Kristina Smith travelled to the Segro Logistics Park in Northampton to hear about contractor Winvic’s giant green project.

Near junction 15 of the M1, a massive new logistics hub is under construction. Covering an area of 180ha, this is the Segro Logistics Park Northampton, and will house seven huge warehouses with a total floor area of 465,000 sq m.
Contractor Winvic Construction has the £122m civils and infrastructure package, which involves shifting some 4.8m cu m of earth, building a new bypass for the nearby village of Roade, upgrading junctions with the motorway and main roads, creating a new rail freight terminal, constructing a road bridge over the West Coast Main Line, installing a footbridge over the new section of rail and even jacking a 98m-long services tunnel under the M1.
Project facts: Segro Logistics Park Northampton
Client: Segro National Logistics
Contractor: Winvic
Contract: NEC3 Option A
Cost: £120m
Programme: January 2021 to April 2024
Contractor’s designer: BWB Engineering
Specialist geotechnical engineer: Hydrock
Earthworks contractor: Collins Earthworks
Surfacing: Toppesfield
Onsite concrete batching: Sitecrete
Concrete slab: Stanford Flooring
Service tunnel: Active Tunnelling
“It is the biggest project in our civils and infrastructure division at the moment,” says Winvic project director Scott Martin, whose construction management team comprises 36 staff, distributed across six work areas.
But it is not just the size and scope that make this project interesting. It is the fact that Winvic is delivering the civil and infrastructure elements of the park to be net zero in construction. The warehouse builds will be net zero too – although Segro has yet to award those contracts.
For Winvic, the emphasis for this project is not on headline-grabbing carbon reductions but on ensuring that its carbon accounting and management is rock solid.
“This is the first net zero project we have undertaken in civils and infrastructure and, rather than saying we want to try innovative new things, we have gone back to basics to understand where the carbon sits and work with our supply chain to reduce it,” says Arun Thaneja, Winvic’s technical and sustainability director.
Winvic has set itself the ambitious target of achieving net zero carbon by 2025 for Scope 1, 2 and 3 emissions, which covers a company’s direct emissions, those for the energy it uses and emissions up and down the value chain. As someone who sits on a UK Green Building Council working group covering carbon offsetting and pricing, Thaneja is determined to ensure that everything is transparent and verifiable – which has been no mean task.
Thaneja’s dedication looks like it may already be paying off. With a few net zero projects under its belt and an innovative real-time carbon calculator almost ready to go live, Winvic can certainly claim that it knows its net zero stuff.
Immense earthmoving
The fact that it takes over an hour to tour the logistics park, and its many elements, in a site vehicle conveys the scale of this project.
The earthmoving effort has been immense. Martin points to a coppice, sitting high above us, which was once the ground level; up to 10m in depth of earth has been taken away in places. At the other end of the site, the difference between the bottom of one of the large SuDS attenuation pond and the embankment above it is some 27m.
Even the ruts from the articulated dump trucks are huge. The army of trucks ferrying earth around the site weigh in at 104 tonnes when loaded, says Martin. “Some of the excavators are the biggest outside commercial mining,” he adds. Currently there are around 70 pieces of plant, although there have been as many as 120.
Train and road connections
Winvic started on site with its main 168-week contract on 4 January 2021 and has already handed over several elements of the project, including two of the plots at the south end of the site, some sections of access road and the 14ha strategic rail freight interchange which will be operated by Maritime Transport.
The logistics park has been designated a Nationally Significant Infrastructure Project (NSIP), which means that it has been granted planning permission by the government through a Development Consent Order, rather than going through the usual local planning application process.
