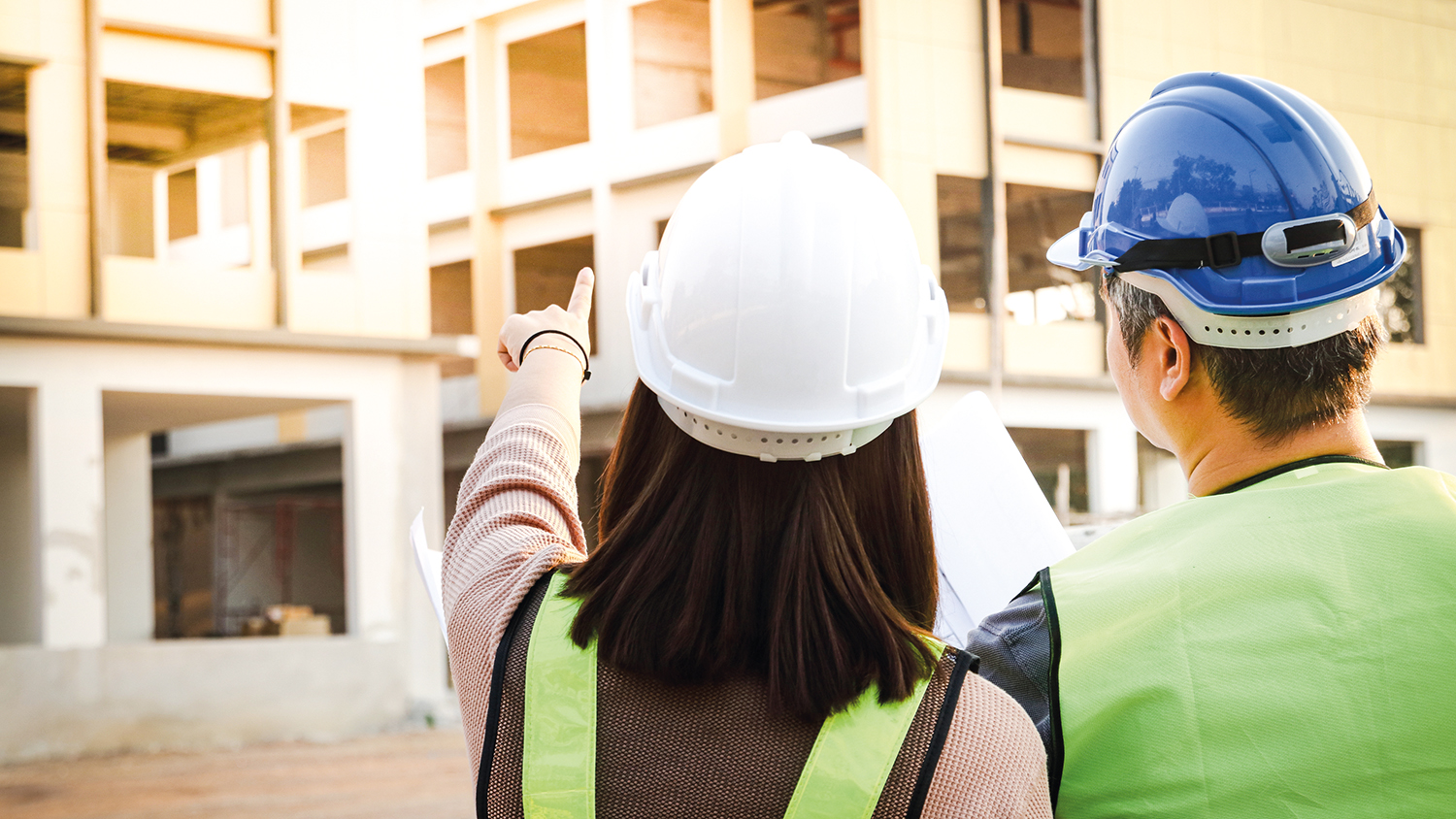
The construction industry needs to change its mindset if it wants to provide the quality assurance it aspires to, writes Nicola Markall FCIOB.
Quality control is in the spotlight. There is an increasing awareness in the industry and the public of the real-world consequences of bad practice, driven by recent high-profile and tragic incidents. For the sector, the Building Safety Act has brought the issue into greater focus.
Controlling quality to ensure we have assurance that buildings are built correctly is fundamental. As things stand, we risk a ‘tick box’ mentality becoming a replacement for effective checks.
Project teams conducting quality control checks should collate evidence backed up by traceable documentation and photographs. They should not merely answer the question ‘Is it done?’ but ‘Is it done correctly and to the required standards, specifications and approved design?’
Beyond box-ticking
This evolution towards ‘ticking boxes’ has crept up on the industry incrementally. It’s a shift that could be driven by several factors. Digital transformation has helped with quality control and problem solving. Yet quality control still requires a project team to spend a certain amount of time on site.
In some cases, condensed construction periods and the shortage of people with the adequate skills, experience and technical capabilities could hinder this process, leading to a ‘ticking boxes’ approach that does not quite provide the quality assurance we aspire to.
At the heart of this issue is the need to build strong, competent and technically knowledgeable teams. Each team member must contribute their respective field of expertise and work collaboratively on delivering a successful project across the board.
Creating teams like these requires careful planning, and it is here that the construction sector can learn from the nuclear sector. In nuclear, planning timelines are by necessity longer and teams are resourced not on ‘who is available’ but on ‘who will best complement the other skills and competences in the team’.
A shift in mindset
Accepting that effective quality control requires investment of time and resources is a mindset shift. To achieve this shift, all stakeholders must understand the value of proper quality control – both in the ‘here and now’ – in terms of keeping every individual on every site safe – and for decades to come.
The consequences of failing to address this challenge are wide-ranging and serious: from having to rectify or rebuild elements of projects or even entire buildings with the associated costs, delay and impact on reputation, right up to injury or loss of life.
As an industry, we have an opportunity to re-evaluate how we approach quality control, and to make sure everyone involved appreciates the value of getting it right, and we should take it.
Nicola Markall FCIOB is technical compliance director at Sir Robert McAlpine.
Comments
Comments are closed.
A good point. I already do this. I spend time on site randomly checking various installations. I’m not predominantly looking at QA paperwork but construction dwgs, specification and manufacturers literature (Technical Submittal) to determine if it’s been installed correctly. I produce a report which includes photographs, specifications and dwg snips with document numbers. I do this for all elements I review whether the installation is incorrect or correct.
This provides an independent review of installation irrespective of whether the Supply Chain Partner considers the area complete or ready for handover. Needless to say, something is no considered non-compliant if it is not complete.