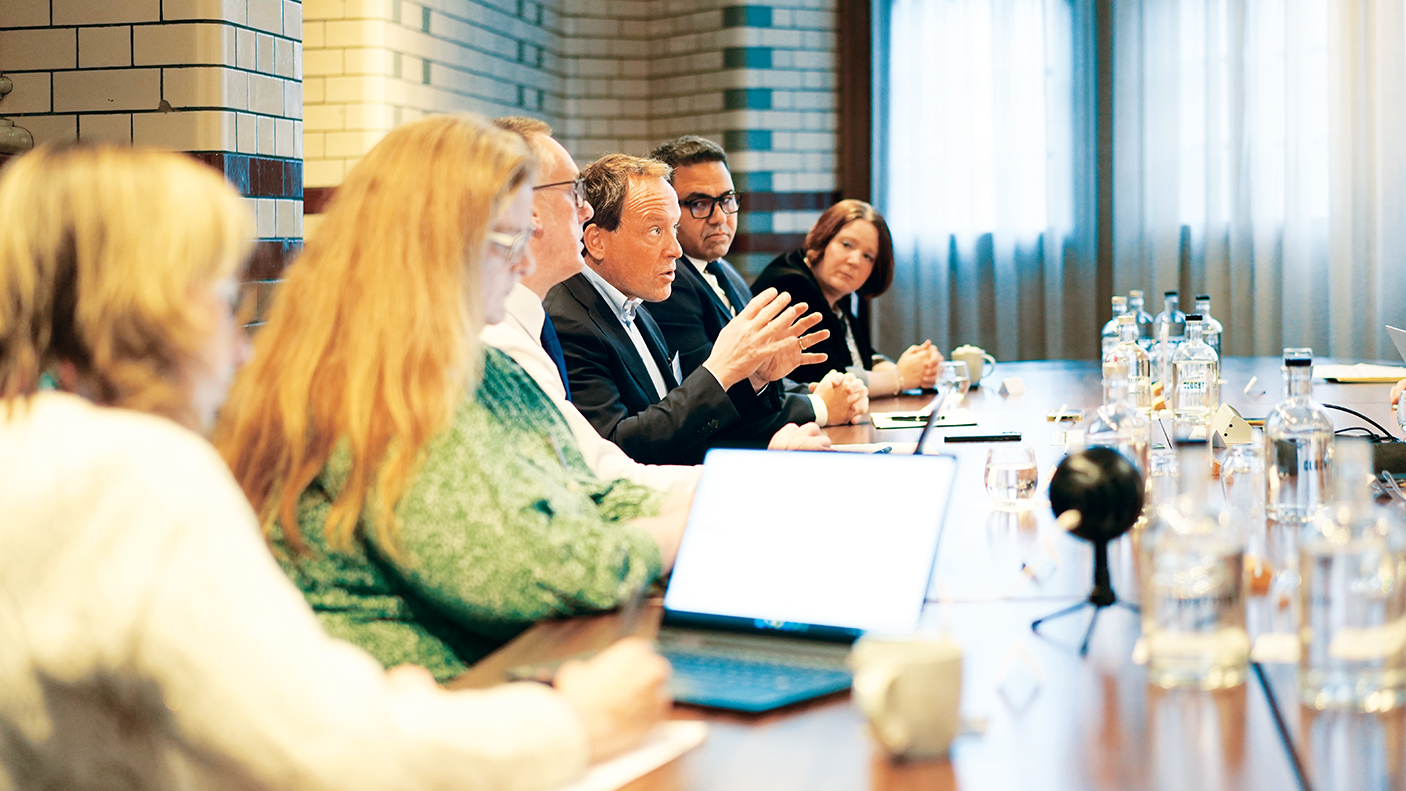
Construction Management, the Chartered Institute of Building and Hilti recently brought together a panel of senior professionals from across the built environment to discuss the industry’s carbon reduction challenge and the role of digitisation. Will Mann was in the chair.
