Clarion Housing’s post-Grenfell strategy has been commended by Dame Judith Hackitt. Will Mann talks to the group’s building safety team about cladding remediation, quality management and the power of data.
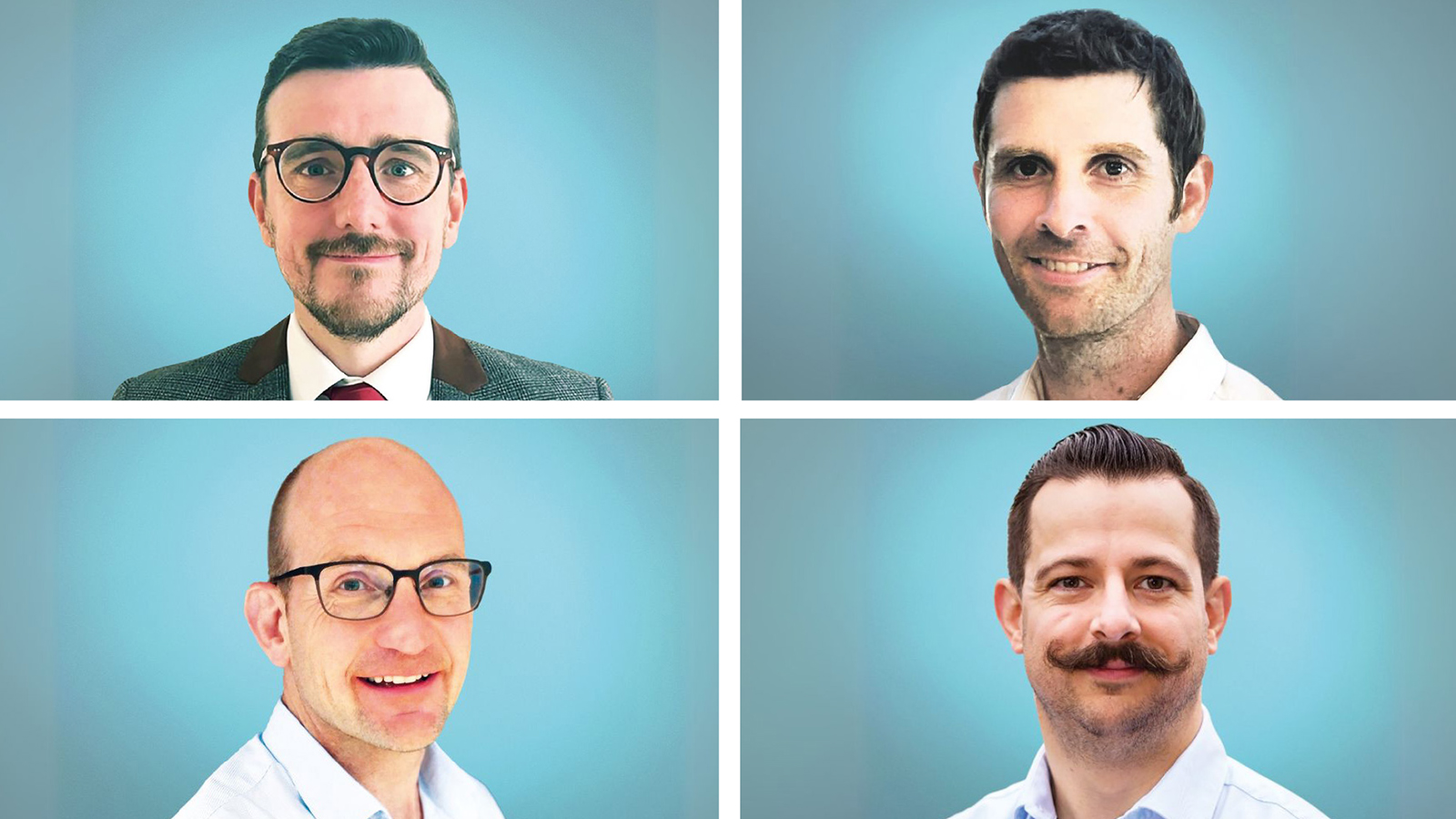
Clarion, the UK’s biggest housing association, is setting a new bar for building safety.