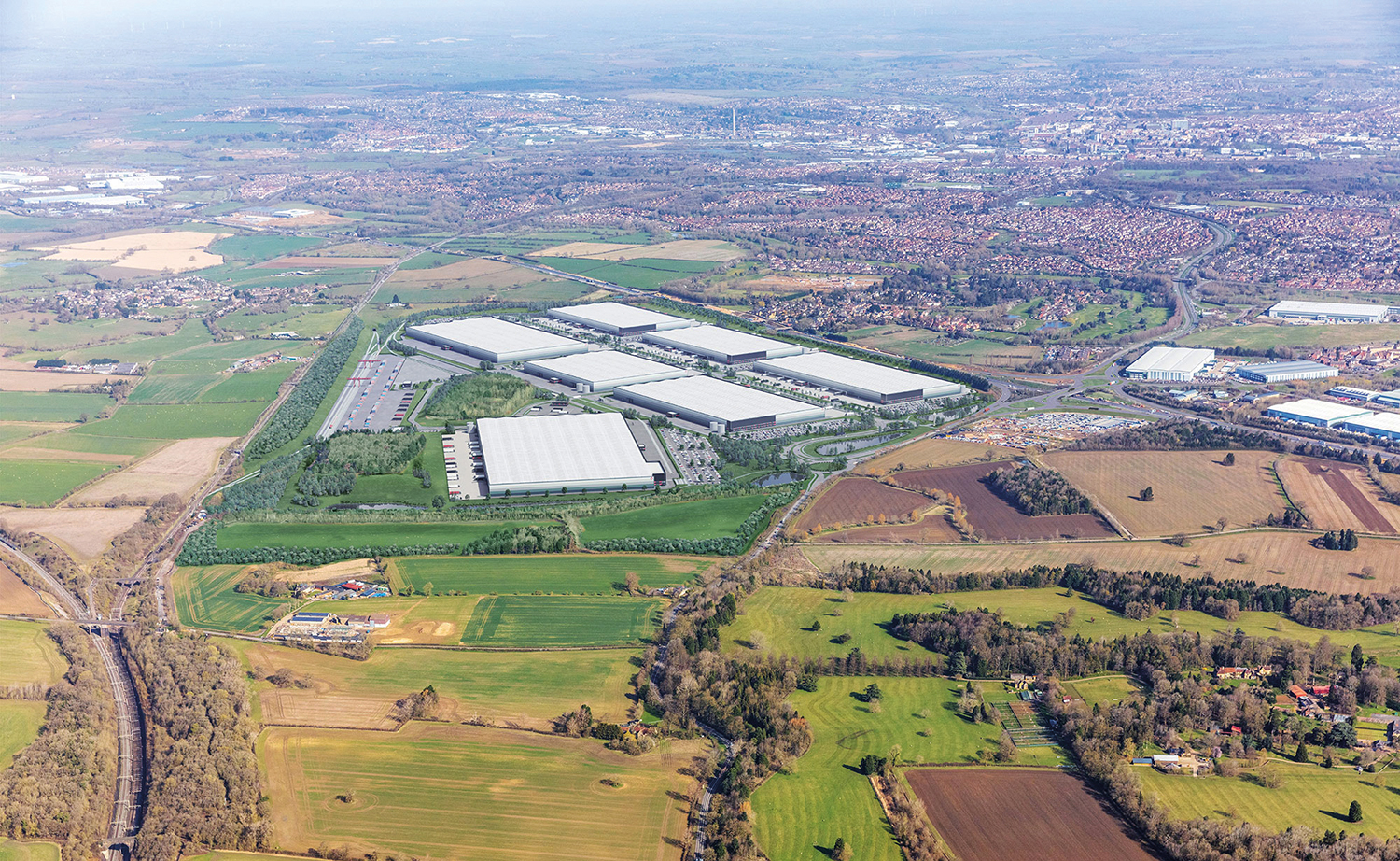
The strategic rail freight interchange, which incorporates a vast slab containing 22,000 cu m of concrete, will be able to receive containers from 16 trains a day, each up to 775m long.
Trains will travel to the park from the West Coast Main Line via the Northampton loop, arriving at the terminal travelling at 40 mph – which is unusual, says Martin. They will then slow down as they travel down a spur to stop and reverse into the terminal for offloading.
Winvic’s contract includes the construction of 4.5km of track, with Network Rail working at the perimeter of the site to make the connection into its line. “We have a tripartite agreement where there are works being undertaken by Network Rail concurrently with ours to meet the programme,” says Martin.
