The transit system being built to connect Luton Airport with its nearest rail station is a complex job, interfacing with live road, rail and air environments. Kier’s Olivia Perkins, who is running the build, talks CM through the major challenges
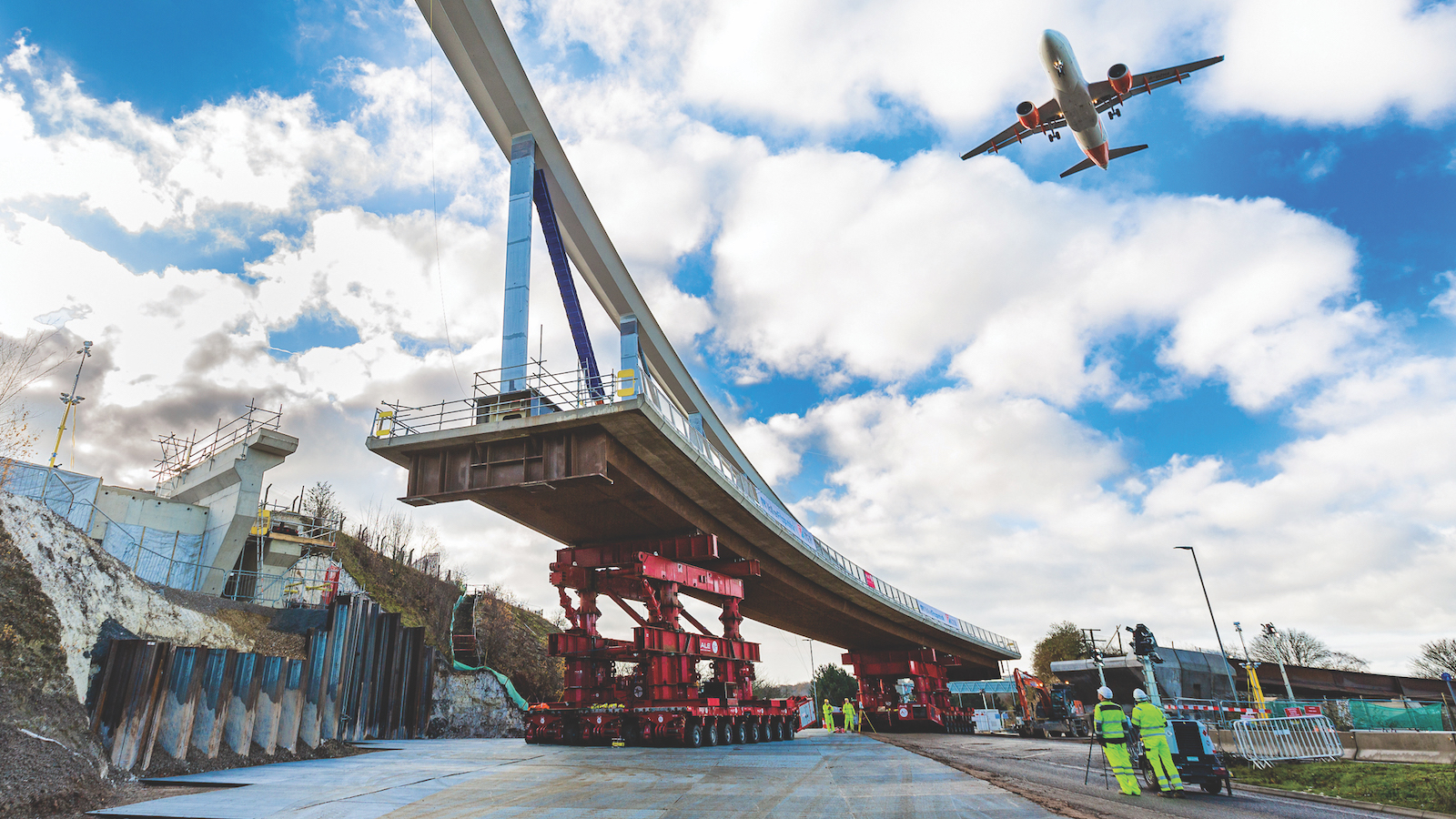
“Communication is absolutely key here,” says Olivia Perkins, Kier’s senior project manager in charge of the Luton DART project, which has an overall value of £225m. And it’s not difficult to follow her reasoning when she describes the complexities of scheme.
