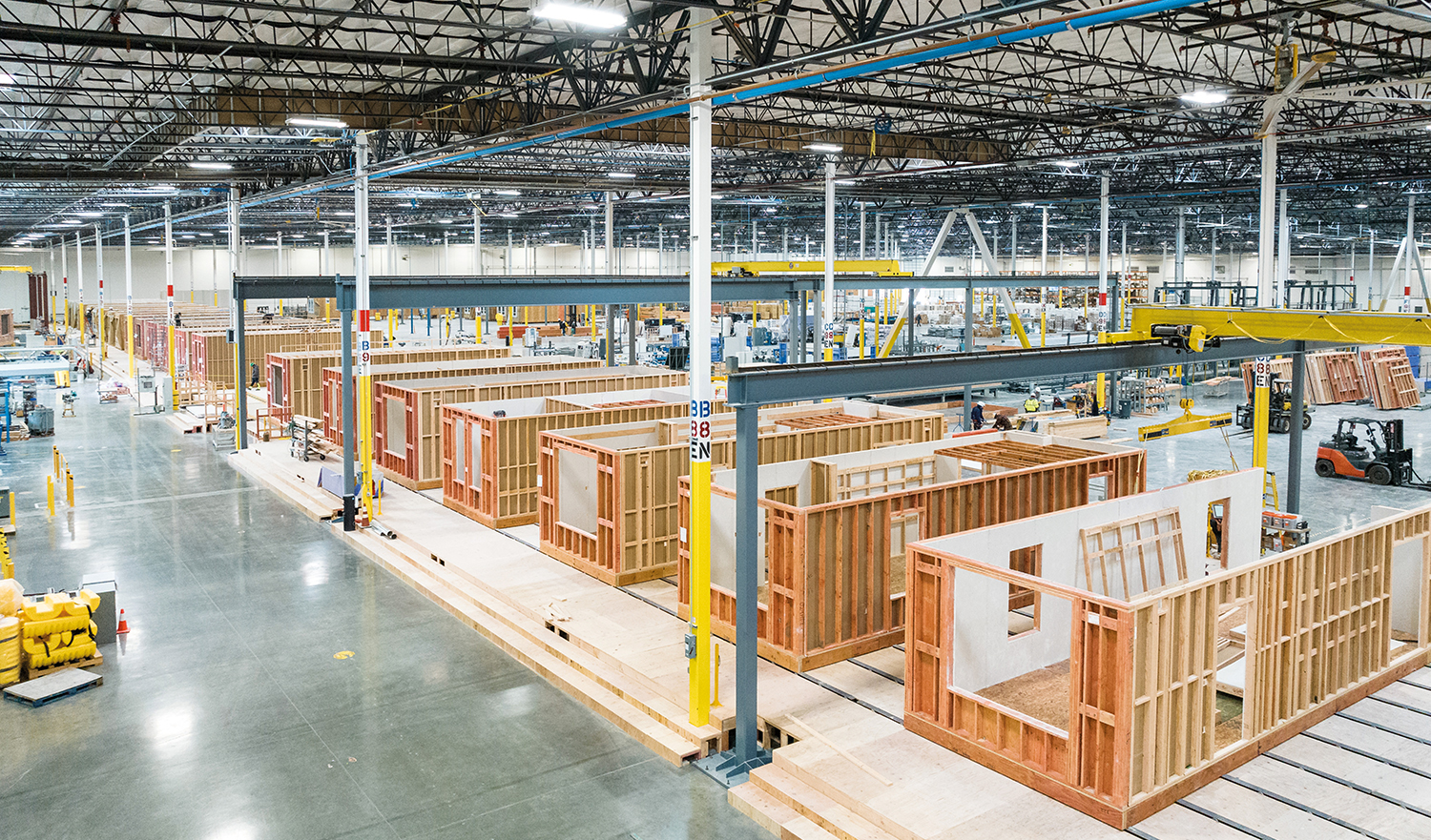
Clearly, modular makes most sense when speed to market is key. For instance, developments such as Greystar’s Greenford Quay (see p30) for the private rental sector or affordable schemes such as Cunninghame Housing Association’s 101-home development in Kilmarnock (see p31).
