Construction clients are key to all the industry’s major challenges, including net zero, building safety, skills, digital transformation and plenty more. Will Mann speaks to a cross section of ‘client side’ CIOB members about their post-pandemic plans
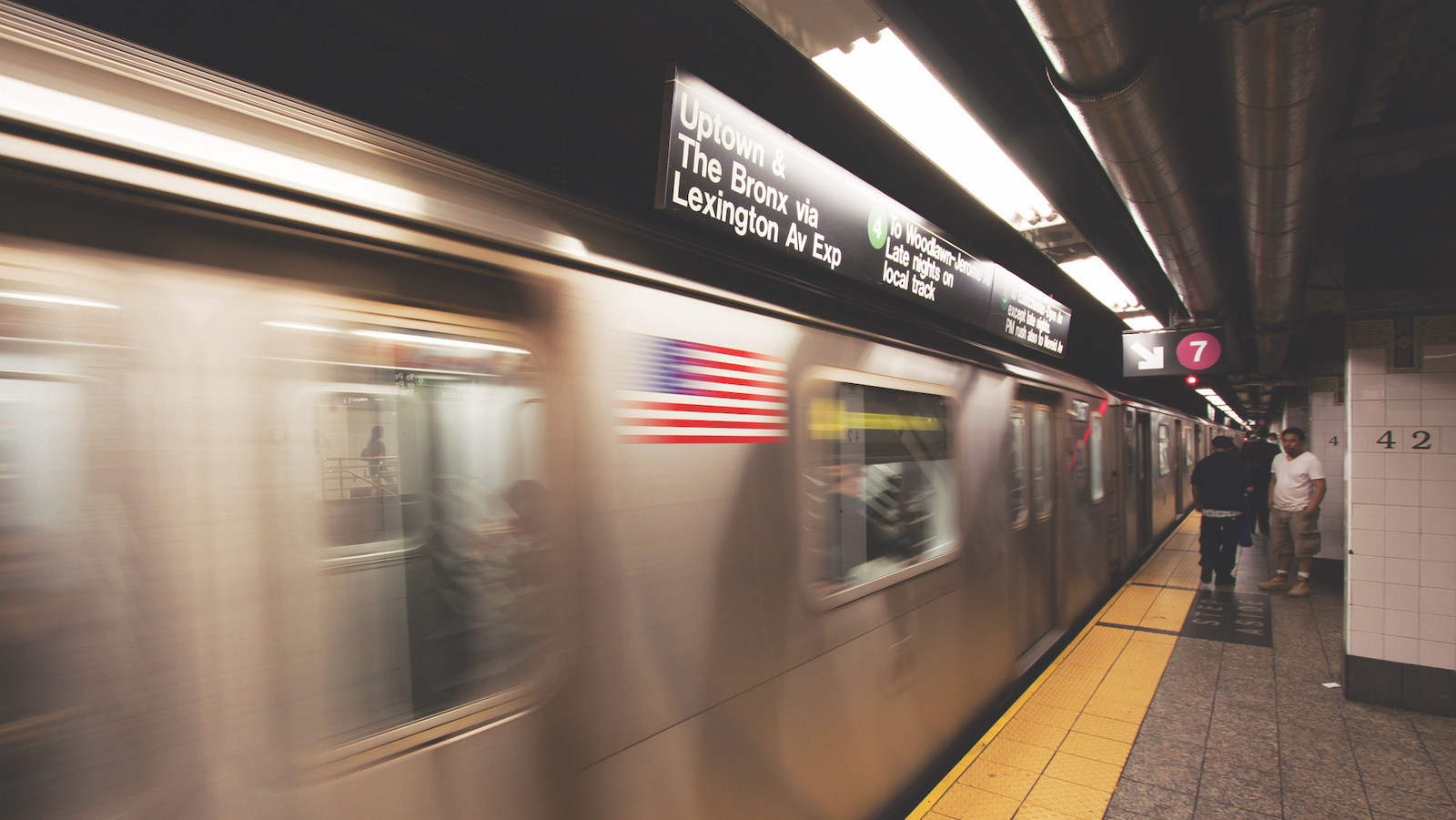
‘We have to think about the long-term effects of covid-19’
Virginia Borkoski FCIOB – senior vice president, program planning and delivery, Metropolitan Transportation Authority, New York City
A lifelong New Yorker, Virginia Borkoski graduated from the city’s Pratt Institute, took a master’s at New York University, and is now in her second spell at the Metropolitan Transportation Authority (MTA). Her office is at 2 Broadway, in Lower Manhattan, where she was working on ‘9/11’. “We watched the towers burn, and felt them fall” is how she remembers it.
She began her current role as senior vice president, program planning and delivery in 2017, and is one of over 2,000 construction and development staff at the MTA, which had projected annual capital spending of $51.5bn (£36.4bn) before covid-19.
“I lead the external partner programme, guiding private-sector designers and contractors through the technical implementation of projects that require MTA review and approval,” Borkoski explains. “This includes design and constructability reviews, construction initiation and oversight, and project ‘close-outs’. My unit is only about 30 people, so for major projects we would bring in expertise from other MTA units.”
Her team’s work covers three types of project: ‘adjacencies’ are projects being delivered by other developers and agencies within 200ft of MTA property; public agencies projects involve partnering with bodies such as utilities; developer improvements involve working with property owners to incorporate improvements to stations in their developments.
“A developer improvement example is the new subway entrance to Grand Central at One Vanderbilt Avenue, a 77-storey skyscraper in Midtown, part of $220m [£155m] of transit improvements bundled into the project,” Borkoski says.
Despite the pandemic, she has remained “as busy as ever”. “There were delays to some projects, but generally, the MTA has been able to accelerate construction work,” she says. “For the first time in the history of the subway, we shut down overnight, from 1am to 5am. Publicly, the reason was we were disinfecting. But we have also used those shutdowns to advance work such as track repairs and accessibility upgrades.”