Singled out for praise by Dame Judith Hackitt at last November’s CIOB James Wates lecture, the group began overhauling its building safety approach shortly after the 2017 Grenfell fire. It now has a sophisticated digital-led strategy for managing its housing stock, interrogating the condition of its assets and carrying out remediation work. Any contractors working on Clarion’s 125,000 homes must meet exacting quality standards.
Leading this programme are building safety director Dan Hollas FCIOB, head of building safety Matthew Lewis MCIOB, lead inspections manager Tom Lawlor MCIOB and technical manager Jack White.
The model developed by the team for assessing and prioritising remediation work has been key to the building safety strategy, says Lewis.
“This has evolved over time as we learned more about our buildings,” he explains. “As we explored more buildings, we fed our learning back into the model, which helped make it more accurate. This approach has allowed us to stay ahead of government recommendations and make better decisions about our stock. It’s been successful in delivering a remediation programme that’s both proportionate and effective.”
The Clarion building safety journey started with aluminium composite material (ACM) cladding investigations in 2017, followed by all other cladding types in 2018. After the Fire Safety Act was passed in 2021, Clarion began intrusive investigation of all higher-risk buildings (HRBs). PAS 9980 was published in 2022 and provided a methodology for fire risk appraisal and remediation.
Understanding the risk
“Early on, we realised we didn’t have easily accessible data to understand the materials used in our buildings and assess the risks they posed,” says Lawlor. “Our first task was to determine what materials were on our buildings and which posed a risk.”
The housing group made an early decision to embrace digital technology, using a laser scanner and creating 3D models. Some 10,000 surveys were carried out. (see below).
“With this data, we created a prioritisation model to assess each building based on its calculated risk, creating five distinct risk priorities, from one to five,” says Lawlor.
The next step was to analyse this data to understand risk drivers. The surveys had produced 19,000 instances of 28 different wall types.
“Some materials, like high-pressure laminate, appeared in only a small number of buildings, while others, such as rendered solid wall and brick slips, were far more prevalent,” explains Lawlor.
“Of our 10,000 buildings, almost 9,000 used half-brick or brick slips as the predominant material. The risk posed by certain materials was more concentrated in a smaller number of buildings but, given the sheer volume of our stock, these
still represented hundreds of buildings that would need investigating further.”
The data from these surveys allowed Clarion to build an appraisal process based on its prioritisation model. Data from each appraisal was fed back into the model, refining the focus on to the buildings with the greatest concerns.
Building height was established as the primary risk driver for external walls.
“Only 10% of smaller buildings below 11 metres needed work,” says Lawlor. “However, the volume of smaller buildings still meant we had many buildings with issues that were in these lower-height categories.
“Structure was another key risk factor. Our analysis showed that the structure of a building was a critical indicator of whether it would fail the PAS 9980 review. Concrete masonry and steel frame structures each made up a quarter of our stock, while timber frame structures, the highest-risk category, were a major concern.
“The future of construction has to be sustainable but everything we have seen about timber frame to date tells us there is a need for more of these construction skills in this country to properly build them.”
Build quality
The Clarion team also discovered that age of construction was an important risk indicator, with buildings constructed in the last 18 years far more likely to fail due to poor construction quality.
“Traditionally constructed masonry buildings from the 1960s to the 1980s had a much lower risk of external wall issues, assuming no problematic materials like plastic spandrel panels were added,” says Lawlor.
“Modern construction methods, however, were where we saw more problems. Of the buildings needing remediation, 39 were built before 2000, and 177 after 2000, which is not surprising for those of us in the industry who have been aware of these issues for some time.”
Clarion has now completed about 1,500 appraisals, with 216 buildings either needing remediation or some form of mitigation.
