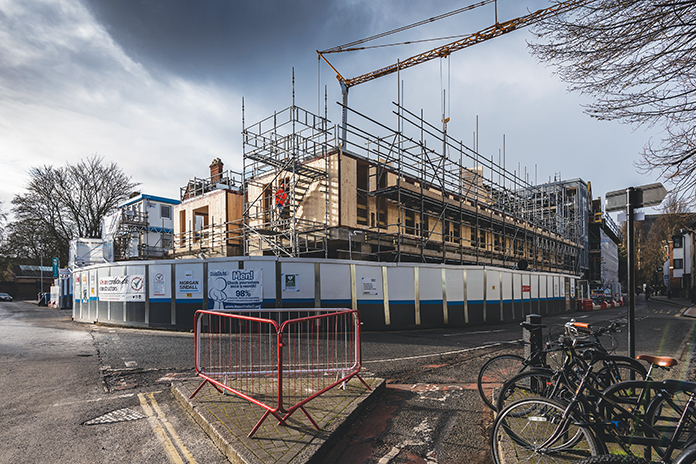
Use of CLT panels on the student accommodation has reduced disruption in the tight city centre location
On the redevelopment of the world-famous Cambridge Union Society building, Morgan Sindall construction has combined heritage restoration techniques with modern offsite construction. Stephen Cousins reports. Photography by Butterflyeffect/Realitypaused.com
Few buildings have a political and cultural history as rich as the Cambridge Union Society (CUS). For over 150 years, it has hosted the likes of Winston Churchill, Margaret Thatcher, Bill Gates and the current Dalai Lama in its famous debating chamber. The Footlights venue in its basement was where Stephen Fry, Emma Thompson, Sue Perkins and David Mitchell
honed their comedic skills.
Cambridge Union Society site redevelopment
Value (CUS refurbishment): £4.3m
Value (Trinity College student accommodation): £10m
Project team
Main contractor (both projects): Morgan Sindall Construction
Project manager (both): Bidwells
Architect (both): Bland Brown + Cole
Structural engineer (CUS): Mott MacDonald
Structural engineer (Trinity): Smith & Wallwork
M&E (CUS): Cunnington Clark
M&E (Trinity): Integral D&B
Groundworks and concrete frame (Trinity): MJS
Brickwork (both): Proctor
Windows and curtain walling (Trinity): Elliston, Steady & Hawes
CLT frame (Trinity): KLH
Structural steel frame: (CUS link): Crofton Engineering
Programme
Start date: December 2018
Completion dates: CUS, December 2020; Trinity, January 2021
Opened in 1866, adapted and enlarged over the decades to meet the Union’s evolving needs, the Grade II-listed building is now undergoing a major redevelopment, including the repair and reinstatement of key Victorian features.
The revamp will give the Footlights venue a refit, extend the existing bar, and replace a section of facade, added in the 1930s, with a replica of the Victorian original. The adjoining development will house a new graduate accommodation block for 45 students at Trinity College with a restaurant on the ground floor.
In construction terms, the project is a play of two acts as main contractor Morgan Sindall Construction juggles offsite manufacturing, including prefabricated concrete and a cross-laminated timber (CLT) superstructure on the student accommodation, plus traditional techniques and materials, including stone, handmade brick, timber joinery and leadwork on the CUS building.
Just-in-time deliveries and CLT panellisation on the student block have helped reduce disruption and noise at the city-centre site, on the corner of Round Church Street and Park Street, a major junction with live bus routes.
An intricate facade retention scheme for the Union building, designed to support the facade while a lower section was demolished and reinstated, had to squeeze within a narrow footprint and incorporate a scaffold for bricklayers to work from (see box, p30).
Nigel Arnold, contracts manager at Morgan Sindall Construction, says: “The temporary works people have really ‘earned their corn’ on this job in coming up with a system that both holds up the building and allows adequate space for workers to build up the new facade.”