Officially known as Direct Air-Rail Transit, this cable-drawn passenger transport system will link London Luton Airport with the nearby mainline Luton Airport Parkway station across a busy dual carriageway. There are several significant design and engineering challenges to coordinate, plus interfaces with live airport, rail and road environments and a workforce of over 200 at peak to manage.
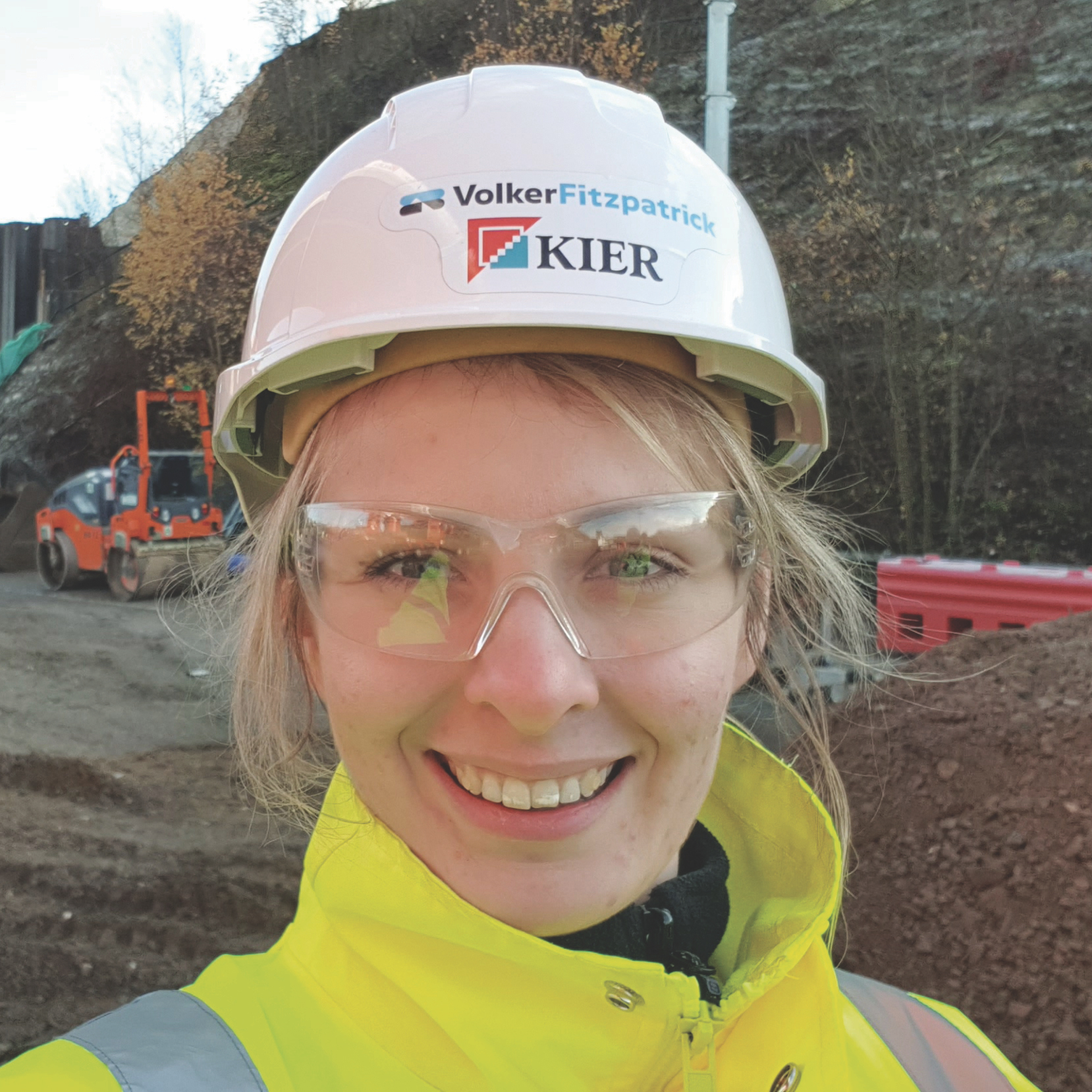
Construction manager CV: Olivia Perkins, Kier
During her civil engineering MEng at Loughborough University, Perkins spent a year with Kier Regional Building, but she has worked on infrastructure schemes since graduating. She spent four years on Crossrail, then moved to HS2, working on tenders and the ECI phase, and spent two months in France with Kier’s JV partner Eiffage, to learn more about high-speed rail. After a travelling sabbatical, she joined the Luton DART scheme in May 2019, taking overall responsibility for the project in summer 2020.
