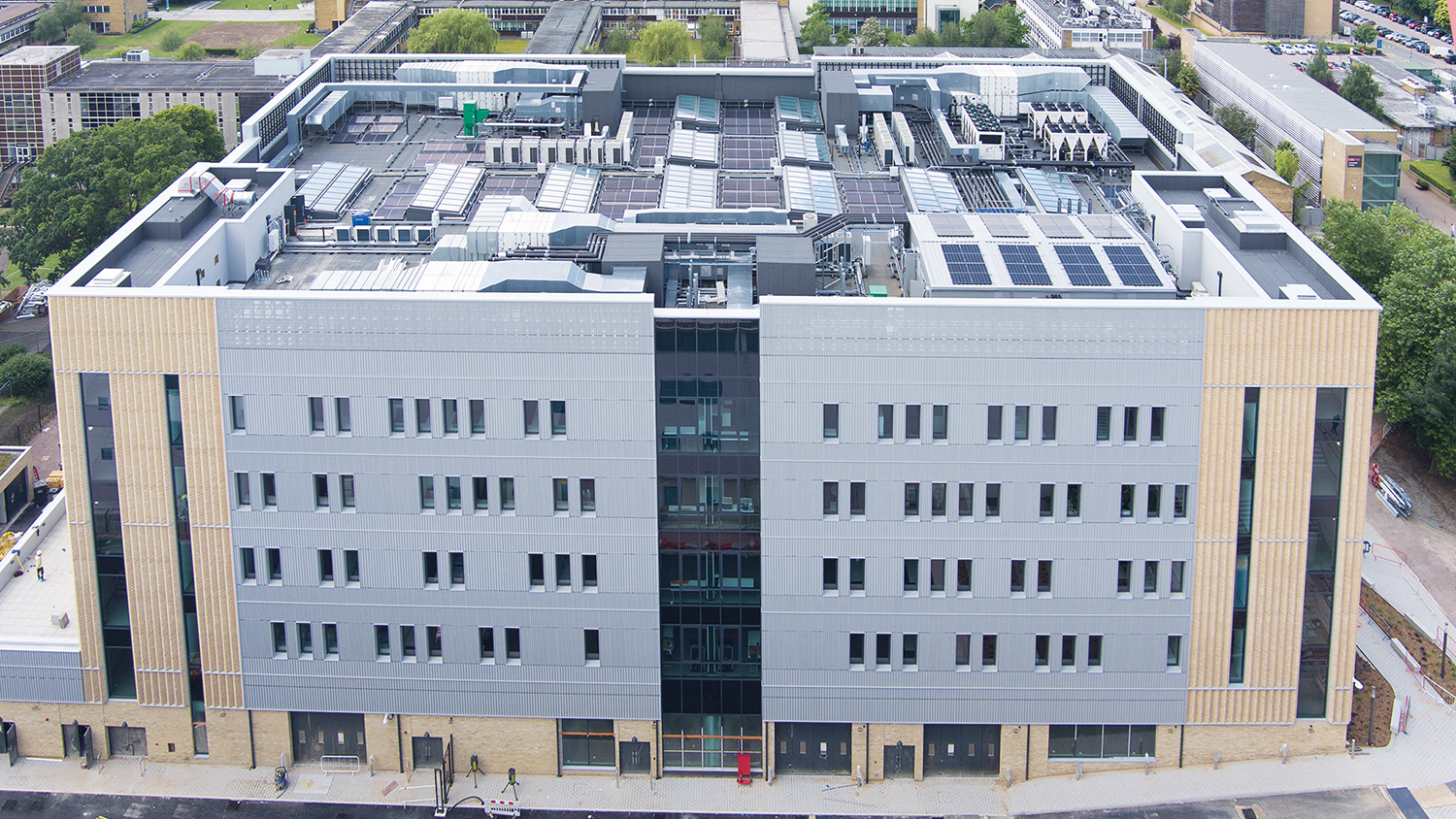
With quality and building safety top of the industry agenda, Adam Sanford FCIOB explains the benefits of collaborative procurement models
With the Building Safety Act placing greater responsibilities upon designers to ensure building works comply with regulations, it has never been more important to get the budget right from the outset.
