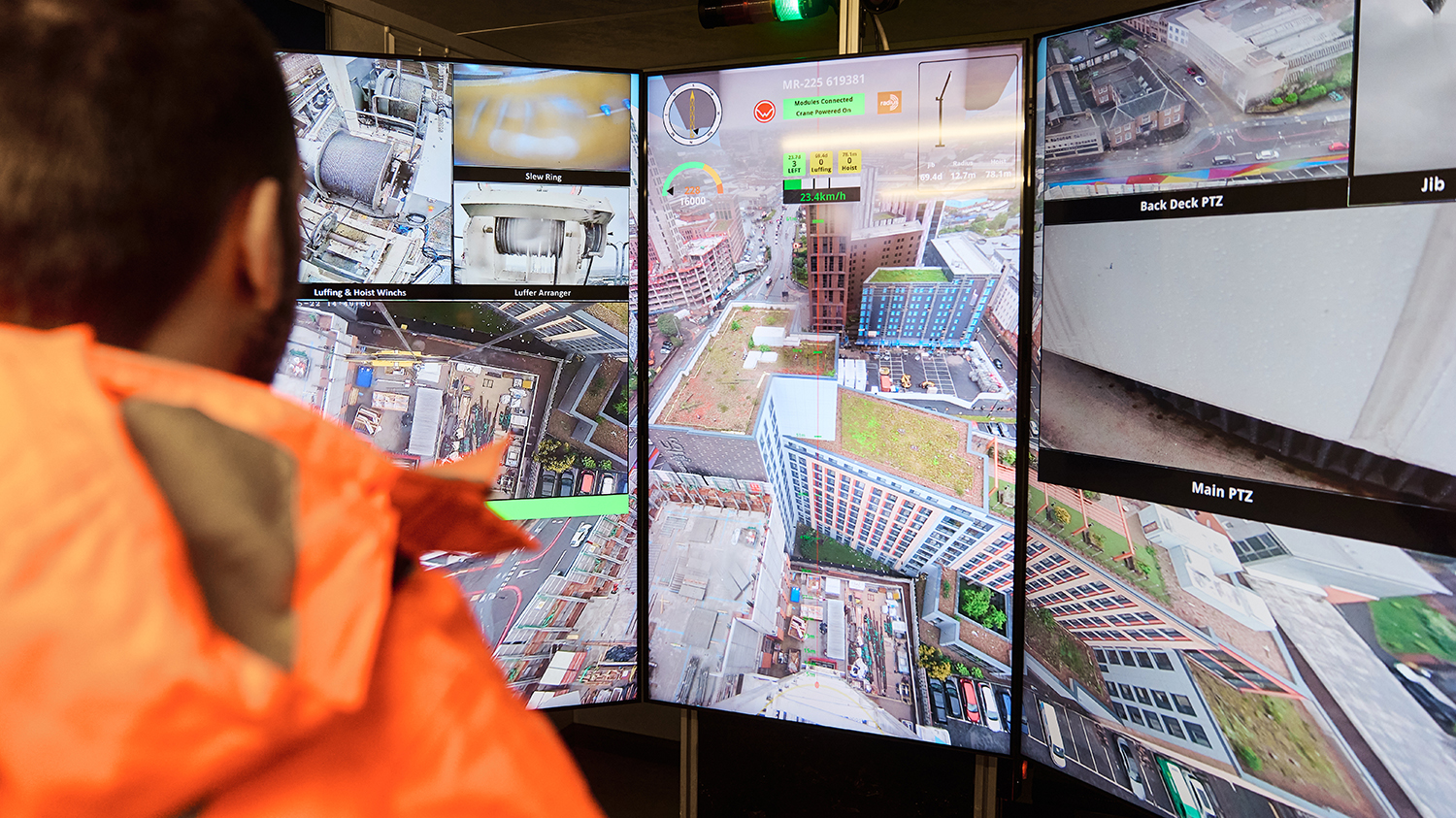
Kristina Smith visits Winvic’s Crown Place Birmingham development, where next-generation innovations can be seen in action, including a remote-controlled tower crane.
Winvic’s Crown Place Birmingham project, a 33-storey student accommodation development, hit the headlines in September 2024 with news that it was using the UK’s first-ever remote-controlled tower crane.
And this isn’t the only innovation on the job. Alongside the remote-controlled crane (see below), project manager David Elson and his team are using a raft of digital tools and technology that start to show what the next generation of construction sites could look like.