Funding frustrations
The redevelopment project follows years of uncertainty over what form it should take and how it should be paid for. The Union, which is a self-funded charity, had explored various options for investment without success until it agreed a deal allowing Trinity College to lease the adjacent plot of land and build a £10m accommodation block.
A joint development plan was approved by Cambridge City Council in 2017, which later had to be redesigned to bring it within the CUS budget of £4.3m. Approval for the revised redevelopment was granted in January 2018.
Andrew Lightfoot, associate at architect Bland Brown + Cole (BB+C), says: “The Union see this as an initial phase of work needed to make right the elements that are slowly failing, to increase the frontage and renovate the bar area to bring in money that should enable future developments and improvements to the building.”
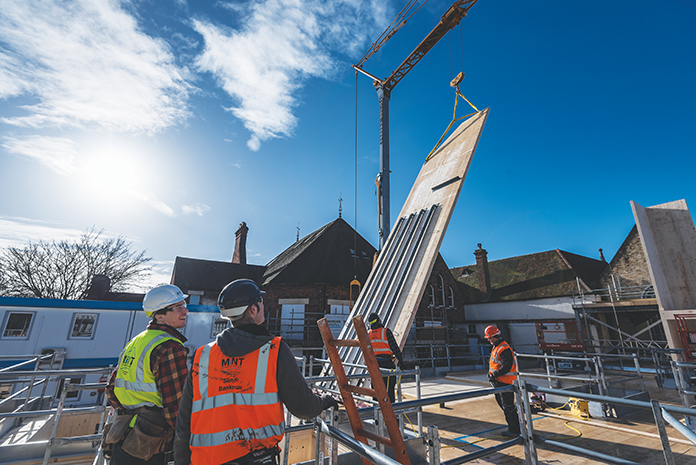
Left and below: The CLT sections that form the stairwell in the Trinity student accommodation building are craned into place
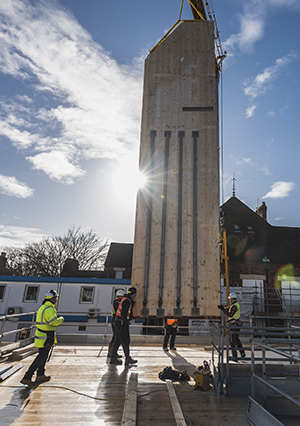
Morgan Sindall Construction is constructing the student accommodation as a design and build, and the CUS building through a traditional form of contract. BB+C is architect on both, working for Morgan Sindall Construction on the Trinity scheme and for the client on the Union building. There are two structural engineers: Smith and Wallwork detailing the Trinity Project and Mott MacDonald on the CUS project.
The two sides of the redevelopment are separate, but share a party wall and a common foundation extends below Trinity and a steel-framed ‘link building’, which provides a new main entrance into the Union on Round Church Street and vertical circulation, including a lift.
Creating the foundation required close communication to ensure both sides completed simultaneously, ready for follow-on work to begin. The complexity of sheet piling used to form the basements and related temporary propping made this a particular challenge.
“Traffic from buses meant the loading situation was quite onerous and sheet piling had to be installed around the perimeter,” says Panayiotis Papastavrou, senior structural engineer at Smith and Wallwork, responsible for the Trinity building. “Temporary propping for the piling had to be installed in different stages to match the sequencing of three months of planned archaeological work, with archaeologists digging on both sides of the basement at the same time.”
“The temporary works people have really ‘earned their corn’ on this job in coming up with a system that both holds up the building and allows adequate space to build up the new façade.”
Nigel Arnold, Morgan Sindall Construction
The CUS building was designed by prolific English architect Alfred Waterhouse, the man behind Manchester Town Hall and the Natural History Museum. Modifications included a major expansion in 1886 to create space now occupied by the bar and library, and several art deco elements in the 1930s, most notably a section of facade running from basement to first floor level along the frontage on Round Church Street.
Most of Cambridge escaped the Second World War with little damage, but a bomb landed on the building causing significant damage to the Library, where some older books still display shrapnel wounds.
