Developments in multilayer pipe mean it is now increasingly used for applications such as heating systems and drinking water pipework. Errolene Stanbridge discusses its growth in popularity
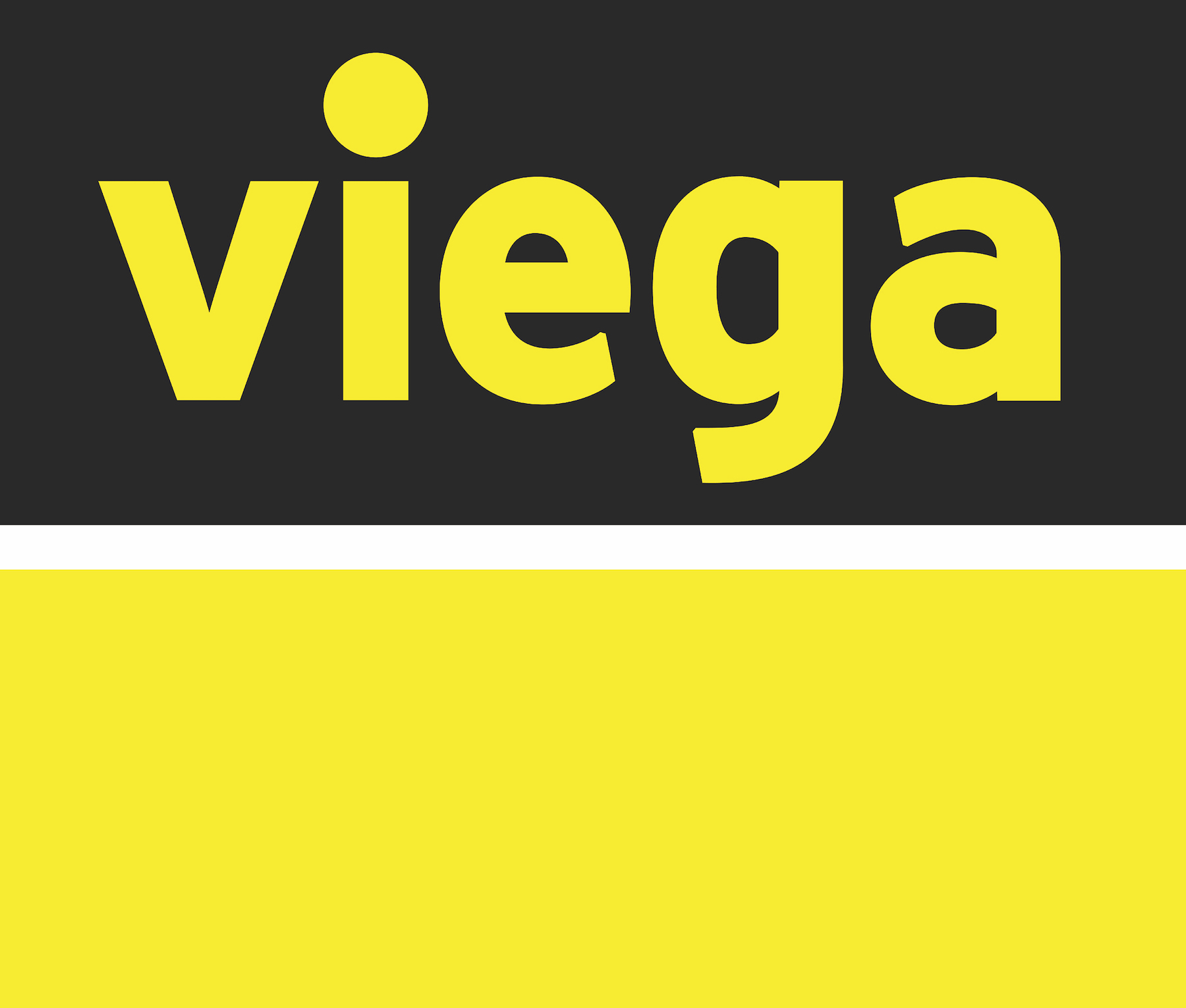
While copper and stainless steel are the traditional go-to materials for many building service systems, the properties of multilayer pipe can provide additional benefits such as a reduced number of fittings, minimal pressure loss and the ability to work in narrow areas.
Multilayer pipe consists of inner and outer layers of thermally resistant cross-linked polyethylene (PEX) with a layer of aluminium between, which delivers durability and retains the shape. The inner and outer layers protect the metal from corrosion. Similar to copper, multilayer pipe has a variety of applications including heating systems, hot and cold-water pipework and drinking water.
As building size increases, the complex geometry to which the pipes must conform increases as well – this can be a challenge when specifying piping systems. One benefit of multilayer piping is that it can be easily shaped using hand-held tools, without the risk of buckling.
This means that pipes can be adapted easily to the needs of the building without the need for cutting and joining them together. Additionally, multilayer pipe can be supplied in lengths of up to 200m and can be used directly off the coil – the installer simply needs to cut the length of pipe that is required.
