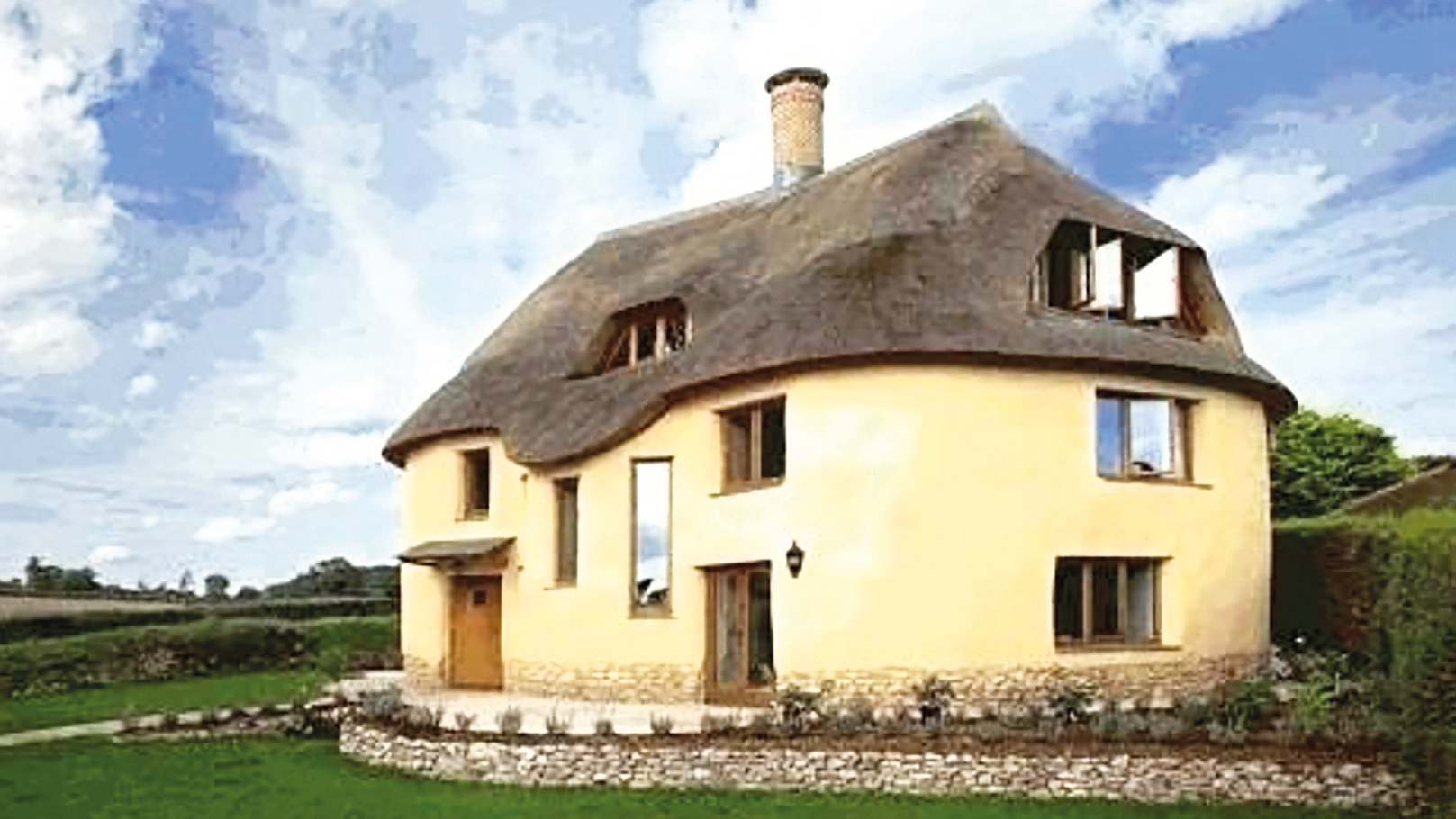
Cob houses could be the solution to low-carbon housebuilding, according to recent academic research outcomes led by a CIOB fellow.
Cob houses built using traditional techniques, mixing earth and natural fibres with water, have existed in the south of England and northern France for centuries, with thousands still in use.
The materials have environmental benefits, including inherent thermal benefits and low inbuilt carbon, but have fallen foul of modern thermal and structural building regulations.
But a cross-border research project led by the University of Plymouth has developed a material used to construct a trial building that meets current building regulations.
Under the CobBauge project (a merging of the English and French words for the technique), academics in Plymouth worked alongside French colleagues to test various combinations of soils and fibres from France and England to create materials that were then thermally and structurally tested.
Low-carbon material
During a tour of the scheme for CIOB members, Professor Steve Goodhew FCIOB, principal investigator on the project, explained the implications for reducing carbon emissions in the built environment.
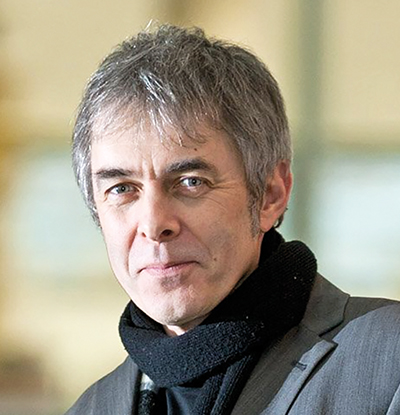
“The main selling point is the fact that the material is low carbon in its very existence,” he said. “And this is to do with the ingredients and the process. We’re trying to reduce global warming gases down to their very lowest level.”
The benefits of cob include the use of locally sourced materials that require little or no transport, low cost and ease of use. The material has low embodied energy and a high thermal mass, which Goodhew says is crucial for regulating the internal temperature in summer and winter.
The tests found that a combination of clay-rich material and hemp shiv provided the best thermal insulation. But it didn’t provide the necessary structural integrity, so a structural mix was added on the inside of the walls.
“The only solution is a structural layer and a thermal layer, in other words a composite of the two together,” Goodhew explained.
Kevin Owen, senior technician at the university’s School of Art, Design and Architecture, provided more information on the materials during a tour of the testing workshop.
A video of the full tour is available at www.ciobacademy.org. Learn more about the CobBauge project at www.plymouth.ac.uk/research/cornerstone-heritage/cobbauge-project.