“The big gains in modular are in speed and quality but the cost is competitive,” says Cole. “We’re seeing that as companies mature.”
Johnson reckons that with a decent scale of building – say 50 homes or upwards – modular can deliver cost parity with a traditional build.
But, he says, there has to be a compelling reason why modular trumps traditional. This could be a constrained site where a modular build works better or a region, such as the south west, where labour is in very scarce supply.
As the carbon market emerges, modular homes could offer advantages. It is easier to produce lower carbon homes – both in production and operation – in a factory environment, argues Cole. Ilke Homes has a zero carbon homes brand, Ilke Zero, which is being deployed to build the first ever guaranteed zero energy bills homes in Essex (see p31).
Hurdles to clear
The biggest challenge for companies is how to ensure that steady flow of projects. Put bluntly, the UK modular housing industry needs more volume, and it needs it soon.
Planning, though a problem for all housebuilders, is more of an issue for modular schemes. “There is a lack of resource in the planning system and then you add into that unfamiliarity with modular construction. That’s a problem when one of your major benefits is speed,” says Cole.
In the US, a different approach helps to deliver greater efficiency, says Smith. There VBC sells a pre-designed solution which means the planning process is far quicker.
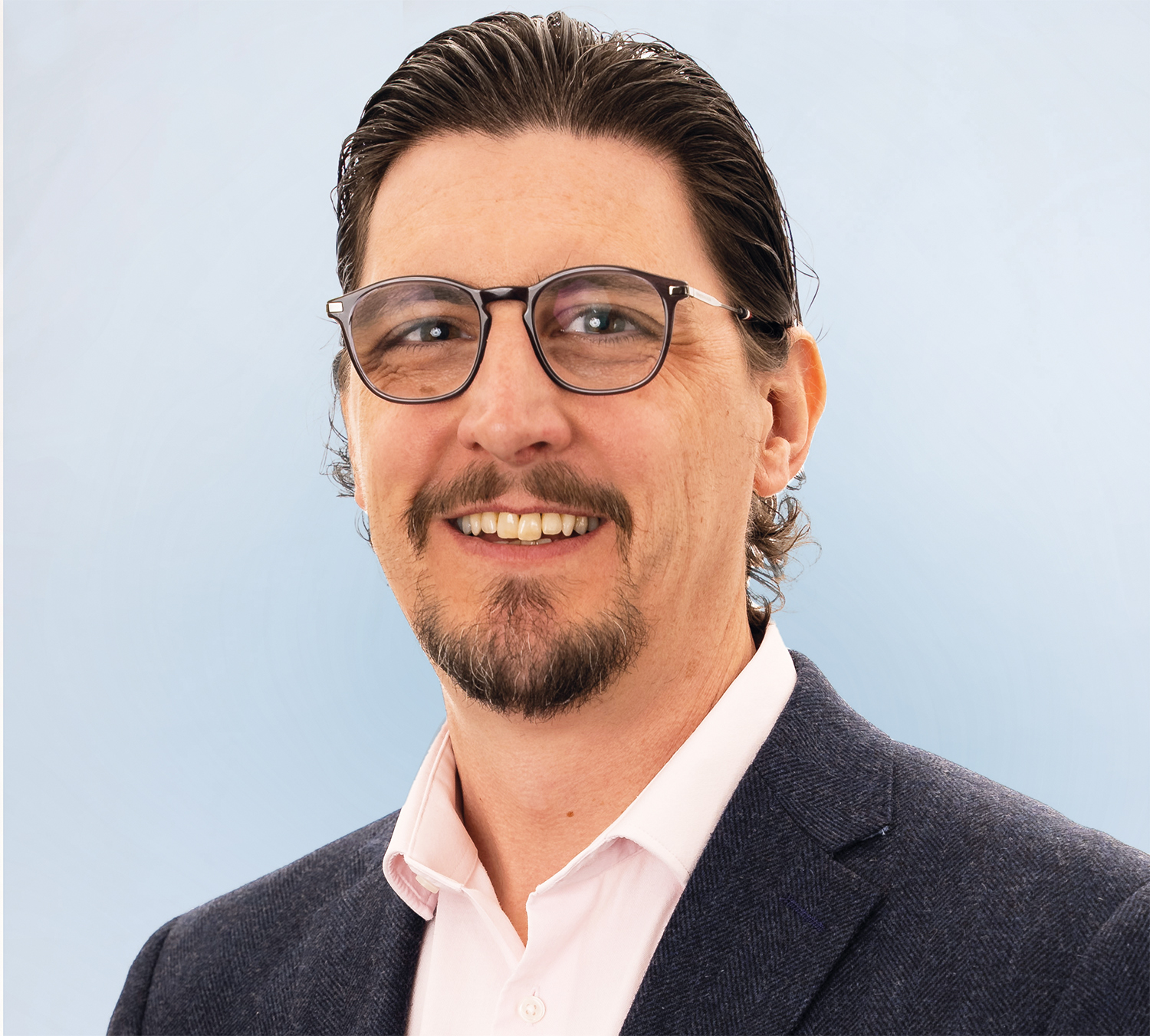
“We need clients to get everything right virtually, so mistakes are not made practically.”