A single-stage procurement model with fixed outcomes alongside squeezed budgets puts the original design intent at risk and can force use of poorer-quality materials, risking both quality and safety.
To achieve true collaboration between public and private sector bodies, and ensure building safety and quality, client organisations must forge deeper relationships via a two-stage procurement model.
This opens lines of communication and due to the pre-qualification stage, reduces the impact of “competitive tension” on specification and materials decisions, and encourages better understanding of the commercial realities of delivering major projects.
Also, at a time of tightened public budgets to the limit, partnering with industry to facilitate innovation is a key tool in unlocking public value.
Quality outcomes
Two-stage open book gives the opportunity to tap directly into the supply chain when making early-stage choices in construction methodology and materials, identifying and mitigating risks in both the design and the cost plan, at a much earlier stage.
This approach can avoid costly reworks later in the process. Not only scope reduction and substitution for poorer quality materials, but amendments to planning consents and utilities alterations.
Projects can all too often get stuck in a ‘doom loop’ of reworks and cost inflation, which can lead teams to make cuts to scope to make it to site. The safety implications of rushing value engineering are well known. But, behind every failed construction, is a design team that were confident in their choices at the time.
Useful guidance
- Southern Construction Framework toolkits, including on Biodiversity Net Gain, carbon, health and safety, are available for free download.
- Southern Construction Framework’s Carbon Toolkit includes a benchmarking tool which, in collaboration with the National Association of Construction Frameworks, collates carbon KPI data to capture a detailed national picture of public sector projects.
In two-stage procurement, during the pre-construction phase all areas of risk are pointed out to you, which allows you to decide the best way forward to ensure quality. It means you don’t suddenly decide later to have cheaper cladding material, or a flimsy roof finish, just because it fits into your budget.
Morgan Sindall showcase
The University of Hertfordshire’s Spectra building, recently completed, showcases the importance of clients and contractors collaborating via a two-stage open book process, to reduce risk early in the project, which allowed the team to focus on quality and safety.