That means daily coordination meetings between supervisory staff and monthly progress meetings. “It is challenging, because everything must be done in line with Network Rail processes and procedures – which is important because it is safety critical,” says Martin. “We are working in collaboration to ensure delivery on time.” The goal is to jointly commission the new line in the second quarter of 2024.
Network Rail is just one of the major infrastructure stakeholders that Winvic must work with on this project. The extensive upgrades to junctions 15 and 15a of the M1, improvements to the A45 and the creation of safer junctions along the A508 have required close cooperation with National Highways and West Northamptonshire Council.
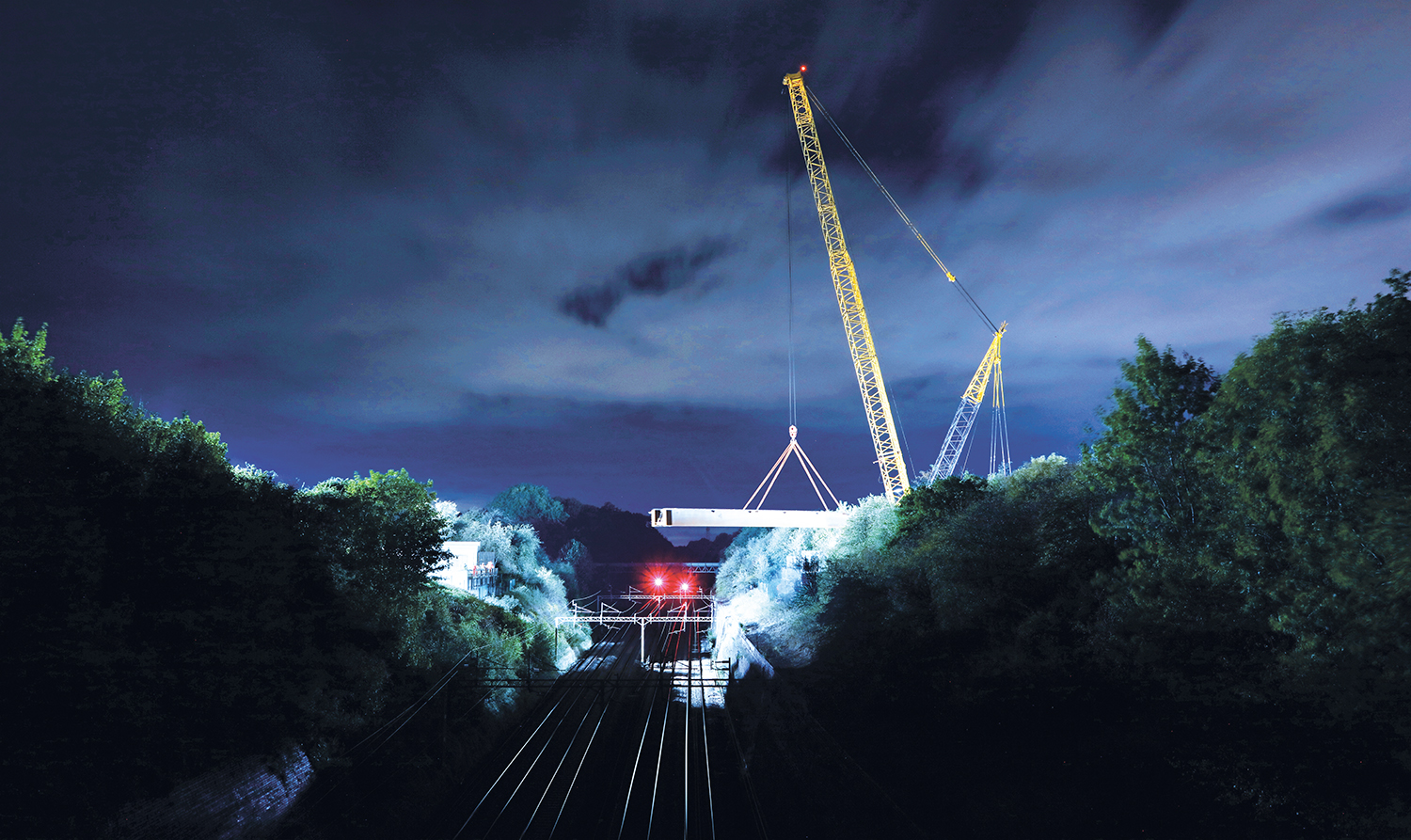
The Roade bypass, a project within a project, required further close liaison with Network Rail. The bypass includes a 264-tonne steel bridge, now installed over the West Coast Main Line and waiting for its deck to be waterproofed. The 1.6m-diameter services tunnel beneath the M1, completed in October 2022, required extensive monitoring of the carriageway above and, again, liaison with National Highways.
