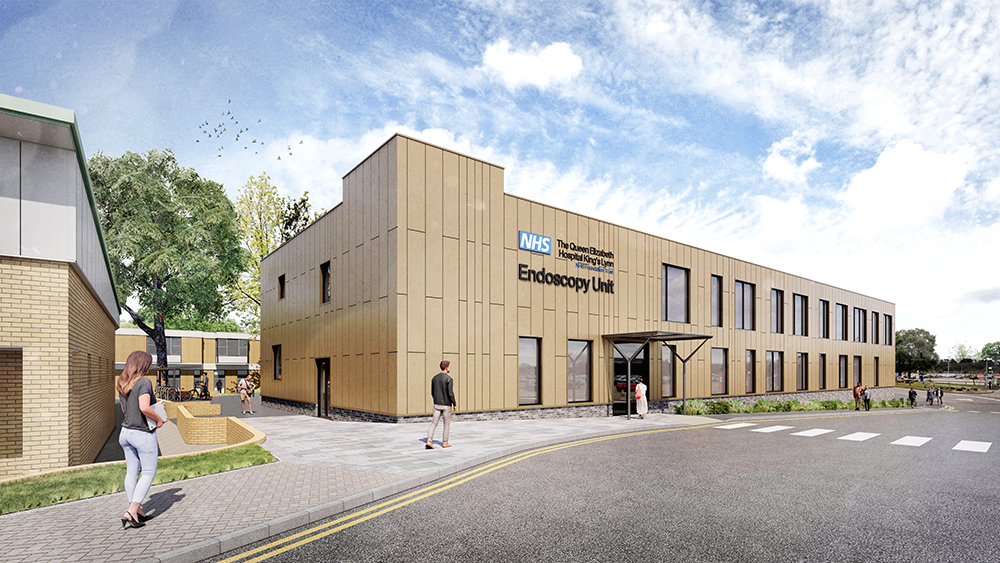
A new Endoscopy Unit at Queen Elizabeth Hospital in King’s Lynn aims to be a flagship for digital innovation and modular construction. CM reports.
The Queen Elizabeth Hospital (QEH) King’s Lynn in Norfolk is undergoing a modernisation programme and digital construction is set to be at the heart of that.
QEH was built as a RAAC (reinforced autoclaved aerated concrete) hospital in 1980. Today, 79% of the hospital buildings have RAAC planks which require ongoing monitoring and emergency repairs. In 2021, the organisation was awarded £20.6m in emergency funding, enabling it to install ‘failsafe’ roof supports, to reduce the risk of RAAC plank failures, and to undertake other modernisation projects. These include a new state-of-the-art endoscopy unit.
Project team – Endoscopy Unit, Queen Elizabeth Hospital, King’s Lynn
Client: Queen Elizabeth Hospital King’s Lynn NHS Foundation Trust
Value: £13m
Client team: Exi Group (project management, design, digital management)
Programme: 11 months
Contract: JCT with amendments
Contractor: MTX
Contractor design team: IBI (architect); DSSR (MEP); Rossi Long (structural engineer); BIMBox (BIM coordination)
Modular supplier: Kingston
The two-storey, 3,913 sq m development will modernise facilities and enable all endoscopies to take place in one building. The new unit will also free up space in the main hospital so the organisation can start installing the roof supports across the first floor.
“The endoscopy unit’s development is critical to the overall programme delivery and therefore speed and simplicity are key,” explains Garry Fannon, director with the trust’s multi-disciplinary consultant Exi Group.
“We took time to understand the challenges of the current physical estate and the time restraint inherent in the project. For these reasons, we decided a modular solution was the best option. Over 90% of the unit will use modern methods of construction (MMC).”
Exi is also working with the trust to develop its digital capability.
“The organisation recognises that its digital maturity is an area requiring investment and sees the new endoscopy unit as a vehicle to test and trial new innovations and technology,” Fannon says.
“Digital working will complement the MMC approach. The project will be in line with the digital aspirations set out in the government’s 2019 health infrastructure plan (HIP) and the ‘digital blueprint’ published in 2020 to steer the design and construction of hospitals.”
The project is following the UK BIM Framework.
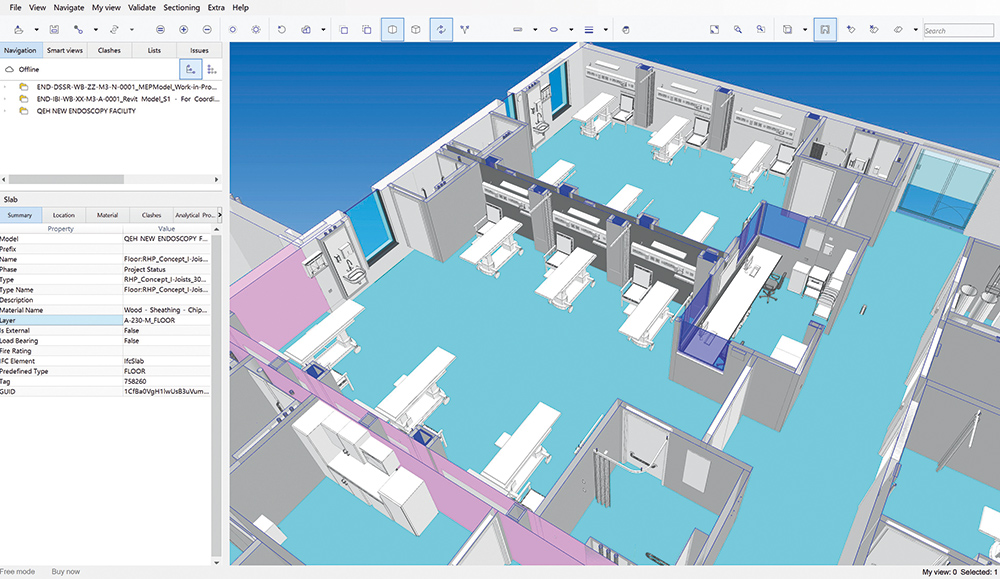
“Exi digital management wrote the project’s exchange information requirements (EIR) and asset information requirements (AIR) on behalf of the trust,” explains Fannon. “The design team of main contractor MTX delivered models with asset data in line with these requirements.”