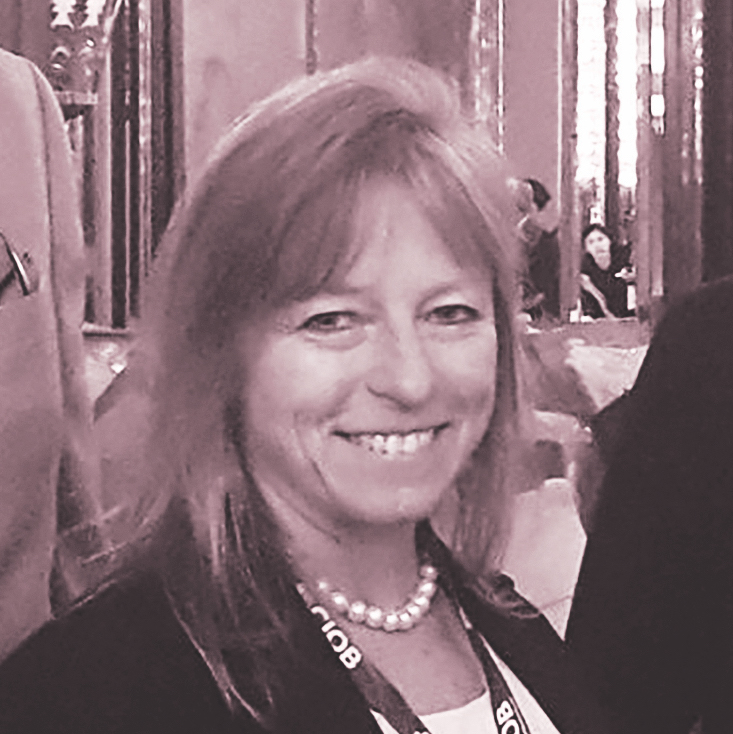
“In the East Midtown rezoning, developers are taking down 100-storey buildings to
put up 130-storey buildings because that’s better value”
She thinks the fall in ridership will affect project planning. “We are looking at a multi-billion-dollar deficit and we have no federal funding,” she says. “The subway is safe – there are 18 air changes per hour – and people are coming back but not that quickly, so we have to think about the long-term effects of covid-19 on ridership.”
But there is still a huge amount of development going on in Manhattan, she adds. “In the East Midtown rezoning, developers are taking down 100-storey buildings to put up 130-storey buildings because that’s better value.”
While quality is a major concern in UK construction, Borkoski says there is a “different mindset” in the USA because of how the built environment professions are regulated.
“Architects, engineers and contractors must be licensed to operate here, and the testing for that is regulated very tightly by the government,” she says. “So, when you put your signature on a set of drawings as a regulated architect, it is a very big deal.
“We have a very rigorous project review system in New York, detailed quality plans, tight building regulations and lengthy ‘punch lists’ which must be followed.
“We also have Local Law 11 in New York City, our ‘Facade Inspection Safety Program’, which requires owners of buildings with more than six storeys to have their exterior walls inspected to a prescribed reporting schedule. That was introduced after incidents where pieces of facade fell off. So when quality issues surface, we are pretty quick at correcting the problems.”
