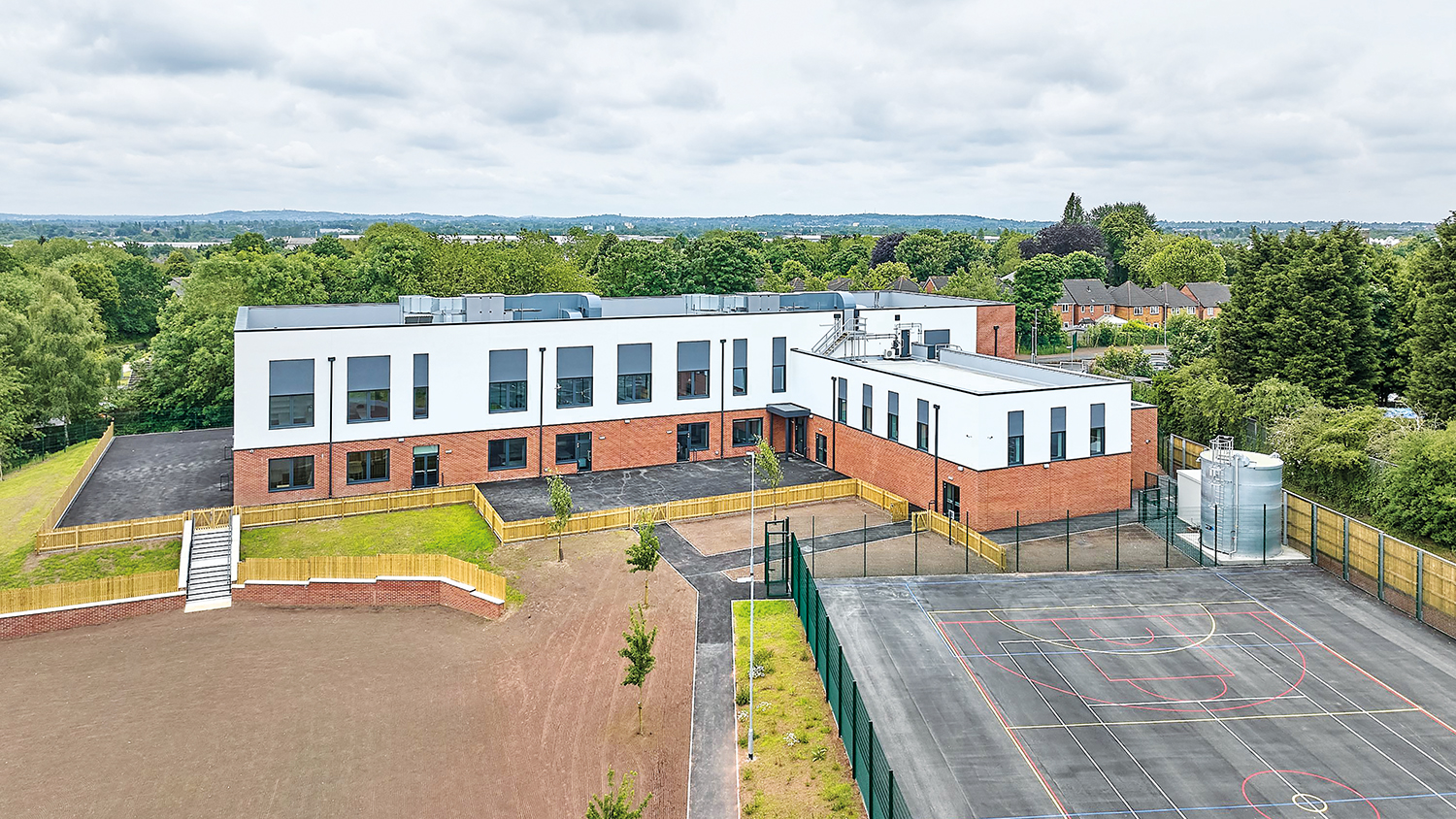
A Passivhaus school in the Black Country has required a whole new level of rigour from Tilbury Douglas. Kristina Smith visited the project ahead of its handover for the new autumn term.