The Panel
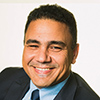
Faiçal Lahmamsi
Chief executive, Colas
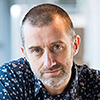
Alistair Kell
Chief information officer, BDP
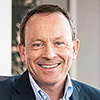
Dr Christoph Loos Chairman board of directors, Hilti Group
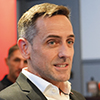
Rainer Ringgenberg
Head of region, Northern Europe, Hilti
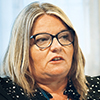
Sharon Turner Group social value manager, NG Bailey
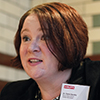
Dr Claire Handby FCIOB Business leadership adviser
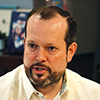
Leigh Carter FCIOB Director, Turner & Townsend

Phil Beaumont FCIOB Head of integrated management office, Costain, and CIOB trustee
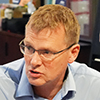
Professor Chris Gorse MCIOB Prof of construction engineering and mgmt, Loughborough Uni; chair of CIOB sustainability advisory panel
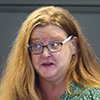
Elizabeth Edgington Group carbon and sustainability manager, NG Bailey
Will Mann: According to the World Green Building Council, the global built environment is responsible for 40% of all carbon emissions, which includes day-to-day operation of structures, plus transporting materials to a site, and 10% coming from the embodied carbon present in the building materials themselves. How is the construction industry going to clean up its act?
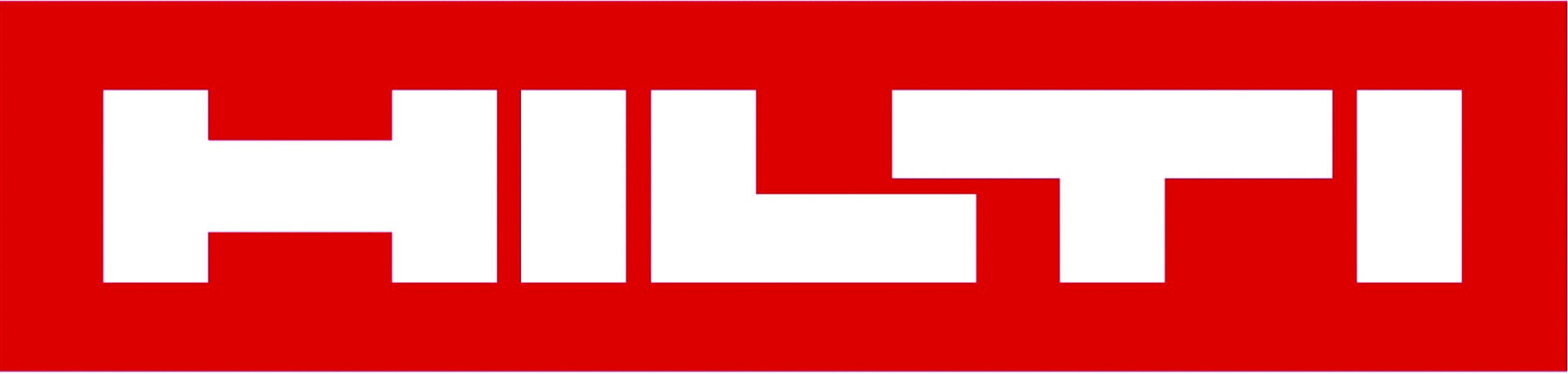
FL: Too much blame is laid at the door of the construction phase of a project. It’s important to consider the whole life cycle of a scheme. Take a major highway project, for example. The construction element contributes a fraction of the emissions that the road users will generate. Scoping is very important when we’re talking about sustainability. And not just focusing on the construction phase, but also much earlier in the process, when it comes to designing a project.
CH: Improving productivity through better collaboration is a way forward to a more sustainable future. We need to create a sustainability culture across the industry, and understand where we’re all coming from, from designers through to subcontractors and manufacturers. We need a supportive consequences culture as well, in light of the Building Safety Act. And the introduction of carbon auditing would focus people’s attention on their bottom line, especially if firms missing carbon targets faced the prospect of a fine.
RR: The supply chain is super-fragmented. We have a lot of different parties on site, all working on their own part of the project. There needs to be greater clarity and transparency around who is doing what. We need to work with suppliers who have a proven track record in sustainability. Suppliers who achieve EcoVadis certification are rewarded and we try to reuse as much material as we can [when a tool is returned to us at the end of its working life]. We achieve around 27%, whereas the average in construction tools is around 9%.
Science-based targets
ST: Part of my remit is to work with our supply chain and ensure they’re working to the same social values as us. Around 75% of our supply chain want to have science-based targets in the future. It also helps that they are on board, firing over a lot of questions in relation to sustainability and what we’re doing to produce it. Our KPIs around suppliers relate to their efforts to lower their carbon footprint and what they are doing to achieve that.
