The recent Intermat construction equipment show showcased the much larger capacity electric, hybrid and hydrogen-powered machines that are now available. Peter Haddock reports from Paris.
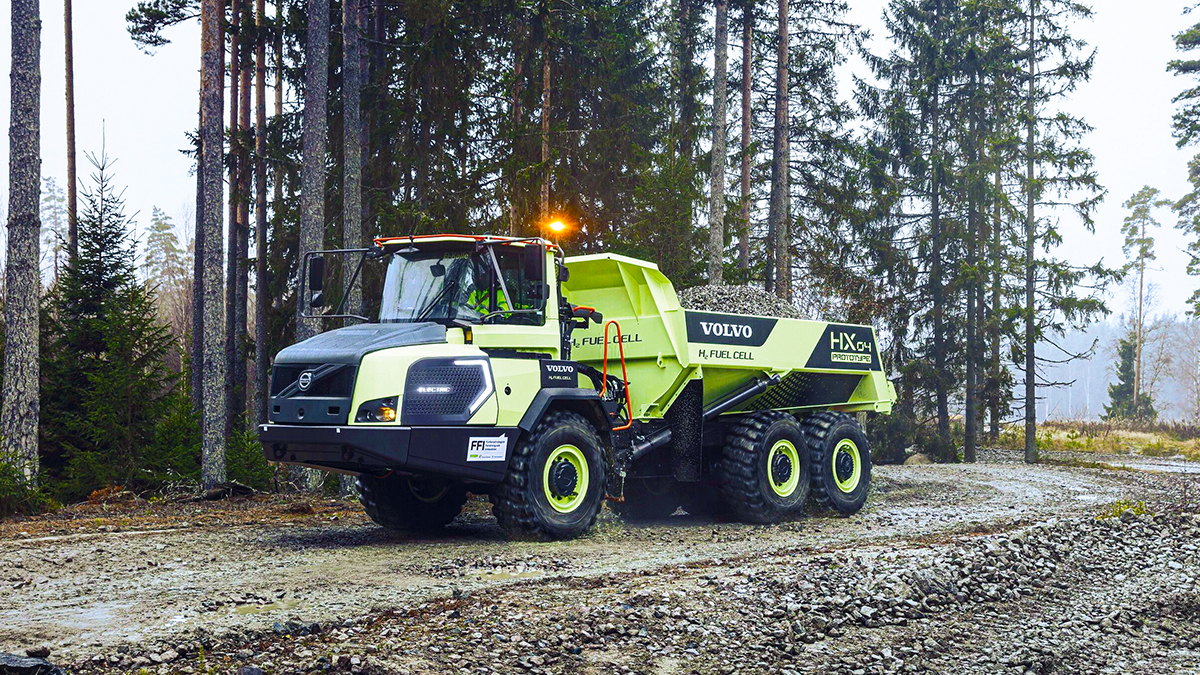
In April, Intermat Paris returned for the first time in six years. The exhibition has always showcased the latest innovations in construction equipment, and this year’s event had a very specific focus on low carbon.
And it was not just about the fuel technology, for digitalisation is transforming the productivity of the plant sector and also contributing towards reducing carbon emissions.
The big theme of the show was how much bigger the machines are that run on all-electric power. Some manufacturers offered a glimpse of a future with numerous options to hybridise equipment – not just diesel-electric, but also with hydrogen.
Chinese manufacturer LiuGong has a range of large wheel loaders and excavators that have already spent many thousands of hours working and proving themselves on job sites across the globe. For example, its 856HE electric wheel loader is already being used for full shifts by both Aggregate Industries and Dalecrete readymix concrete to load aggregates.
Bigger-capacity machines
Product expert Oliver Keates explains: “This model is a 21 tonne machine with a 423kWh lithium iron phosphate battery that can be charged in 1.7 hours. It is powered by a 160kW engine, has a 3.5 cu m bucket capacity and can operate for more than 11 hours on a full charge.
“But this is not our largest wheel loader, as we have revealed our new 870HE 24-tonne product at Intermat that has a bigger capacity with a 4.7 cu m bucket as standard and a 423 kWh engine.”