Project: Crown Place Birmingham
Contractor: Winvic
Cost: £80m+
Form of contract: JCT Design and Build with amendments
Client: Crown Student Living
Architect: ECE Westworks
Engineer: Meinhardt
Programme: 153 weeks
Completion: November 2025 (targeted)
Subcontractors
Concrete frame and groundworks: Midwest
Facade: Hansen
MEP: Highadmit
Pods: Offsite Solutions
Piling: Volker
FF&E: Deanestor
Roofing: Advanced Roofing
Crown Place Birmingham will be Winvic’s highest-ever build. Comprising a 33-storey tower, stepping down to two lower sections of 12 and nine storeys, this is the contractor’s second project for client Crown Student Living, following on from a similar, but smaller, development in Nottingham.
Less than 20 minutes’ walk from Birmingham New Street and close to Aston University, the 814-bed development will provide more facilities than most student accommodation, such as a yoga room, retro games room and an external terrace at first-floor level. Some students will be able to live in ‘duplex clusters’, effectively two-storey houses with their own staircases, within the building.
No closed roads
This is a very tight site, says Elson: “We’ve got one metre on one side, one metre on the other and theoretically 35mm on the other two sides. We are on a red route into Birmingham, so we are not allowed to close the roads, but we did get a bus lane closure to create a drive-through bay to offload the vehicles, one artic at a time.”
Work started on site in February 2023 with groundworks, ground remediation and the installation of continuous flight auger (CFA) piles. In September 2023, contractor Midwest began work on the reinforced concrete frame, which combines precast vertical elements and cast-in-situ horizontal ones.