Borkoski has been a fellow of the CIOB for almost 10 years and a trustee for three, which gives her “a different perspective and allows me to see what the rest of the world is doing”.
“It has also been critical to hear how other CIOB client members have managed construction during covid-19,” she adds.
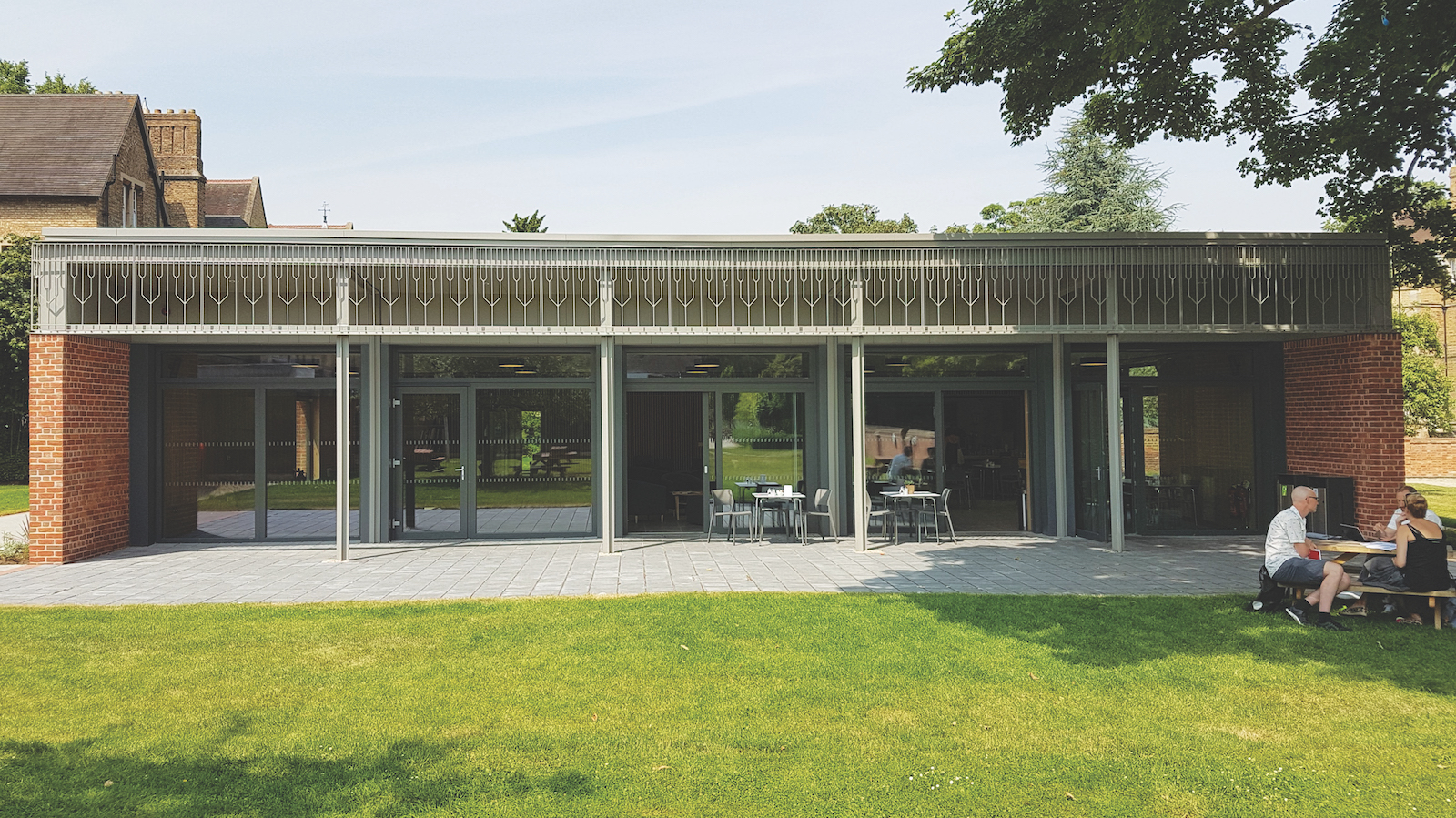
‘Passivhaus is an effective way of ensuring high quality’
Jennifer Makkreel MCIOB – deputy head of capital projects, University of Oxford
Jennifer Makkreel worked client side in the Canadian construction industry before moving to the UK in 2008, working for Oxfordshire County Council, then taking her current role as deputy head of capital projects at the University of Oxford in 2014.
“It is challenging; there are conservation and aesthetic considerations – we have many historic buildings – as well as the end user requirements, plus sustainability,” Makkreel explains.
She juggles “35 live projects at any given time” and her pipeline runs to more than 160 projects with a total value of £1.7bn, at various RIBA stages from 0 to 7. These include major schemes such as the Life and Mind Centre, a partnership with L&G.
“At £200m, this is the largest building project ever undertaken by the university,” she explains. “But at the other end of the spectrum, we have much smaller projects such as a £180,000 library refurbishment.”
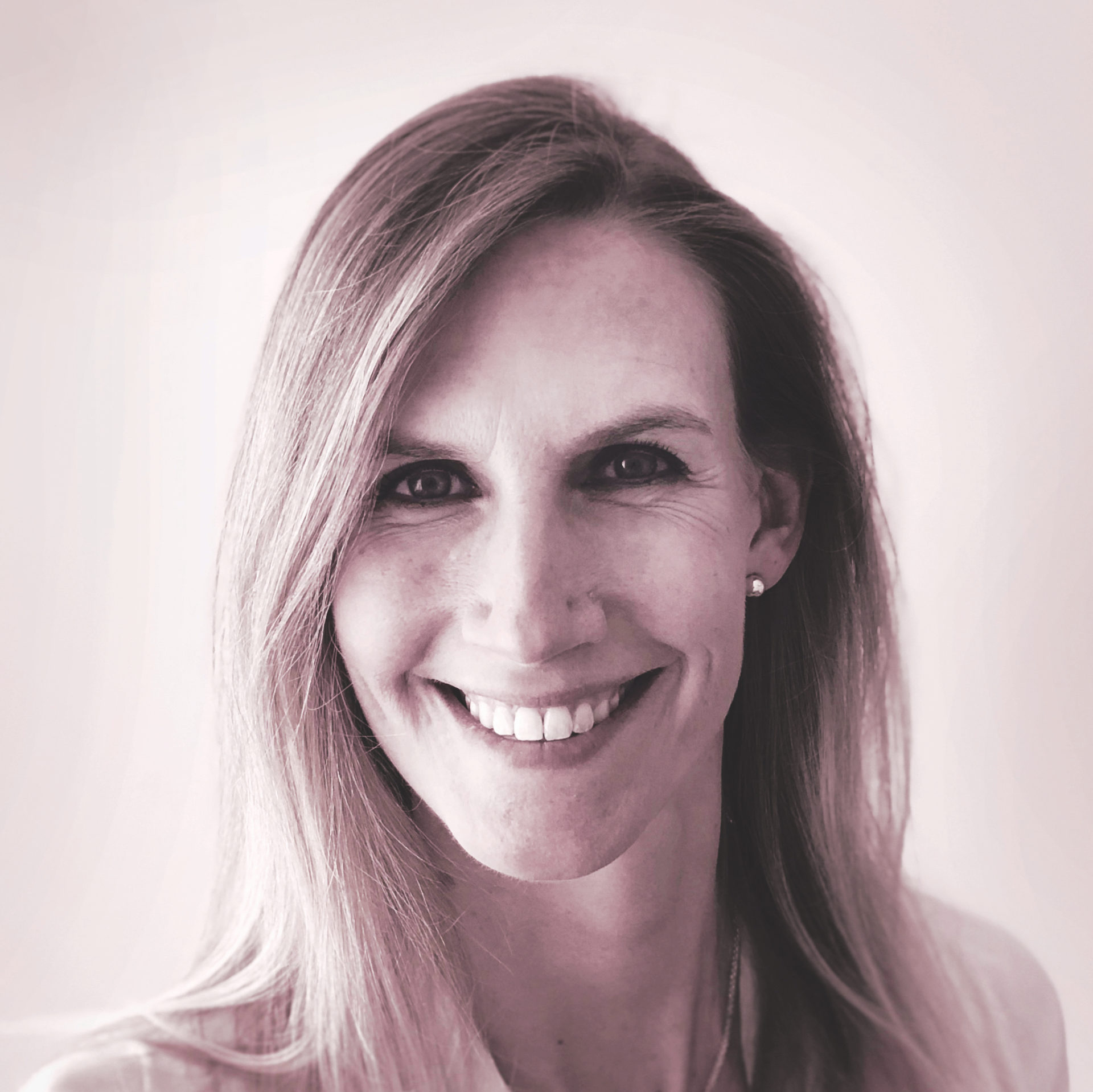
“My message to contractors is that everyone wins if you deliver right first time”
In the pandemic, she found it “very helpful” to connect with other CIOB client members, praising AstraZeneca’s Brian Street for his “fantastic covid risk assessment document”.
