When it comes to tackling dust on the jobsite PPE is often considered the go-to solution, but the HSE’s Hierarchy of Control says it should be the ‘last resort’. Matias Jarnefelt looks at the reasons.
Since the start of the Covid-19 outbreak, the availability and quality of PPE equipment has been a constant source of news. Naturally those on the frontline and the most vulnerable are the main priority to receive what is available, but this has led to a lack of PPE equipment for other sectors, including construction.
This has proved a challenge for contractors and tool operators because face masks have long been the go-to protection for any task that generates dust, but what if I told you that the HSE considers this the last control resort?
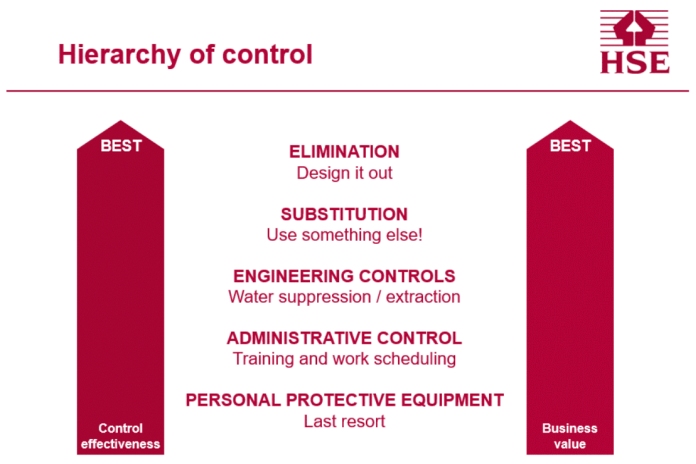
The Health & Safety Executive’s (HSE) hierarchy of control (above) looks at the effectiveness and business value of five different approaches, with the top classed as ‘best’ practice followed by the ongoing steps to mitigate risk. It is a methodical path that should be used with any task that will create dust.
The most effective method of control recommended by the HSE is elimination. The nature of dust and prevalence in the construction industry means that eliminating dust from your jobsite entirely isn’t feasible. In this case, evaluate the task and assess whether the result can be achieved a different way.
If that is not possible you can challenge the task itself. Through substitution, look at different ways of working that can reduce the amount of dust generated. For example, as compared to drilling, are there alternative methods you can use such as direct-fastening or will detection systems help reach the end requirement with less hassle.
The next step, as recommended by the HSE, is to focus on engineering controls. Use dust removal systems (DRS) to extract dust where you cannot avoid generating it entirely. On-tool extraction maximises the amount of dust removed at the source and has the added benefit that less time is needed to set up and clean down working areas before and after carrying out a job.
Administrative controls help identify and implement procedures for safer working. This involves carrying out risk assessments, educating workers through training, and making changes to operations. For example, setting working time limits on applications where possible and rotating workers to other areas of the jobsite to minimise exposure time.
With Covid-19, PPE is in high demand, and there is a worldwide shortage across industries to contend with. It’s considered the least effective method of control and the last line of defence in controlling dust exposure. But again, this carries risks, the question has to be asked whether the mask carries the correct filtration to protect the user from respirable crystalline silica (RCS) dust and has it been fitted properly.
Throughout October, the HSE has been undertaking its annual construction health inspection visits where the focus is on control and knowledge of respiratory risks and occupational lung disease. They are looking at the hierarchical approach to controlling dust on your site and asking what steps are being taken. It is best for all to explore the most effective options first and reducing risk to workers in the process.
It’s time for the construction industry to act on dust. On 5 November, join our webinar on the impact of dust and hear from leading industry experts as they evaluate the current landscape and issues surrounding dust exposure.
Matias Jarnefelt is the managing director for Hilti