This is the second project where Winvic has deployed a hybrid concrete solution, Nottingham having been the first. At Nottingham, Winvic used two-storey-high precast columns; at Birmingham the columns are just one storey tall.
“Because we are going higher here, we had to think about the wind effects, and also this is a far more compact site, so laying two-storey columns down off the lorry would have been difficult,” says Elson.
Faster construction
Using precast vertical members requires less hook time from the tower crane, since there’s no reinforcement to be lifted and no shutters to be erected and struck. The quality is better, says Elson, because it is factory fabricated, and the speed of construction is faster. Compared to an all in-situ frame, it is cost neutral, but programme certainty is greater, he adds.
“We can stand all the precast columns on a floorplate in a day,” he says. “We are turning a floor slab every eight days. And, whilst our core construction is slightly slower than slipping or jumping it, the quality of the finish is demonstrably better – which means we won’t be trying to finish the core while people are moving up and down the staircase.”
To provide edge protection as the floors follow on from the columns, four-floor-deep climbing screens from Hünnebeck wrap around the perimeter of the tower. The screens can be hydraulically lifted or lifted using the tower crane.
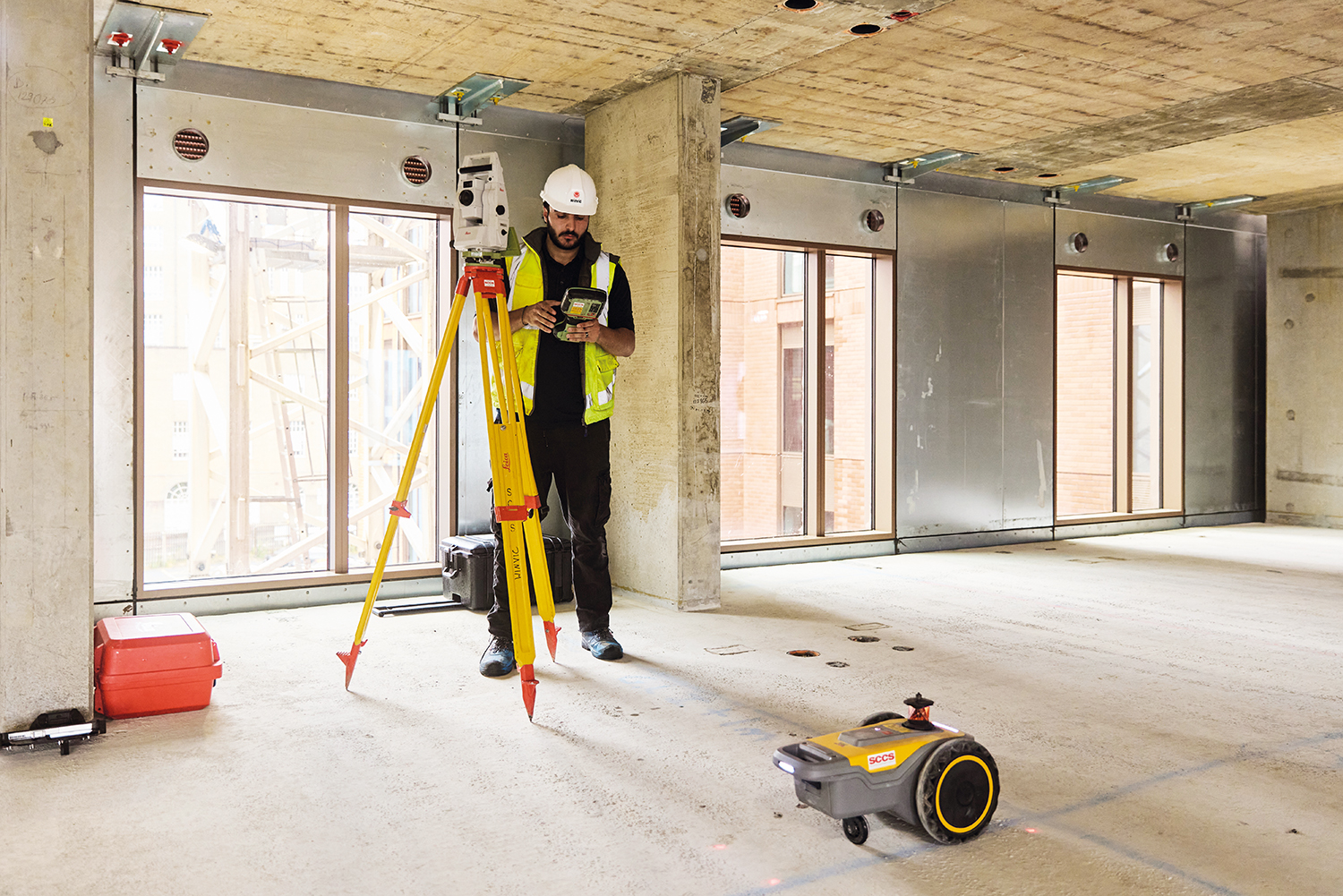
To cast the floor slabs, Midwest is using a Doka table lifting system (TLS), which allows the formwork to be lifted and positioned without using the tower crane. Again, this frees up hook time and means that the operations are not impacted if wind speeds are too high.
Facade design
Winvic changed the design of the facade due to the limited space on site, with no room for scaffolding or mast climbers. Instead of a steel framing system (SFS) with brick slips, Winvic switched to a brick facade unitised curtain walling system from Danish company Hansen, which it believes is a first for the UK.