Covid has created uncertainty with the university’s capital works programme. “No one is expecting a cost-neutral scenario,” she says.
“We have demonstrated we can work more flexibly, so do we need the same office footprint? It is a fluid situation, but we may have to tighten our belts.”
Quality is now coming to the top of agenda. “My message to contractors is that everyone wins if you deliver right first time,” she explains. “We have found that the Passivhaus methodology is a very effective way of ensuring high-quality construction. The university now aims to deliver all projects worth over £1m to Passivhaus standard. This requires the right attitudes, the right materials, early engagement with the supply chain and absolute precision in execution.
“Main contractors haven’t quite bought into it yet; they tend to see the risks before the benefits. But by spending more time up front and working to an efficient programme, you deliver a high-quality product and spend less time having to fix those issues that typically come up towards the end of projects.”
The university has completed one Passivhaus-certified building to date: the Student Hub for Kellogg College.
“It is not always possible to deliver a Passivhaus-certified building but the EnerPHit retrofit Passivhaus standard is available for refurbishment projects,” Makkreel says.
“Also, we have become more aware of the carbon footprint of new build, and that now goes into our thinking when deciding on refurbishment or building from scratch.”
She reports “positive experiences” from offsite construction, citing some temporary faculty buildings which had to be operational for five years, with teaching and research laboratories. “We were able to engage with modular contractors, deliver and open the buildings within nine months – and we’re talking really high-quality space,” she says. “We always ask the question on what’s the way to deliver the building, rather than just get an architect to design it.”
Makkreel has been a CIOB member for 13 years and chairs her local hub. “As a client, we are one step removed from the coal face of construction delivery, so the CIOB helps us to be part of that conversation,” she says.
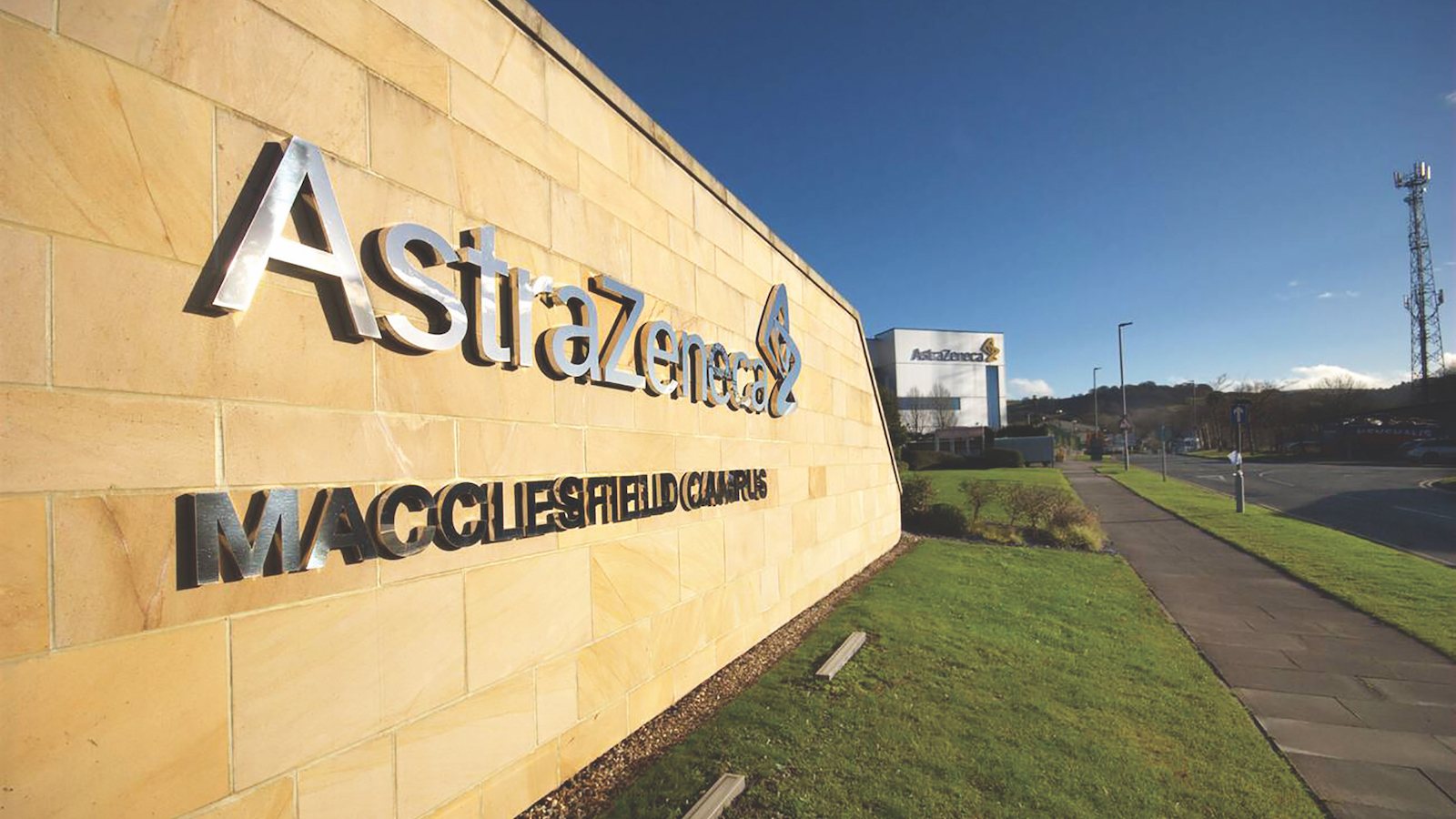
‘A completely different attitude to lump sum contracting’
Brian Street MCIOB – construction lead, AstraZeneca
Brian Street started out in construction with Wimpey Group in 1986, later setting up his own consultancy. He began working for pharmaceutical giant AstraZeneca in 2001 and is currently construction lead on its Alderley Park campus and construction SHE lead at its Macclesfield site.