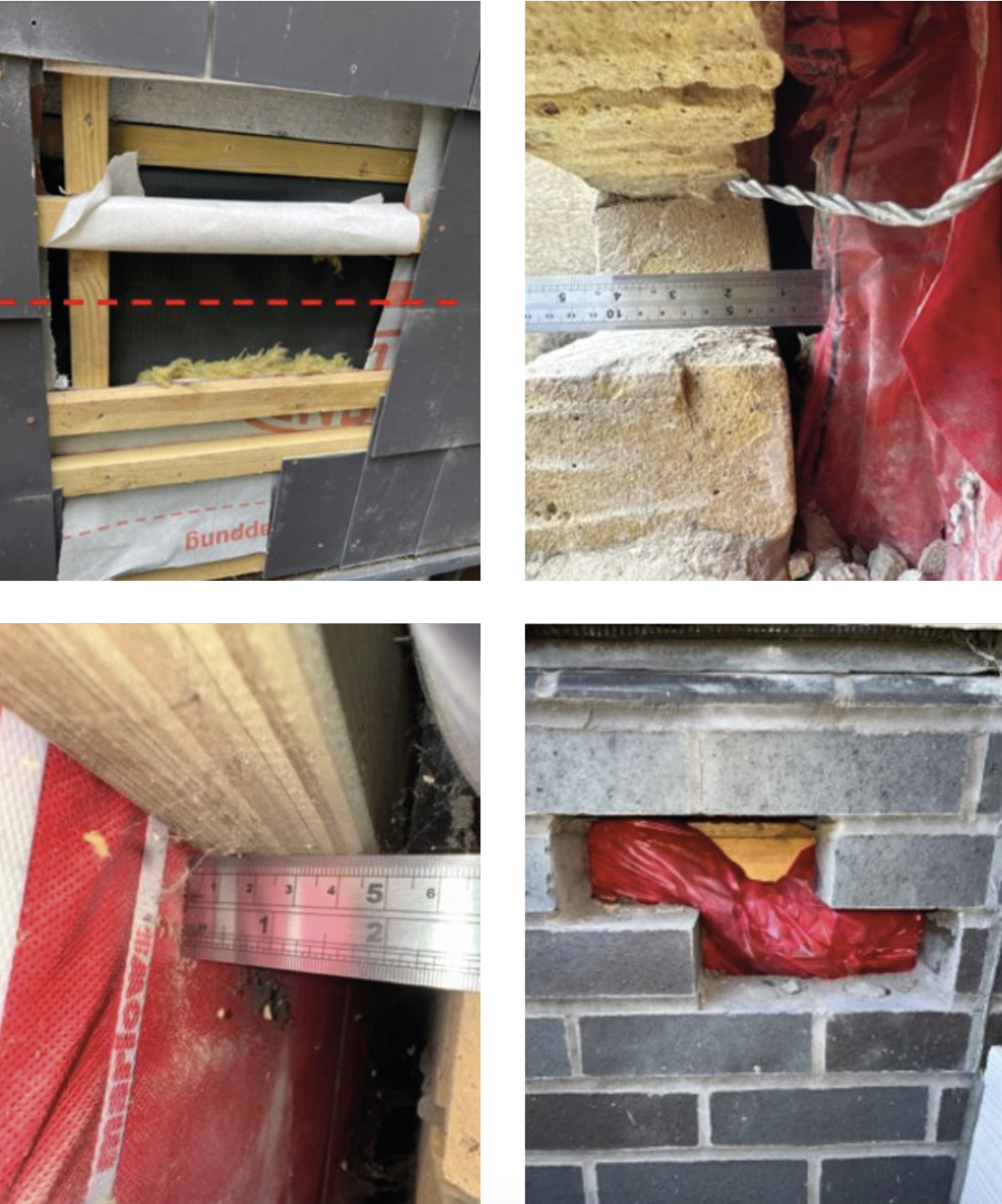
“When we started, the failure rate for appraised buildings was almost 100%, because we were focusing on buildings we suspected had issues,” says Lawlor. “However, as we progressed through our model, the failure rate dropped to around 20%, with 80% passing, which reflects our improved targeting of the most problematic buildings.
“With external wall issues, materials are now relatively easy to identify and remove. The bigger issue has been hidden construction problems, like poor workmanship. We’ve found issues with the construction quality of buildings, such as missing cavity barriers or gaps that allow fire to spread through facades.