There’s one word that keeps coming up on a tour of Tilbury Douglas’ Wednesfield Technology Primary School project: meticulous.
Built for the Shireland Collegiate Multi Academy Trust (SCMAT), on behalf of the Department for Education (DfE), this is a Passivhaus-standard school project. There’s no room for ‘good enough’ on this project; to get accreditation from the Passivhaus Institute, everything must be bang on.
Wednesfield Technology Primary School
Cost: £11m
Client: Department for Education/ Shireland Collegiate Multi Academy Trust
Programme (including demolition): February 2023 to June 2024
Form of contract: Design-build, DfE construction framework
Contractor: Tilbury Douglas
Designer: Corstorphine & Wright (C&W)
Timber frame: Timber Innovations
MEP: Dodd Group
“This is one of the most challenging projects I have had,” says Tilbury Douglas project manager Kevin Miners. “It’s certainly the most meticulous I’ve ever been on.”
From the design and execution of joints and other details to the materials used to the collation of information for every piece of kit, the Passivhaus standard requires all the ‘t’s to be crossed and the ‘i’s to be dotted. For Tilbury Douglas and its supply chain, that has meant extra attention to detail – and extra time taken – particularly on the floor slab and the joints for the timber-framed system.
DfE framework
The school was tendered under the DfE’s 2017 construction framework back in 2020. “This is a flagship project for the client,” says Matt Lakin, contracts manager for Tilbury Douglas. “Passivhaus is not just about applying sustainable design to save the planet, it’s about saving money for the schools too.”
Wednesfield Technology Primary School is a two-form entry school which will eventually take 446 pupils. The main part of the building is a rectangular block with classrooms located over two storeys: nursery and younger children on the ground floor and older children upstairs, together with a small library and a SEND (special educational needs and disabilities) room. A smaller, one-storey wing joins the main one at right angles, housing a multi-purpose hall and kitchen.
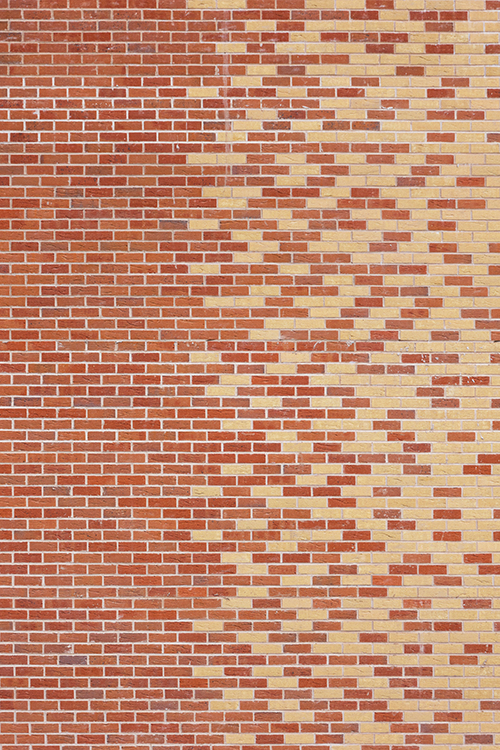
This will be the fifth school that Tilbury Douglas has built for this trust. That gave the contractor and its designers an advantage when tendering, says James Edwards, associate architect at Corstorphine and Wright (C&W) Architects, which leads the design team.
When bidding through the framework, contractors are given a control design which has been produced by the DfE’s architects, in consultation with the school involved. Bidders then have a short time – around four weeks – to price it and propose any changes.
The trick is to deliver both the generic requirements for DfE and the specific requirements of the trust or school, explains Lakin. Bids are then assessed on cost, quality and programme.
Tilbury Douglas had delivered other technology schools for the trust. The idea of these schools is that the children work with digital equipment and tools from the earliest stages so that they are equipped to work in a technology-driven world.