Each panel is one storey or 3m high, with varying widths, from two bricks wide to a full window’s width of 1,600mm. The structure is a curtain walling system clad with glass or bricks from Forterra, which have been mechanically fixed into a Forterra carrying frame. The panels are hung onto brackets cast into the slabs, with four lines of gaskets between them to provide air and water tightness.
“The quality of the unitised facade is phenomenal,” says Elson. “It is so sharp and crisp. I challenge you to find a vertical brick joint.”
Rather than plumb between floors, as is often the practice for multi-storey construction, Winvic is using coordinates to set out every floor slab, to avoid any errors being compounded. “We’re just about to cast level 22 and the most out we have been out is 4mm,” says Elson.
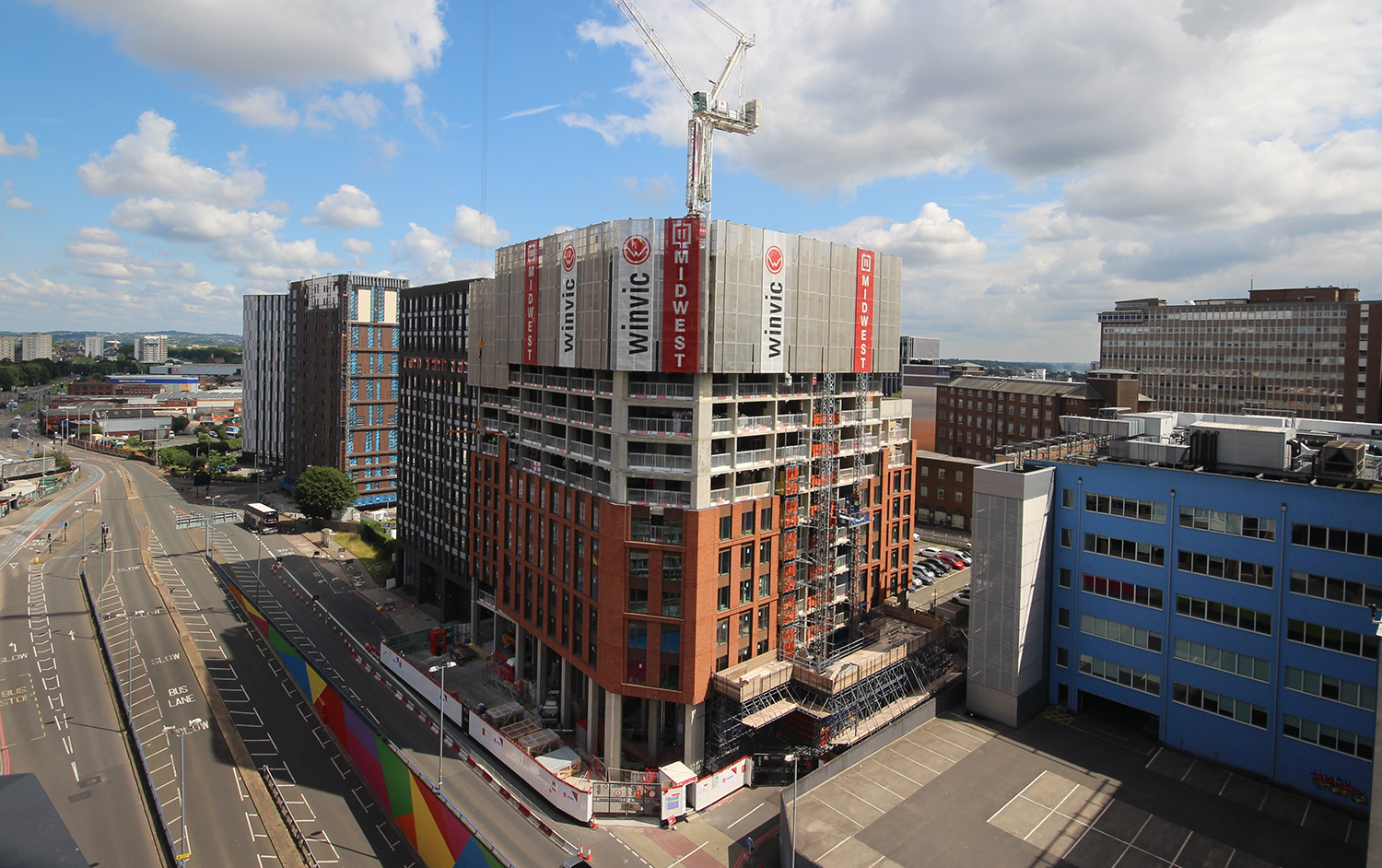
New tech in action
Inside the building, we meet some younger members of the team, who are busy working with some of the technology that Winvic is trialling on the project. Former T-level student and now full-time employee Anas Ahmed is carrying out quality assurance (QA) checks with the help of GAMMA AR.
Ahmed holds his mobile phone over the light switches that have been installed, and the augmented reality image of where the BIM model says they should be is superimposed over the top of the picture. “It’s a clever bit of kit which makes QA easier,” he says. “And it’s very accurate.”
Another former T-level student, Mohammed Sammad, is standing with a remote control while a robot draws lines on the floor. This technology, HP SitePrint, marks up the position of every item for every room of the building: partitions, wardrobes, bathroom pods, switches and sockets, sprinklers, spotlights, ventilation ducts and fans. Winvic is trialling one of only six prototype generation 2 HP SitePrint robots in the world, and the only one in the UK.
