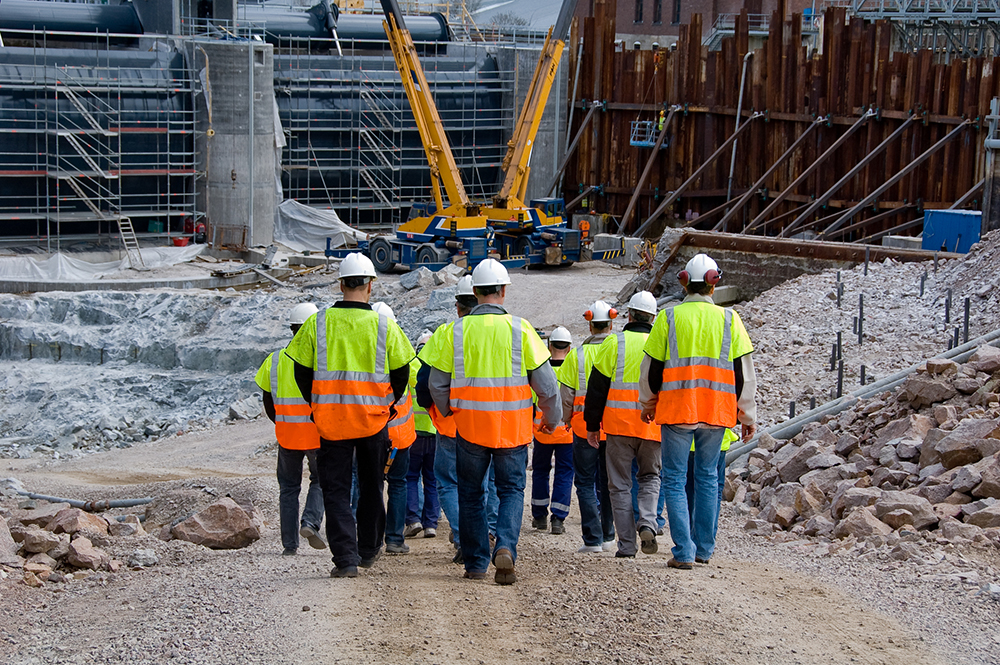
There is no doubt that construction companies are finding it difficult to recruit, needing traditional skills, like bricklaying and carpentry, as well as newer skills such as those relating to building information modelling (BIM), modern methods of construction (MMC), the incorporated use of drones and other technologies. Why is this, and how are the shortages affecting the sector? asks Karen Plumbley-Jones.
Many sectors are struggling to find and retain staff, which is not unusual in a period of almost full employment. However, in construction the problem is particularly acute as labour and skill shortages are not a new phenomenon.
Several factors contribute to this perfect storm. Older workers retire and are not replaced at the same rate by younger employees, the pandemic led many workers to reassess their personal situations and pursue different careers, and the cost of employing migrant workers has skyrocketed post-Brexit – employers face issues with visas, increased red tape and costs of up to £10,000 to employ a single EU worker.
There are also widely-held misperceptions about working in construction, for example that it involves only manual labour and lacks career opportunities. When you also consider the known lack of diversity in the sector (City & Guilds Group research found that only 9% of women would consider a construction job), it is unsurprising that employers are increasingly concerned about how they will staff projects.
Challenge in the sector
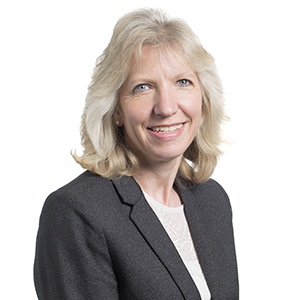
“The government and education institutions need to collaborate, encourage the take-up of T-levels and work on developing the skill sets needed for the future of construction.”
Employers are raising pay to attract recruits and with advertised construction salaries increasing by 6.7% in the first half of 2021 and skilled site labour costs increasing by 3.6% in September alone, the impact on costs makes building work more expensive. However, most construction contracts do not contain fluctuation clauses to allow the price of works to change where labour costs increase.
This leaves the contractor facing increased costs that cannot be passed on to the employer, thus hitting contractors’ profit margins. Some contractors are finding it difficult to finish projects on time because they do not have the labour available, which in turn affects their cash flow and puts their business at risk in the long term. This issue is also prevalent in other countries, such as Germany.
The solutions
We need a joined-up approach by various stakeholders. The government and education institutions need to collaborate, encourage the take-up of T-levels and work on developing the skill sets needed for the future of construction – including BIM, MMC, robotics, materials innovation, green technology, data expertise, smart cities and more.
