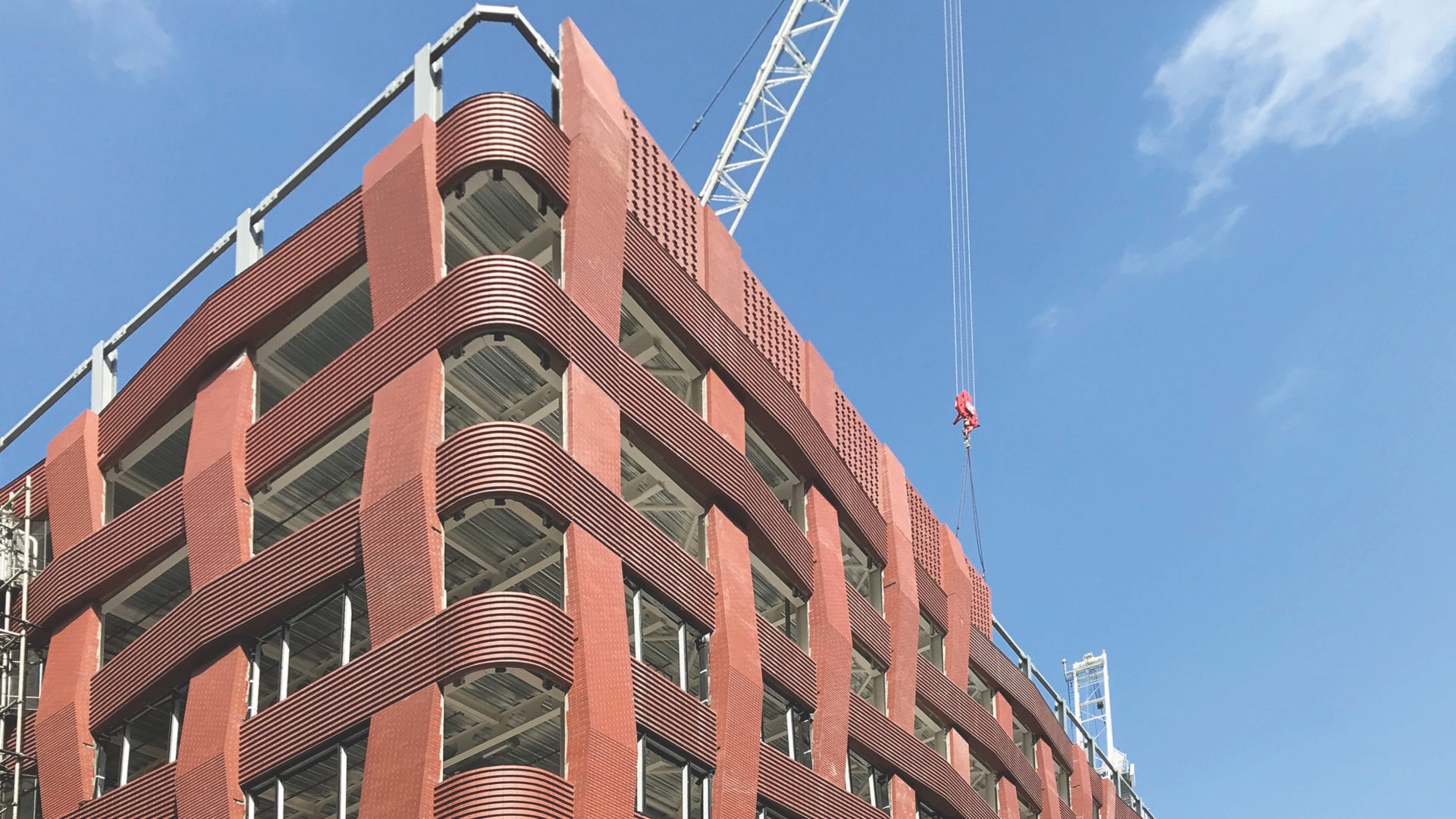
Covid-19 restrictions did not stop precast concrete specialists from keeping projects on programme – and the sector is now looking ahead with optimism. CM reports
When covid-19 hit the UK last March, the precast concrete industry was better prepared than most. Controlled factory conditions and efficient site processes meant the sector could adapt quite easily to lockdown restrictions.
Thorp Precast has operated at 100% capacity at its 8ha site in north Staffordshire. While many construction sites, particularly in urban locations, can be congested workplaces, the opposite is the case for precast manufacturing plants.
“Physical distancing is relatively easy to achieve in the factory, with plenty of spacing between each active working mould over several casting sheds,” explains Steve Morgan, technical sales manager.