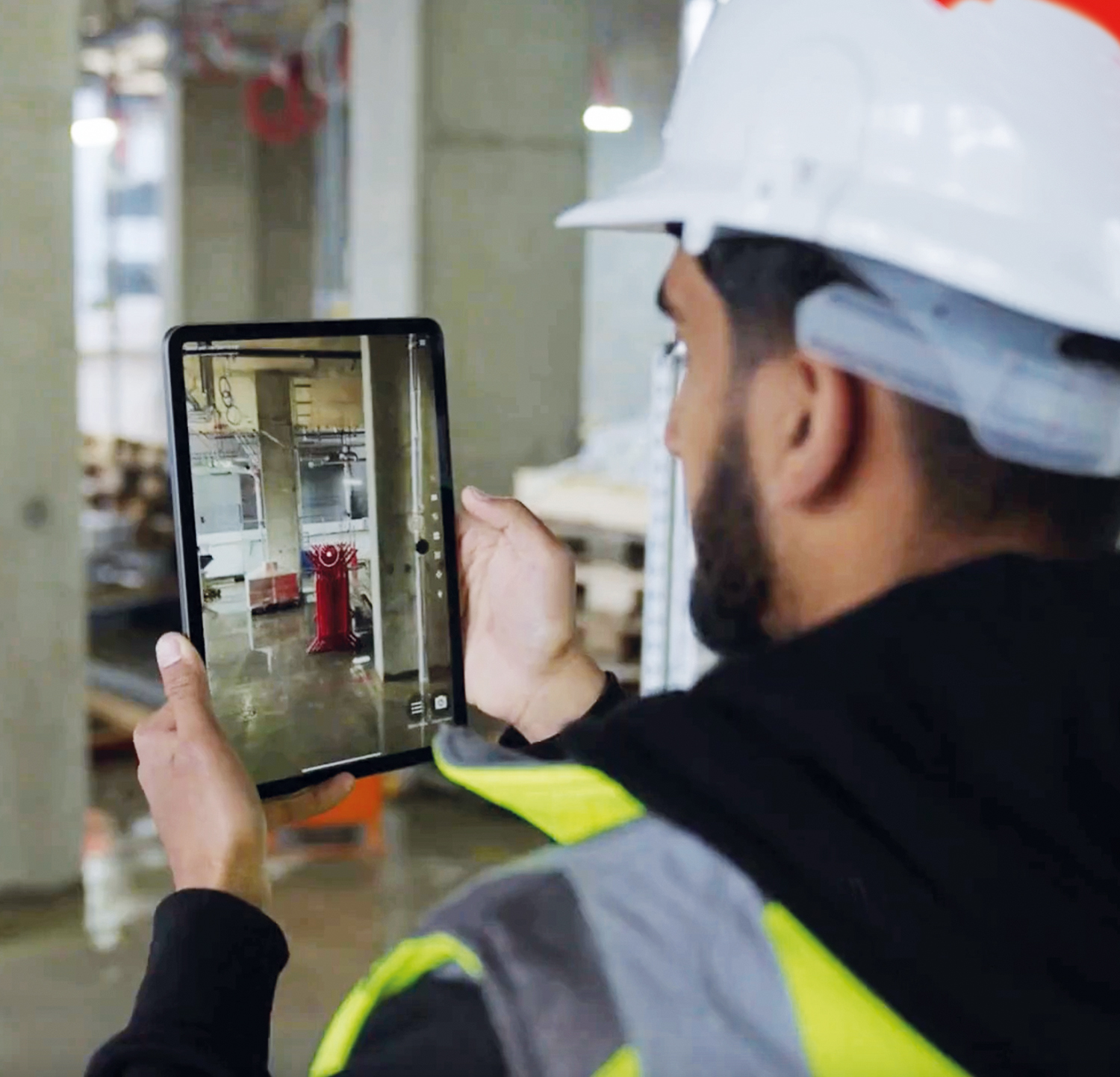
“The whole driver of using it is to prevent rework and clashes,” says Elson. “When the dryliners put the studs in, they know where the sockets and switches will be. We are at level 12 and we have not had one clash between MEP, dry lining and joinery.” It’s faster, too, he adds, and removes the risk of setting-out errors.
Elson is brimming with pride over the work of 17-year-old Viktoriia Grachova – who came to the UK from Ukraine – and has taken a leading role in using the HP SitePrint robot for setting out. She is studying for her T-level, while working part-time on site.
Battery power
Elson is also keen to point out the site’s energy source: a battery, housed in a container which has replaced three 350kV generators. Elson explains that the tower crane, the goods hoist and the passenger hoist would have required a generator each to provide the startup loads they needed.
The battery, called the Enertainer and supplied by startup Hong Kong company Ampd, converts 90A to 400A and provides all power for the site, trickle charging itself from the mains. “Because we are on green electricity, we have saved 150 tonnes of carbon in four months from the beginning of July and 600 litres of diesel,” says Elson.
With no fumes, no noise and no risk of diesel spillages, the Enertainer is perfectly suited for city sites, says Elson: “Going forward this will be implemented on all our multi-room sites.”
It’s difficult to find fault with this beautifully run site. The Considerate Constructors Scheme (CCS) assessors appear to have come to the same conclusion: the project scored 48 out of 45 and 46 out of 45, due to extra points awarded for the innovations in use here.
