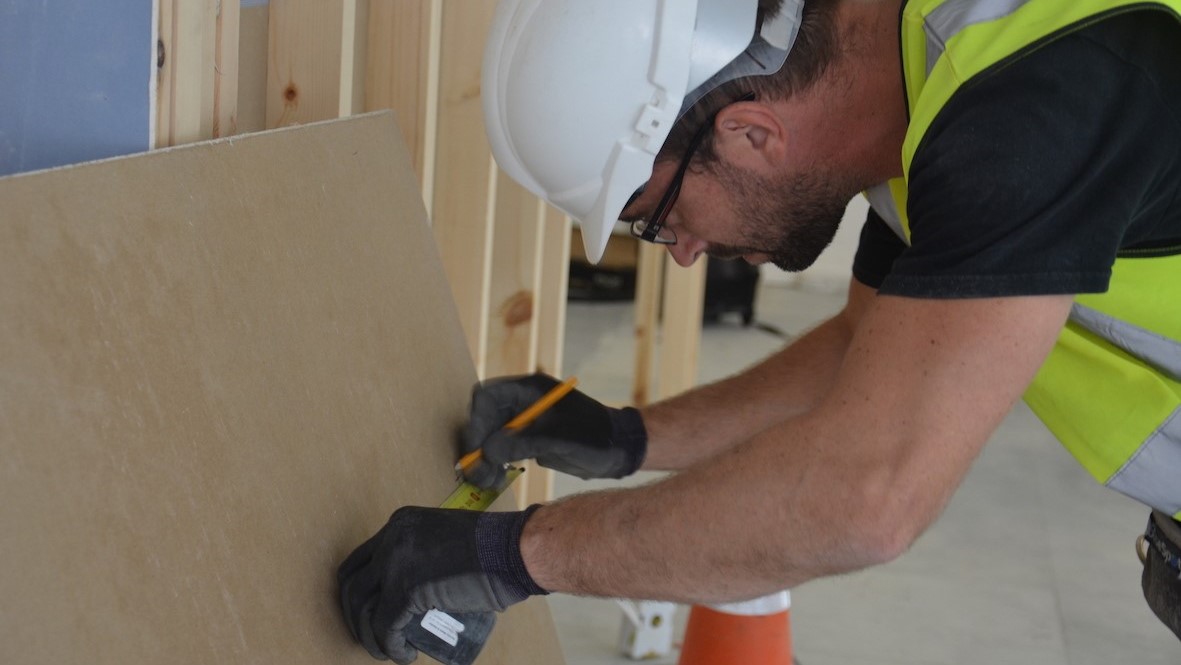
Researchers at the University of Bath are investigating how bacteria could be used to create a new type of environmentally friendly plasterboard.
Microbiologists from the university and concrete experts from its Department of Architecture and Civil Engineering have been awarded funding by the National Biofilms Innovation Centre (NBIC), for a six-month pilot project that aims to optimise the properties of the prototype plasterboard using their bacteria-based construction technology (BBCT).
They are working with start-up Adaptavate, which makes biodegradable plasterboard, Breathaboard. Breathaboard uses compostable crop waste instead of gypsum, is lighter and has better thermal and acoustic insulation compared with traditional plasterboard.
If successful, the plasterboard can be scaled up and developed further.
Dr Susanne Gebhard, senior lecturer in Bath University’s Department of Biology and Biochemistry and the Milner Centre for Evolution, is leading the project in collaboration with professor Kevin Paine from the architecture and civil engineering department.
Gebhard said: “Biofilms are formed when bacteria stick together to coat a surface, as opposed to growing neat dot-shaped clumps on a petri dish.
“This is a really exciting project that will see whether we can exploit the natural biofilm-forming abilities of bacteria to function as a kind of glue that will help improve the properties of biodegradable construction materials.”
Jeff Ive, technical director at Adaptavate, said: “Gypsum is the third most used construction material and accounts for 3% of UK carbon emissions.
“It’s either mined or produced from waste from coal power stations and is becoming increasingly expensive to produce. As it’s calcium sulphate based, it also needs to be disposed of carefully so it doesn’t harm the environment.
“Our Breathaboard is a low-carbon sustainable alternative to gypsum-based plasterboard and could make a real difference to the carbon emissions of the construction industry.
“We’re delighted to be working with the University of Bath to further develop this product.”