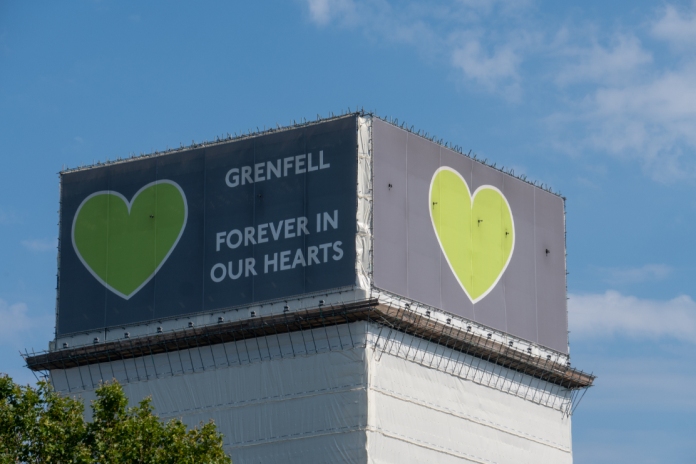
The manufacturers of the combustible cladding and insulation used on Grenfell Tower “exploited ignorance” around terms such as “class 0” and “limited combustibility” within the construction industry for their own commercial gain, the Grenfell Tower Inquiry has heard.
Adrian Williamson QC, representing the bereaved and survivors of the Grenfell Tower disaster, yesterday (9 November) set out in an opening statement at the start of module 2 of the Inquiry’s second phase what believed went wrong with the production, marketing, testing and certification of the products used on the building.
Williamson said: “This reveals an industry in which Arconic, Celotex and Kingspan were content to push hazardous products into the marketplace and sought to market them dishonestly. These products should have been safe, they should have been tested and certified rigorously, and they should have been marketed in an honest and transparent fashion. None of that happened. The testing and certifying bodies, such as the BRE and the BBA, were quite happy to go along with this process.”
Williamson called the marketplace in which the products were marketed “a place of astounding ignorance”, with many of those involved not seeming “to know or care what was meant by terms such as ‘limited combustibility’ or ‘class 0’.”
He said: “The manufacturers were of course only too happy to exploit this ignorance for their own commercial gain. At all times they concentrated on the route to market, not the route to safety.”
Williamson detailed how Arconic, which manufactured the Reynobond PE cassette cladding product, was “well aware” as early as 2004 that it had failed a French Centre Scientifique et Technique du Bâtiment (CSTB) test.
He also noted that two years later, Kingspan began to market its K15 phenolic insulation product, despite a 2008 BRE test that had to be extinguished early because it “was endangering setting fire to the laboratory”. Williamson went on that Kingspan “managed to persuade” the LABC to issue a document signifying its approval of K15 Kooltherm in March 2008. “What mattered was not safe products or thorough certification, but getting ahead of their rivals in the marketplace,” Williamson said.
‘Misleading’ information
Williamson also claimed that Arconic “misled” the British Board of Agrément (BBA) when it sought to obtain certification for its Reynobond product by providing only a test report for the riveted version of the product, which obtained Euro class B in tests, but failing to disclose the cassette system test report.
An internal Arconic email sent in March 2010 by France-based Arconic technical manager Claude Wehrle noted: “Reynobond PE in cassette form doesn’t obtain level ’B’ either! Having said that, this shortfall in relation to this standard is something that we have to keep as VERY CONFIDENTIAL!!!!”
Wehrle is one four current or former Arconic employees who has so far refused to appear before the Grenfell Tower Inquiry, citing the French Blocking Statute, a French law which seeks to prevent employees of French firms making disclosures to foreign courts.
Williamson also highlighted a July 2009 email Wehrle sent to management regarding a high-rise fire that had occurred in Bucharest where flames had spread along the façade made up of ACM PE panels. Wehrle said: “Here are some pictures to show you how dangerous PE can be when it comes to architecture.” Williamson said the email showed that Arconic was already aware that its product was dangerous.
Celotex
Turning to Celotex, Williamson detailed how Celotex saw its first BS414 test for its FR5000 product fail, after it was terminated early due to excessive flaming and fire spread. In May 2014, Celotex secured a pass on a second BS 8414 test after placing a 6mm magnesium oxide board behind the cladding, used in conjunction with a 12mm thick layer of the cladding.