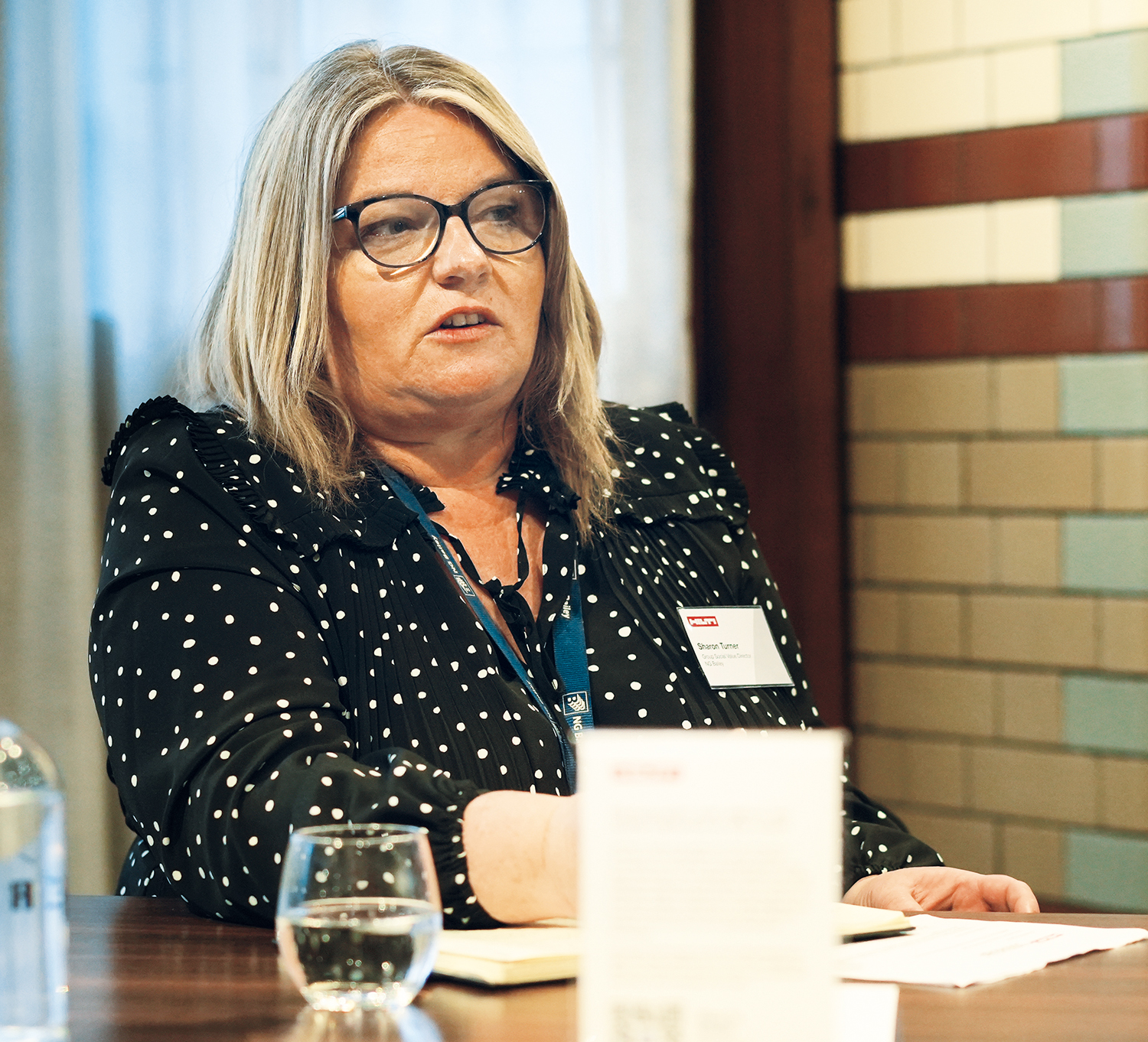
AK: There needs to be some sort of mandatory dutyholder role within an organisation, whose responsibility it is to ensure that that company meets its carbon emissions targets. That could be a gamechanger for the industry, but how that is likely to play out through legislation is open to question, particularly with the current government moving away from legislation around environmental issues rather than showing it is determined to tackle the problem through parliamentary action.