CV: David Elson, operations manager, Winvic
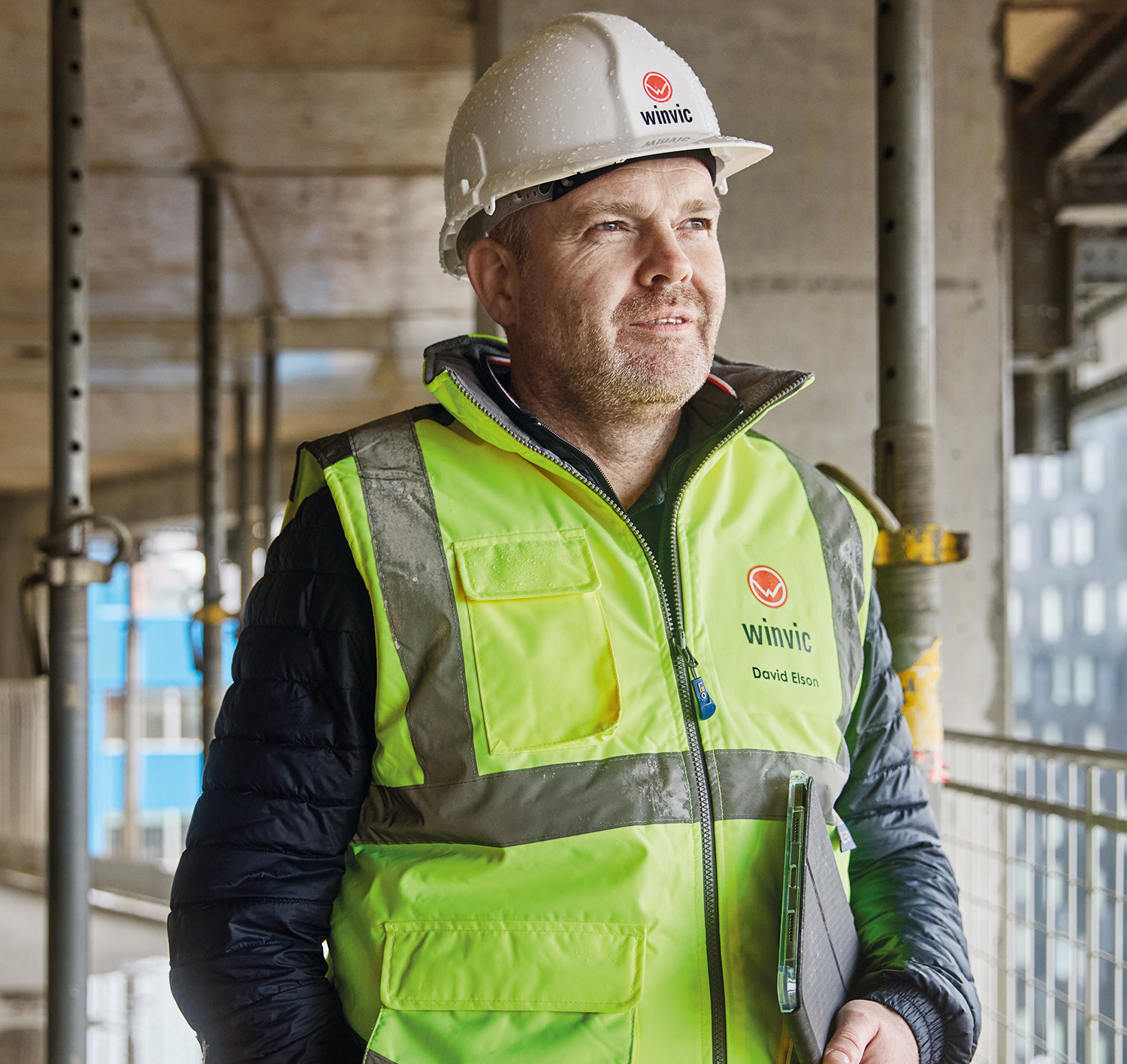
David Elson’s construction career started straight from school, with a job as a site engineer for Tarmac. He went on to study for a BTEC in civil engineering followed by a construction engineering management course at Loughborough University, both while working.
Having worked up through the ranks to become a project manager at Tarmac – which became Carillion – he moved to work for a local contractor that had set up a development arm for five years, then spent a year with Willmott Dixon, before Carillion persuaded him to return to the business in 2009, where he spent the next 10 years. Six years ago, he joined Winvic.
Elson has worked on most types of project over his career: prisons, hospitals, schools, industrial, commercial, offices, residential, student, apartments and hotels, public and private sector, traditional and PFI. “I like to build,” he says. “I am a builder. That’s my game.”
When asked what he likes most about construction, he replies: “The people. As management contractors, we rely on our suppliers and subcontractors to do the work. I like dealing with people.”