Earthworks strategy
From a logistics perspective, one of the biggest headaches has been executing the earthworks, says Martin, since a large proportion of the ground here can’t be handled when wet due to its composition.
“Because the ground has a high sulphate content, that precludes us from using lime to reduce the moisture content,” he explains. “Cementitious materials react with the sulphur to give a swelling effect that can cause an increase in volume of up to 400%.” This has limited earthworks contractor Collins to working for only five or six months of the year.
The strategy for the earthworks has been to keep it all on site, which has helped lower the carbon footprint of the scheme. Much of it is being moved into 2.5km of embankments – or mechanically stabilised earth retaining walls – around the western, northern and eastern perimeter of the site which will serve to shield the development from its neighbouring villages.
As well the sulphate rich Oadby Till, a soft clay, there is Whitby mudstone on the site and limestone deposits in one area, which will be redeployed beneath the new bypass. The earthworks walls are made up of layers of Whitby mudstone and geogrid with reinforcing mesh at their faces, tied into the walls with anchors.
On entering the site, the trains will be shielded from view by the earth walls, with the trains passing through a tunnel at the north-west corner of the site. Winvic has constructed the tunnel – in-situ concrete for the base and walls and precast T-beams for the roof – ready for earth to be piled over the top of it. There are twin tunnels, although only one will be used initially with the second one constructed to allow more trains to run in the future.
