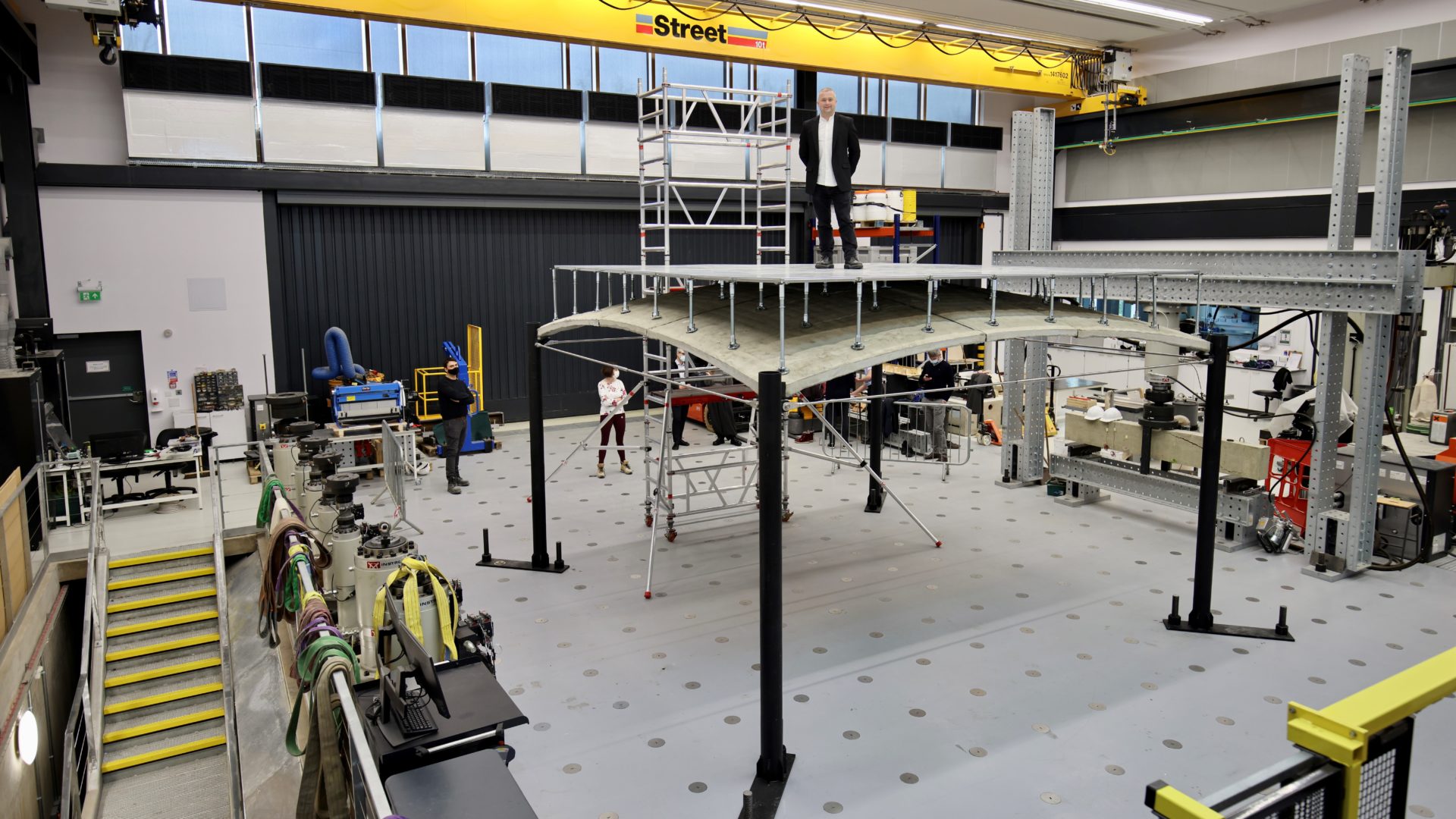
A new style of vaulted floor that cuts concrete usage by up to 75% could replace solid slab floors as construction moves towards net zero targets.
That’s according to researchers at the University of Bath, Cambridge and Dundee, who have unveiled a full-scale demonstration of a thin-shell floor. The 5m x 4.5m thin-shell structure has been built in the NRFIS laboratory of Cambridge University’s Civil Engineering Department.
