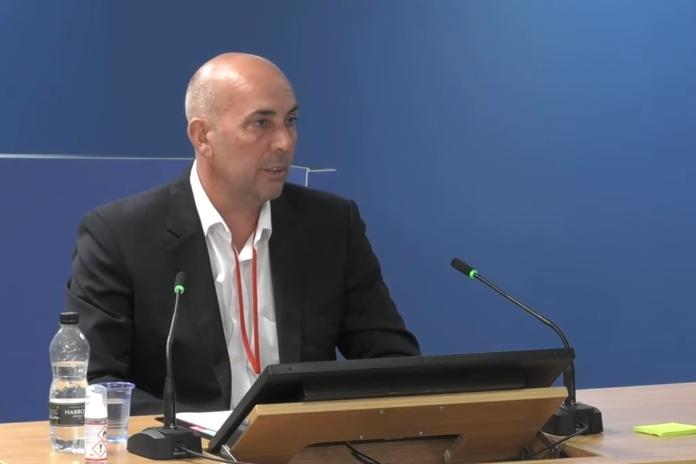
The subcontractor working for Harley Curtain Wall to install cladding and insulation to Grenfell Tower did not receive any guidance on how to fit cavity barriers, one of its directors told the Grenfell Inquiry.
A report by Dr Barbara Lane following the Grenfell Tower disaster in 2017 found that some horizontal cavity barriers had been installed in the vertical position, as well as uncovering poorly fitting and cut cavity barriers.
Giving evidence to the Grenfell Tower Inquiry yesterday (30 September), Grahame Berry (also known as Bez), a director of fitting firm Osborne Berry, confirmed to counsel to the Inquiry Kate Grange QC that the business didn’t have any guidance from the manufacturer, Siderise, on how to install the cavity barriers.
Asked how, in the absence of any such guidance, Osborne Berry could be sure that the barriers had been installed correctly, Berry said: “Because the mock-up we done, the original sample we done, was inspected by Harley, Rydons, the building inspector, Building Control, people like that come and inspect it to make sure they’re happy with what the sample looked like, and then for us to progress on after that.”
Berry, who by the time his small firm was instructed by Harley had 32 years’ experience installing building envelopes, said he hadn’t heard of Approved Document B at the time, and didn’t recall any discussions with anybody at any time during the project about the compliance of the materials he was fitting with the Building Regulations. He also didn’t discuss the fire performance of the materials he was fitting with anyone on the project.
Berry and business partner Mark “Taff” Osborne employed just one other fitter at their firm and no formal contract existed between Osborne Berry and Harley for the works. Berry had worked as a fitter for Harley for about 20 years before incorporating Osborne Berry.
Berry claimed there were no discussions about the standard of quality of the work required on Grenfell because it was similar to tasks that his firm had performed on other projects for Harley previously.
Manufacturers’ instructions
Berry said that he was not aware at any stage on the Grenfell project of being provided with instructions from cladding manufacturer Arconic (also known as Alcoa), nor did he check any instructions before installing the ACM cladding. He wasn’t aware that the cladding contained a PE core.
Meanwhile, he only found out when Osborne Berry got to site that the vertical and horizontal fire stops (of which far more were required than vertical) were two different products. He said he didn’t remember using cavity barriers with an intumescent strip on previous projects and couldn’t remember if Osborne Berry had used Siderise cavity barriers before.
The horizontal barriers were ventilated breaks and the vertical breaks were “full fill”, non-ventilated breaks. Asked how they distinguished between a horizontal cavity barrier and a vertical cavity barrier, Berry said the horizontal ones had a black strip on the edge of them.
Asked what sort of guidance would have been given to the fitters on the project and how they would know what to do with the cavity barriers, Berry replied: “We done the first mock-up, and after that we took them up there, showed them the initial mock-up, and then took them on the mast climbers and explained to them how we wanted it done, showed them how we wanted it fitted on the building, and then after that they were working either beside us on another machine or on our machine as well, so we were watching how they were fitting it and making sure we were happy with their quality of work and stuff like that.”
Poor workmanship
Berry estimated there was a “good two months or more” between the installation of the horizontal barriers and the installation of the vertical ones.