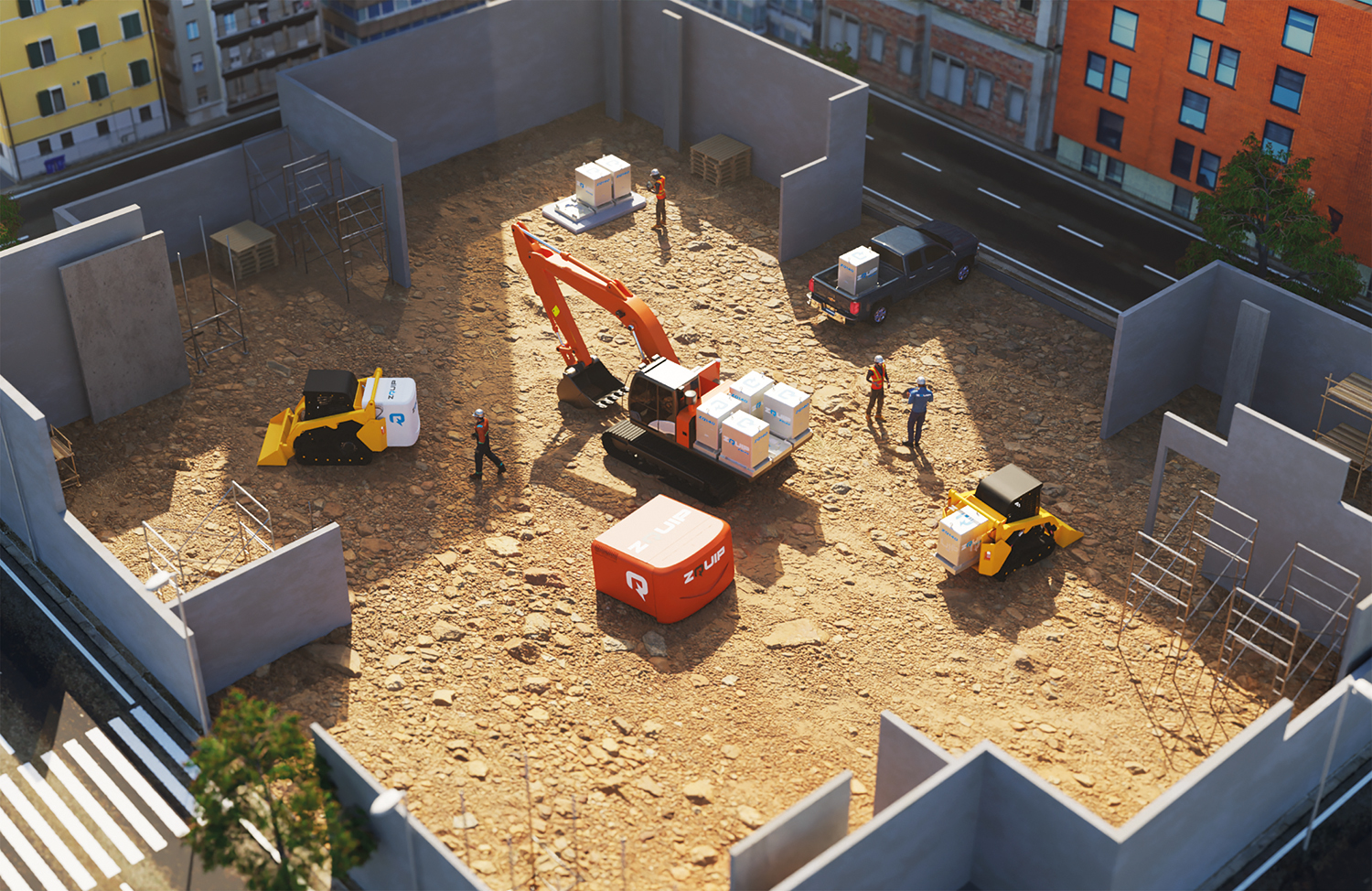
Intermat was also the first European show to showcase Volvo’s prototype hydrogen fuel cell articulated hauler. The HX04 has been in testing for a number of years since it was announced in 2022. It can be charged with 12kg of hydrogen in around 7.5 minutes, enabling it to operate for approximately four hours. This shows the very real possibility of hydrogen becoming a usable fuel in the future, particularly on larger sites.
Fuel cell wheel loader
For US manufacturer Develon, the hydrogen story came in the form of its DL250-FCEV, a fuel cell wheel loader. It is based on a single platform design that allows it to be equipped with a fuel cell powerpack running on hydrogen but also offers the ability to transition to a battery electric vehicle by installing a battery pack.
This shows how the manufacturer is enabling future machines to be powered by a range of fuel types, a theme throughout the show.
With the transition to greener and quieter solutions now becoming more popular in Europe, and being mandated for certain cities, looking for a whole-site solution has, until recently, been very difficult.
However, electric machinery specialist Moog Construction used Intermat to present its ZQuip retrofit solution, which can turn existing diesel equipment into electric machines and back again.
Moog director Scott Scheffler says: “With ZQuip, we can help whole sites transition to low-carbon battery power, as the solution can work with a wide range of equipment types from a huge variety of manufacturers.