When the pandemic struck, Thorp senior management consulted with all operatives on the coronavirus dangers and new guidelines for safe working. “All our staff opted to continue working in line with the new measures, which has resulted in no lost productivity and no cases of covid-19,” explains Morgan.
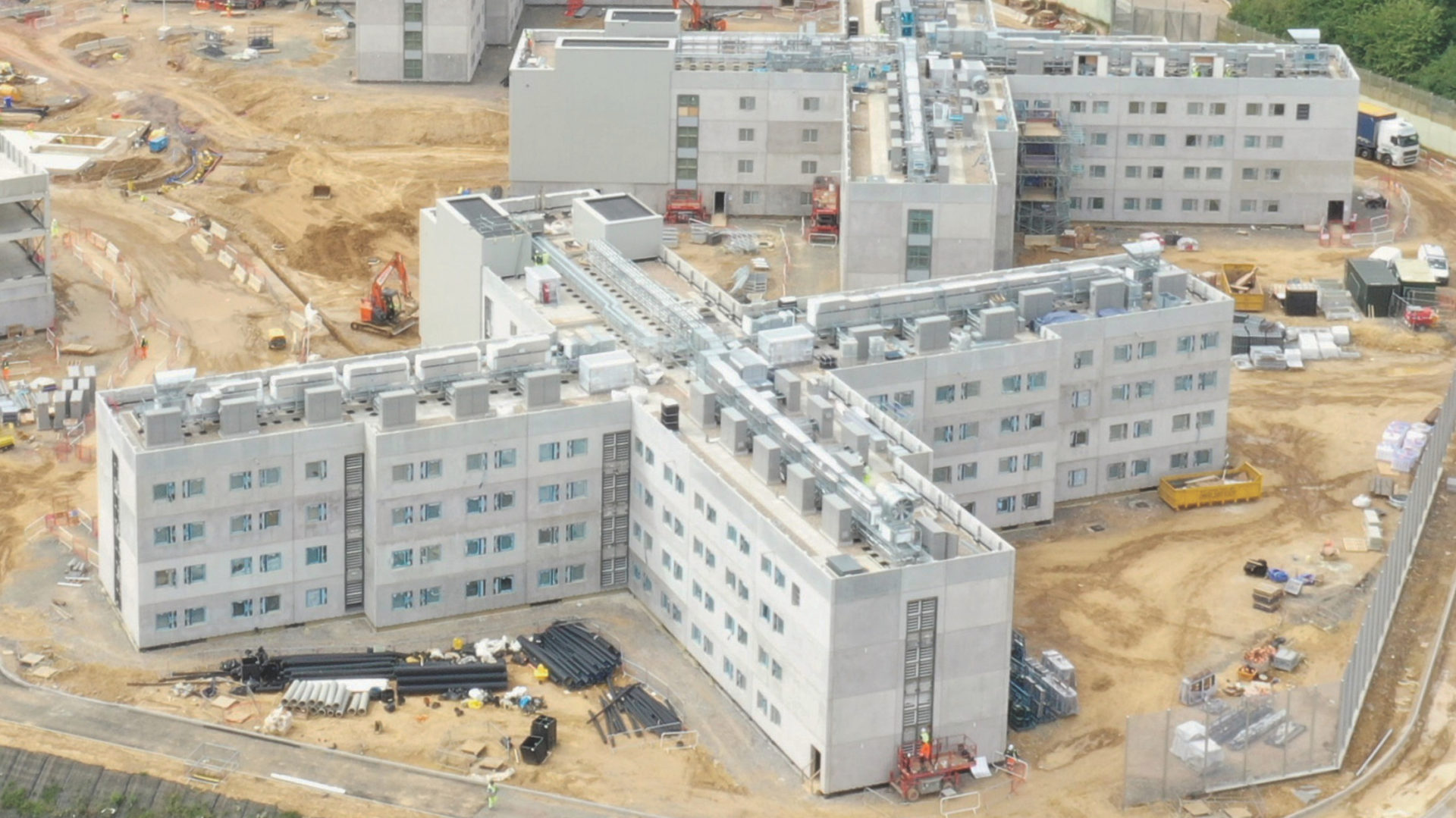
There have been a few changes to operating procedures.
“We have one person working per mould, reduced working hours and fewer people working in concrete pouring teams,” explains Morgan.
“We also have bubbles for workers when travelling to and from work in the same vehicle. They clock in at the factory gate and not on a machine, and strict one-way systems have been introduced. We also restrict access to the plant much more, with everything carefully recorded and booked in.”
Away from the factory, Thorp workers have to follow social distancing requirements on delivery to site and installation of the precast units.
