Do construction leaders create the right environment for quality on projects? Dave Stitt isn’t so sure
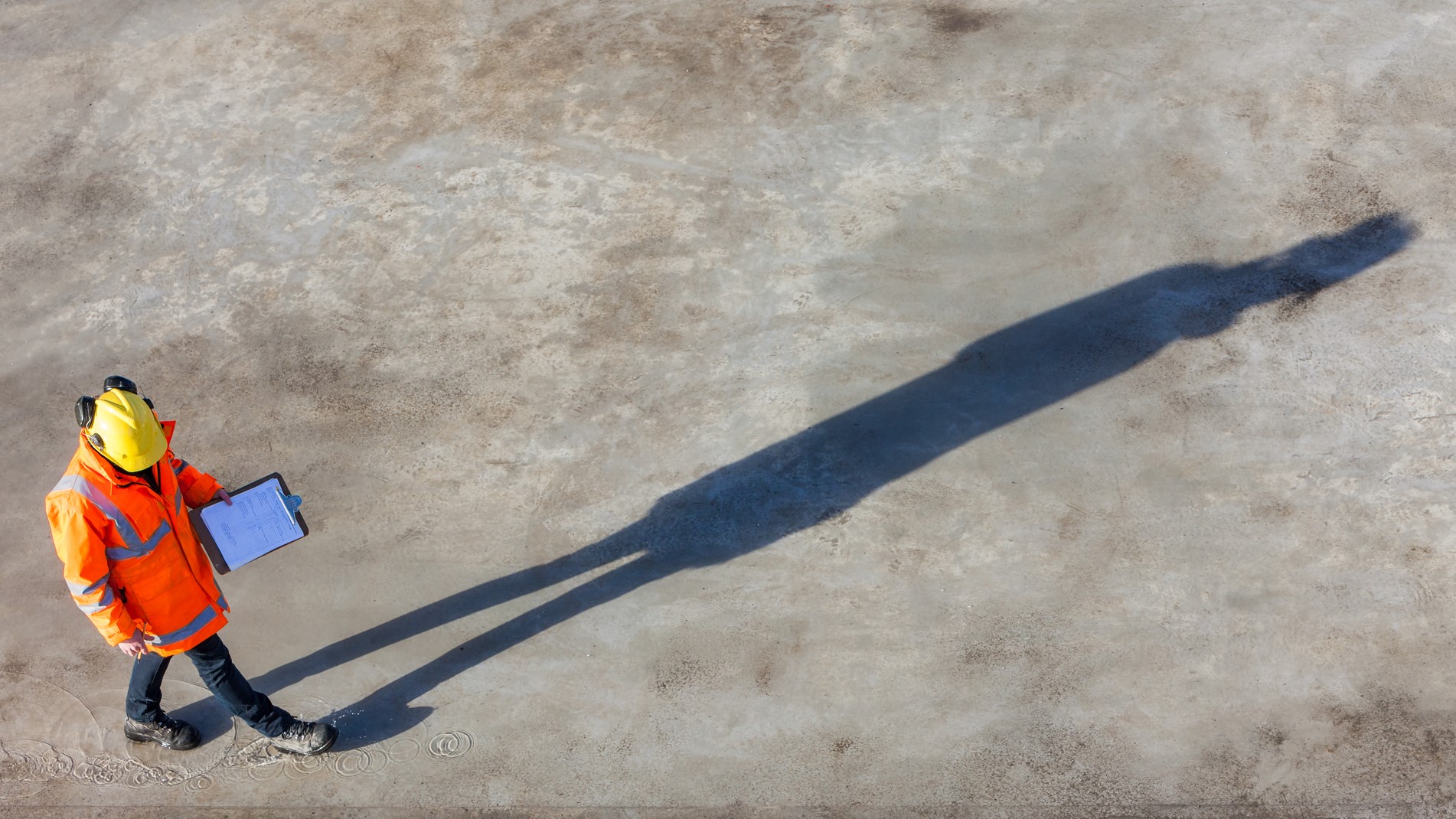
A frightening question hit me as construction disasters mounted at the end of the last decade: Edinburgh schools, the catastrophe of Grenfell and the collapse of Carillion: they each stemmed, all or in part, from issues of poor quality.
The question was: has the industry in the round become so warped by the hard task of making money from building things that it is losing the ability to build things correctly? It’s a bleak question. Thankfully, I decided the answer was no. We can still build complex things well, and we do. But the disasters have shaken us and raised complex questions.
Now I’m concerned at how responses to these disasters are taking shape. There’s a tendency to focus on systemic issues, whether they be forms of contract, approaches to procurement and finance, project management protocols, regulations and quality assurance regimes.
“Show me someone who cares and I will show you quality work. Show me quality work and behind it I will show you someone who cares.”