There have also been concerns over quality and standards. In December 2022, the National Fire Chiefs Council (NFCC) published a position paper on modern methods of construction (MMC), singling out volumetric modular buildings as an area for particular concern. The NFCC claims there is a lack of competency around building regulations and MMC, a lack of research, and potential issues
with tall modular buildings.
The government is keen to see modular and other forms of MMC succeed and is funding measures to help manufacturers get it right.
In September 2022 the Construction Innovation Hub – a government-funded organisation founded by the Manufacturing Technology Centre and BRE to help push transformation in construction – launched the Construction Product Quality Planning (CPQP) framework. Aimed at offsite manufacturers, this is a set of guides written to help them comply with the latest standards and with the Building Safety Act.
New standard for MMC homes
In January this year the Department for Levelling Up, Housing and Communities (DLUHC) announced that it had commissioned the British Standards Institute (BSI) to develop a new standard for homes built using MMC in a bid to give homeowners a wider choice of warranties, insurance and mortgages.
Cole points out that modular homes can already gain warranties, insurance and mortgages. All Make UK Modular’s members are accredited by the Build Offsite Property Assurance Scheme (BOPAS) and some of them use NHBC Accepts, the National House Building Council’s review service for innovative systems.
VBC would like to counter some of the concerns around building regulations and quality with a platform design approach deployed across the modular sector.
“At the moment every manufacturer is developing their own solution and getting everything individually tested in terms of thermal, acoustic, fire, structural performance,” says Johnson. “It’s costing a fortune in R&D. That is one of the things that is making modular more expensive.”
Platform design approach
Some individual companies already claim to be using a platform design approach – but a platform used by just one company is missing the point, he says.
Smith thinks that platform design would increase confidence in the sector.
“One of the benefits of the platform design philosophy is that if someone ceases to trade another company can easily pick it up. It also leads to a more collaborative approach between manufacturers in the sector. There’s enough business for everybody to be successful and to develop a healthy pipeline, working in an open platform design.”