“There are also complications with timber batts that are insufficiently sized to fill cavities, and cavity barriers that are misused or incorrectly installed. These issues are far more difficult to address than simply removing problematic materials.”
Lawlor believes that industry perceptions of cladding risk may be misplaced. “We often think of the cladding crisis in terms of buildings with complex facades, such as those with spandrel panels,” he says. “But we’re finding issues even in buildings with solid brick facades. These buildings may have hidden risks, such as combustible insulation, missing cavity barriers and timber frame structures that need proper protection.”
Lawlor adds that developer claims have played a “significant role” in the remediation process.
“We’ve been negotiating with original builders to compel them to address these issues as the government has mandated,” he says. “Developer claims can take a long time to resolve.
“PAS 9980 is not meant to be a legal tool, yet it’s increasingly becoming the default for resolving disputes with developers.
“It is a challenge achieving consensus among all stakeholders, including original builders, building control, fire engineers and residents,” Lawlor continues. “There are shifting perceptions of what constitutes an acceptable level of risk. What fire engineers deem acceptable today might not be acceptable tomorrow.
“We’ve seen examples where different engineers come to different conclusions on the same building. One engineer might sign off a building, while another might not, creating an asymmetry of outcomes that poses a risk to the industry.”
Lawlor also flags the issue of futureproofing. “As regulations for buildings above 11 metres become more stringent, we might be signing off on older buildings but creating a growing disparity between existing and new buildings in what’s considered acceptable,” he points out.
“Another concern is that if we allow developers to sign off these older buildings, this could incentivise future shortcuts, knowing that the system may accept these buildings without addressing all their risks.”
Clarion has to date remediated more than 100 of its buildings under PAS9980, half of those requiring remediation.
“The data that we’ve collected has meant that we’ve been able prioritise some buildings and get them remediated in a much quicker way,” says Hollas.
Given the history of poor construction that its surveys have uncovered, Clarion now has a rigorous quality management process for its contractors.
“We’ve put into place systems during the remediation work to make sure we’re able to monitor the build quality,” says Lewis.
CIOB’s Client Strategy
CIOB’s Client Strategy aims to support construction clients by curating and sharing
best-practice digital resources which will help them achieve improved project outcomes. Further information: www.ciob.org/industry/support-for-clients/professional.