Fortunately, Perkins has plenty of experience of major infrastructure projects – and large project teams.
“I’ve got five section managers in charge of the seven different sections [see map], and each of them is always vying for shared resources,” she explains. “We’ve only got one concrete supplier across the whole DART project and at times there were clashes over which concrete pours took priority. So I had to make tough choices and do what’s right for the job overall, and the client.”
The VolkerFitzpatrick-Kier JV (VFK) began work on the DART scheme in April 2018. From the Parkway station next to the mainline rail connection, the route – which climbs around 30m over its 2.1km course – heads south-east over a 350m-long concrete viaduct then crosses the A1081 Airport Way on the curving Gateway Bridge.
This 1,000 tonne sloping steel structure, 80m long, was prefabricated over eight months at a location half a mile away before being taken to the site on two self-propelled transporters. The bridge was raised up on jacks, then lowered into place during a 10-hour window in November 2019.
“The design of the bridge structure had to be stiffened to take into account the transportation, the equipment required to install it at the site, and the temporary propping,” says Perkins.
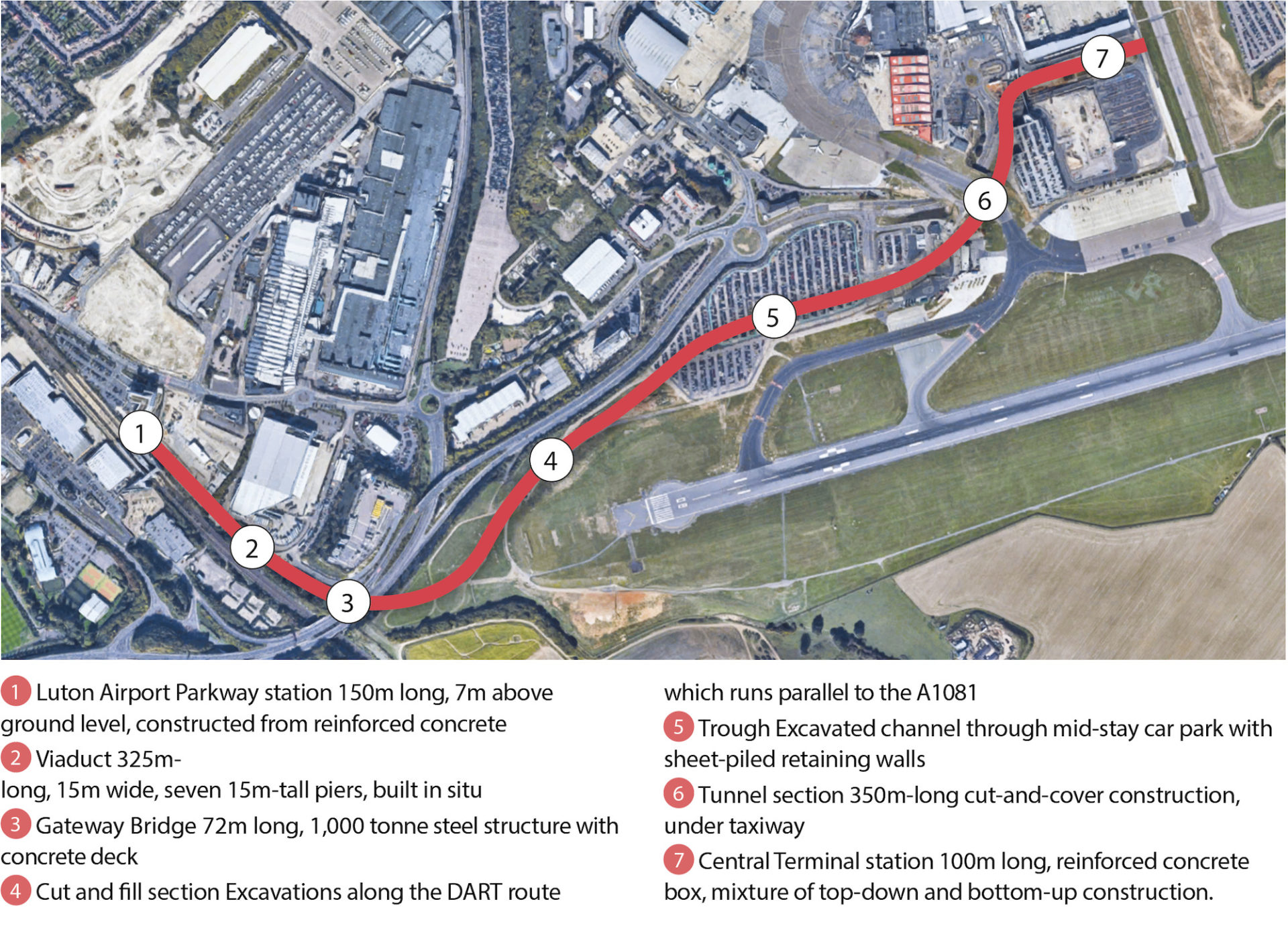
“Digital visualisations were really helpful in planning the operation.