The art deco facade was poorly conceived and executed by today’s standards, so the client proposed to replace it with something more in keeping with the original and with the location in a conservation area. “Over the years, the render had blown, the Crittall windows were pinned back because they were rattling around and the whole facade was getting to the point where it was becoming unsafe,” says Arnold.
Hidden structure
The designers pored over the original plans, kept in the V&A museum in London, to develop appropriate details for the masonry, timber windows and other heritage features. Subsequent site investigations revealed hidden elements not included in drawings. The external render concealed an array of steelwork and fabric in varying conditions.
Council planners wanted the CUS and Trinity College buildings to resonate with each other, so the external facade of the student block will also feature stone and brick but detailed in a more contemporary way: pared back with fewer profiles in the stonework and deeper reveals. Skilled craftsmen using traditional construction materials, such as solid masonry and handmade bricks are working across both projects.
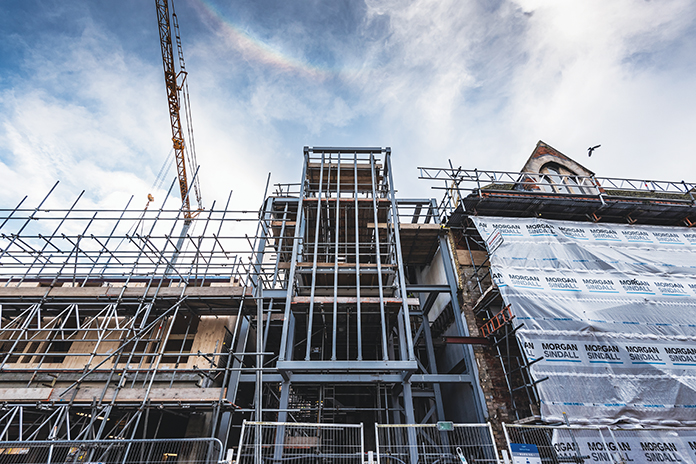
A steel-framed link building will provide a new entrance and vertical circulation during construction, above; and CGI, below
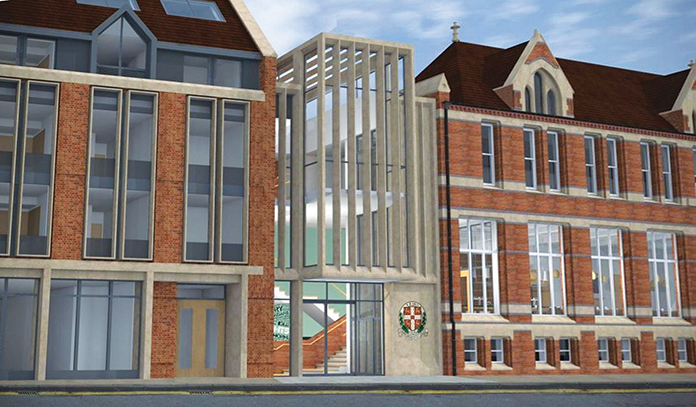
The outer skin of the student accommodation will conceal a distinctly 21st century structure comprising multiple elements of in-situ concrete frame, up to first floor level, and a CLT superstructure rising to the fourth floor.
The groundworks contractor, MJS Construction, joined the project early and proposed that the ground and first floor slabs were cast using a Bamtec reinforcement system, by Hy-Ten.
Papastavrou comments: “The large rolls of prefabricated reinforcement provided an enormous advantage in terms of programme and labour. In addition, precast concrete stairs lifted in by crane helped minimise time on site.”
The superstructure will comprise 500 cu m of engineered timber, delivered in 11 truckloads by supplier KLH and installed by a team of six. A self-erecting crane distributes the panels around site.