Clash detection process
“MTX’s design team also worked with digital consultant BIMBox on the BIM coordination, to increase efficiency and accuracy and reduce risk in the design process,” Fannon continues. “The clash detection process captured and resolved all major design issues before enquiry documents were sent out to the modular supply chain. The HVAC design team were able to coordinate the network of services into small cellular rooms first time.”
The BIM process helped modular supplier Kingston to generate the modular design, Fannon explains.
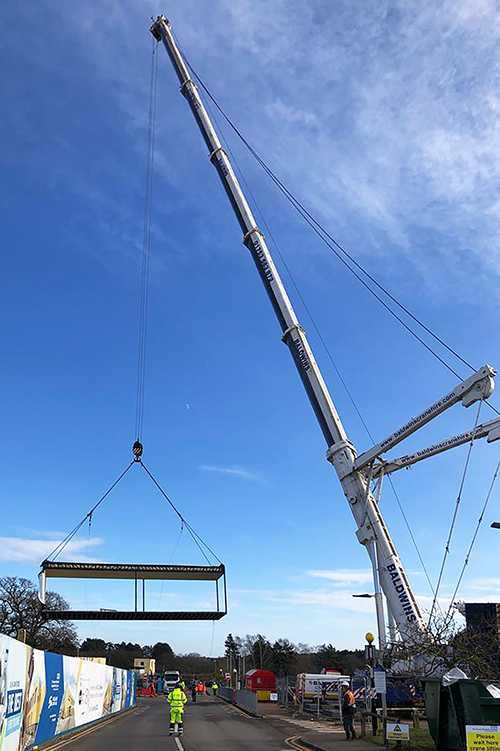
“One of the challenges for a modular contractor is coordinating the design before they go into manufacture,” he says. “Delivering a coordinated design that has been through a BIM process allows the modular contractor to achieve design approval a lot quicker and thus start manufacturing sooner.”
Installation of the 53 modular units, each typically 3.6m wide and 15.5m long, began in February 2022.
To monitor quality, MTX used 360 photography platform Multivista, offering the contractor and the QEH team a full audit of the construction process.
“Multivista visits the site every two weeks and takes images at the same point,” says Fannon. “The platform allows the user to look historically at each room and interact with the imagery.”
The new unit will include smart technology, which has been designed with the clinical teams and will be installed on site. This includes interactive information screens, supplied by Clevertouch, and smart room sensors which capture information affecting the patient experience, such as light and temperature levels, and how frequently a room is used.
The project is due to complete by the end of June 2022.
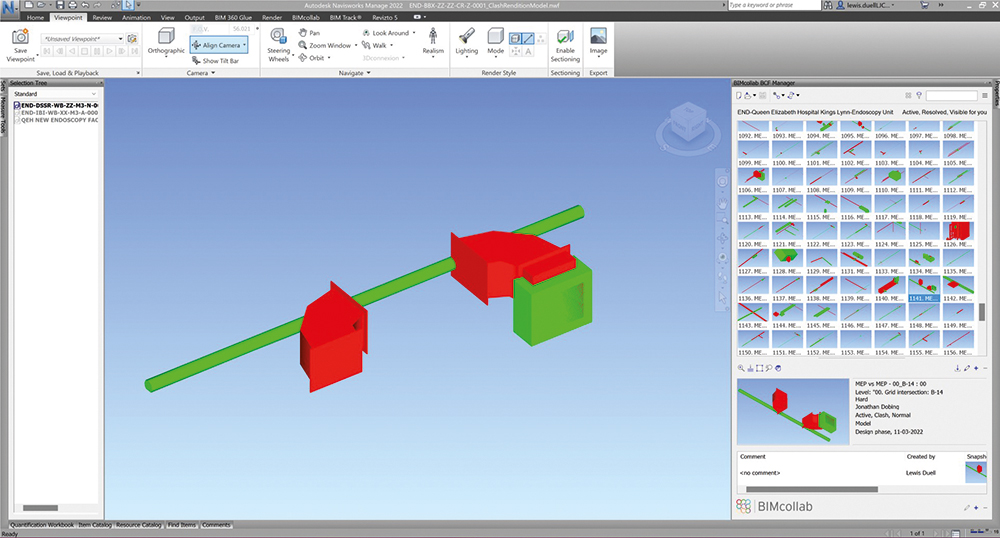
Fannon says: “This ‘digital flagship’ is the result of a collaborative process involving QEH’s digital team, clinical staff and supply chain partners. The outcomes will support QEH’s ambition to improve their digital maturity and estate management strategy.”
Exi Group is also developing an estate-wide digital-first approach strategy with QEH that will deliver a more efficient facilities management service. “This will allow the QEH estates team to move away from their analogue estate and allow computer-aided FM to be trialled,” says Fannon.
Meanwhile, QEH is bidding to be one of the eight new hospital schemes announced by the government last year. The plans are for a single-phase new build or a part new build and part refurbishment. If approved, the digital learning from the endoscopy unit will be invaluable for the new hospital project.