He also agreed that there was poor workmanship in the installation of the cavity barriers on site, based on a report by Dr Barbara Lane, which highlighted horizontal cavity barriers installed in the vertical position, poorly fitting and cut cavity barriers with rough edges and gaps, or cavity barriers cut around cladding rails, creating gaps. But Berry said he didn’t notice these problems on site at all.
Grange asked how poor workmanship could have been carried out without Osborne and Berry noticing.
Berry said: “I can’t see how it’s arisen because of the other checks that people have come round after we’ve installed the stuff ourselves, there was checks after we’ve installed all our stuff on the building anyway, the insulation, the firebreaks as such. So I can’t see how that got missed, to be fair.”
Asked who checked the cavity barriers and insulation before the panels were installed, Berry replied that it was Harley project manager Ben Bailey.
Grange said that in his evidence, Osborne had said there was often only a small time gap between installing the cavity barrier and then putting the insulation boards around it.
Berry said: “Yeah, but there would have been times where — lunchtimes or at the end of the day, there would have been areas open that weren’t completed as such which someone could inspect at that time. So there was never ever a time where someone would have been up the building and every area was completely finished as such, yeah.”
He agreed with Grange that there would have been “plenty of opportunities” for anyone inspecting the work to have seen the quality of cavity barrier installation before the insulation was put on.
Grange asked: “Is it possible that some of the fitters working for Osborne Berry were left to their own devices when they were fitting these barriers, and installed horizontal in the vertical position without there being any checks of that?”
Berry replied: “Most of the time we were always on site looking at what people are doing on various mast climbers around the building, so I can’t see how it’s happened.”
Competence
Osborne Berry did not subcontract its work at Grenfell Tower but normally used between eight and 14 self-employed fitters through the installation process. Some of the fitters were recruited through agencies.
Grange asked what steps Osborne Berry took on the Grenfell project to satisfy themselves of the installers’ competence and suitability for the work.
Berry said: “Whoever come to site, we would then put them with either me or Mark or someone who has been on there a while who is competent enough to do the job, and they would take them under their wing and show them what to do as well.”
After the Grenfell project had finished, in 2017, Harley director Ray Bailey asked Berry for “CSCS and train course details for all your operatives”. But Berry told Grange that he wasn’t asked for such information on the Grenfell project.
Complaints
Grange asked Berry about an email from Rydon’s project manager Simon O’Connor to Ben Bailey at Harley about a number of complaints from residents about Berry. The email claimed that Berry had knocked on windows asking for tea, banged on people’s windows to scare animals, and fed wrong information to residents “saying that it’s all been put in the wrong way round because of Rydon and hopefully it won’t leak”.
The email also cited complaints of “a complete lack of respect for health and safety (climbing across climbers – dropping material on public footpaths) to mention a few”.
O’Connor threatened to remove Berry from site permanently if there was one more incident on site.
Offered a chance to respond to the email, Berry said the concerns were not communicated directly to him but that he had an email from Ray Bailey, Ben Bailey’s father and director of Harley, about O’Connor’s email.
He said: “I replied to Ray saying that I don’t believe that the guy is saying and it’s not in my nature to do this sort of stuff anyway.”
Grange recalled evidence from Ben Bailey saying that he spoke to the individual and said his behaviour was unacceptable. But Berry asserted that Ben Bailey had never spoken to him about the complaints.
He denied telling residents it had all been put in the wrong way because of Rydon and that hopefully it wouldn’t leak, and said he was “not stupid enough to climb across a climber when it is 10 or 12 or 15 floors up in the air”.
The Inquiry continues.
Comments
Comments are closed.
Sadly poor training and making it up as you go along rather than following manufacturers instructions is endemic in the industry. However, manufacturers and designers need to realise the environment that people are working in and the fact that semi skilled and trained people will be working with them. When I read “poorly fitting and cut cavity barriers with rough edges and gaps, or cavity barriers cut around cladding rails, creating gaps” described as poor workmanship, I do wonder about the expectations of site workers by specifiers.
Previous generations understood this and used materials and designs that were pretty foolproof in that they had a high tolerance to being poorly installed and would work despite the workmanship being a long way from perfect.
Don’t think I’m defending shoddy work and lack of training and instruction, I’m not. However we have to be realistic about the calibre of the workforce, and the conditions were asking them to produce perfect workmanship in. Its not easy working 20m up on a mast climber in the wind and the rain and the faults described, whilst not wanted shouldn’t be a surprise.