“In a typical year, we might deliver 80 to 100 projects with £25m in total construction spend,” Street says. “Work ranges from lab refurbishments to offices. The campus at Macclesfield is like a small town, with over 4,000 people working there, plus another 400 at Alderley Park, so all our projects have to be delivered in a busy operational environment.”
Street’s team acts as principal contractor and principal designer, with 40 self-delivery staff.
“We are very hands-on; we don’t just appoint a contractor and wait for the keys to be handed over,” Street explains. “Because of this, we have fewer issues with defects and delays. We still have a budget and timescales we must work to, but there is a completely different attitude to what you’d find with lump sum contracting.”
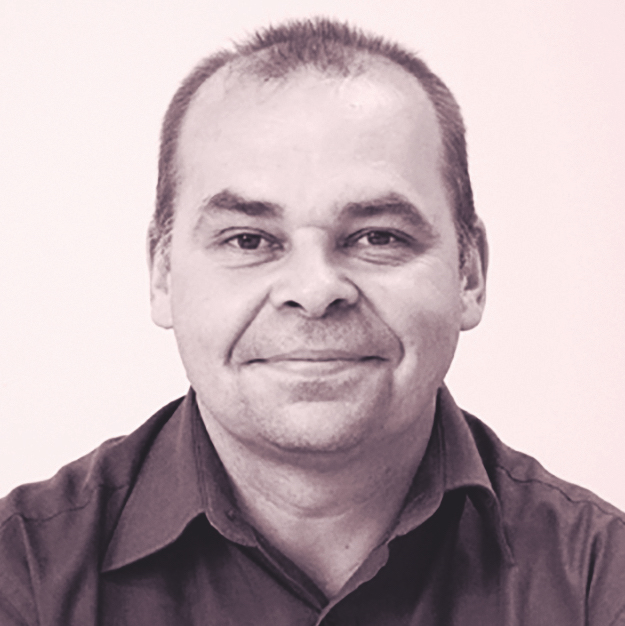
“They operate to very high standards in terms of drug manufacture and that culture
steers us too”
As a manufacturer of critical medicines, AstraZeneca continued operating through the pandemic. Street developed his own covid-19 risk assessment for construction operations, based around the Construction Leadership Council guidelines, which was widely shared and praised by other CIOB client members.
“We can take some positives from the pandemic,” says Street. “We have been forced to ‘microplan’, so we could know not just which subcontractors were coming onto the site but also the names of individuals, a week in advance. The benefits have been fewer surprises; our suppliers have had to plan better else they cannot bring workers or deliveries onto the site.”
Street says there is a very heavy quality focus at AstraZeneca. “We can’t hand over a production line to the operations team which doesn’t work,” he says. “They operate to very high standards in terms of drug manufacture and that culture steers us too.
“Quality management KPIs exist on all projects here and we set the bar high – at zero defects. We achieved that on 87% of all projects in 2019.