These are important and need sorting out, but they miss a crucial ingredient: leadership and culture at the company level.
Systems are supposed to keep everybody on track, but we know they don’t always. Systems can be gamed and rules can be followed to the letter but not the spirit. Unexpected things happen, opinions diverge, commercial priorities clash.
Attaining quality relies partly on systems, but also on the chemistry that is always at play among people. When the chemistry is wrong, it breeds mistakes, misunderstandings, defects and waste.
That chemistry is where leadership and culture come in, and while high-level debates play out over systemic issues, construction business leaders can start laying the foundations for better quality right now, within their companies, whatever the eventual outcome of these debates.
Six crucial questions
I spent 25 years at the coal face of delivering projects, and know that mistakes happen routinely: big and small, often unreported. They erode margins, damage reputations and spark disputes. People make mistakes; I know I did, especially as a young site engineer thrown in at the deep end.
With that in mind, here are six questions that construction business leaders should ask themselves:
- Do you have the right people with the right skills and experience in the right jobs to bring about a quality result?
- Are your newer, younger staff being guided effectively into maturity as professionals?
- Do your people know that quality is the top priority, along with everything else that must be top priority? Have you told them?
- Are your people empowered to spot quality issues, and the conditions that breed them, and speak up immediately?
- Are the relationships among your people strong and productive enough so that, working together, they can take action to head off quality issues when spotted?
- Are your people rewarded for taking this kind of collective initiative to ensure quality again and again?
Each of these questions is a leadership and culture issue that can be addressed within a company.
Manager or leader?
Over the years I’ve come across few construction business leaders who talk about quality. Safety, yes, but quality rarely gets a mention.
There’s a saying: “Show me someone who cares and I will show you quality work. Show me quality work and behind it I will show you someone who cares.”
Leadership is about creating an environment where people care about and can do their best quality work. If you’re not actively creating that environment – then you may be a manager in a leadership role.
Consider the tiers of construction business leadership. Engineering is about designing and sorting out technical stuff; management is tending to the organisational mechanics set up to get stuff done; leadership provides direction and creates the culture needed for success.
What best describes you? Is quality at the top of your agenda, or is that left to the QA manager?
Dave Stitt FCIOB is a leadership team coach at DSA Building Performance, specialising in construction. He is currently running the Coach for Results course at CIOB Academy.
Comments
Comments are closed.
Very refreshing approach and observations. I never thought about while safety is at least given lip service if not practiced, quality is something you only find at Marks and Spencer. Another observation I have distilled from a life time in the industry is that as long as money is the motivation, ‘care’ is not an option. “They can keep the 5% retention, I’m not coming back…”, and “…we meet the deadline no matter what is missed out – they won’t know” (shop fitting e.g.). As a tradesman I was criticised for doing everything properly and had to learn to moderate to a reasonable standard not a good one. Unfortunately this approach doesn’t work in critical systems such as fire stopping. The care you talk about can only come from workers on flat rate pay i.e. employees, or the very few genuine professionals left that pick and choose their customers – but consumers and businesses alike want ‘cheap’!
Quality should be the top agenda. The majority of Leaders I have worked alongside do care. I find one persons idea of quality differs to the next. We all have a part to play and it starts at the beginning the client and their expectations.
Architects drawings and scope is this a quality product ? What is the average number of times drawings are revised on site ? How many RFIs are send on average?
Procurement & competency
QS contractor packages ? How many meetings and time wasted on sorting out packages.
Planning How many times is the construction programme revised and reissued ?
Say your QA manager snags a plot the contractors address the snags , plot is accepted by QA Manager.
How many times have our experienced leaders , Managers revisited these plots only to find it’s not acceptable to your standards.
Switches & sockets not level , screws not aligned, loose fixtures and fittings, wall and ceilings decorations making good grinning through.
No mater what the value of the contract or who the end user is , the standards of quality and end user requirements should be the main priority when undertaking a project we all have a part to play on insisting this.
Having been in the industry for over 40 years as a trades man and now in Management i have seen the results of being pressurised in to condensing programmes and cutting cost and how they affect the quality of the end product. The most successful projects i have been involved in have had realistic budgets and programme durations for design and construction but most importantly a Client that is willing to work collaboratively with the Contractor. There’s a lot more to delivering a quality project than just having the right level of experience within the team. How many projects have we been on where we start construction before the design is developed to a sufficient level to keep pace with the construction programme. We then get pressurised to build out of sequence (lets think outside the box and come up with a work around) sorry doesn’t work. It leads to reworks, increased costs, morale on site takes a dip and so does quality. Yes having the the right level of experience within a team is important but the issues with quality within the construction industry are more deeply rooted than just having the right team in place.