But what is net zero?
Winvic is working to the UK Green Building Council’s definition of net zero, which says that projects must first cut between 30% and 40% of embodied carbon emissions, before offsetting. And offsetting must be through verified schemes, either the Gold Standard or Verified Carbon Standard (VCS), explains Thaneja. The aim is to achieve a mix of investment in social, ecological and renewable schemes.
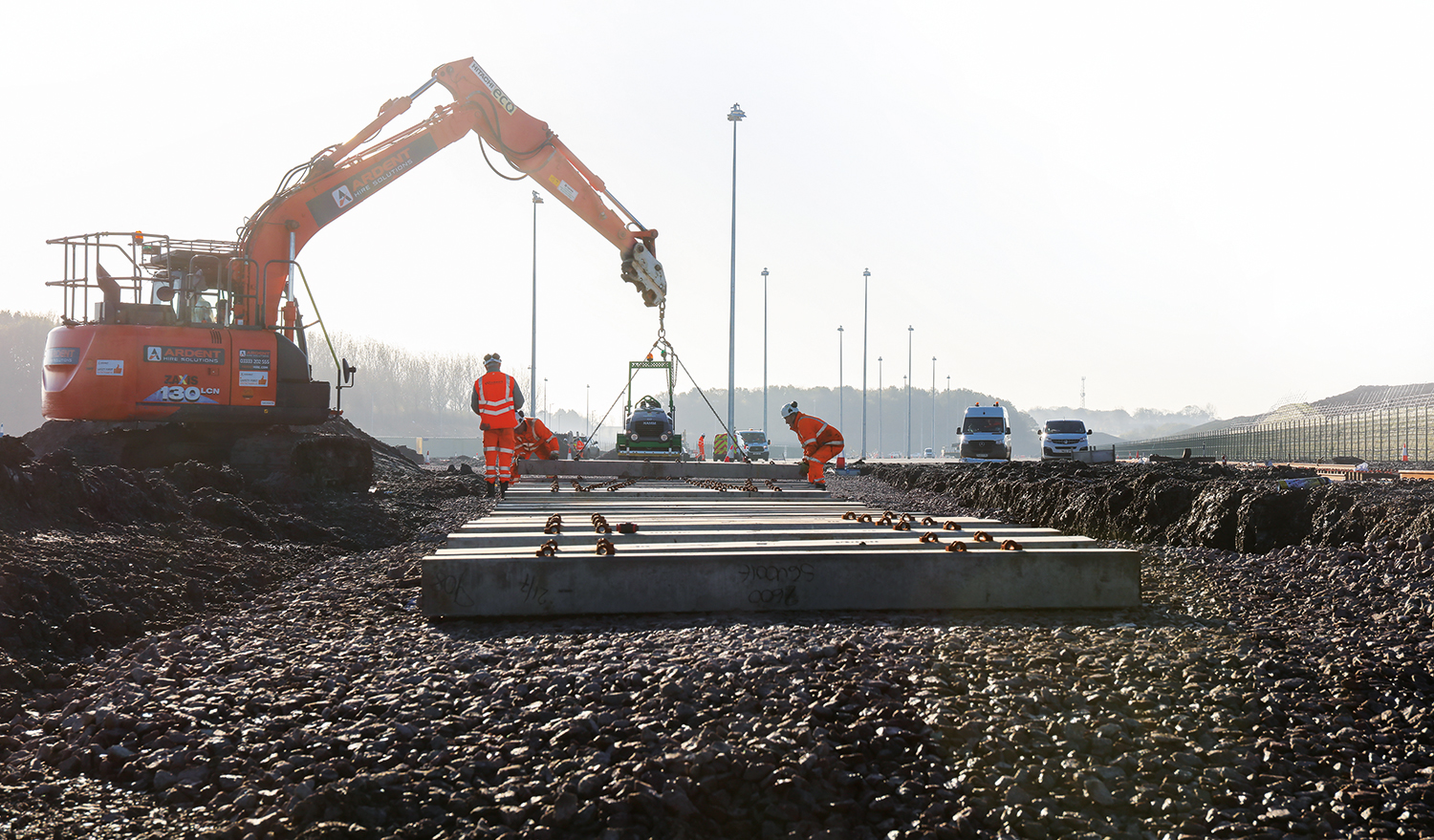
The Segro Logistics Park Northampton was Winvic’s first net zero civils and infrastructure contract awarded, although it has subsequently won two more, says Thaneja. One was the Ascent Logistics Park in Leighton Buzzard, handed over to Firethorn Trust in September 2022, with both the civils and infrastructure and buildings achieving embodied carbon 30% below 2020 benchmarks. This was a much smaller affair, however: 10ha delivered in 12 months.
Winvic’s first ever net zero project with Segro was a warehouse building on its East Midlands Gateway logistics park, a speculative 18,580 sq m cold store warehouse handed over in November 2021. Winvic, which also delivered the infrastructure and civils work for the East Midlands park, later built a 55,740 sq m distribution unit there for Maersk, completed in December 2022. Maersk is aiming for this to be net zero in operation, as well as in construction.
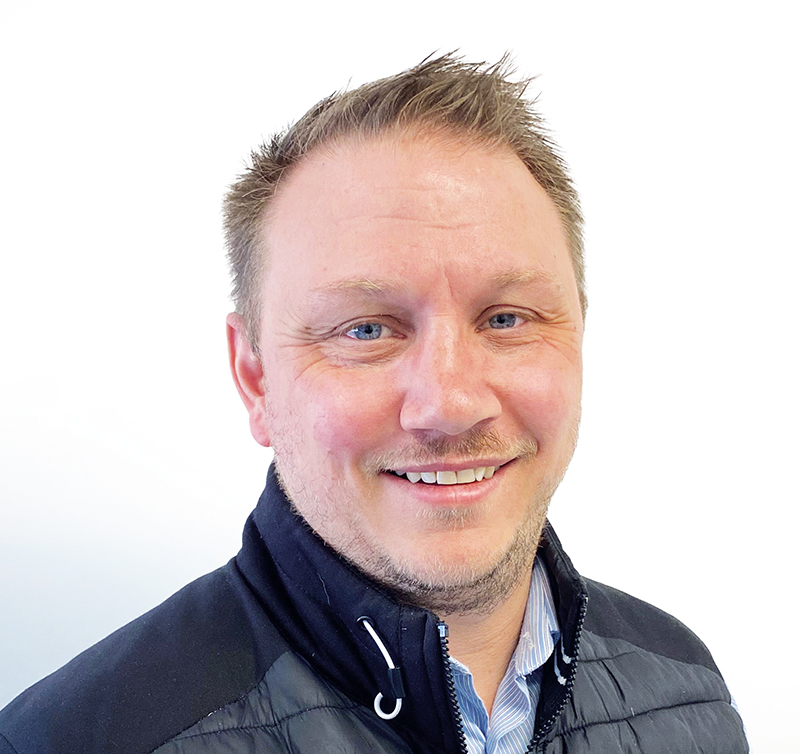
CV: Scott Martin, project director, Winvic
Scott Martin began his construction career in 1996 at the age of 17 working as a technical assistant for Lincolnshire County Council, where he received a good grounding in all things civil engineering.