Start on site
Tilbury Douglas started on site in February 2023, demolishing the one-storey Edward the Elder School building, which had been vacant since 2007. Most of the demolition waste has been used to level up the site – which required up to 2.5m of fill in places – and some of the bricks were retained.
Once planning permission was granted, Tilbury Douglas faced its first Passivhaus hurdle. The building sits on a raft foundation, with a double layer of insulation under the slab. The joints of the insulation are staggered, to prevent heat loss, and the insulation extends all the way under the upstand and around the edge of the slab.
“All the pieces of insulation were hot wire cut so that they were dimensioned exactly to the millimetre,” says Lakin.
Like every detail on this school, it had to be modelled, explains Edwards. “We had a Passivhaus designer who modelled every detail in 3D,” he says.
Each joint has to be individually assessed on site, with evidence – including photos – supplied to the Passivhaus designer and then on to the Passivhaus institute. Tilbury Douglas’ Passivhaus champion on this project was site manager Ben Howman, whose job it was to scrutinise every element of the build.
Achieving airtightness
The need to prevent cold bridging and achieve airtightness at junctions caused a few extra issues when it came to assembling the timber frame, a system called Larsen Truss which was supplied by Timber Innovations, a company located just 25 miles from the site. The system consists of twin walls of timber frames braced together, boarded with OSB internally, cement board externally, then infilled with 380mm of mineral insulation – some in the factory and some on site.
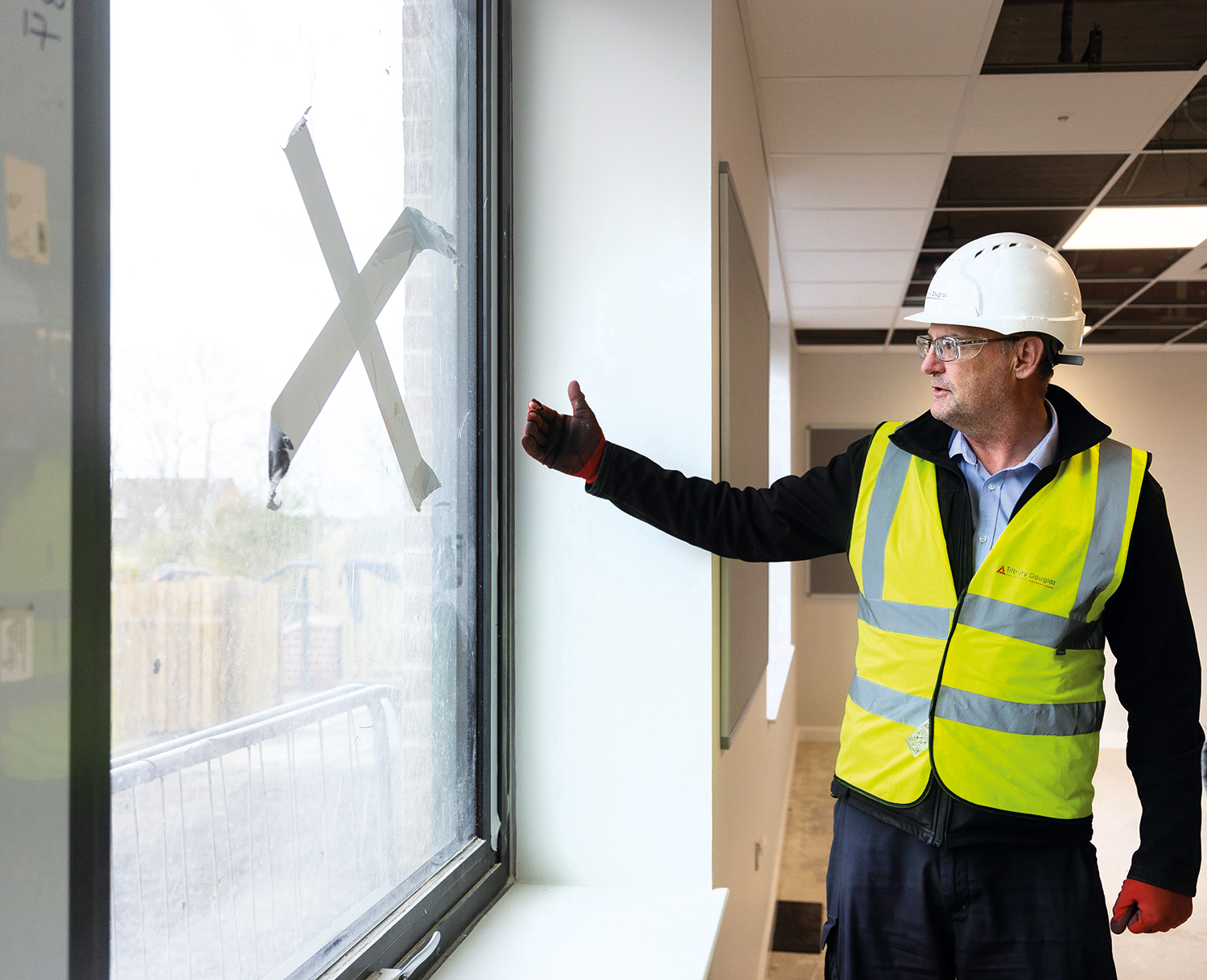
The panels are more usually used for housing projects and the way that adjacent panels are normally joined to each other was not good enough for the school Passivhaus requirements. To overcome this challenge, Timber Innovations delivered panels that had short, unfinished sections at either end, so that the insulation and boards could be installed on site, ensuring there was no cold bridging.
