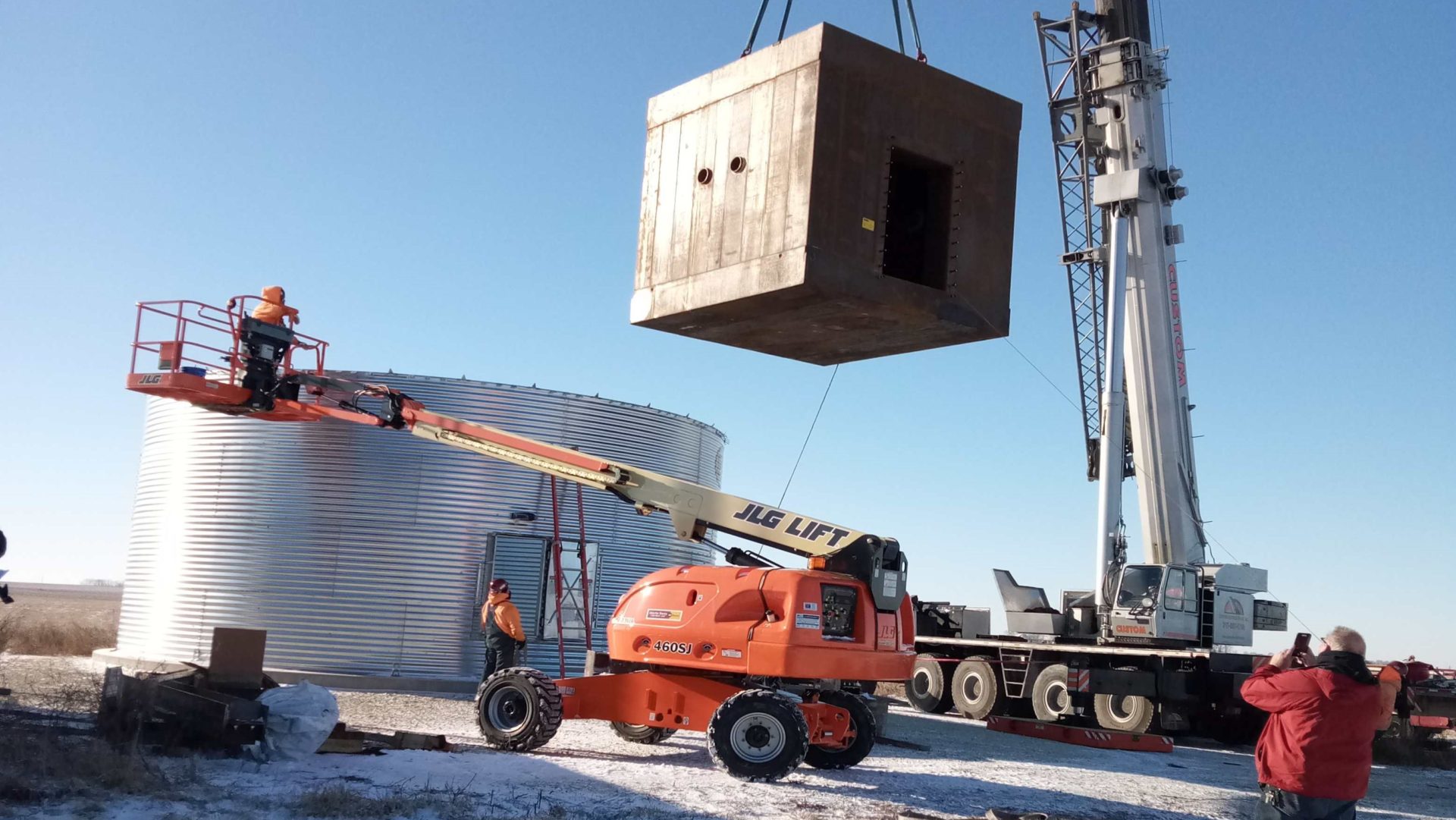
A modular steel construction system developed in Scotland has been used to construct a ‘blast box’ in the USA for explosive testing as part of a research programme on advanced warhead technologies for the US Department of Defense.