The vault-shaped floor uses 60% less carbon in its construction than an equivalent flat slab that could carry the same load.
The floor has been created by the UKRI-funded ACORN (Automating Concrete Construction) research project, which Laing O’Rourke is also involved in.
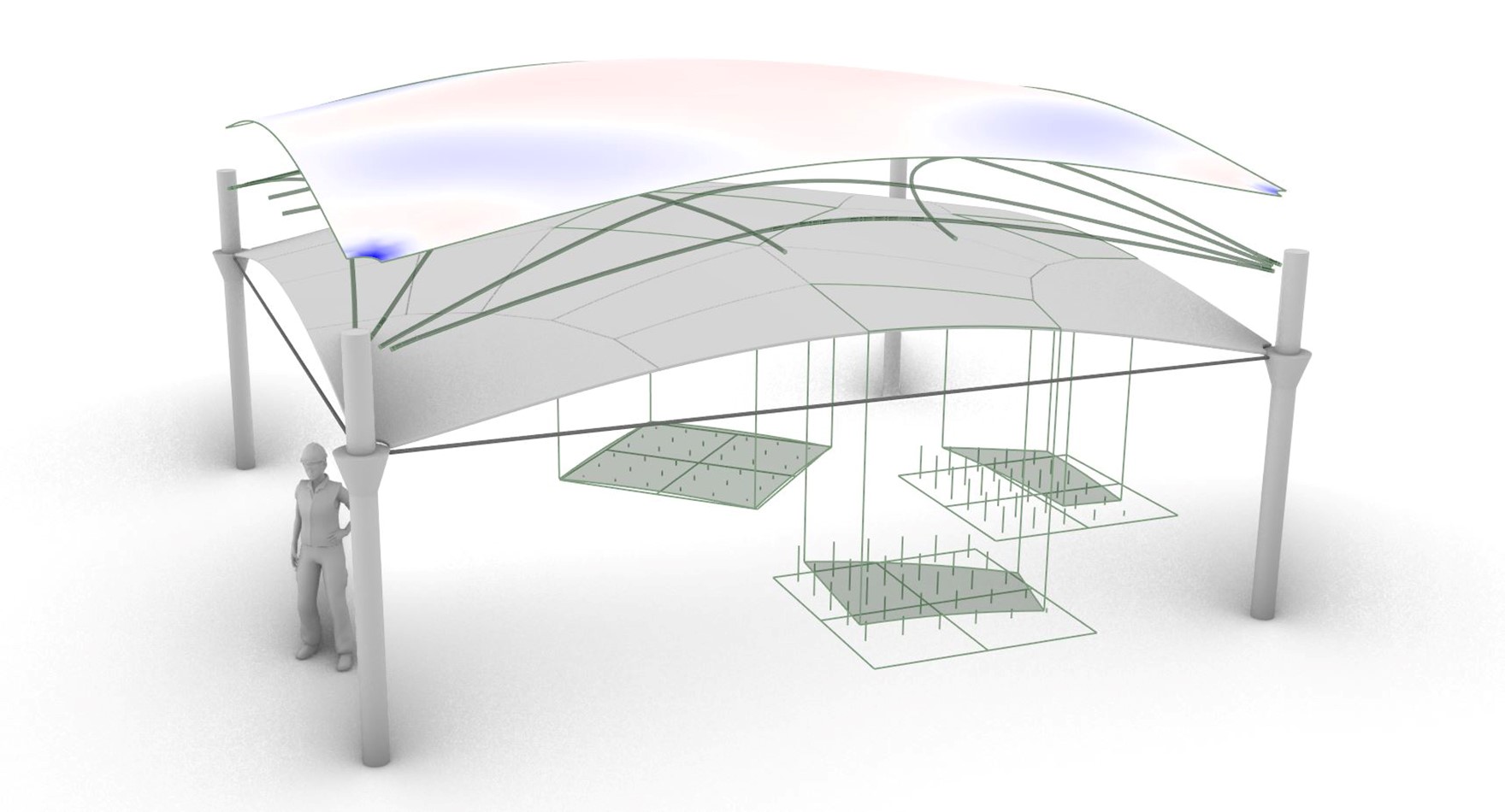
The innovative approach plays to concrete’s strength of resisting compression. Rather than being laid flat, where it requires steel reinforcement, the concrete is used only where it is needed to work in compression. The new shape cannot be made using traditional temporary formwork, so the ACORN team has developed an adaptable mould and a robotic concrete spraying system that can be used in an offsite factory.