Exciting challenges lie ahead in construction, including solving the housing shortage and achieving net zero, so a collaborative effort from both industry and education could encourage young people to consider the impact on their futures, smash the stereotypes and pursue a career in construction. Employers should be clearer about the wide range of roles available and skills to be gained. Construction companies need to invest in technology and do things differently to attract a diverse and talented workforce.
The role of employers
While increasing pay may provide a temporary fix, it is not sustainable long term. It can lead to a spiral of rising wages and employers may find themselves pulled into a bidding war for talent. In the short term, there are several strategies construction companies can adopt to navigate this challenging climate and recruit and retain employees:
- Expand recruitment campaigns to reach a wider demographic – only 13% of the current workforce is female.
- Pay a fair wage and look at other benefits to attract employees, such as access to private healthcare and permanent health insurance.
- Take steps to reduce the gender pay gap – employers with 250+ employees must publish their gender pay gap annually, however there is no requirement to take action to reduce gender wage inequality A review of the legislation is due this year. Employers could also voluntarily monitor their disability and ethnic pay gaps.
- Have a zero-tolerance approach to discrimination – take action as soon as an allegation is made with robust grievance, disciplinary and equal opportunities policies in place. Also carry out regular diversity and inclusion training and consider reverse mentoring.
- Ensure good induction/onboarding processes to welcome new employees. Line managers should meet employees regularly for one-to-ones.
- Provide plenty of training opportunities – including apprenticeships and re-skilling – and invest in personal development.
- Introduce a clear career structure so employees can apply for promotion and remain with their employer, rather than changing jobs to find a new challenge.
- Introduce flexible working – trialled in construction in 2021. At the moment, employees may make a flexible working request when they have 26 weeks’ employment, such as a change in their hours, place or times of work. Employers can reject a request for eight stated business reasons. Following a recent government consultation, it is likely that the right to request flexible working will be expanded in the near future.
Karen Plumbley-Jones is a practice development lawyer specialising in employment law at Womble Bond Dickinson.
This article was co-written by Michelle Essen, managing associate at Womble Bond Dickinson.
Comments
Comments are closed.
Rattling on about Net Zero and Diversity nonsense won’t get houses built, it’s just more “on trend” waffle.
More apprenticeships, tax breaks to train and retain, in house trade management and priority tender selection for non subcontractor based main contractors.
The issue with lack of good tradesmen and women is the lack of training, the apprenticeship scheme hasn’t been the same for many year. the introduction of the NVQ scheme failed to deliver competent tradesman/women.
Apprenticeship need to go back to its roots and train individuals properly and give them a 5 year training plan, you cannot train a bricklayer/carpenter /Plumber or electrician in 18months its not possible. The large organisation appear to prefer a scheme that pushes desktop apprenticeships rather than the core trades.
More importantly a qualify and competent trades person on site is paramount to an individuals development. (sadly not many left any more) Many of the national organisation (Not all) don’t have tradesmen and woman they favour the desktop side of apprenticeships rather then at trade level.
Organisations that build should be forced to develop good core tradesman and women If they develop/build in construction should be forced down the road of good training for core tradesmen and women. The tax system could force them down this route? equally the financial support should be there to give the employers the impetus to train properly. Richard
One of the big problems is the way workers onsite are treated. Everybody says health safety and welfare are important. From my experience and observations thats fine until an ambitious programme goes behind then its forgotten just to keep on that programme.
Classic I saw minus 3 and the steel fixers were on lifters putting bolts in frames being lifted. What will happen to the fixers hands in 10/12 years, rheumatism, will their managers/programmers worry about them, no.
Come on everybody look after you staff and their future health
What I have noticed is that construction worker are not treated good by management. They are treated as disposable, forced to work long hours, without opportunities to growth, no benefits, and no job stability because no construction site last forever. Who would want to have a job like that?
As per usual: too little, too late. To be more precise, too slow, too late.
And with the robotics industry making serious progress, manual labourers need will also decrease or become very niche.
I find myself in this article: as being a person who participated on both sides: the execution(worked) and the design part.
I like both of them in equal measure, but I had to give up the execution, since there is a sort of ”big boy’s club” atmosphere to it. What I mean is, there is this incentive, to retain talent and train new employees, but with the clear intent to keep them at that entry level that suits the contractor best.
Additionally, any attempt to demand better working or employment conditions are frown upon. This phenomenon is widely spread and hidden from outside, as a ”dirty little secret” that nobody is ready to admit to. The clearest example is seminars, where contractors are taught to ”deal” with legal issues coming from worker unions and particular cases, rather than drafting contracts that benefit both parties.
This experience comes from a 1st world country, where you would expect good working conditions.