“We have a long-term relationship with our supply-chain partners and they understand our quality expectations – they don’t just rely on an end-of-project snagging process.”
Street became a CIOB member early in his career. “I saw it as a key professional qualification and I still do,” he says. “As a client, the networking benefits have enabled us to share experiences about many issues affecting construction and this has been very valuable professionally.”
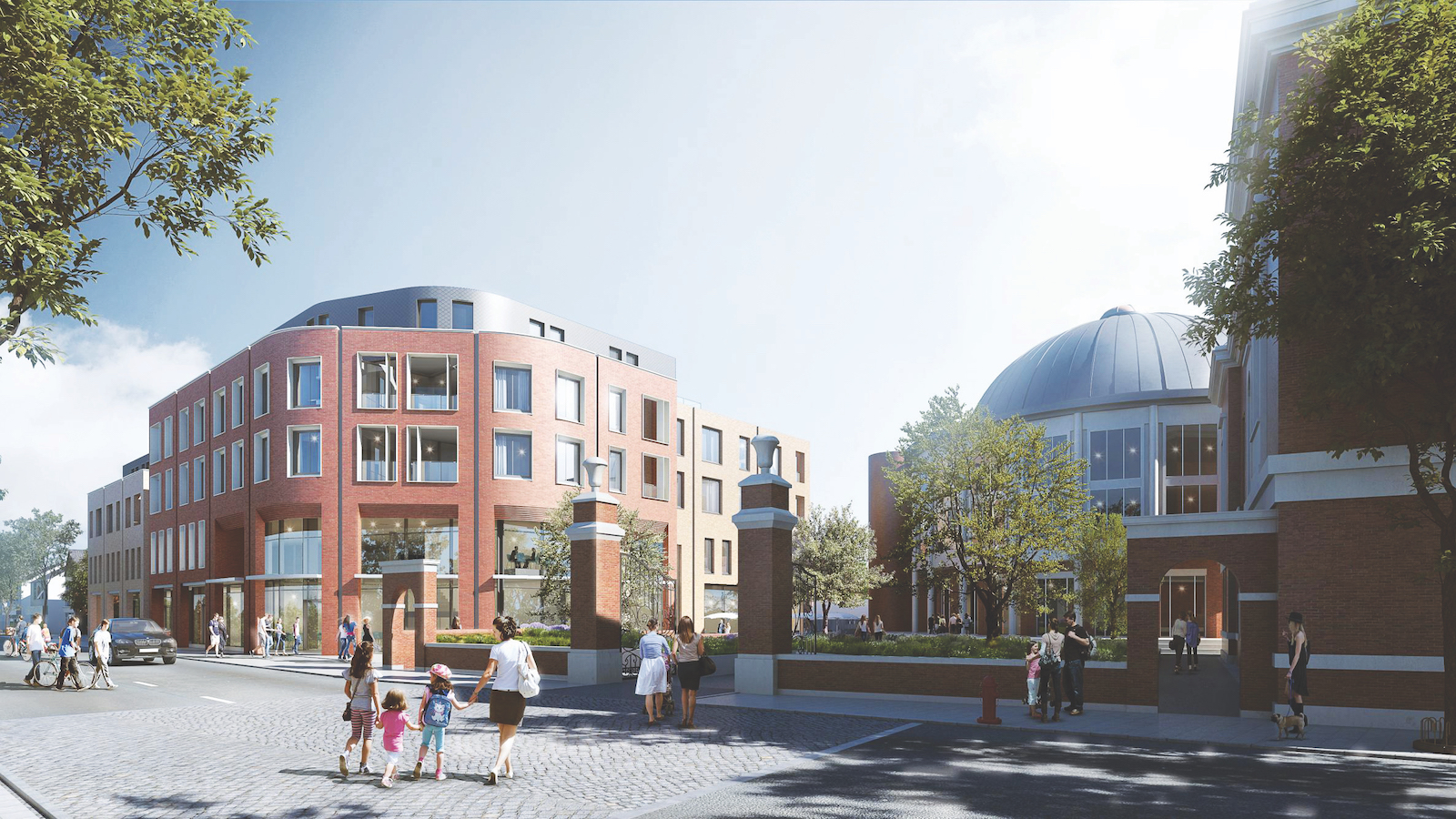
‘We take a progressive approach to working with contractors’
Ray Ford FCIOB – construction director, strategic investment, Braintree District Council
Ray Ford has worked in construction for over 40 years, for major contracting names including Taylor Woodrow and Bovis Lend Lease, before switching to the client side a decade ago. For the past 18 months he has been construction director for Braintree District Council’s strategic investment team.
“Braintree created the team to manage their £100m investment in property development which helps augment their spending budget,” Ford explains.
Braintree has three projects under construction, with several others in the pipeline, and uses frameworks to appoint the project team.
The biggest live project is Manor Street, the £35m redevelopment of Braintree town centre, where Kier is contractor. Horizon 120 is the £24m transformation of a 26ha field on the A131 into a business innovation park, where Balfour Beatty is delivering the infrastructure works.
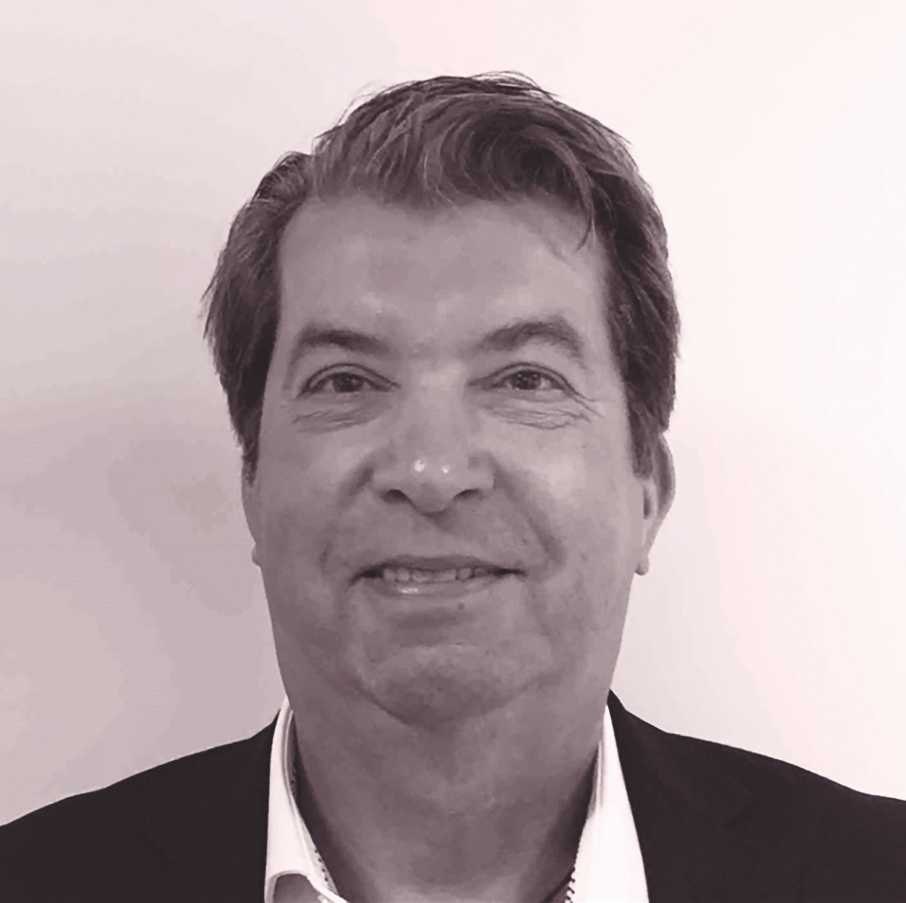
“We work with ‘Premier League’ main contractors and expect compliance and excellent quality”
Ray Ford, Braintree District Council
Braintree’s third live project is the £2.5m I-Construct Innovation Hub, where construction SMEs can learn about BIM, modular building, robotics and other innovations.
“Investing in BIM and other associated technologies is expensive for SMEs,” says Ford. “Here, they can learn how these technologies work, how it can help develop their businesses, and make an informed investment decision with potential grants.”