Gamechanging crane control
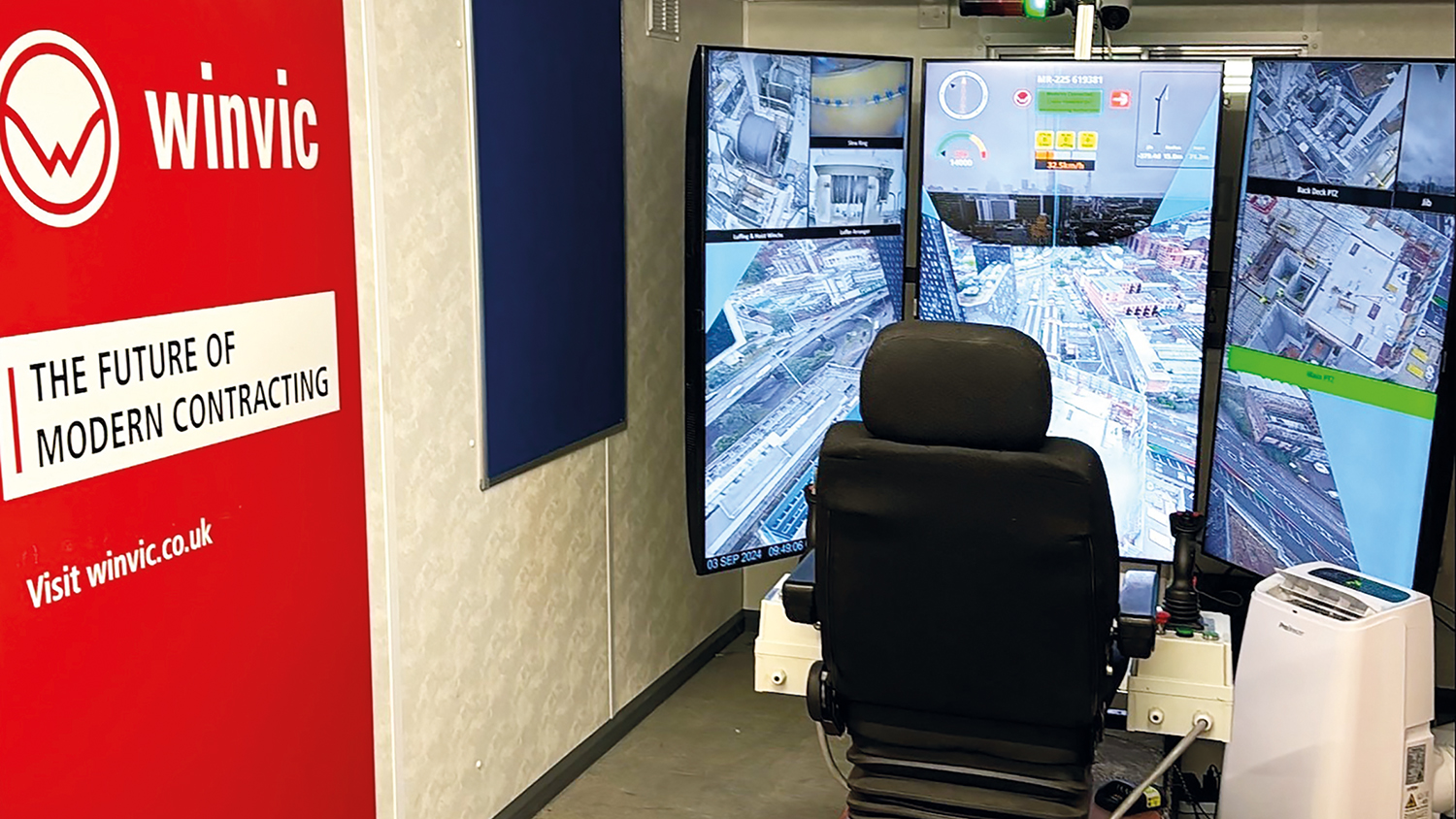
There’s something a bit disconcerting about walking into a site cabin and finding the tower crane driver sitting there in front of multiple screens. It feels more like a security room, or even a gamer’s bedroom. But the driver’s chair is exactly the same as the one up in the cabin at the top of the tower crane and the controls are the same too.
This is the first time that this remote-controlled technology, Skyline Cockpit, has been deployed on a project site outside its home country of Israel. Crane company Radius had been using it in its yard for around 18 months and introduced the idea to Winvic.
Dale Burton, who is the resource manager at Radius, is sitting in the chair when we visit. Driving the tower crane remotely feels the same as if he were in the cab, he explains: “When you are driving the crane you feel the machine move. Here, your eyes take in the movement conveyed by the cameras.”
There are plenty of arguments for why this style of tower crane driving is safer than the traditional method. The operator has more information – such as wind speed and radius data – displayed in front of them; the cameras give better views of the site and of the hook; there isn’t a 30-to-40-minute climb to reach the controls; and if an operator were taken ill, getting them to safety would be a straightforward matter.