When the council joined forces with Babtie Group – now Jacobs – in the late 1990s in a public-private partnership, Martin gained experience on site as an assistant resident engineer and, as he says, found his calling.
From 2001, Martin has worked for civil contractors and as a freelance project manager, moving to Winvic and his current role in early 2021. “I just enjoyed being on site more than being in a design office,” he says. “I enjoy the cut and thrust of building schemes.”
The biggest challenge for any net zero project currently is the lack of verifiable data, says Thaneja. “We need to find the baseline with the supply chain,” he explains. “We have done their carbon assessments for them to work out what reduction measures we can achieve.”
Winvic has 230 supply chain partners and has worked with the top 75 – in carbon emission terms – to work out baseline emission data and then look at how to reduce emissions. Many product suppliers did not have Environmental Product Declarations (EPDs) which provide embodied carbon information, as these are costly and lengthy to obtain. Winvic has worked with its suppliers and EPD provider BRE, to obtain EPD information for some 70-plus products.
Winvic has also been developing an in-house AI-based carbon calculator which can be linked to a BIM model, with Innovate UK funding. The AI allows the raw data to be taken from the model to give an initial carbon calculation, using data from previous projects, which is then updated as the design and construction progresses.
“By October, we want the majority of projects to have an iPad which is linked to the platform in our head office and which will tell them in real time what the carbon emissions are,” says Thaneja. Currently the Northampton project is achieving a 36% reduction in carbon emissions.
Reducing carbon
Measures for reducing carbon on the Northampton project, compared to a 2020 baseline, have included using fly ash and slag to replace some of the cement in concrete, with the proportion varying by the application but at an average of 35%. Batching concrete on site reduced embodied carbon due to transport, as well as reducing waste.
Plant was initially running on hydrogenated vegetable oil (HVO) but after concerns were raised about HVO’s palm oil content, Winvic went back to the drawing board with Collins, looking at which bits of kit could be replaced by hybrid diesel and electric and how they could change practices to burn less fuel. The site cabins are powered by a Hussh Pod hybrid generator.