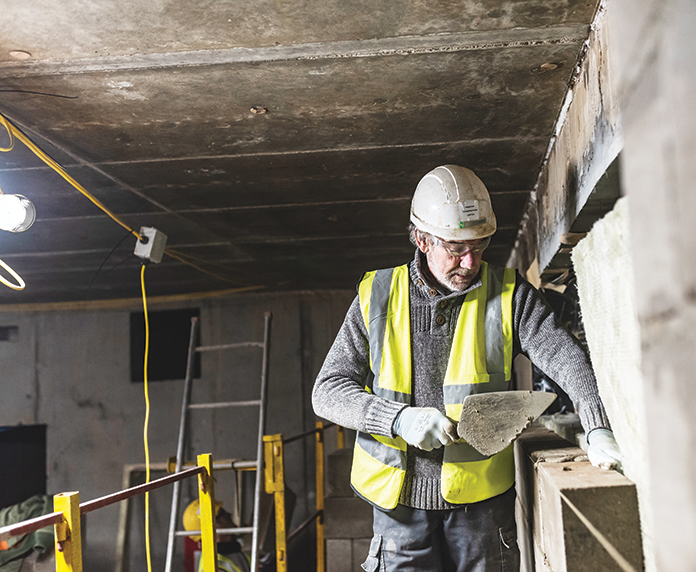
Heritage trades work behind the scaffold
This approach helped minimise noise and vibration. CLT is well suited to student accommodation, in terms of strength and achievable spans, says Papastavrou. “Clients like the idea of using the material because time on site is precious.”
The timber structure is now virtually complete, whereas on the CUS side, bricklayers have only reached about eight courses high, which demonstrates how modern construction has managed to innovate despite its reputation for being slow to adapt.
With the frame up, work has begun installing aluminium windows and curtain walling elements. M&E first fix and screeding in the basement are underway.
Next door, the Union building exterior will get a makeover, including repairs to timber windows and slates and a thorough clean up, ready to welcome the next generation of budding British politicians, actors and comedic talent.
Tricky temporary works
The facade retention system is a complex engineering design on a narrow footprint.
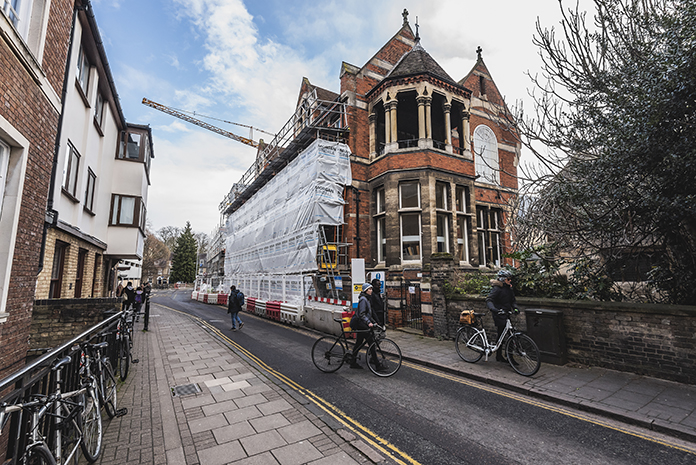
A compact solution avoids encroaching on the road
To reinstate the Cambridge Union Society (CUS) building’s masonry facade from ground to first floor level, Morgan Sindall Construction worked with structural engineer Mott MacDonald to devise an elaborate facade retention system, comprising a network of galvanised steel internal and external props, plus 18 mild steel needle beams, each weighing around 140kg, that thread through the existing masonry wall at first floor level.
The introduction of the painted needle beams has made it possible to remove the 1930s steelwork, brickwork, blockwork and Crittall windows at the lower levels of the building, and then to install replica Victorian brick, stone and timber windows.
The solution had to be compact, in order to fit within the 1.5m-wide footpath that runs alongside the building without encroaching on the road, and to integrate with a highly bespoke access scaffold that enables tradespeople to carry out repairs and restoration on the facade.
“I have never seen a facade support as intense as this,” says Nigel Arnold, contracts manager at Morgan Sindall Construction. “We had to open up and survey multiple layers within the CUS to ensure the props wouldn’t clash with the rest of the structure.”
He explains: “Foundations underlying the structure had to be designed to reduce loads from the props to an acceptable level and take into account the poor ground conditions. Maintaining access and egress for labour and materials through the propping and the scaffold is an ongoing issue because it is such a tight space.”