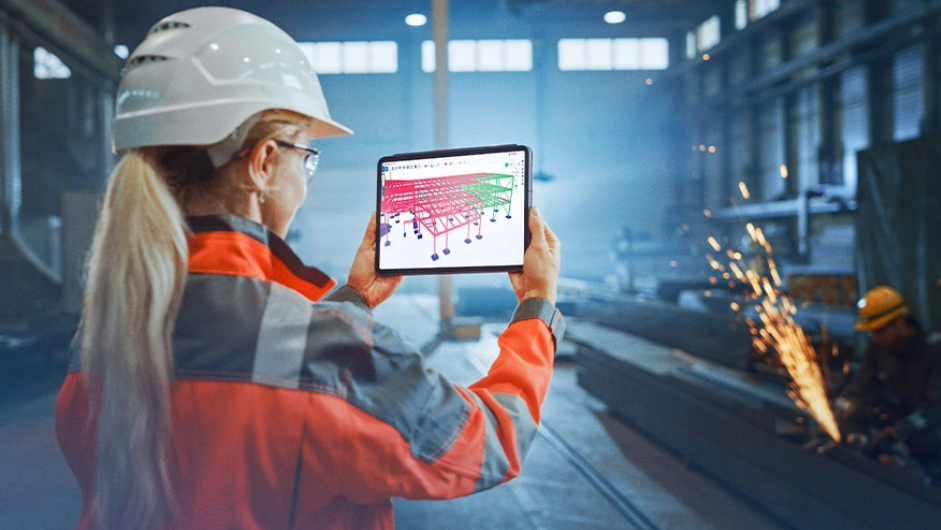
When it comes to reducing a project’s environmental impact, a lot of attention falls on the initial engineering stages. However, this is not the only place where change is needed. Chris Gatehouse explores the role management information systems can play in the journey to net zero.
Every stage of the RIBA Plan of Works (PoW) generates carbon, making it everyone’s responsibility to do their bit. Even once the approved 3D model has been passed onto the fabricator, changing the way you work can have an impact on lowering the structure’s carbon emissions.
One way is to employ a management information system (MIS). While primarily developed to help improve efficiency and productivity levels, this tool can also lead to sustainability benefits.
Smarter fabrication, greener construction
Used correctly, a digital MIS can be deployed throughout the entire fabrication workflow, from the initial estimating and procurement stages through to the shop floor and beyond.
Consider the estimating and bidding stage as an example. The ability to produce informed estimates not only helps to protect your profit margin – critical during a time of material cost and availability volatility – but it can also contribute to an improved carbon footprint.
A key part of this is being able to generate accurate material lists and quantities, ensuring that you are optimising your steel utilisation, reducing waste, and only ordering the steel you need for the job in hand.

By having a 3D model linked to your digital MIS, you can automatically generate quantity take-offs (QTOs) using the model data. As well as providing a more efficient process, this streamlined flow of data offers the assurance that your QTO is optimised and accurate, reducing the likelihood of human error.
No excess materials, no excess carbon
Another way to reduce carbon is to improve accuracy. Whether caused by errors at the detailing stage or the inefficient transfer of information, material wastage can be a major problem on any project. This could take the form of structural components being fabricated and delivered to site, only for contractors to discover that they cannot be used, due to clashing with other sections.
As well as the obvious delays, these errors and the subsequent rework required to rectify them can also result in excess carbon being generated – emissions that could easily be avoided.
Here, again, a digital MIS will deliver. Such software is not just for managers – everyone can benefit from coordinated and easily accessible project data. Using a digital MIS and other technology, fabricators, welders and machine operators can view the corresponding 3D model and 2D drawings on a tablet, taking the model from the drawing office to the shop floor.
As well as helping to resolve any queries quickly, having everyone connected to the central BIM model and its high levels of information can contribute to a more efficient and more accurate way of working.
Fewer mistakes means less rework, waste and carbon
Trimble’s Tekla PowerFab is developed specifically for steel fabricators, offering connected steel fabrication management. A comprehensive software suite, it provides a systematic and collaborative approach, delivering a smooth, continuous and real-time flow of information on projects from start to finish.
For more information, click here.
Chris Gatehouse is account manager, detailing and manufacturing, at Trimble UK