CL: If we can have better data transparency, and appreciate what that data is telling us, then we can do a better job. On a wider scale, we should look at the cost of carbon. As long as we don’t set targets for companies, don’t apply a cost to carbon emissions and punish those who don’t meet those targets, we will not move forward. Also, better design can help lower overall carbon emissions by making better use of fewer materials. And of course we have to look at the entire life cycle of a building when determining its carbon output.
PB: The issue of a material’s provenance is important, especially when we’re talking about sustainability and ESG areas. At Costain we’re keen to see where a material has come from. Is that bauxite ethically sourced? How has that aggregate been produced?
Minimising transportation of materials, where possible, is another area we want to address. And reducing waste. People seem to accept 5% waste, but why should that be? You see lots of materials left over after a project is finished. We should be managing that better.
EE: Much of what we’re all trying to achieve can be affected by our customers. We can work with them to try and persuade them about carbon issues, get to them to shift as well. But until they get on board it can be very difficult.
A construction firm can be environmentally committed but investment is going to be difficult if the customer isn’t interested; the nuts and bolts of sustainability simply just aren’t sexy. We must get the carbon reduction message across better, and we need to support our customers to show them the way on sustainability.
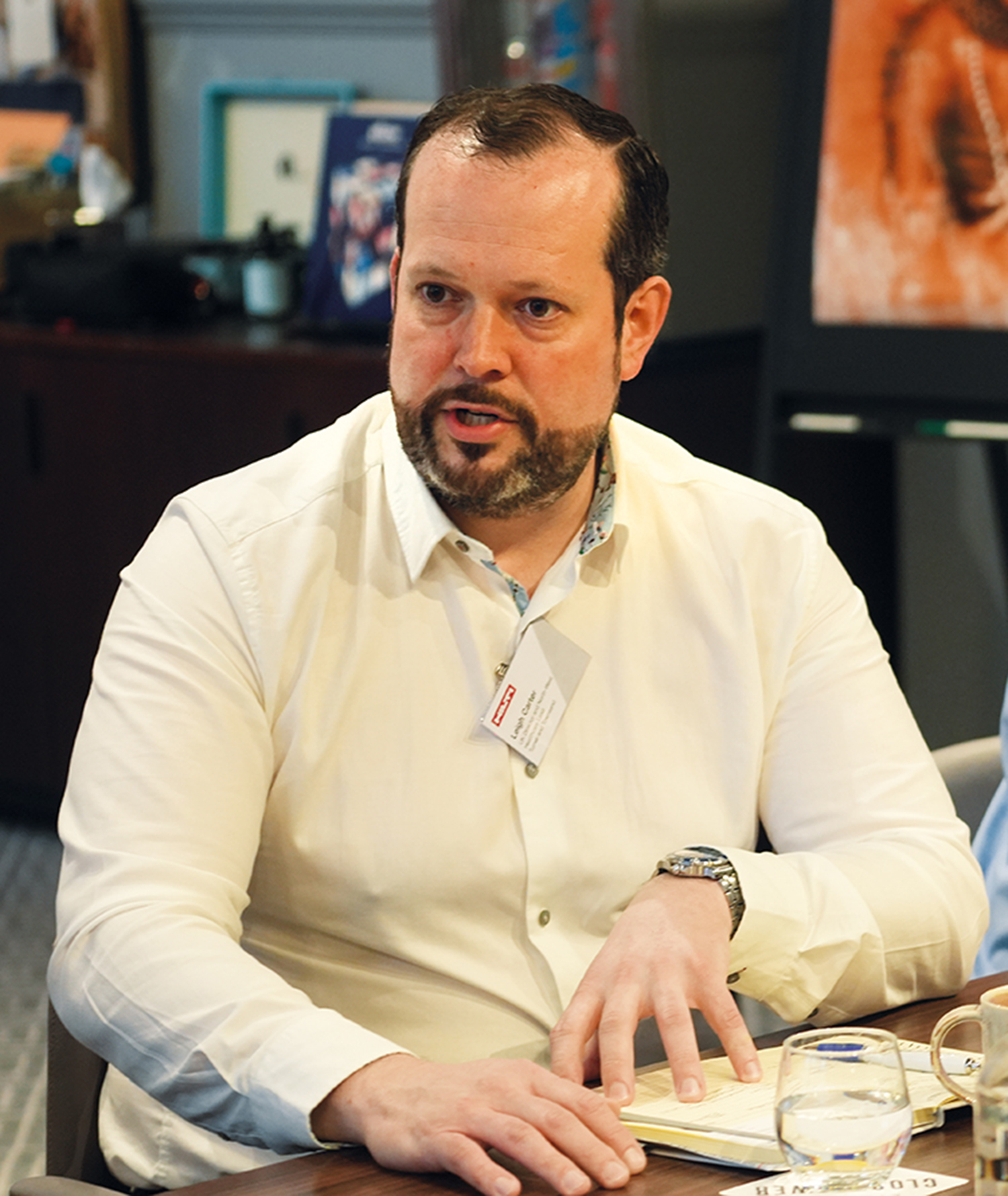
CG: Uppermost in my mind is the integrity of the information, the data, that we’re working with. Currently there are significant gaps in the information on many building products in use, gaps in the services the industry offers, and significant gaps in terms of the carbon databases being used and how we calculate embodied and operational carbon of a building.