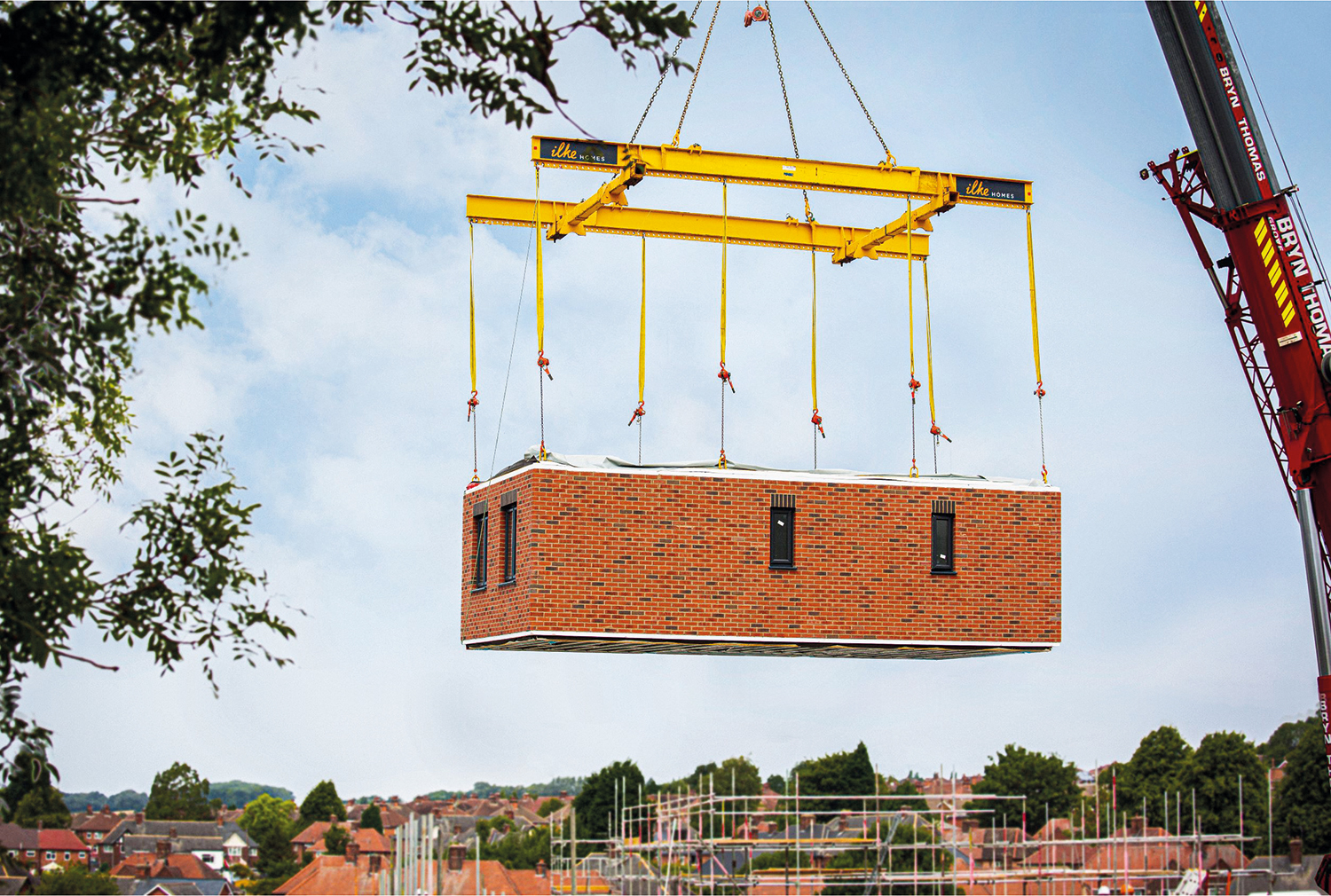
Some quality issues are down to a basic lack of understanding among clients and designers, says Johnson, which also erodes some of the benefits of modular.
Standard designs can get modified as clients, designers and planners get involved. Or production is rushed through in a bid to hit deadlines without all the necessary information in place. “We need to educate clients so that they don’t truncate the design time, and instead ensure they get everything right virtually so mistakes are not made practically,” says Johnson.
Creating a pipeline
With the government’s housebuilding target of 300,000 homes a year still looking unachievable – we were nearly 100,000 shy in the year to March 2022 – modular could help, says Cole. He thinks that ramping up to 30,000 modular homes a year by 2030 would be a “pragmatic” target rather than an aspirational one.
Make UK Modular would also like to see 40% of the Affordable Homes Programme dedicated to MMC, with half of that going to modular. That too would be eminently achievable, says Cole. The programme’s target for MMC in is 20%, but he reckons the MMC proportion might already be at 40%. “It has gone further and faster than the government expected.”
Cole is hopeful that metro mayors could find ways to band together to create the necessary housing demand – and to deliver employment where needed: “The principle is about looking at connecting areas where there is a high demand for employment with areas where there is high demand for housing.”