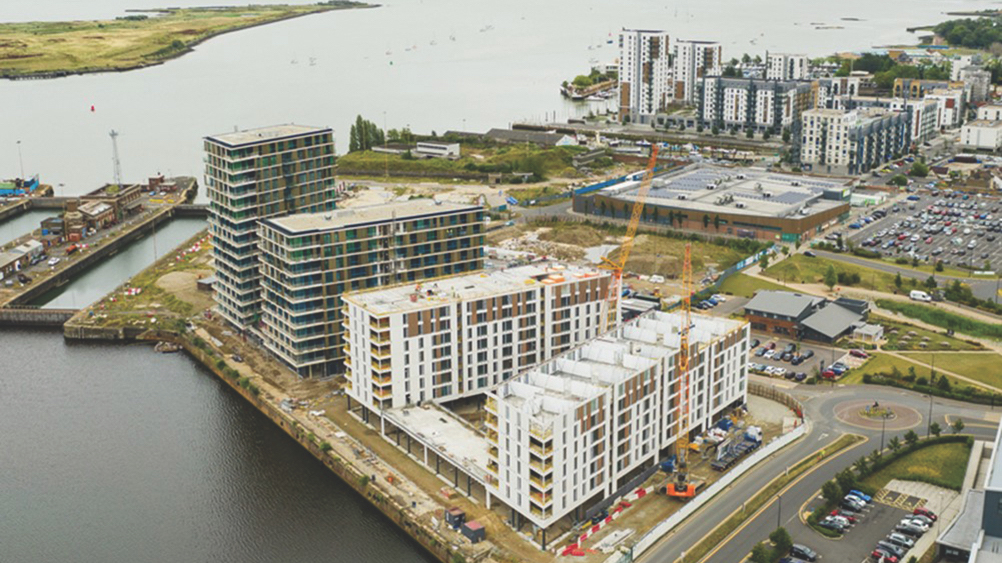
“They are small teams, but they all use relevant PPE, particularly if working face to face, and install panels with operatives on either side of a precast panel, ensuring that social distancing is maintained,” says Morgan.
“A huge benefit of only needing four to five men on site at any one time to maintain maximum productivity is that we can install a conservative average of five to six panels per day on our projects, regardless of the wider restrictions of covid-19,” he adds.
This meant programmes have been maintained across Thorp’s projects, such as the new HM Revenue & Customs office at 3 New Bailey in Salford, where Thorp is working with main contractor Bowmer + Kirkland, delivering brick-faced precast panels in a ‘basket and twill weave’ design.
Another precast specialist, Sterling Services, won its record contract – for the City of London Academy in Hackney and the adjacent Britannia Leisure Centre – just before covid-19 struck. Morgan Sindall is main contractor and Sterling is designing, manufacturing and installing Portland and brick-faced panels.
“Naturally we were anxious when the pandemic hit; would we be able to continue manufacturing?” recalls Sterling managing director Chris Bell. “Would we suffer from staff shortages? Would sites remain open and would we be able to access materials?
“However, due to our large open spaces and the nature of our processes it was feasible to continue production at the same rate whilst maintaining social distancing and ‘covid-safe’ health and safety measures.”
One crucial manufacturing issue for Sterling to consider was availability of materials.
“To ensure that we had the capacity to continue manufacturing, we purchased many materials in big bulk loads to insure against any future closures of supplier businesses,” says Bell. “This was a foresight we came to be glad of when merchants, timber mills and sanitary suppliers started to close or run out of stock.”
Work on the City of London Academy to install the facade panels, comprising large double-window, storey-height units with integral bricks, copings and cills, commenced on programme last May. One of the key stones at the front of the building contains the City of London emblem which was cast into the precast unit from a rubber mould. This unit was installed in early June. Sterling’s work on the Hackney scheme is continuing into 2021.
Creagh Concrete has also stayed busy since covid-19 arrived and managing director Noel Culbert believes this could be a watershed moment for the precast sector.
“Times of crisis can be both threatening and liberating and we see this as an opportunity,” he says. “The twin challenges of climate change and the pandemic are an opportunity to transform our thinking.”