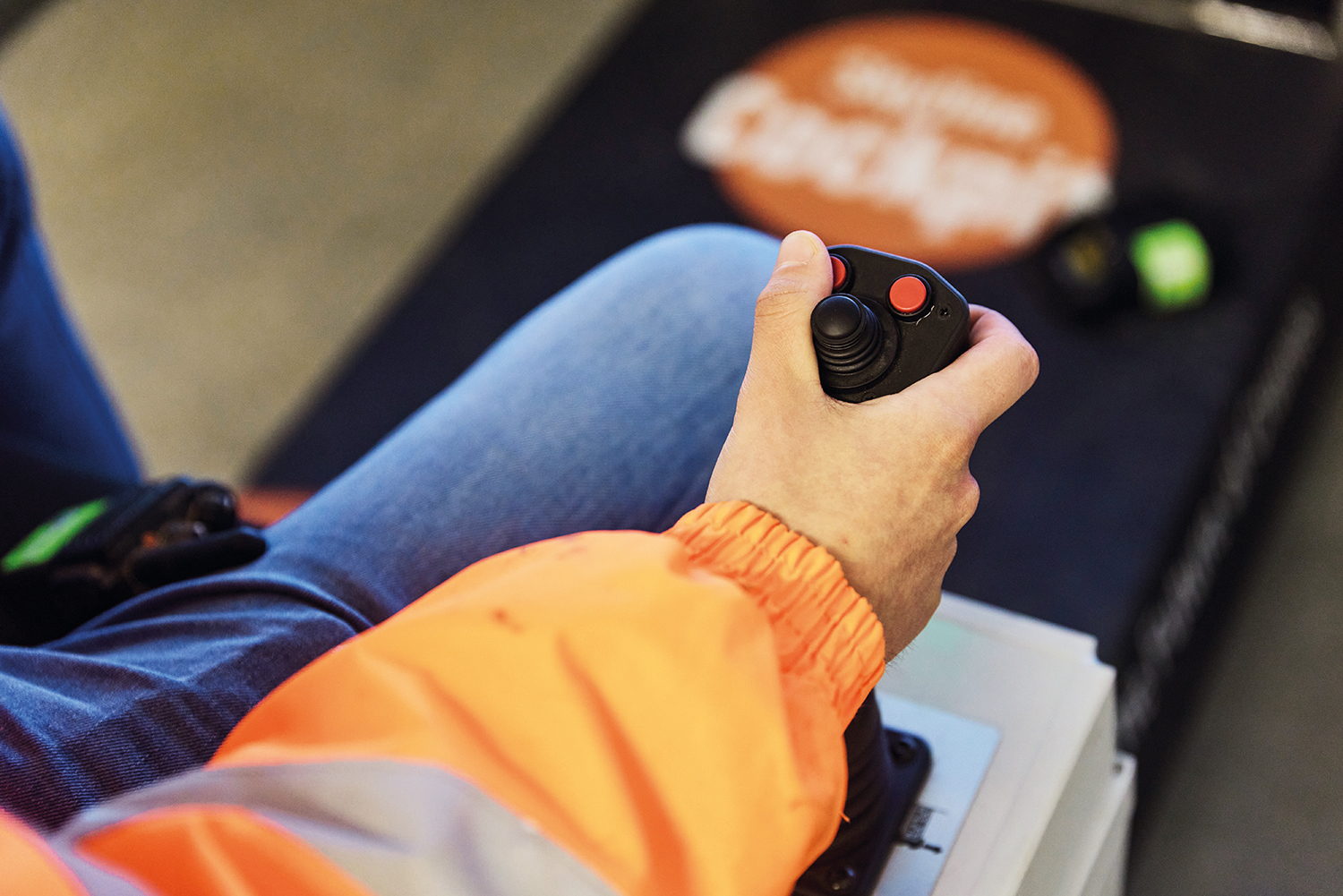
Better for wellbeing
It’s better for wellbeing too, says Burton. “Being stuck up in a crane, you are a bit isolated,” he says. “All you have is the walkie-talkie; it is your friend. Down here you have more interaction.” Going to the toilet is a far more civilised experience too.
The Skyline Cockpit system also offers the opportunity to collect and analyse data. “Once we get eight weeks’ worth of data, we can highlight busy and quiet points and move activities around, for instance bringing deliveries in at quieter times,” says Winvic project manager David Elson.
After a 12-week trial, Winvic elected to keep the system on site. Elson says that by analysing the daily and weekly patterns of activity for the crane, it has improved efficiencies in lifting by just under 10%.
Currently, Radius has three drivers who can use Skyline Cockpit. And unfortunately,
two of them have just been tempted to lucrative jobs in the Middle East. However, as Elson points out, this crane could theoretically be driven from anywhere in the world. It can also be operated traditionally, from the cab, if needs be.
Winvic’s angle on the crane has been that it’s a good way to encourage younger people to become crane drivers; the controls could be any design, says Elson, even the same as an Xbox controller. Ultimately, this technology could reduce demand for tower crane drivers.
“There’s a chance it could be semi-autonomous, although it’s not quite there at the moment,” says Burton.