We created a simulation of the bridge travelling along the road and were able to see if any trees or street lighting would be affected. Demonstrating how the structure would be lifted off the transporters and set into place was very helpful for the workforce. The simulation was also informative for the local council and our airport client.”
After the Gateway Bridge, the DART turns north-east, climbing steeply alongside the A1081, before running in a trough through the mid-stay car park. It then dives into a cut-and-cover tunnel, beneath the taxiway, before twisting under the A1081 again, then emerging in the Central Terminal station.
Digital technology has come into its own here too, says Perkins.
“For the cut and fill section, we used GPS machine control using Trimble software, programming the earthmoving equipment with the required profile data,” she explains. “This meant a more efficient dig, minimising the amount of material excavated, and by using ‘fill areas’ around the airport, we sent zero waste to landfill.”
“The main focus for me has been good communication and creating a framework that gets the team working together”
The excavated sections were lined with sheet piles and the tunnels and tunnel approach areas – around 350m of the route – were braced with hydraulic props from Groundforce. “Through value engineering, we were able to remove approximately one-third of the props along this section, compared to the original design,” says Perkins. “Sensors monitor the loads on the props and validate the assumptions in design.”
Construction of the two stations also required complex engineering. The Parkway station sits at ground level, extending 7m in height, while the Central Terminal station is being built underground, using a mix of top-down and bottom-up methods, beneath the airport’s old drop-off area.
Both feature parasol-style roof designs – “giant umbrellas which span the width of the station”, as Perkins puts it, with gold-coloured cladding.
Cantilever beams
The structure of each parasol comprises central columns which support eight high-level cantilever beams, spanning longitudinally, transversely and on the diagonals. Each bay is 22m wide. The cantilever beams are tapered steel plate-girders, varying from 1.2m deep at the root to 0.45m at the tip, to limit their weight.
“To take the weight of the cladding, we had to pretension the cantilever steels which extend out from the vertical sections,” says Perkins.
“This type of roof structure can deflect under asymmetric loading, particularly wind. Stainless Macalloy bars, 42mm in diameter and preloaded to 230kN each, provided the necessary restraint against deflections.”