Being able to bend the pipes is an important consideration, as the larger the number of connectors needed for a piping system, the greater the impact on the performance of the building services. Fittings and pipe connectors all contribute to the overall friction of the pipework and cause a reduction in flow and water pressure.
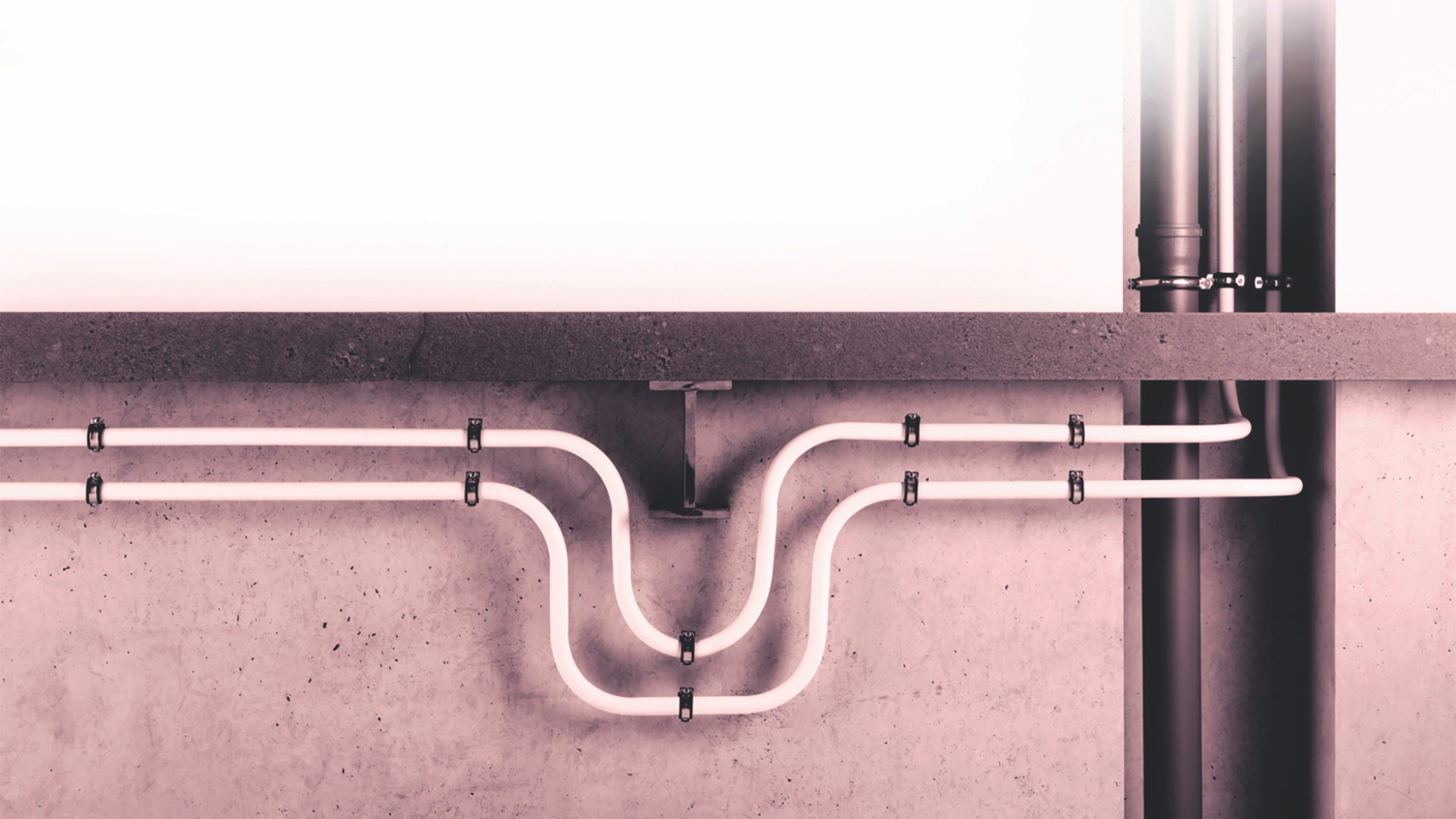
The resistance added by each component can be measured as a pressure loss coefficient, also known as the zeta value. The total interior surface area of the pipe also contributes to the friction within the system, so longer pipe runs will increase the pressure loss. The selection of both pipe and connectors with low zeta values will help optimise the performance of the system.
“One benefit of multilayer piping is that it can be easily shaped using hand-held tools, without the risk of buckling”
Viega’s Smartpress system, for example, can reduce pressure loss by over 80% compared to standard designs, due to its very low zeta values. A standard design brass degree elbow connector with a zeta value of 17 will result in a pressure loss of 340mbar at a flow rate of 2m/s, whereas Viega Smartpress offers a flow-optimised alternative with a zeta value as low as 2.7, resulting in a pressure loss of only 54mbar at the same flow rate.