The team has also developed software to optimise floors for a given building design, and control the automated manufacturing system to produce them.
The test floor has been manufactured in nine transportable pieces and is joined together with a connection system. The floor also incorporates reversible joins so that it can be disassembled and reused at the end of a building’s life. Each piece took half an hour to make and the whole floor took a week to assemble. Researchers say commercial versions manufactured offsite could be produced and assembled much more quickly.
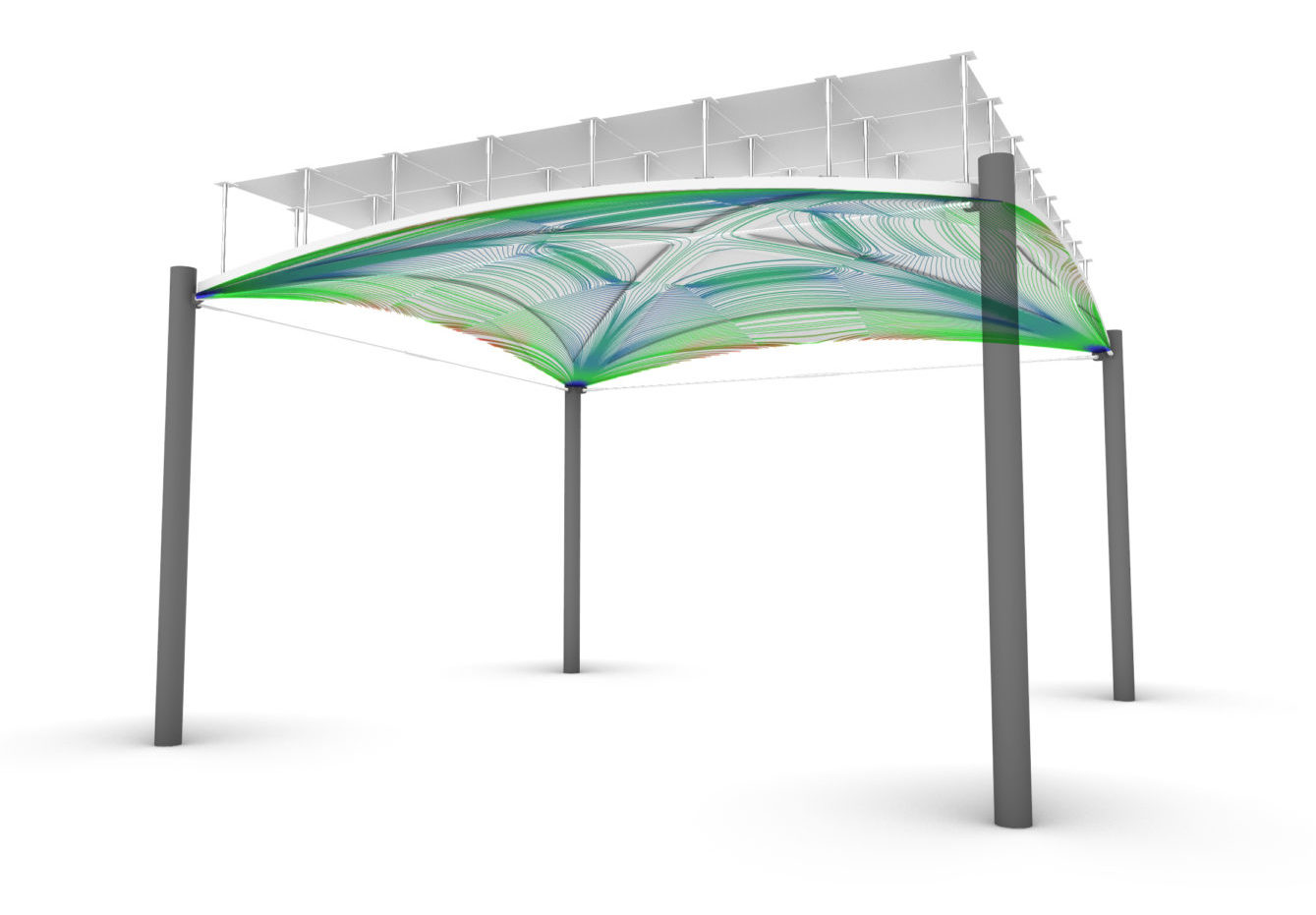
Dr Paul Shepherd, a reader in Bath University’s Department of Architecture & Civil Engineering and the principal investigator for ACORN, said: “Since concrete is the world’s most widely consumed material after water, and its production contributes more than 7% of global CO2 emissions, the easiest way for construction to begin its journey to net zero is to use less concrete. That has been the driving force behind this project, which we hope could make a major difference to the impact of construction.