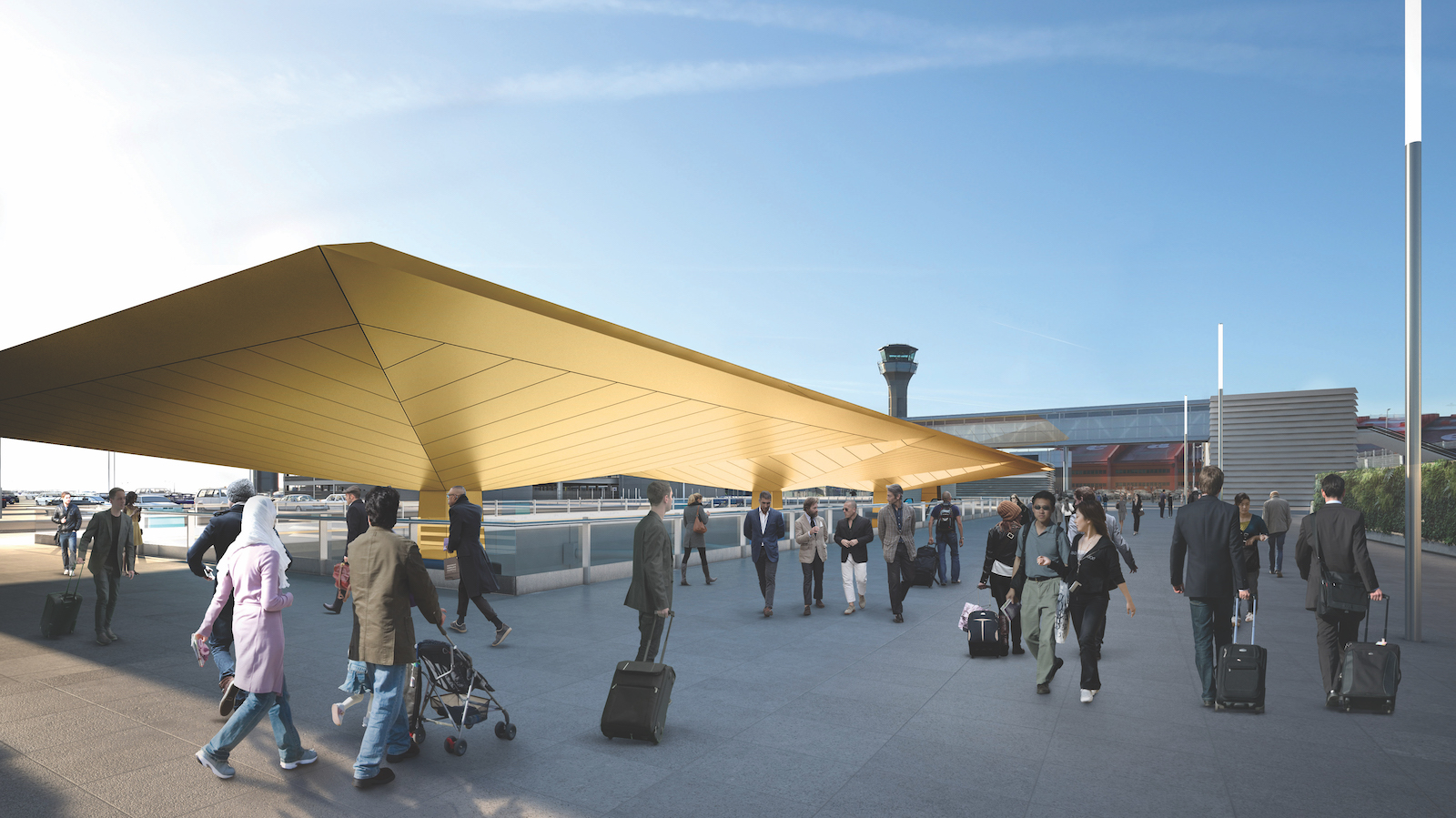
The 100m-long Central Terminal station is being constructed in a deep concrete box, where the design required a fair-faced finish on the 8m-high lining walls. “Normally, we’d tie the shuttering into those walls so the shutters wouldn’t pull away during the concrete pour – however the client didn’t want tie holes visible,” explains Perkins.
“Instead, our subcontractor NJ Doyne, with Peri, devised a temporary works solution where we had two parallel wall shuttering systems, one on either side of the station box, with a massive prop in between to balance out the forces. Once this system was in place, we could do a pour a week, moving the shuttering system along the length of the station.”
Project team
Client: London Luton Airport Ltd
Value: £225m
Main contractor: VolkerFitzpatrick – Kier
Main consultant: Arup
Transit system: Doppelmayr
Other consultants: Tony Gee & Partners, Hewson Consulting Engineers, RPS Group, Coffey
Key subcontractors:
NG Bailey, NJ Doyne, M O’Brien, Severfield, Prater, Victor Buyck, GEL Engineering, Cemex, Arcelor
Programme: April 2018-early 2022
On completion, the Kier JV will hand over a full digital asset model to the client – down to the concrete mixes used. This process is managed using Dalux BIM management software, which was also used to digitise daily diaries and checksheets.
The project has remained operational throughout the pandemic, working in line with the CLC’s site operating procedures, says Perkins.
“This has actually promoted safety improvements,” she explains. “We stopped and reassessed a number of the operations for social distancing, which allowed us to rethink how activities were executed that we sometimes take for granted. For example, we reduced manual handling to improve social distancing, increasing mechanical methods for moving materials around during the reinforced concrete works.
“Installing the parasols meant having more than one person in a cherry picker. We couldn’t avoid that. So we used larger MEWPs, minimised close proximity time, added PPE and put teams into ‘bubbles’. ”
Skills training hub
One legacy of DART that Perkins is especially proud of is the Construction Skills Hub, a joint venture between Kier, VolkerFitzpatrick, the client and local authority. “We have delivered construction skills training for 720 people in the local community and employed 33 apprentices across the project,” she says. “The DART project may be relatively small in terms of national infrastructure, but the local upskilling programme has been a major achievement.”
Reflecting on her role leading the project, Perkins says “this was a stretch position” but a “great experience”.
