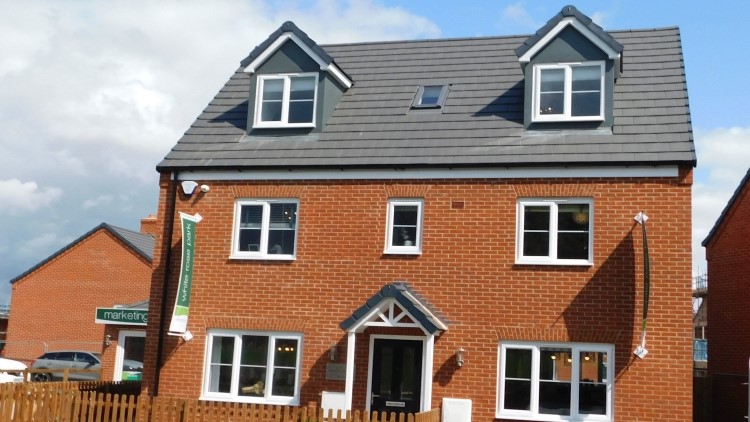
Housebuilder Persimmon plans to double its team of quality inspectors to 60 by the end of this year, as it announced a renewed focus on build quality.
Presenting the company’s financial results for 2020, chief executive Dean Finch, who took up the role five months ago, said: “I want the Persimmon Way to become less our own quality assurance process and more a guarantee for customers. Our ambition is to build right, first time, every time, by setting new industry standards for construction, independent inspections, and employee training.”
Among other measures Persimmon announced was to adopt “more exacting building tolerances than existing industry standards”.
The team of 60 independent quality controllers will report to the group construction director and will assess every plot Persimmon builds at key stages and will only allow work to continue if standards have been met.
Meanwhile the ‘Persimmon Pathway’ will provide a tailored training programme to every direct employee, starting with site-based workers.
Finch said: “With a significantly expanded team under our group construction director and a new group technical director, we are strengthening our central oversight to ensure the consistent application of these standards. This is clearly crucial, but to strengthen our customers’ trust, we need to go further.”
For the year to 31 December 2020, Persimmon’s revenue fell slightly to £3.3bn, down from £3.7bn the year before. It made a pre-tax profit of £783.8m, down from £1bn in 2019. New home completions in 2020 numbered 13,575, down from 15,855 in 2019.
Finch said: “Persimmon delivered a robust performance in 2020 despite the challenges presented by the pandemic. I would like to commend our workforce for the effective way covid-secure operating protocols have been adopted, protecting our customers, local communities and colleagues alike whilst maintaining effective on-site operations.”
Comments
Comments are closed.
It isn’t only a case of increasing inspectors, it is educating site management to control quality in the first place – this is basic site management procedures surely?
Maybe they would be better employing trades who actually know what their doing.
Quality is achieved by giving site teams enough time to build correctly. Still too much emphasis on numbers at Persimmon and little or no interest in delivering a quality product from senior management.
The biggest challenge for Persimmon is changing the poor culture within the company towards customers who are considered a nuisance if they dare to complain.
The perfect QA process is an illusionary, ethereal dream with many subbies either too lazy or too time poor and all unaware of what needs to be benchmarked and recorded because they are guided by main contractors even more ignorant than the people they supposedly control and monitor.
The entire industry should hang its head in shame at its deficiencies….