“Essentially, ZQuip can be retrofitted to diesel powered mobile equipment, from small mini excavators to larger 20-tonne models, wheel loaders, skid steers and many more machines.
“The batteries are also interchangeable from machine to machine and can be swapped in a matter of minutes. So you can have a bank of them charging and even swap them out if you are not using a particular machine.
Single electric power solution
“Being modular, you can use a single battery in a mini and four to five in a larger machine, converting the whole site to electric power using one single solution. We have also designed the batteries to be mobile power stations.
“This means you can take a battery to a machine and use it to charge the battery without swapping them. And you can even take the battery system out and return it to a diesel machine.”
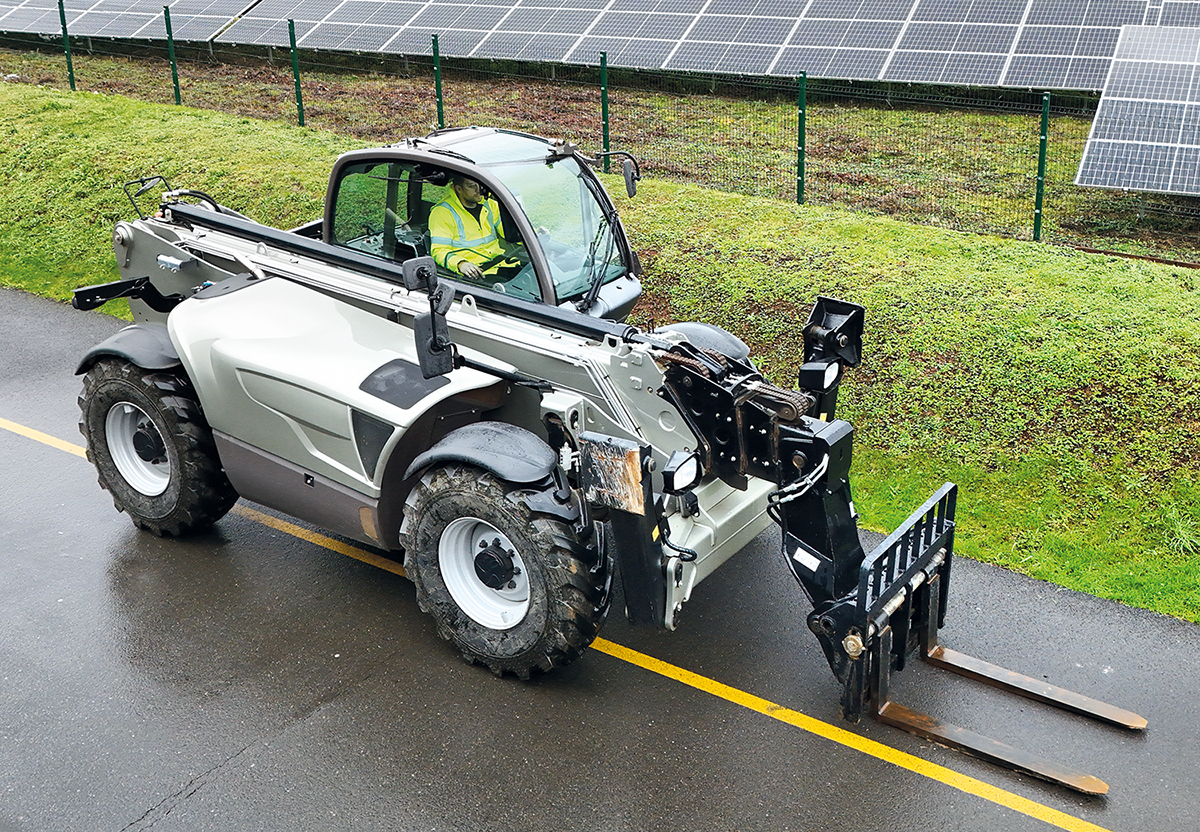
Back in the UK, Peterborough-based Perkins Engines has been using the latest in 3D modelling and fluid dynamic simulation to turn an existing diesel-powered telehandler into a diesel electric hybrid.
The unit in question, called Pathfinder, was a large 18m-reach telehandler previously operated with a 75kW diesel engine. Now, inside the same engine bay sits a new advanced power solution using a Perkins 55kW diesel engine with 20kW of electric power. This combination delivers the same power as the original engine with a 10% fuel saving and some added benefits.
Best of both worlds
Iain Evans, manufacturing engineer at Perkins, says: “With Pathfinder, we wanted to show manufacturers that it’s possible to get the best of both worlds regarding power and fuel choices while ultimately saving fuel and carbon emissions. And for equipment like telehandlers, it’s all about optimising the machine to reflect different types of applications.
