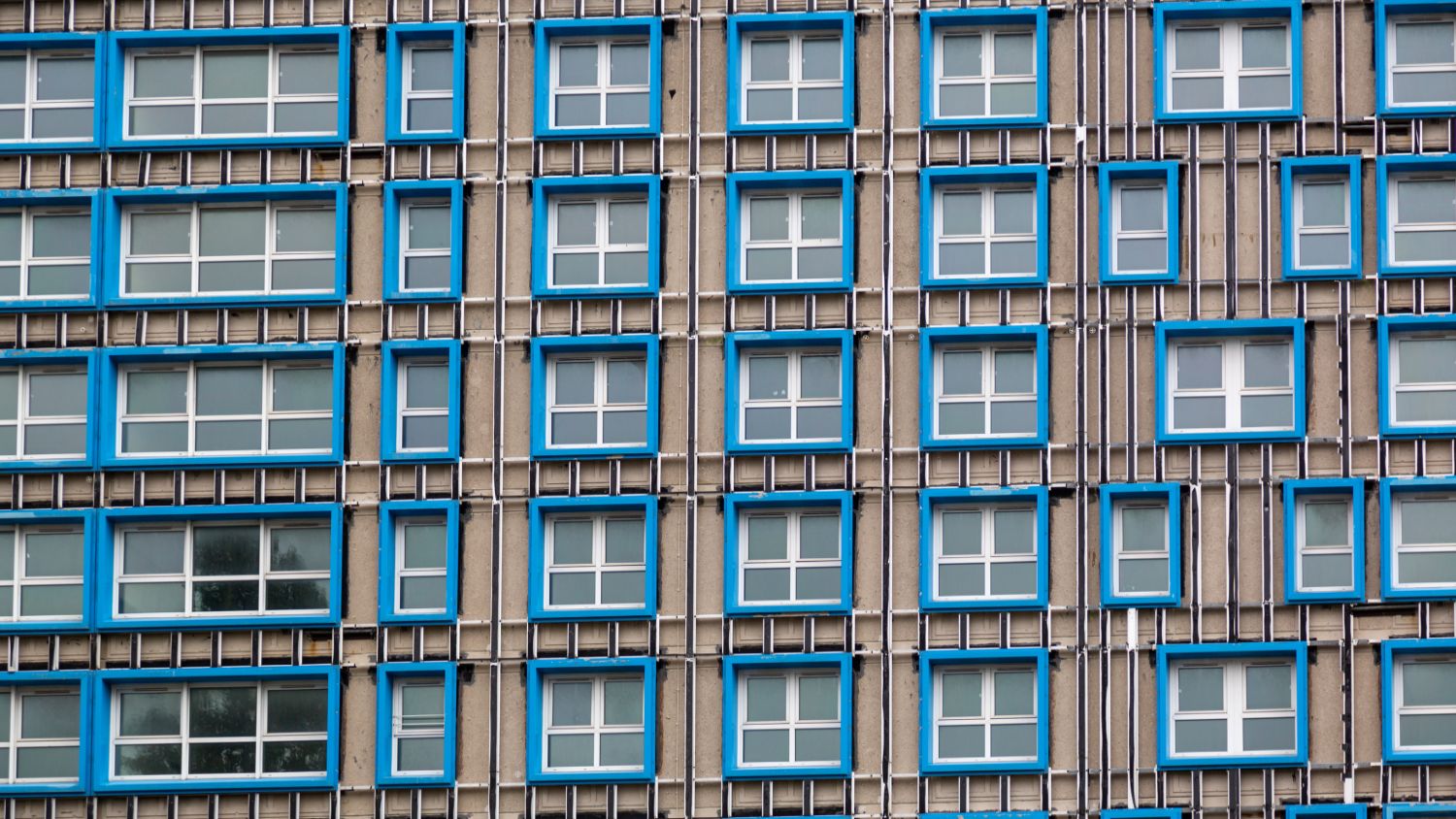
Why doesn’t the government make the cladding manufacturers pay up for this debacle? You will always get installers who don’t come up to scratch and lack knowledge. Stop making the ‘customer pays’ philosophy the norm. A radical rethink needs to happen.
Stewart Craven
Putting the cost solely onto developers misses two key parts of the supply chain that should be contributors to any remedial costs. While everyone is focused on the cladding and therefore the material supplier, what about poor installation, particularly missing firebreaks in the cladding and around windows and any poorly installed fire detection and suppression systems? This is defective construction and should be borne by the contractors and, if they are no longer in business, perhaps the warrantors.
Peter Brooker
Workers urged to open up over stress (CM, 5 May)
I believe that I suffered from being overworked and blamed for things that were out of my control, as well as being verbally abused on site by a worker. This had been going on for over six months, sometimes in front of my line manager, and nothing was done about it so I decided to document the abuse in writing. Unfortunately I let a work coach from head office know this fact and within two weeks I was paid off, citing a lack of trust. Since then, I have been in and out of work but would really like to leave the industry and do something completely different – in other words, less stressful.
Name and email address supplied
Provide your own feedback on latest industry issues by posting comments online or by emailing the editor at [email protected]
Comments
Comments are closed.
Where the cost should found for cladding remediation is tricky, manufacturers overstated or lied about material performance, the installer installed incorrectly, but how often have you been told that a material purchase and subcontractor order has been placed based on a ‘commercial decision’, where cost is the sole driver to the Main Contractor. I hear it all the time and when I question the decision based on differences in product certification I am told it is ‘Value Engineering’ and the new product has a certificate, but no one in the commercial team has read or evaluated the specifications, just the cost. If the manufacturer has lied or with held vital performance information, then they should pay. If it is shoddy installation then the installer pays. If it is a money saving exercise, then the Main Contractor pays. Simple.