“I just hope that one day soon this type of low-carbon automatically manufactured building becomes so widespread that people walk by without noticing.”
Adam Locke, programme leader of the Europe Hub Technology & Innovation at Laing O’Rourke, added: “The ACORN demonstrator is a very useful stepping stone in the progressive pathway to decarbonising our solutions and complements very well our own work in this area.”
ACORN has received funding from UK Research and Innovation under the ISCF Transforming Construction programme.
Comments
Comments are closed.
EDITED:
Looks good (harking back to Medieval Vaulted Ceilings in Cathedrals and the like), however given the fact that the over-all floor depth would be significantly increased, this would mean the over-all height of a building would also significantly increase (extra materials / labour for the extra height walls, and also Stairs, Service Risers etc.) – thereby eating into any savings which may be made by using this Vaulted Ceiling System.
brillaint – but the ‘old’ boys did this in brickwork – was involved in demolishing a warehouse circa 1850 where vaulted (not full arches) were used to lessen floor thickness, and they loaded it with materials 6 floors.
so glad the modern concrete has ‘caught’ up well done the the researchers exactly what our industry needs to carbon zero
Looks like an update on the Guastavino Arch (Catalan Vault) popular in the late 1800s in the US!
Vaulted ceilings, wow that’s certainly bringing floors/ ceilings up to date, I’m still researching for when brick vaulted roofs were first introduced and found this;- Amongst the earliest known examples of any form of vaulting is to be found in the neolithic village of Khirokitia on Cyprus. Dating from c. 6000 BCE, the circular buildings supported beehive shaped corbel domed vaults of unfired mud-bricks and also represent the first evidence for settlements with an upper floor.
Can computers and designers learn anything from that. Modern world!!!!!!!!!!
Good to see attempts at innovation but not viable for multi storey resi…!
Would very quickly lose a completely storey…
JC
I would suggest before we comment on whether any additional concrete in the column height would offset the concrete savings in the slab we would need the accurate dimensions and spans etc. The fact that this is being researched would suggest that there will be a significant benefit. Building loads will reduce, bespoke handling methods will be required but should be straightforward to develop. For me the challenge will be to develop a suitable system for underfloor M&E installation that can cope with curved substrates and be quick to install. It is feasible but will require a lot of design & supplier coordination.
While the design looks elegant, like so much stuff that gets sent out to the field to be built, the only way it can actually be done is in Auto Cad on paper
1) it could only be done as a precast element, you could not field fab this
2) all those steel attachment rods are punch points waiting to happen.
3) shipping and handling would be nearly impossible without massive losses
4) if it was managed to be built the ultimate future user would be very likely to destroy it by cutting a hole in the wrong place, or some other commonly done thing, done by some uninformed carpenter or plumber or electrician, that you can get away with in a more robust system.
I love this innovation, especially the ability to be ‘de-constructed’ and re-used. As an experienced building surveyor I have seen many bespoke engineered buildings all striving for environment excellence in their time. Through the life of the building I have seen highly engineered concepts be let down by future maintenance and tenant alterations that are applied to buildings without a knowledge of their underlying design principles. Has this been considered at all or is it the hope that this becomes so widespread that everyone will be so aware of it. Having seen what I have seen in my career, I could easily see that people cutting the support wires or core drilling large holes through through lightweight concrete deck – will it be able to withstand this type of treatment without disproportionate effect?