Emma Curtis, area director at Morgan Sindall who oversaw the project, says that “the biggest benefit of two-stage procurement during this project was that it allowed us to bring in our supply chain early. This enabled us to take the time to source materials that had the appropriate fire rating certification.”
She adds: “It also meant that we could spend time liaising with our fire consultant and the building control officer to make sure that they were comfortable with the designs and the materials that we were putting forward.”
The two-stage open book process allowed Morgan Sindall to work with the university to embed sustainability, a key focus of higher education institutions amid net-zero targets.
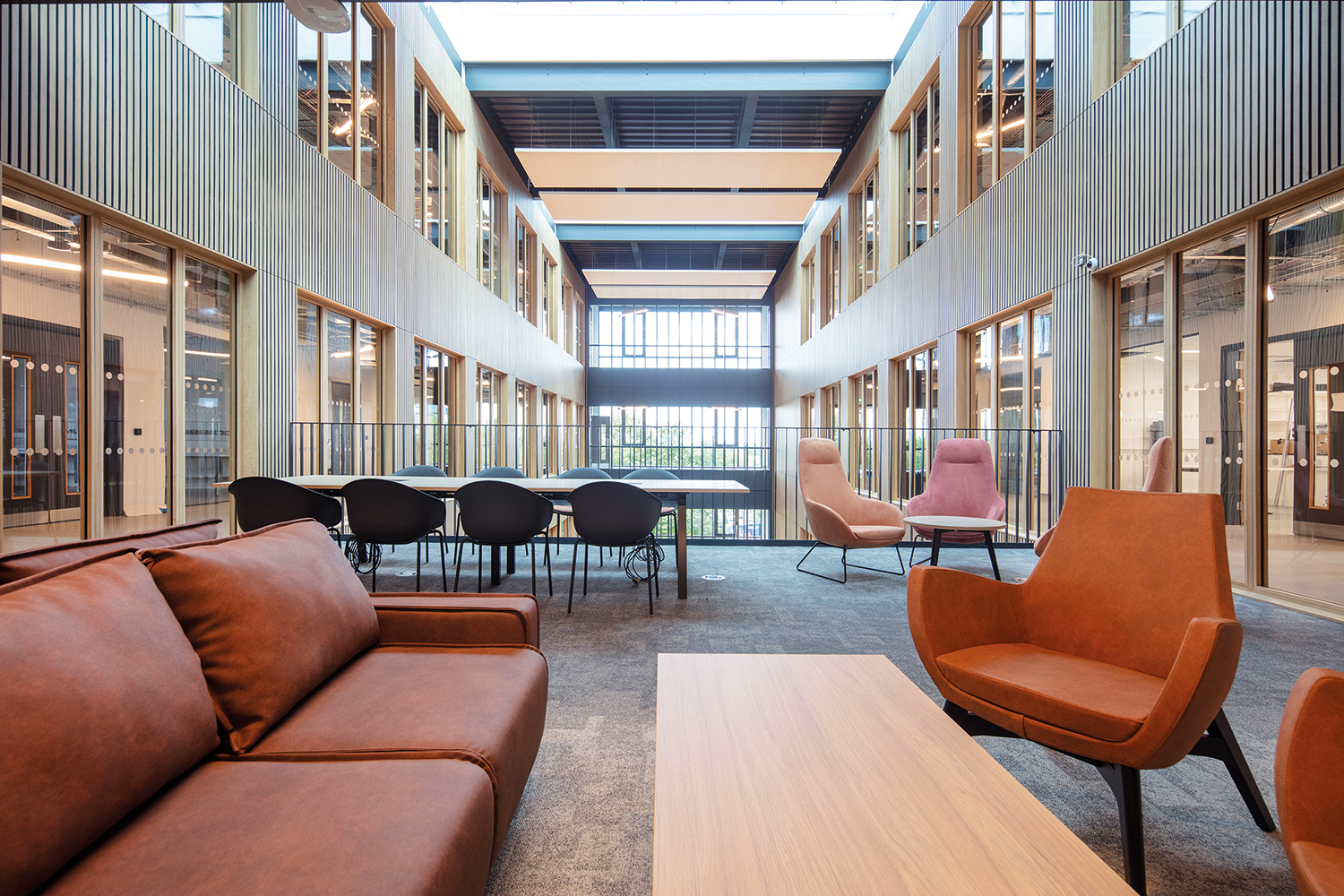
The contractor worked with its supply chain to source sustainable materials, using timber for staircases as opposed to steel, and worked with the client team on the electrical side to ensure longevity in terms of maintenance, and installed motion sensors that switch off when not in use.
With buildings being long-term assets and net zero targets currently at the forefront of clients’ minds, it has never been more important to understand a building’s operational use from the outset.
Q&A: Two-stage procurement
What happens in the first stage?
The mini-competition stage is where bidders compete for the contract based on their capacity, capability, stability, experience and strengths of their supply chain. This stage acts as an opportunity for the client to review the approaches of bidding contractors and compare their rates for profit, fees, overheads and other additional costs associated with the project.
What happens in the second stage?
The contractor and their key supply chain members are engaged as early as possible. They become part of the pre-construction team with your key stakeholders, professional advisors and supply chain members. The team will work to an agreed objective, cost and programme.
They will fully scope the project and assess risks early on. This reduces any chance of unforeseen issues occurring later in the project that impact costs and deadlines
How does using a framework enhance this process?
A well-managed framework will set out a process by which suppliers can work together to better understand the labour and materials supply markets and share this information with the framework user base. This can then feed into pre-procurement market engagements and early project planning.
Frameworks can facilitate much-needed collaboration in the industry through added-value workstreams such as the Southern Construction Framework carbon, social value, and health and safety working groups. Southern Construction Framework makes market information freely available to the industry via its quarterly market intelligence reporting.
Adam Sanford FCIOB is operations lead at Southern Construction Framework.