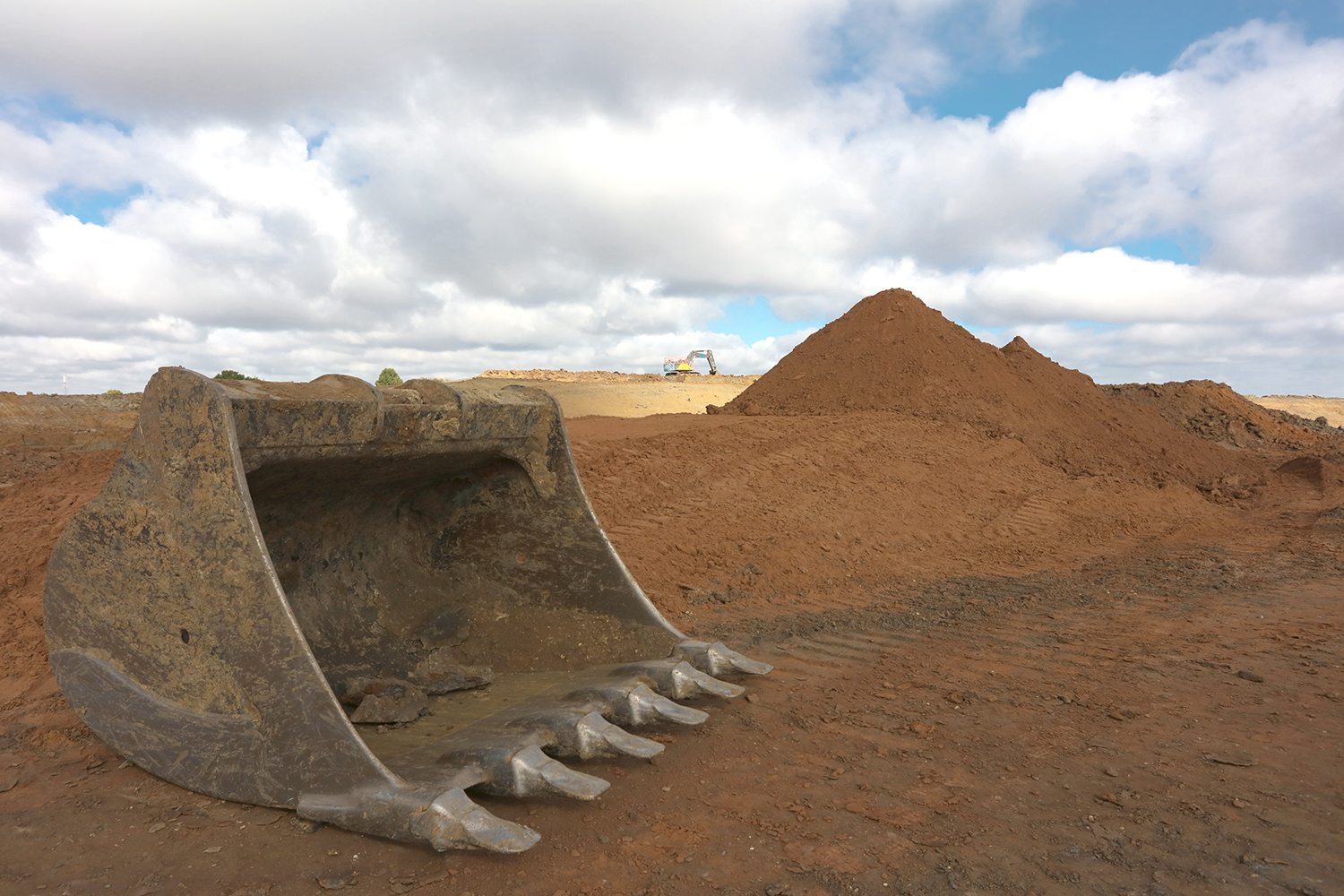
Most of the drainage will be made from material recycled from milk bottles. Although the manufacturer has been selling these for a few years, Winvic had to work with it to work out the embodied carbon up to delivery on site, since it did not have an EPD.
“We can now assess 97% of our bills of quantity for embodied carbon,” says Thaneja. “There are some items that you just can’t achieve verifiable data for, such as mastics or cleaning products.”
Winvic has already purchased VCS and Gold Standard carbon credits – for reasons of transparency, explains Thaneja: “Some people wait until the very end of the project and are selective about what they assess. I want everything to be verifiable and auditable by a third party.”
From brown to green
Although much of the park is still a muddy brown colour, pockets of greenery are emerging. Landscapers are already busy at work and must install no fewer than 60,000 trees, 20km of hedgerow and 30,000 shrubs by the end of the contract. The finished development will boast 32ha of park and grassland.
There are around five months’ worth of earthworks left to do, says Martin, which should mean that everything is in place by the end of 2023. Roade’s bypass should be largely complete by the autumn, with some work continuing into early 2024.
We don’t know yet who the tenants for this vast logistics park will be and how far they will wish to go down the net zero road. We do know that Winvic would be very willing – and able – to accompany them on their journey.