Williamson said that a Celotex PowerPoint presentation entitled “above 18 metres” produced in May 2014 showed the results of the tests, together with what was said to be market research which had been carried out, “showing that nobody understood the test requirements”.
And he highlighted Celotex’s datasheet for the Celotex RS5000, which recorded that this was the first PIR insulation board to successfully test to 8414, to meet the criteria set out in BR 135, and was therefore acceptable for use in buildings above 18 metres, as well as having “class 0 performance throughout the entire product”.
William said: “There was no suggestion in this document of the failed test or of any of the other uncertainties of which Celotex were well aware. Moreover, the assertion of class fire performance throughout the entire product was itself misleading, as it was not class 0 throughout, since class 0 only related to the spread of fire on the surface. Furthermore, the standard for insulation in a building above 18 metres was higher than class 0; it was limited combustibility. Celotex were well aware of the confusion within the industry between class 0 and limited combustibility, and used it to their advantage. This was consistent with the approach which Celotex took to the market in general, and in their dealings with Harley relating to Grenfell in particular.”
Arconic, Kingspan and Celotex all deny any wrongdoing.
Testing and certification
Williamson said there would need to be an investigation into the “toxic and incestuous culture and practices” of the industry. He asked: “How did it come about that unsafe products were manufactured, marketed and sold? How did the testing and certifying bodies allow this to happen?”
He accused the Building Research Establishment (BRE) and the BBA of failing to discharge their responsibilities adequately. He said: “They were far too close to their customers. Testing was inadequate and certification haphazard. It is not as if they were unaware of the risks. Indeed, in May 2013, at a crucial point in the development of the Grenfell design, the BRE circulated a newsletter with the headline: ‘The latest high profile fire in the UAE has reaffirmed the need for properly approved, installed and maintained cladding systems in high-rise buildings.’ By their failures, the testing and certification bodies contributed significantly to the Grenfell disaster.”
He explained how, in January 2008, the BBA issued its certificate for Reynobond ACM but that the BBA “did not consider the fact that the tests were carried out on two types of cores used in the ACM cladding and their differing smoke production when reacting with fire”. He also asserted that the BBA also failed to identify whether the fixing system used was riveted or cassette.
Meanwhile, he accused Arconic of breaching its contractual obligation to notify the BBA immediately of any new or additional information concerning its product or its suitability. The Reynobond PE cassette panel was re-tested under the European Standard, achieving class E in 2011, 2014 and 2015, but none of the test results were disclosed to the BBA, Williamson said. In January 2014, riveted Reynobond PE was also classified Euro class E and then consistently classified Euro class C but none of those results were disclosed to the BBA either. Williamson said: “Thus, from January 2014, the BBA certificate statement that Reynobond PE achieved Euro class B was untrue for both cassette and riveted products.”
When it came to the BBA, Sam Stein QC, also acting for the bereaved and survivors of the Grenfell Tower disaster said: “We suggest that the BBA as an organisation was beset by fundamental issues. Those issues compromised its ability to discharge its safety-critical function. Those issues included a lack of independence arising from a fear of losing business, competing commercial interests, and a drive for cost efficiency over accuracy.
“The BBA also permitted Arconic an extraordinary degree of control over the certification process. Mr Albon, the chief scientific officer of the BBA, confirms Arconic requested the BBA to consider the riveted and cassette versions as different fixing systems rather than as separate products. It appears the BBA simply acceded to this, so rather than imposing its requirements on Arconic, the BBA allowed Arconic to dictate that riveted and cassette versions of the cladding system should be considered different fixing systems rather than separate products. Any form of regulatory control should include updating and checks on currency of testing and certificates, and once the BBA certificate was issued, it was then the BBA’s duty to regularly review the subject of the certificate to ensure it remained regulation compliant.”
BRE ‘not involved’ in testing Grenfell systems
But Samantha Leek QC, counsel for the BRE, said in her opening statement that the testing house had “no involvement” in assessing the safety of cladding systems installed on the tower.