Braintree has taken “a progressive, collaborative approach to working with contractors” through the pandemic, Ford says. Manor Street was on site when covid-19 struck and delays to utility works outside the contractor’s control caused an eight-week hold-up.
“We worked alongside Kier to re-sequence the project, paying them a premium so we didn’t lose time; we have tenant agreements to honour,” he explains. “On I-Construct, we extended contractor Beardwell’s contract from 38 weeks to 42, recognising that social distancing meant the interior fit out would take longer.”
Most of Braintree’s property falls outside the scope of the Building Safety Bill but, even so, it has changed the specification in places. “On Manor Street, the balcony decking was designed as timber, a Class B fire-rated material, but we’ve gone for a Class A ceramic decking material,” Ford says. “We’ve also appointed a consultant to check all the cladding specification and installation.”
On the Manor Street residential units, Ford says Kier is taking photos of every fire barrier in every flat, to be incorporated into the health and safety file and handover pack.
“We work with ‘Premier League’ main contractors and expect compliance and excellent quality,” Ford says. “I also insist that every scheme has a resident clerk of works.”
Ford believes CIOB membership is an “extremely important badge and an indicator of a quality and professional manager”.
He adds: “I look at the contractor teams working on our projects, and if any of them are not CIOB members, I will mentor them, as is the case currently with a Kier project manager on Manor Street.”
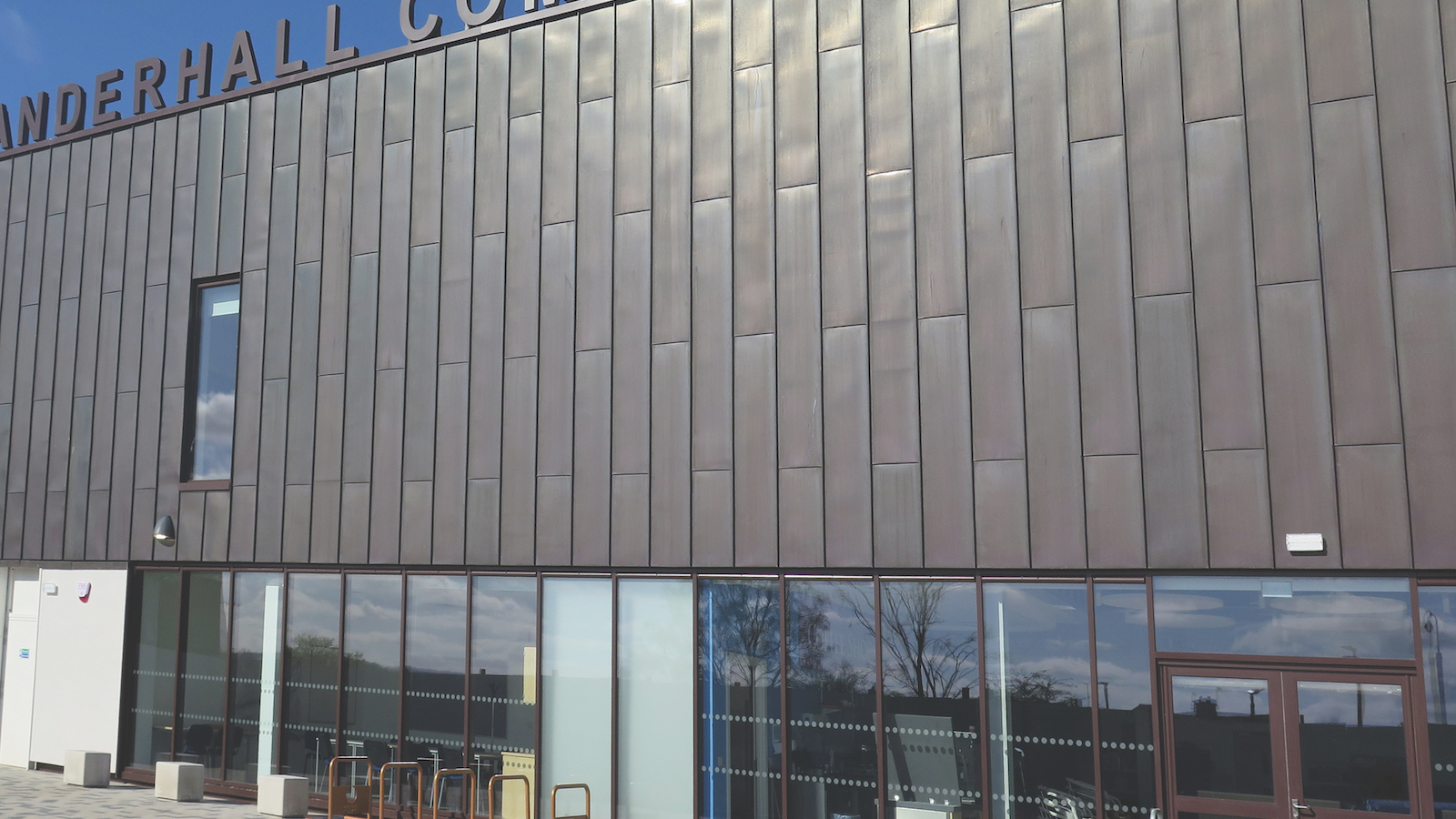
‘There is a push for more community benefits from projects’
Maurice McCann MCIOB – director, McCann Estates
Maurice McCann spent 15 years with Ogilvie Construction before moving client side with developer Macdonald Estates in 2007. In 2009 he started McCann Estates.
“We act as development managers, pulling together and delivering projects, helping public clients achieve better outcomes from their investments,” he explains.
His first scheme was Lasswade Centre in Edinburgh, a pilot for the Scottish Futures Trust, and the latest is the £16.8m Danderhall Community Hub, a primary school with library, leisure centre, nursery and cafe, for Midlothian Council. “Our approach has strengthened communities and improved income streams for our clients so services become much more sustainable,” he says.