The quality of information across the industry can vary considerably, but as a sector we have to step up, take a lead role and improve this. We have to improve the integrity of the information being relied upon.
WM: How do you think digitalisation and new technology can help with reducing carbon emissions?
LC: We’ve worked on a hospital building programme, where we’ve standardised rooms and modularised the process. The starting point is reimagining what a hospital is.
Rather than taking up space in an acute hospital facility with offices, we ensured the building had the digital infrastructure so doctors could meet patients virtually, which saved them travelling to the hospital. The potential around standardising hospital design means people don’t have to design from scratch. That’s going to save a lot of carbon, we believe.
AK: A key point here definitely concerns the materials. And having a materials database. It’s about agreeing a standard set of information that we require from every manufacturer.
That’s going to allow us to understand within our design work what the embodied carbon actually is. It’s going to begin then to allow us to utilise emerging technology, such as AI, to help inform better decision making in the design process.
And that’s also going to force the material suppliers to improve their processes, leading, hopefully, to fewer emissions.
CG: We’re making progress on simulation tools but they still rely on performance data that is embedded in the tools we’re selecting. And we’re sticking with products that are known quantities that we’ve tested. People make assumptions for products we haven’t tested, and it’s those assumptions that present risks.
Changes can be made to a product on site, such as on a cladding system, and consequently it doesn’t perform as expected. Ad hoc adjustments like that can cause real problems, particularly in terms of a facade’s integrity.