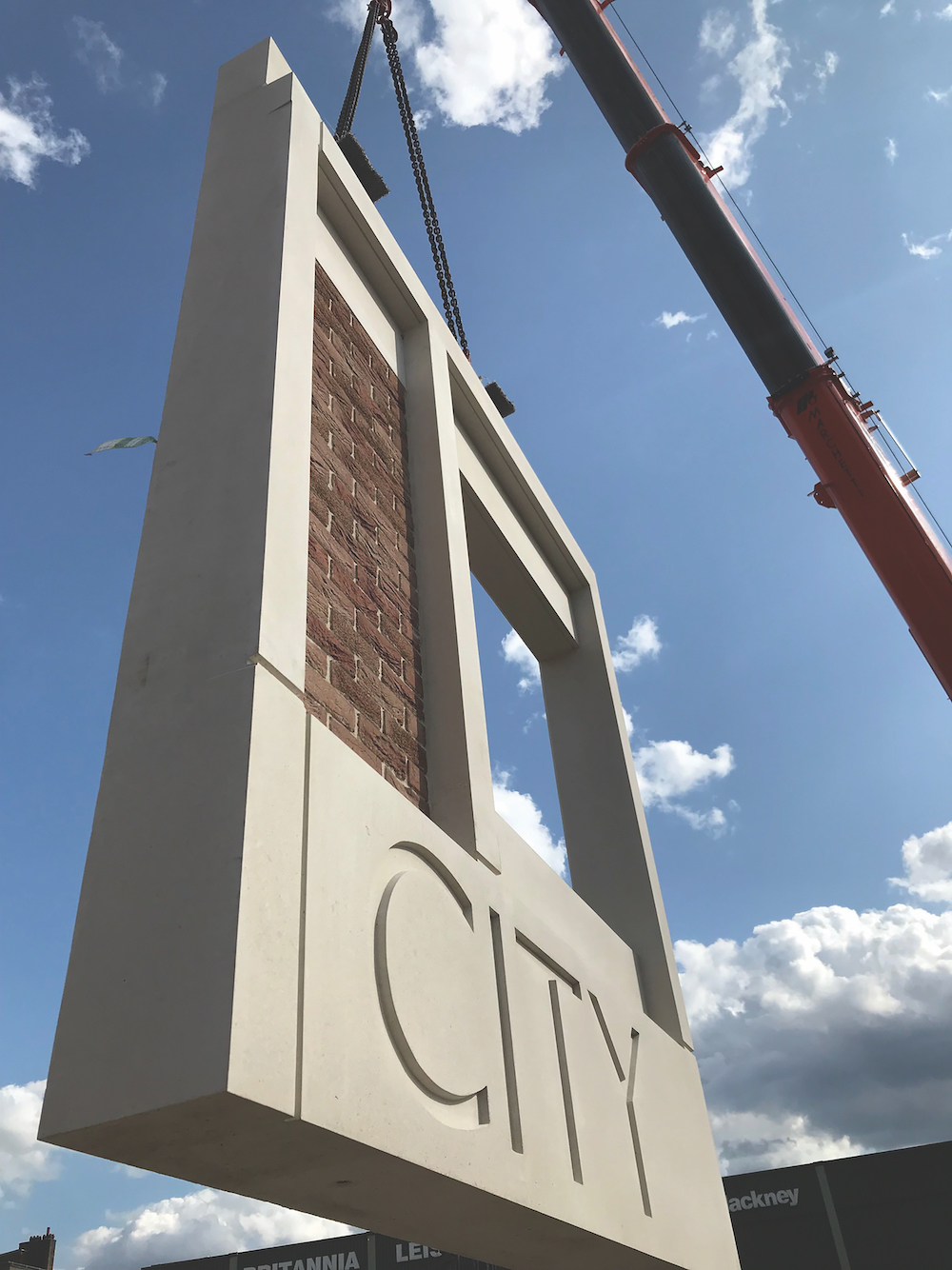
One of Sterling’s facade panels bearing the City of London Academy logo is craned into place
He sees it as “inevitable” that offsite manufacturing will be adopted more extensively, and forecasts growth in Creagh’s Rapidres system, the company’s fast-track crosswall build system commonly used in apartments, student accommodation, hotels and social housing.
The benefits of Rapidres were demonstrated during the first lockdown when Creagh was able to deliver programme savings across many projects, says Culbert.
“A safe working environment was enhanced, with less people on site meaning social distancing was achievable,” he says.
These projects included the Chatham Waters development for Russell WBHO, a two-block, seven-storey residential development in Kent of 193 apartments. The frame comprises structural walls and solid hollowcore flooring, with a facade of white etched precast concrete with bronze panels and balconies.
Creagh’s ambition is to build 20,000 apartments in the next decade, says Culbert, with further investment in its manufacturing capacity.
Comments
Comments are closed.
Off Site Manufacturing (OSM) modular construction is definitely the way forward but, there are insufficient materials integration. Panels are clean and robust but the resultant visualisations at present from an architectural perspective steel remains with remnants of a concrete jungle. Merely a different approach to the high rises of the 60s and 70s. But material integration will change that. From a modular aspect quality safety labor to list but a few does work extremely well.