“For example, you previously had to have a 75kW engine as the machine needed this to perform intensive tasks like heavy lifting. However, when you look at how often this power is required, it’s only around 20% of the time, meaning you have a 55kW engine working to deliver all the other tasks.”
In addition to fuel savings, a big advantage of this approach is that existing machines can be converted, in this case, to work for some time indoors without the engine required at all. This could eliminate the need for another machine for applications like loading and unloading from outside to inside warehouses.
For plant hirers, this approach could offer customers much more flexibility and for manufacturers, in this case, the design of the machine itself doesn’t have to be changed.
LiuGong’s electric loader
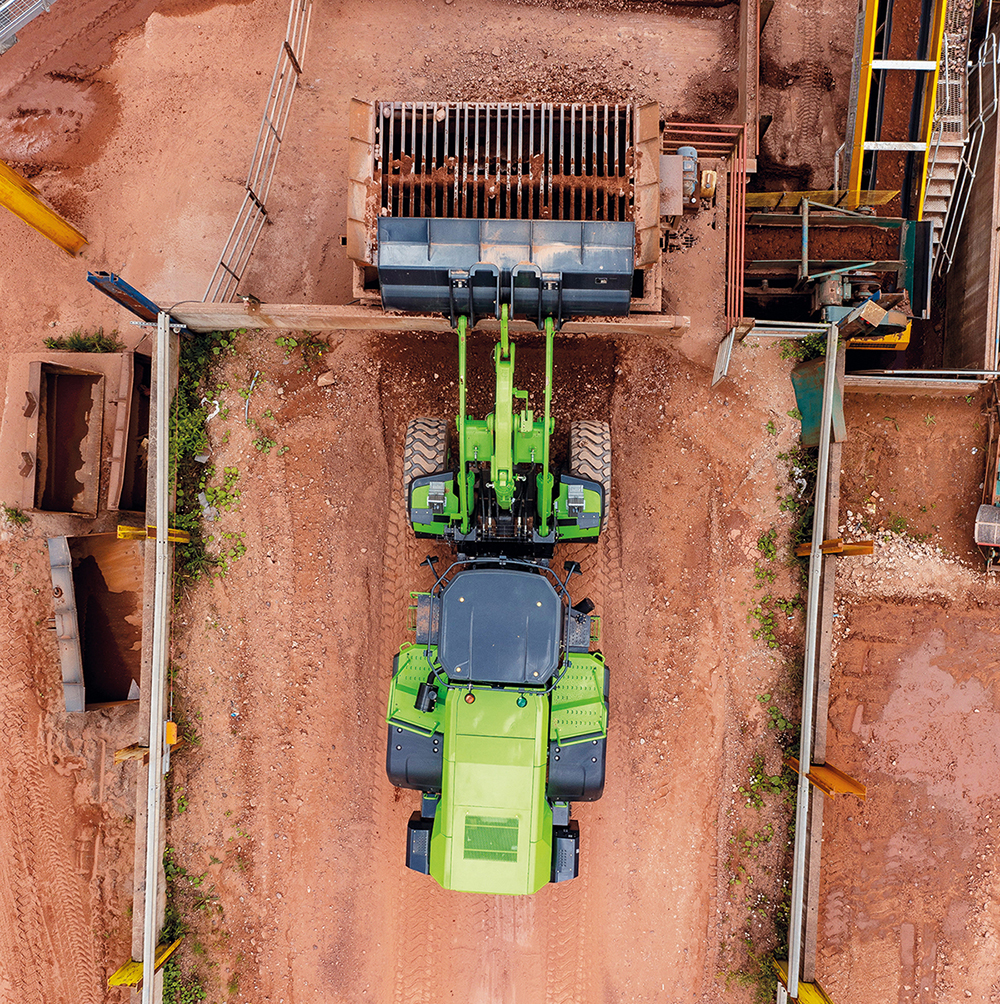
The 856HE, manufactured by LiuGong, is the world’s first commercially available battery electric loader. It is the very first the company has rolled out in Europe.
The machine has been put into action at the Aggregate Industries Bow plant in east London, where the loading shovel will be used to load aggregates from the site’s Bow railhead.
The 856HE will also be used on the London Concrete readymix plant to keep the site clear.
The 21 tonne vehicle has a 423kWh lithium iron phosphate battery with a fast charging capability of 1.7hrs.
The machine has a 160kW engine and 3.5 cu m bucket capacity and can operate for more than 11 hours on full charge.
Most importantly, it uses zero fuel, has zero emissions and produces low noise and vibration.
