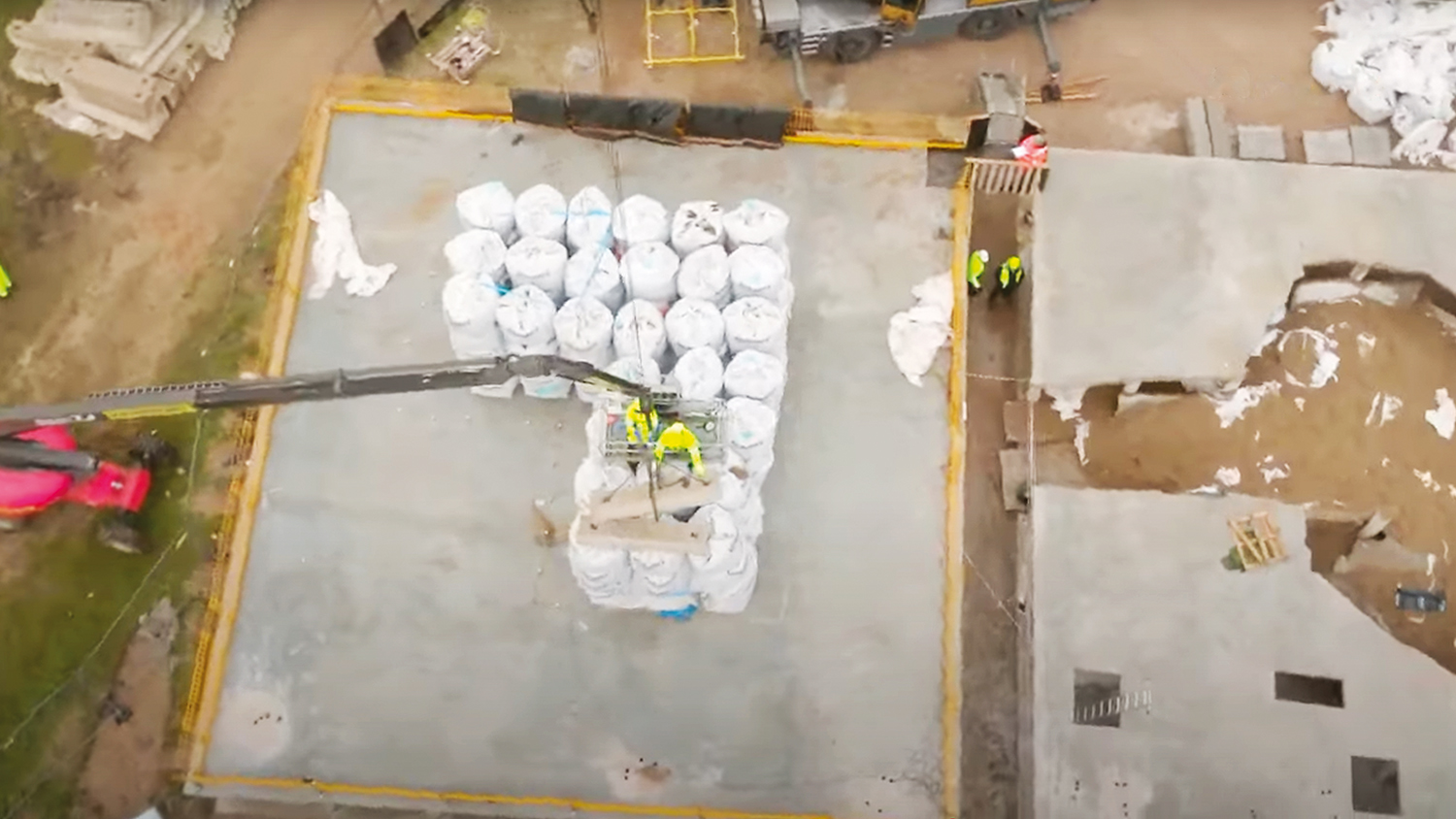
Construction wants to improve its productivity and sustainability – and these emerging concrete technologies could be central to that.
Self-stressing concrete
Arriving in the UK from Latvia is a chemically self-stressing concrete, which contains a patented combination of three admixtures and steel fibres. Called PrīmX, the concrete has been developed by Primekss to be both stronger than conventional steel fibre reinforced concrete and non-shrinking.
A test comparing structural performance of a PrīmX floor slab versus traditional steel fibre-reinforced slab of the same thickness showed the traditional slab collapsing after 159 tonnes of sandbags were added, whereas the PrīmX slab did not collapse until 211 tonnes of sandbags had been loaded on.
Projects in Sweden and Denmark demonstrate how the concrete can be used without joints for the floor slabs of huge logistics and distribution centres. There are four Primekss-approved contractors in the UK.
Self-healing concrete
One of the most developed self-healing concrete technologies – by Basilisk, which came out of the Technical University of Delft – uses bacteria within the concrete to close cracks.
The bacteria are activated by water, multiplying and producing CaCO3 – limestone. Last year, contractor Heijmans Infra installed the self-healing concrete for the first time in the wall of an underground pump room for the Vijfeiken Tunnel in Rijen.
In the earlier stages of development is Mimicrete, which sees polymer-based tubing installed within concrete elements, which will rupture if the concrete cracks, releasing a healing agent.
The Cambridge University startup is working on a project at the Global Centre of Rail Excellence which will look at how the technology could be deployed in railway sleepers and retaining structures.
Recycled cement paste
Another Cambridge University spin-out, Cambridge Electric Cement, is progressing with its project to industrialise the conversion of recycled cement paste back into Portland Cement.
The cement paste – separated out from recycled concrete – is used as the flux material in an electric arc furnace (EAF) used for recycling steel.
After the first successful industrial trial at Celsa UK’s Cardiff EAF was announced
in May 2024, the project raised £2.5m in seed funding in July 2024 from a group of investors focused on decarbonisation technology.
This means that Cambridge Electric Cement, Celsa UK and the other industry partners – AtkinsRéalis, Balfour Beatty, Day Group, Materials Processing Institute and Tarmac – can continue with the development of the low carbon cement.