The Steel Bricks system has been developed by Modular Walling Systems based in Renfrewshire and will be used to create an ultra-strong 3m3 chamber for the University of Illionois and Urbana-Champaign’s testing programme.
The blast box will comprise two steel face plates internally connected to create a ‘sandwich’ panel. The steel structure is then manufactured off-site as a single piece, before being filled with 72 tons of self-consolidating concrete in a continuous pour once installed.
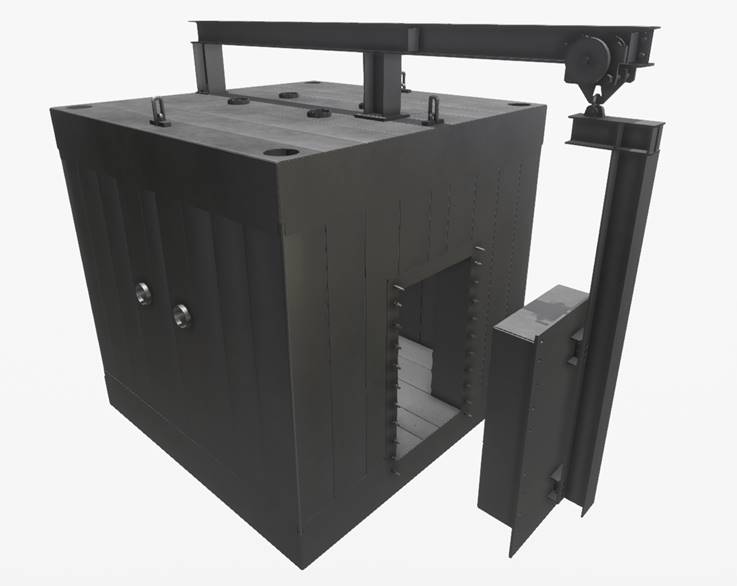
Dr Stewart Gallocher, founding director of Modular Walling Systems, said the proprietary process which gives the blast box its strength, as well as reducing on-site time and labour costs, could also make it suited for the global nuclear Small Modular Reactor (SMR) market, estimated to be worth US $1.2 trillion (£870bn) globally.
Dr Gallocher: “The Steel Bricks system, with trademark diaphragm holes running through the webs, has been assembled in such a way that the concrete is poured through holes in the roof, flowing down the walls and filling the base mat before coming back up the walls and lining the ceiling – all in one continuous pour.
“This is a ‘first of a kind’ concept in the fast-emerging world of steel composite construction and proves that the Steel Bricks system can provide not only the walls and suspended floors or roofs in steel composite but most importantly a base mat. This takes away the need for conventional foundations, eliminating the traditional Achilles Heel of this form of construction which are the weak points of the base mat to wall connection.”
“Many attempts have been made during the past 25 years to devise simple, safe and rapid fabrication methods to internally connect steel faceplates. But most have lacked commercial application due to being too expensive and labour intensive. We have now proved we can successfully deliver a solution which is technologically proficient whilst providing significant cost and time saving benefits.”
The blast box was fabricated in the UK by Caunton Engineering, at the company’s manufacturing headquarters in Nottingham before being shipped to the University of Illinois at Urbana-Champaign.
Caunton Engineering and Modular Walling Systems are now in discussions with potential customers about a broad range of applications for the Steel Bricks system – including the global nuclear industry. Dr Gallocher said: “The success of the University of Illinois contract shows that the Steel Bricks system is perfectly suited for markets where potentially dangerous materials are being handled and where time on site needs to be minimised. We believe that this technology, combined with the significant cost and time reductions of off-site manufacture, will now provide a major stimulus for the global roll out of Small Modular Reactors.”