RR: One area which can help is services, hardware and software. We have a lot of requests from customers who want to improve sustainability by having fewer materials in a project. Greater use of BIM, plus having more people, more engineers out in the field and better back office support all helps. Plus we’re seeing customers switching from fossil-fuelled tools to battery-powered ones. One made the switch and removed 50,000 litres of gasoline per year from his cost base. Good news environmentally too.
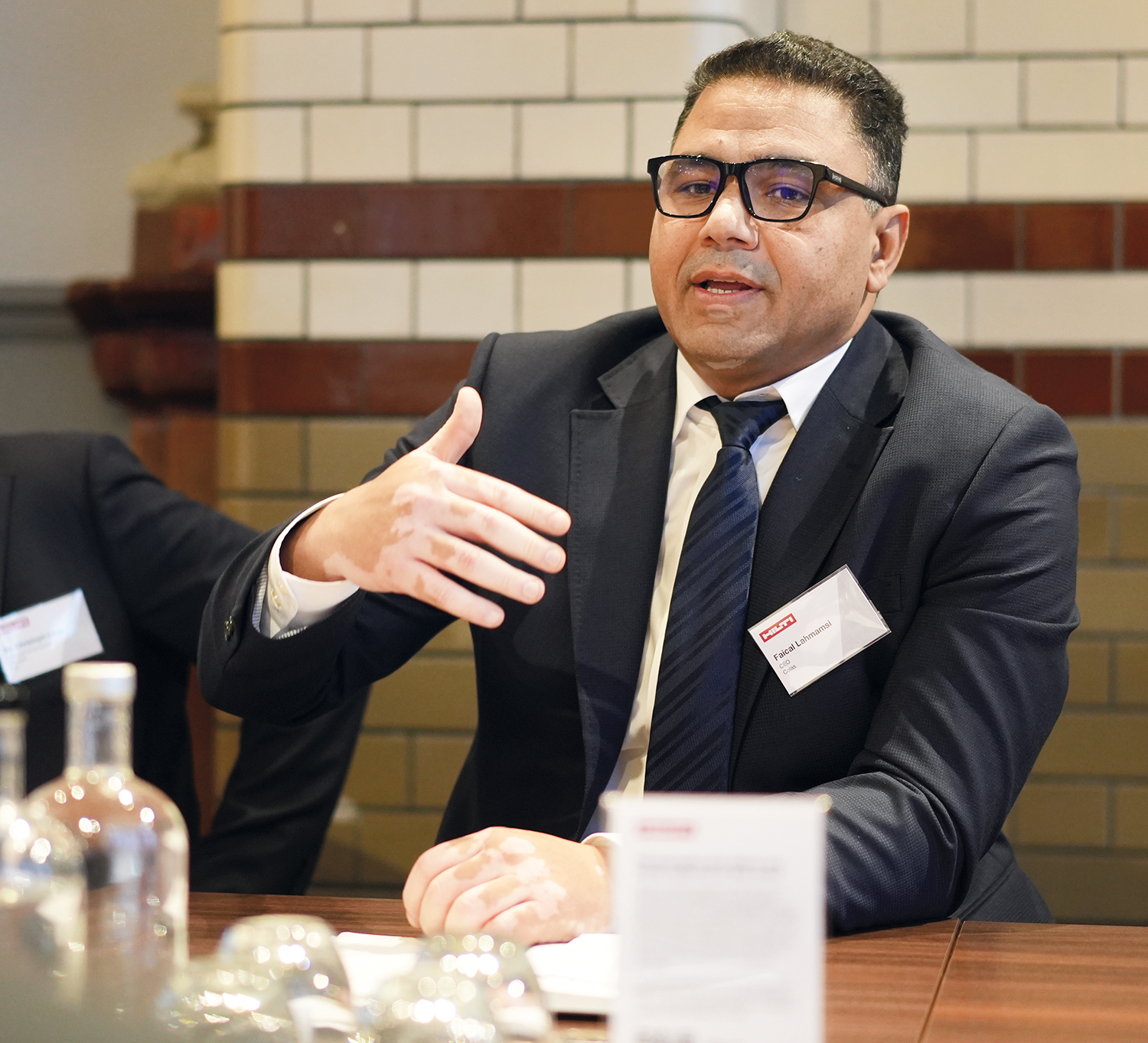
ST: We’ve run a design and build programme called ‘Engineering Your Future’. It includes BIM obviously, and covers how students can make buildings greener and more energy efficient through product selection. Plus we employ digital technology to measure our social value, and we have KPIs used to assess how this situation is progressing.
FL: We’re developing a large number of digital solutions globally and have recently introduced some to the UK. One of these, called Anais, uses data already installed in vehicles to monitor and assess driver behaviours. It can help with road network management by enabling remote identification of an issue through its behaviour change warning system.
We have another digital tool which creates a map of an area, like a Google Maps for the construction activity, called 2IN (pronounced ‘twin’). It brings together a wide range of data about buildings, roads, underground infrastructure, etc.
The issue is whether we as an industry have the skill sets for our technological ambitions. We’ll need universities and other educators to develop programmes so that we have the skilled people we need.
WM: Is digital adoption making construction more productive and more profitable?
PB: I feel we have to demystify some of the language around digital technology, and perhaps drop the term ‘BIM’ and simply refer to the wider concept and requirements of information management in line with ISO 19650. Many people don’t appreciate what it means. We need to come up with better ways to get those who perhaps don’t connect with digital technology to do so. And the language used may be a place to start.
