Martin McCabe explains what happened when the HSE paid a surprise visit to one of his sites during lockdown to inspect its coronavirus protection measures.
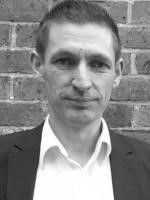
An unannounced visit from the Health and Safety Executive is never great news.
And that’s what happened on one of my projects last week.
I manage health and safety for HGH Groundworks and Civil Engineering. This sees me managing health and safety across the company on multiple projects. Our work has always been high risk. Deep excavations, work in confined spaces and plant operations are the norm. It’s hard work and it brings many hazards with it.
Then came coronavirus. The spectre of the global pandemic lurked over us. As I visited my sites it came up in conversation more and more. In a few days I observed some people go from nonchalance to panic. Others remained indifferent until the day of lockdown. The situation needed leadership. And effective communication was the key.
The starting point was to be honest with people. There was a lot we didn’t know. We were monitoring the news and government advice. As a subcontractor on the majority of our projects, we were in constant dialogue with our clients. We had ordered extra PPE and hand sanitiser in January but it still hadn’t arrived. These were the facts. We gave everyone the big picture.
Keeping people informed
This is something we are terrible at in construction. We’ve all heard about the golden thread of information for project quality. The same applies for keeping safe during a crisis. We need to give our people the big picture rather than a tiny snapshot. We shouldn’t treat our people like they’re on Project Pigeon.
Project Pigeon was a secret programme during World War II. The US Navy needed a weapon able to defeat the German Bismarck battleships. They had the missiles. But the guidance systems were too big and too primitive to be much use.
Burrhus Frederic Skinner was a Harvard professor of psychology. He reckoned he could train pigeons to guide the missiles. He’d train them to tap a target on a screen with their beaks, controlling the direction of the missile. His tests were successful but abandoned in favour of radar, the new technology of the day.
And the construction industry can be like that. Treating our people like pigeons tapping at a screen to stay on target. Not giving them the full picture. Expecting them to stay the course like pigeons guiding a missile. This is not the way.
Daily monitoring
Working with one of our clients, we developed a strategy for one site that we would end up using everywhere. We started daily monitoring of everyone’s temperature along with a symptoms check. We brought in social distancing measures – and we enforced them. Cleanliness of welfare was prioritised. We moved office staff to working from home. We enforced single vehicle use for travel to and from work.
One by one our clients began shutting sites. The Prime Minister’s lockdown announcement came on 23 March. Against the odds, we had four projects remain open throughout. Each site was an open space with work that allowed for social distancing. Those next few weeks were hard but we got through it. It was all down to the professionalism of the staff and their ability to adapt.
Our closed projects gradually began to reopen. We sent small teams to site to set out collective protective measures for each job. New walkways, signs, hand washing stations, one-way systems. Our experience of keeping four sites open throughout meant we were well prepared. We had already adjusted to the ‘new normal’.
HSE visit
The HSE visited one of our sites, on which we are a subcontractor. We have by far the most prominent presence on site. The site was one that had shut down and recently reopened. We had applied everything we’d put in place elsewhere.
The HSE’s visit was unannounced. The inspectors were inducted and went through the site’s coronavirus symptoms checks. They interviewed some of our staff. They asked what our covid-19 checks were. They enquired about our travel arrangements. They looked at our method statements and risk assessments. And they reviewed our records of symptom checks and re-inductions. Interestingly, they were still keen to focus on plant use and maintenance. They checked plant operator competence and inspection records. Even in this new world, some things will never change.
We received no actions from the visit. It’s down to the dedication of each member of the team. Strong supervision has been crucial. This experience has only reinforced my view that site supervisors are the key to getting things right. They’re the people who drive the culture and behaviours on site. When you have supervisors who lead by example, it gives you the best chance of success.
Martin McCabe is head of safety, health, environment and quality at HGH Groundworks & Civil Engineering, and a member of the CIOB’s education, qualification, standards and practice board.
Comments
Comments are closed.
Excellent, I agree that supervisors are the key to safety, quality control and safety culture but unfortunately a lot are not trained in these areas
I was at a housing site yesterday. The Site run by Vistry Homes was in my opinion, very well organised for COVID-19 Compliance. I was very impressed at the measures they had taken to keep all staff safe as well as out the box measures. Well done Vistry Homes, Cawston.
I am retired but volunteer at our local scheduled monument in a health and safety capacity. This article will be very useful in helping to get our 100+ volunteers to understand why we are asking them to temperature test, cover up and work in an unusual manner, especially as most are over 60 and are often face to face with the public.