Since covid-19 struck, McCann says clients are looking to bring their capital plans forward. “One is bringing forwards schools planned for delivery in 2026 to the next two years,” he says.
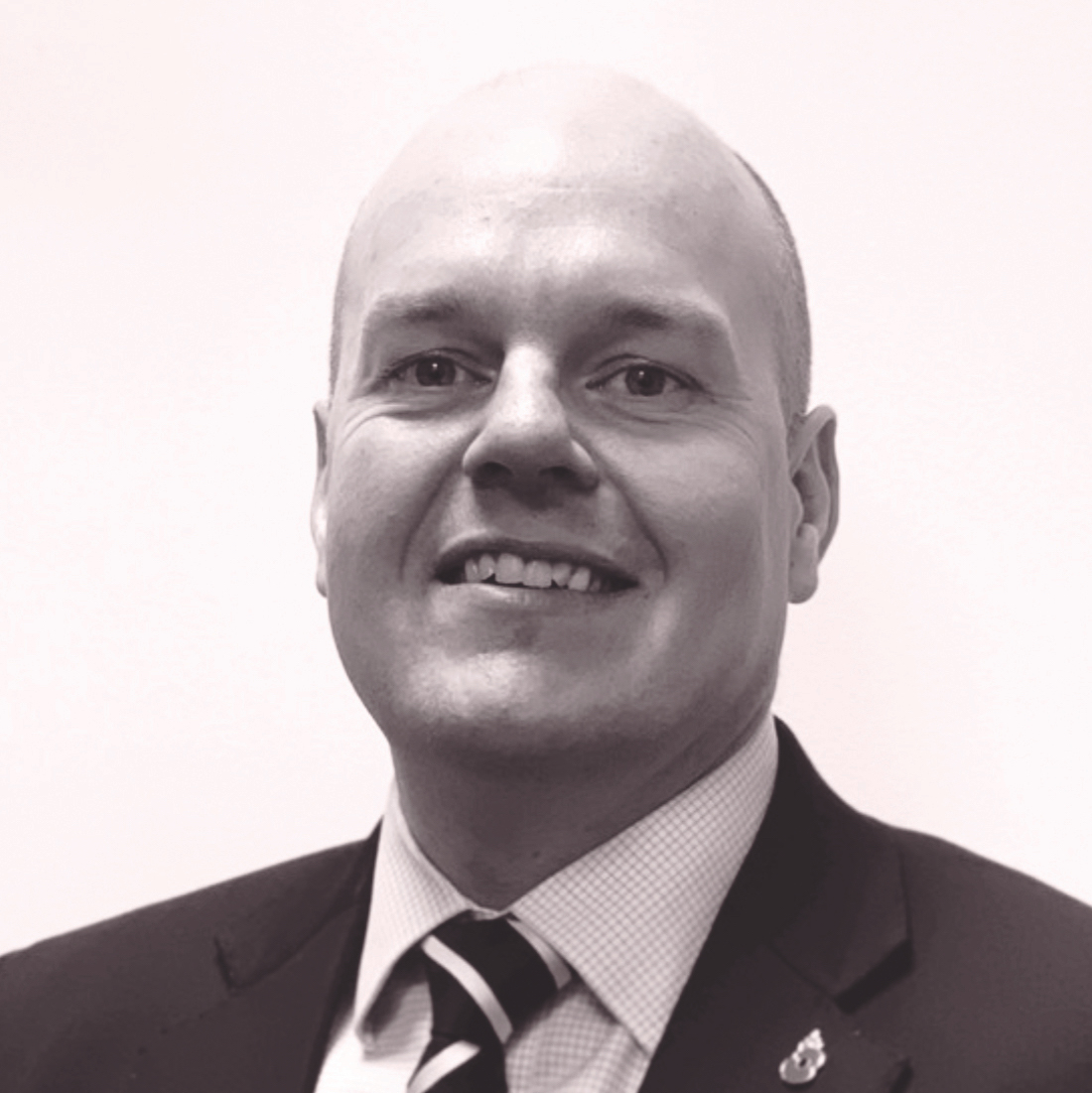
“We have an obligation to ensure the specification is clear so contactors price product rather than risk”
“Sharing the pain” has been his policy on contracts during the pandemic. “Our contractor on Danderhall was meant to hand over in October but we moved that date to February,” he says. “We know we will all pay the price as clients if in three years these companies disappear and prices in the industry begin to increase.”
Edinburgh is where quality concerns first emerged, after the Oxgang School wall collapse. Standards are being watched “closely” in Scotland, he says.
“We oblige designers to report back to us on work progress and our appointment documents are set up to reduce the contractor design portions to a minimum,” he says. “Too often consultants tendering for work will increase the number of contractor design portions to keep their fees low.
“This is counterproductive for clients who end up paying for the lack of clarity through quality of the product.
“We have an obligation to ensure the specification is clear so contactors price product rather than risk. Contractors are good at buildability and logistics, not sorting out a design that hasn’t been put together properly. Because we put the work in before we go to tender, we tend to achieve a better quality of product at a more economical price.
“We need quality to be on a level with safety and I want to see contractors treating it just as seriously. ”
He also wants contractors to deliver more training: “In Scotland, there is a big government push for more community benefits from developments, including apprenticeships, and we include these obligations into all of our contracts.”
McCann is pleased by the “huge drive” to adopt digital technology in Scottish public sector investment but warns of “a digital skills shortage”.
“We advise our clients to approach the digital agenda with a collaborative agenda, developing the skills working with contractors,” he says.
Through the CIOB, McCann finds knowledge-sharing of best practice with other clients “really useful” and would like to involve contractors “so that both sides can have open and collaborative dialogue around issues faced by construction”.
“The CIOB is uniquely placed with members from all areas of our industry,” he adds.