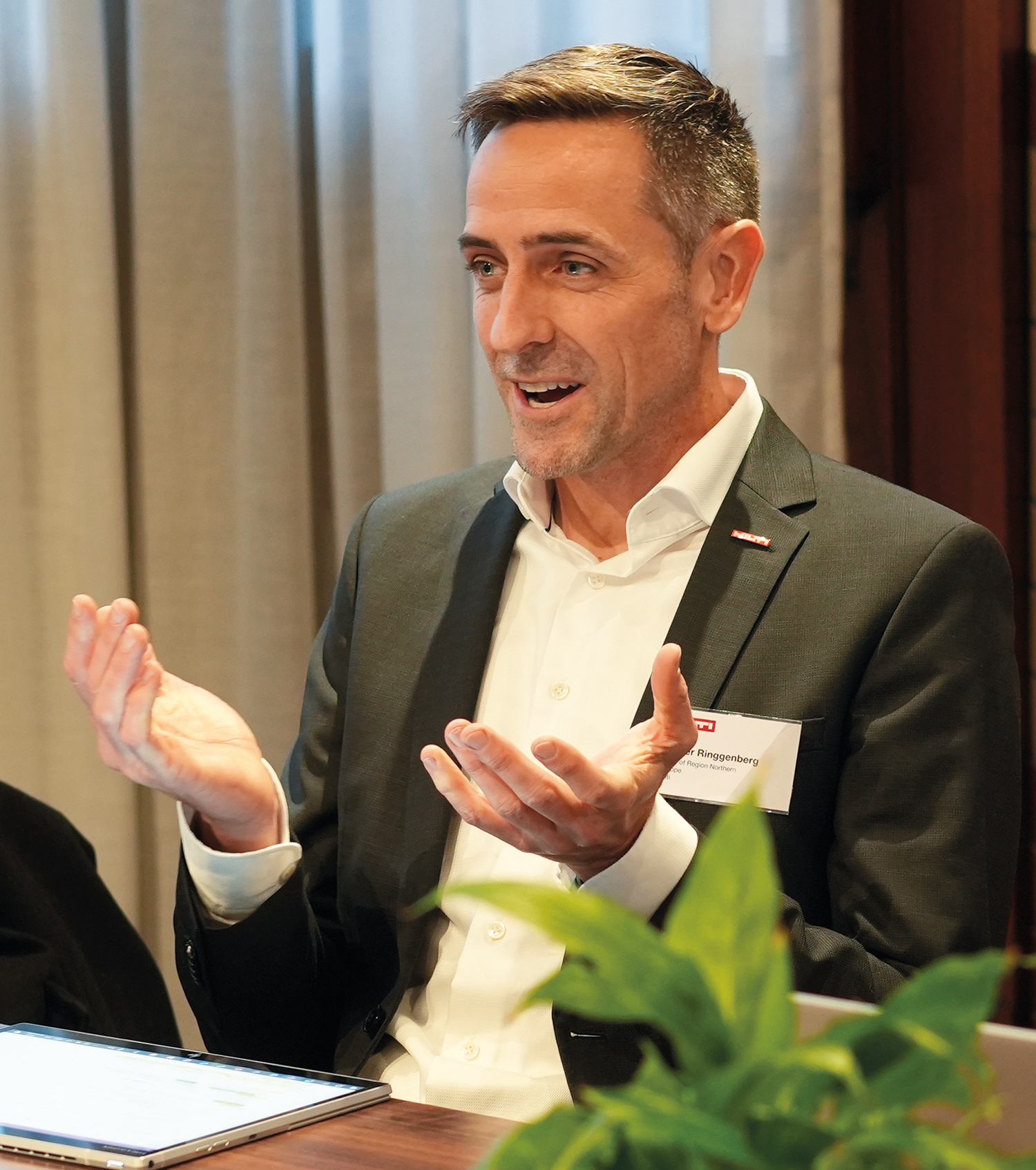
EE: We’ve been looking into waste measurement, and clearly digital technology is going to play a big part in how we improve our assessment of waste generation and how we can reduce it. It’s obvious that we need to be embracing these things, although the thought of having even more data to go through is rather overwhelming.
LC: We’re really focused on pushing our digital agenda. It’s about creating a shift in outlook, a shift in mindset, in terms of how you’re going to do the job and the tools you’re going to use. It takes time to evolve those different behaviours effectively, but it’s the direction we’re heading in.
FL: Like Leigh, it’ll take time, but we’re seeing a lot of progress the more we move into that space. We’re seeing efficiencies being created, we’re definitely eliminating waste and, as a result, we’re lowering our costs. Introducing digital technology can help us identify where we need to do things better and can achieve efficiencies, which can have a positive knock-on impact in terms of carbon emission reductions.
CH: Post-pandemic we’ve all seen different ways of working and many of us are using digital technology to work remotely. Businesses do far more work on things like Teams and Zoom than before. That eventually feeds through to the number of people required on a building site. I’m really optimistic about digital tech’s potential… and I haven’t even touched on the benefits of digital twins!
CL: We have to be realistic and acknowledge that we are an industry in transition. There is going to be a cost element to having so much digital technology in a building.
A newly completed building with all these things might be a bit more expensive to build than one without. We need to take a leap of faith. Digitisation and data transparency are needed for productivity, sustainability and safety. But the industry’s leadership needs to play a role in driving the digital agenda. We’ve just to go through a tipping point.