“On all our remediation projects, we’ve implemented a system called Multivista (Construction Documentation Photography Services), and we go out and photograph the site at regular intervals. If any issues are identified, we can check that they’re not replicated across the site.
“That also means that in future we can use the photography documentation to peel back the layers of the building as the remediation took place and see what the contractor has done. That’s been incredibly useful, not just in terms of monitoring quality, but also defending the works that we’ve done from a legal perspective and demonstrating to building control.”
Clarion’s data management strategy
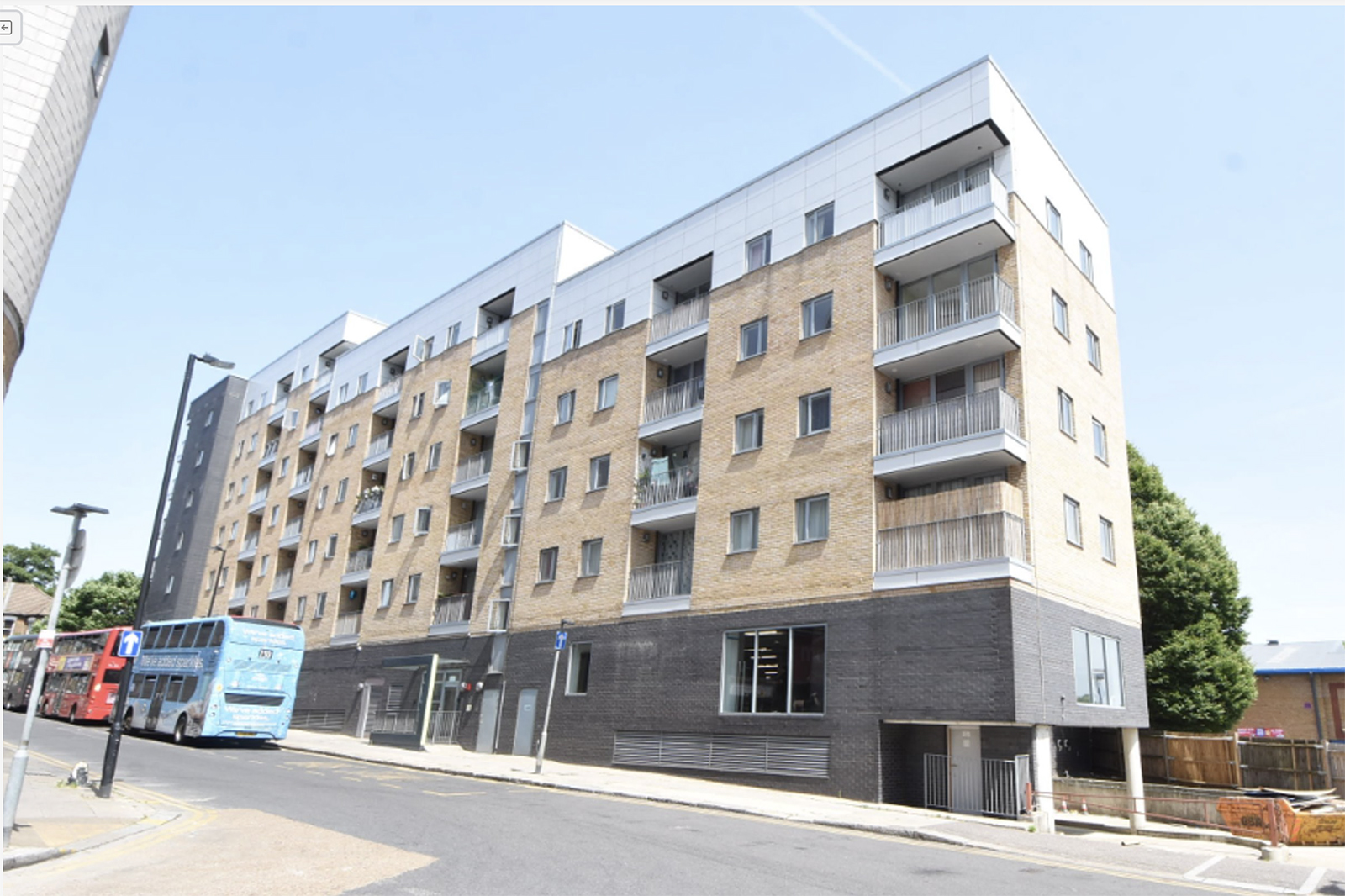
Clarion’s approach to data collation and management follows the ‘quality in, quality out’ mantra.
“When people are going out on site, we’ve got a system that will capture the information in a template format, so that we were getting consistency in the information,” says technical manager Jack White.
“For example, an external wall will be broken down by material, insulation material, type of frame etc. If there are changes, we’ll be able to react to that quickly by clicking a button and making the changes to information about that external wall. Hopefully, we’re setting the foundations with our system that we have now, so that in the future we can be really agile, flexible and quick to respond.”
Matthew Lewis, head of building safety, adds: “We’ve set up our technology so we can look at a whole external wall as a system. It’s not just the components that make up the outer skin and the inner skin, but all the elements that interact with that.
“We can also identify all buildings that have a particular product. If, say, we wanted to look at thermal wood cladding, we could pull up all the buildings where we’ve identified that being present.”
This feeds into Clarion’s golden thread strategy, White says, where the group is working with Bentley.
“There was no software solution out there that worked across a portfolio and for housing,” he explains. “We spoke to several vendors and found Bentley, who had a lot of different tools, and were keen to work with us. It’s been a really good relationship.
“We still go out and laser scan buildings and one of our team creates our smart models using those scans. The models are a lot more advanced now, compared to when we started shortly after Grenfell.”
“But we’re not putting in resident information, we’re trying to keep the two separate, in case we need to give third parties access,” he adds.
“We’re calling our technology Clarion Built Environment (CBE),” says building safety director Dan Hollas. “But this is not a commercial project. We’re keen that other organisations can learn from our experience.”