Digital tech to avoid collisions
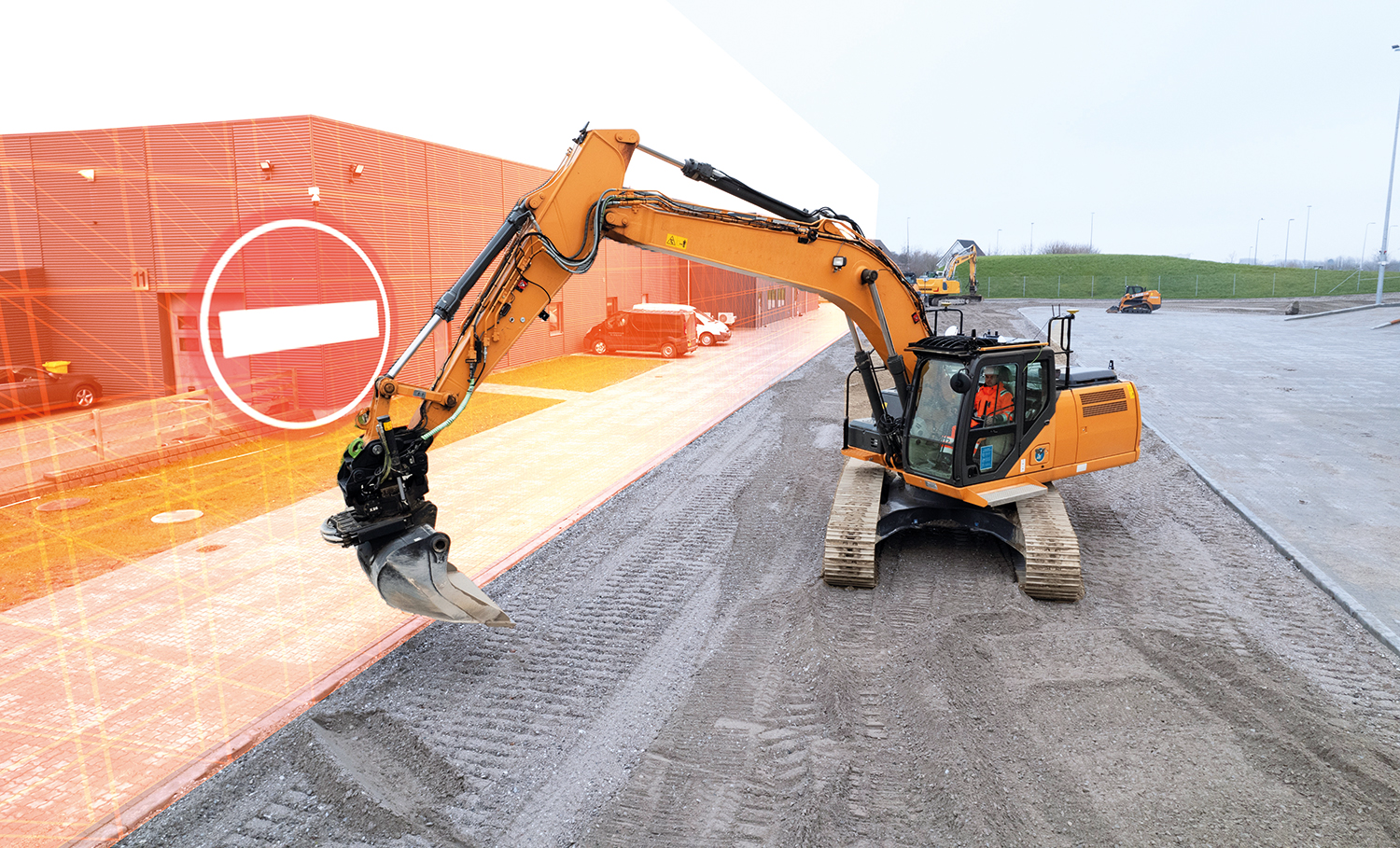
While the range of low-carbon equipment continues to grow, so too does the digitalisation of the sector.
At Intermat, industry leaders Leica Geosystems and Xwatch Safety Solutions joined together to deliver the first integrated electric Hitachi machine. This showcases 3D collision avoidance and 3D machine control on one machine.
The system’s sophisticated design enables the creation or importation of 3D avoidance
zones, both above and below ground, directly within the Leica Geosystems MC1 3D machine control software.
The technology solution is already rolling out on-site with Costain and Flannery Plant Hire in the UK on the M6 motorway.
Leica Geosystems and Xwatch Safety Solutions have brought together 3D collision avoidance and 3D machine control on one machine