“It took us until January to get the building watertight because it took us a lot longer to do the structure than we had expected,” says Miners. “But taking that extra time to make sure paid off in the end when we had such good airtightness results.”
For Passivhaus accreditation, two airtightness tests must be undertaken, the first when the structure is complete but before fit out. The first one delivered outstanding results, far surpassing the minimum requirement: air changes per hour were 0.225 air changes per hour (ACH) at 50 pascals, well below the required 0.6 ACH. The second airtightness test, carried out when the building was nearing completion, also came in well under the requirement at 0.48 ACH.
Meticulous timing
The building is brick clad – for its entire height on the wall facing the road, with render on the upper parts of the other walls. The brick was a requirement from the planners, explains Edwards, echoing the brick of the school that had stood on the site and of the Vine Inn, a Grade II-listed pub which sits directly opposite, on the other side of the main road.
The brick lodge building for the original school also remains on site. Tilbury Douglas has repointed it, replaced damaged roof tiles and given it new facias, guttering and drainpipes. The school will refurbish it internally, with plans to make it into a community space.
To the back of the school site, which runs along the Wyrley & Essington Canal, there will be a huge outdoor space, enhanced by existing woodlands – whose preservation was a strict part of the brief. The wet weather this year means that Miners is not as advanced with the outdoor elements as he would like, but they are shaping up now.
Tilbury Douglas handed over the new school during the school summer holidays, in time for the autumn term. It appears that the meticulous Passivhaus approach has paid off.