In addition, the Viega Smartpress system replaces the traditional O-ring construction with a robust and durable polyphenylsulfone (PPSU) support structure that also simplifies the installation process. This provides up to a 30% time saving on site when compared with alternative systems.
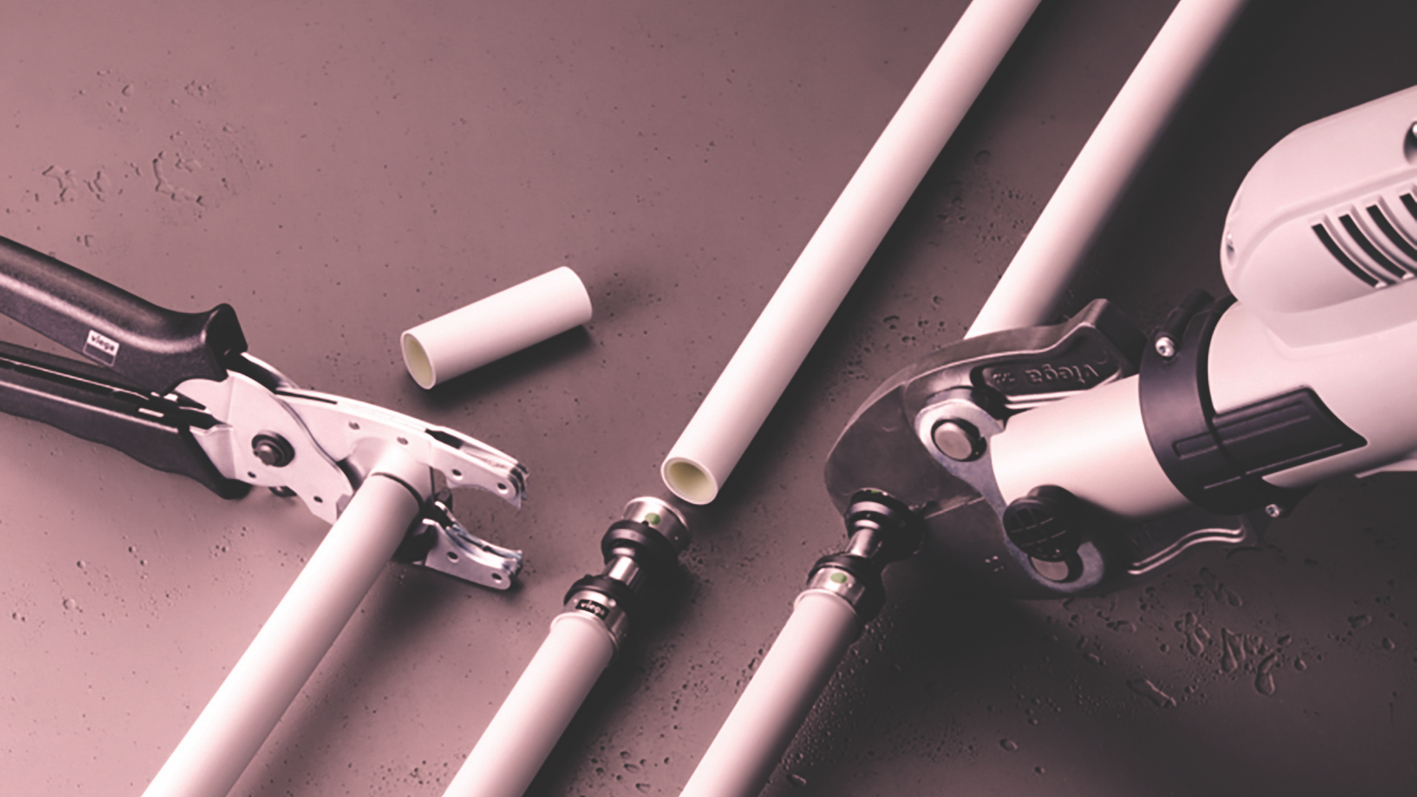
To ensure reliability, Viega’s Smartpress range features a solution to highlight any connections that may have been inadvertently left unpressed during installation.
Some press connection products will appear secure by not leaking at a nominal test pressure, only to fail when the system is operational, but Viega’s Smartpress products incorporate a flowpath channel called the SC-Contur, meaning that unpressed connections are guaranteed to leak during a test; wet pressure tests use pressures anywhere between 1.0 and 6.5 bar, and dry tests between 22mbar and 3.0bar.
The Viega Smartpress system is manufactured from high quality stainless steel, ensuring a reliable and durable system – as a lower quality multilayer pipe can buckle under pressure, causing costly remedial work later on. In addition, it is tested and approved for use within drinking water applications, to certify that it does not contaminate the water.
For further information about Viega’s range of solutions, including the Viega Smartpress system, visit: www.viega.co.uk.
Errolene Stanbridge is a technical sales manager at Viega.
This article has been produced in partnership with Viega.