“I have worked on major infrastructure schemes before but working in and around a live airport is challenging. We have worked hard as a team to build trust with the airport, local council and our client.
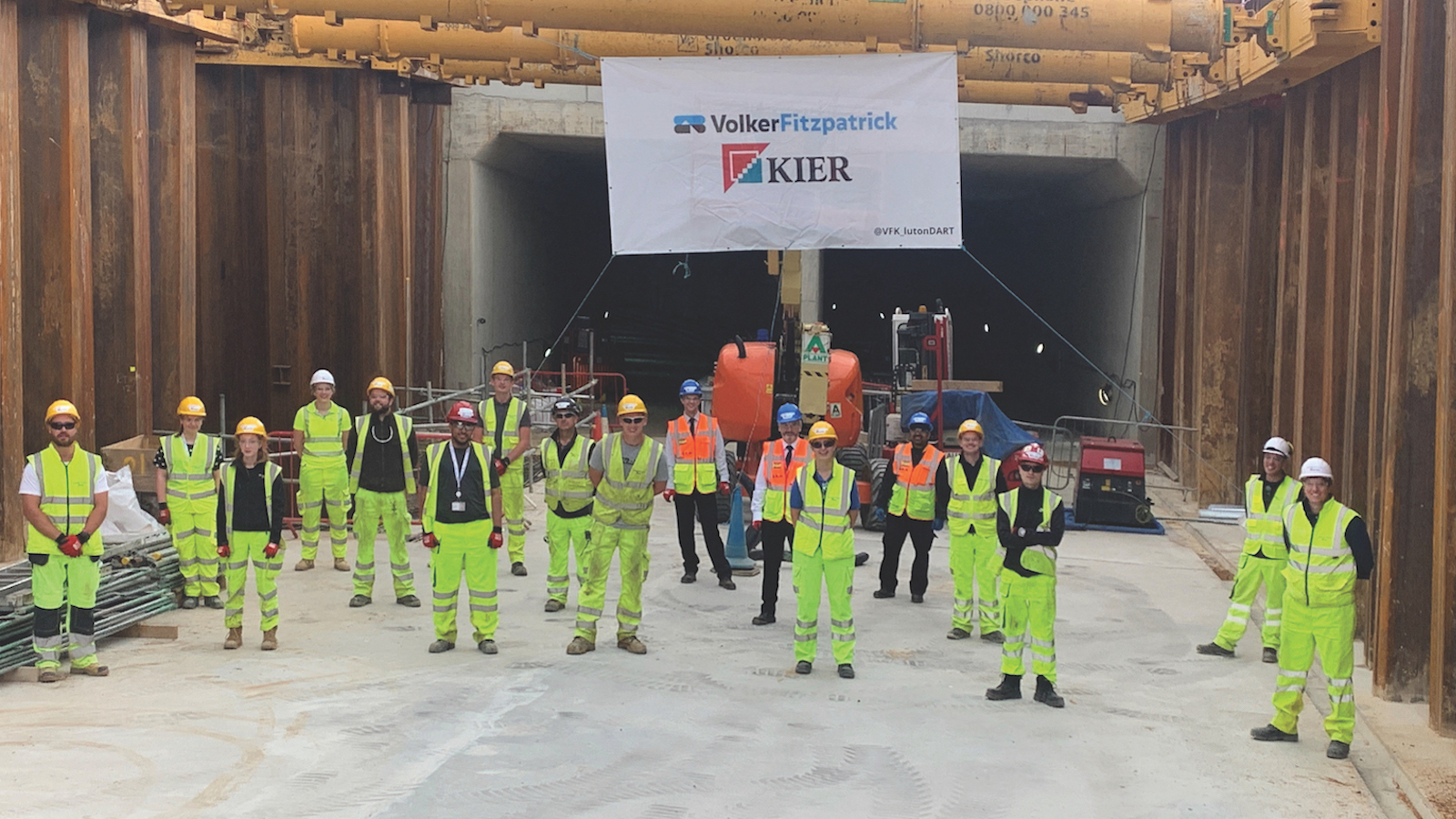
“The main focus for me has been good communication and creating a framework that gets the team working together. We have had a diverse and young team at Luton DART, keen to prove themselves, alongside some highly experienced foremen. It is the shared achievements of a number of these individuals that has created a level of teamwork that has overcome the many technical challenges.”
The project is scheduled to finish early in 2022. Once in service, the Luton DART will allow rail passengers alighting at the Parkway station to reach the airport in under four minutes, 24 hours a day.