CVs: Matt Lakin and Kevin Miners
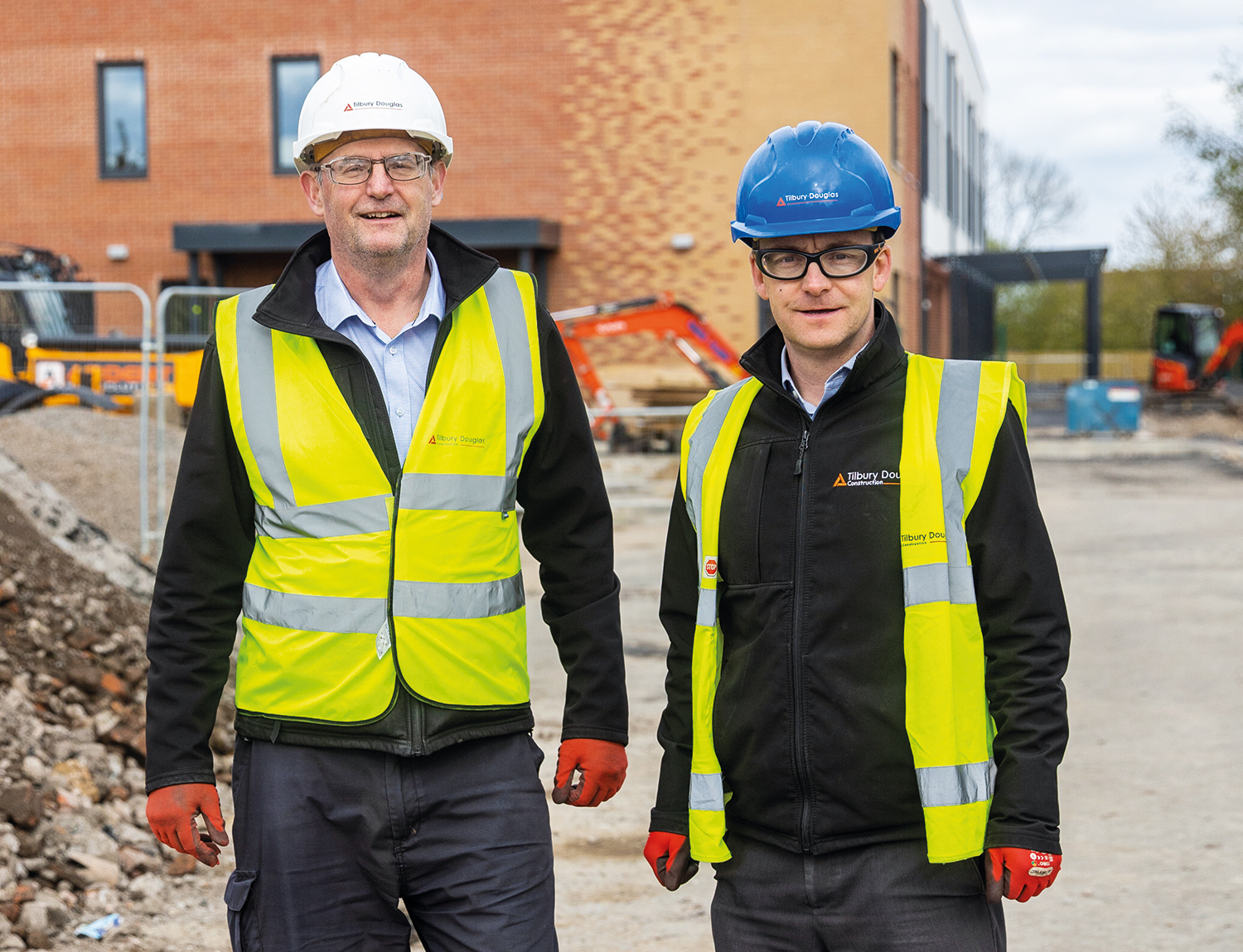
Matt Lakin (above right) began his career in civil engineering. After time spent working on infrastructure jobs including the West Coast Main Line and M6 toll motorway, he moved to the Queen Elizabeth II hospital in Birmingham, working for Balfour Beatty.
He decided to switch from civils to building so that he could be based at home, rather than travelling from job to job: “I wanted to have a life, as well as work,” he says. “And a complex building project like a hospital can be just as challenging as an infrastructure project.”
Lakin has worked for Tilbury Douglas for 10 years, starting as a project manager and moving up to contracts manager four years ago, covering the East and West Midlands in projects from £5m to £30m.
Kevin Miners (pictured above left) has also been with Tilbury Douglas for 10 years, having been with Costain for eight years and Skanska (Trafalgar House) prior to that for 15 years.
Miners was inspired by his father to join the construction industry: “My father was a bricklayer who passed away when I was young and I liked helping him build things,” he says. “I also liked technical drawing and ended up doing a building OND and it developed from there.”
It’s a career that is always gratifying, he says: “You have the satisfaction of completing a project that will be there to be used for many years to come.”