Leek said: “BRE is not a regulator and does not fulfil the function of a building control authority. It has no mandate, role or authority to monitor what manufacturers and suppliers do with their test and classification reports, and has no oversight as to how they are used to fulfil their obligations under Building Regulations. BRE’s function is that of a test house; in short, to burn systems and products and assess how they perform.”
She added that after the disaster, BRE provided technical support to the Metropolitan Police Service investigation into the fire, to help ascertain how the fire developed and spread in the way that it did. She said: “BRE’s assistance established that the two cladding systems on Grenfell Tower, one incorporating Celotex RS5000 and one incorporating Kingspan K15 insulation, in combination with polyethylene-cored aluminium composite material, fail against BR 135. It was shown that, had any of the two companies involved with the manufacture, supply and use of those systems engaged a test house, it is highly unlikely that the fatal fire would have spread as it did.”
BBA emphasises contractual relationship with certificate holders
In its opening statement, given on 5 November by counsel David Sawtell, the BBA said it has “agitated for a full adoption of the Hackitt Report’s findings, which it enthusiastically endorses”.
Sawtell said: “A BBA certificate…affords confidence to a specifier or designer as to the assertions made by a product’s manufacturer about their product’s properties. A BBA certificate provides a summary of the information necessary to make a decision on an individual application. But a BBA certificate must be read in its entirety. They are intended to be technically robust but also concise.”
He added: “The BBA’s relationship with certificate holders is contractual. A certificate is based on the documentary material that is provided by the supplier, and the applicant certificate holder pays a fee to the BBA for initial assessment and, if appropriate, certification and subsequent inspections. Pursuant to its contract, the supplier has obligations to make disclosure of any testing that has been carried out. Any changes to the composition of the material also have to be reported under the contract by the manufacturer. The effectiveness of the certification process is therefore based on certificate holders observing the terms of their certification contract in good faith…It is particularly important that manufacturers disclose to the BBA all test results and other information that may be relevant to the assessment of the product.”
Rydon: ‘Arconic knew Reynobond was dangerous’
Also giving its opening statement yesterday (9 November) was Rydon, whose barrister Marcus Taverner QC argued that Arconic knew its Reynobond PE 55 product was dangerous.
Taverner said: “Certain themes have been developed by Arconic in the course of this Inquiry to the effect that Arconic were mere manufacturers of a product, but it was up to others to make sure that its RB 55 PE or any other PE product was lawfully and safely used. As a result of this and in any event, says Arconic, it did not need to know, and indeed knew little or nothing, of the relevant regulations which governed or restricted its use…We submit that Arconic’s position is simply not borne out by the facts and is indeed insensible.
“Arconic had dedicated personnel responsible for ensuring the safety of their products, understanding and keeping up with national and international regulations, as well as individuals charged with overseeing independent testing and certification of their products.
“Arconic concluded well before and repeatedly by the time of the sale of RB PE 55 for use at Grenfell that it was so highly dangerous that it should not be used in what it called architecture, certainly not on resident tower blocks over 18 metres, and most definitely not in its cassette form. Arconic discussed these matters internally right up to the time of the fire in June 2017. Secondly, internal documents establish that Arconic had concluded that regulations precluded the use of RB PE 55 in many jurisdictions, certainly at any height above 18 metres in residential tower blocks. As to the UK, the continued opacity of the UK regulations were such that Arconic viewed that they could be ‘worked with’, to use Arconic’s own words, to allow it to market and sell for use in the above 18-metre UK market what it knew to be dangerous PE.”
The Inquiry continues.
Comments
Comments are closed.
Fascinating account of this aspect of the Grenfell Investigation. The certifying bodies were allegedly “To close to their customers”
Makes you wonder if this is the case with other certifying bodies or individuals who have the power to certify on behalf of a certifying body.
It also raises a number of questions regarding the initial and ongoing training of design professionals in terms of material science.
Does EU law not overrule French law in the case of Arconic’s refusal to attend the inquiry on a tragedy that happened when the UK was still in the EU. Even though we have now officially left the EU should EU law still apply for when we were members? Surely it was not just the UK that had to comply with EU law or is EU law not relevant to a tragedy like Grenfell?
Very interesting and as is the case for the building control market, the move to commercialise testing and regulation in our industry seems to have gone to far. manufactures are often the most powerful players with project teams and contractors working on ever decreasing budgets and margins.
I was a building products manager in 1984 when Alcan supplied aluminium bonded cladding to the Falkland Islands.
The relative flammability of the foams was well known even then
Grenfell has confirmed that construction materials’ flammability affects every building’s occupants, so the confusing jargon of classifications of flammability, combustibility and surface spread should be replaced with simple language that any layperson can understand. Here we see the evidence: obfuscation leads to death.
It does make you question whether, as a professional, you want to be involved in specifying anything…….
We can act in good faith and be diligent and yet if something goes wrong everyone is pointing fingers. You can always be more careful or check one more thing, or do one more inspection.
As an aside, no doubt other people noticed on the footage from Grenfell that tenants had changed their front doors and all were different. Some had glazing, some solid. I doubt hardly any were properly fitted fire doors. Even resolving that would have been a nightmare. Who pays? No one wants to until there is an incident
With traditional materials we can rely on accumulated experience and construction textbooks. This is not possible with new and developing products where we are largely dependent on the manufacturers’ fitting instructions and published technical information.
To obtain detail of fire test reports which underlie published certificates takes determination and persistence. This makes carrying out due diligence a daunting task. This is particularly so as the fire tests rarely replicate the proposed uses of the tested products and therefore are of dubious applicability.
I remember back in the days of the GLC, all London Boroughs had vastly experienced in-house “divisional surveyors” and engineers that looked after the housing stock. At a time when external wall insulation products began to be affixed to the outside of multiple storey blocks, I remember on one occasion doing a pitch to one of them and proposed the use of an SDFRA grade polystyrene insulation behind a traditional sand:cement render. I assured him that the (will not be named here!) manufacturer had tested the insulation and it achieved a “will not add to fire” type classification. The 1st time I spoke to him about this system he laughed; the 2nd time I am sure he wanted to throw me out of the building. He did excuse my lack of age and experience however, BUT said “if you want to insulate the outside of my high rise buildings then we can discuss this, but using a system that is certified as non-combustible and no thermoplastic insulants. We went away, and came back with a Swedish system, with a track record, a BBA certificate, a full-scale fire test having been conducted at the Warrington FRC, using (as the insulant) ………Rockwool. It limits the spread of fire and is still relatively stable” at 1100* centigrade – one of the reasons it is used in fire barriers. I know for a fact that there was a fire in one of the flats years after the cladding was completed, with no damage to the cladding
Ask any tradesperson on site with a reasonable level of experience how flammable the insulation materials are, extruded/expanded/PIR/PUR, they may not know the name or type but I am sure will say that they all burn when you show them a piece. Funny how the bloke with the broom knows more than the specifier, maybe I over simplify it but this fire was an example of ignorance, cost cutting and profit making that resulted in the loss of so many lives.
I come across these sorts of problems daily in my inspection of building works as an expert witness across all aspects of finished works, Structural, fire, water, electrics etc where checks and controls are sadly lacking and its all too easy for contractors to tick the boxes take the money and run!! When I tried to raise my concerns following Grenfell I was told the government shutters had already come down!!
Malcolm Birchwood FIOC MJMA
The most telling remark is the one from Mr Williamson QC that the market was “a place of astounding ignorance” where no one knew or cared about the meaning of core technical terms. Spot on. That has been a common conclusion in my career developing and explaining fire-resistant glass and glazing over many years. It is still the same 8 yrs after I retired, whilst still involved in broader fire safety product-related matters. Technical knowledge relating to products is astoundingly poor.
Architectural design and building technology requires a high level of technical understanding. It isn’t there at the level that is necessary.
Having worked for many years specifying products, I found Part B of the Building Regs, dealing with fire, was a shambles. It had been patched up and added to over the years, and it was very difficult without hours of study to make out exactly what was required. It also referred to numerous British Standards, which cost hundreds of pounds each, and are beyond the budget of smaller enterprises, who rely on on historical knowledge and manufacturers assurances.
I hope this tragedy will lead to properly funded regulations which are easy for everyone to understand.