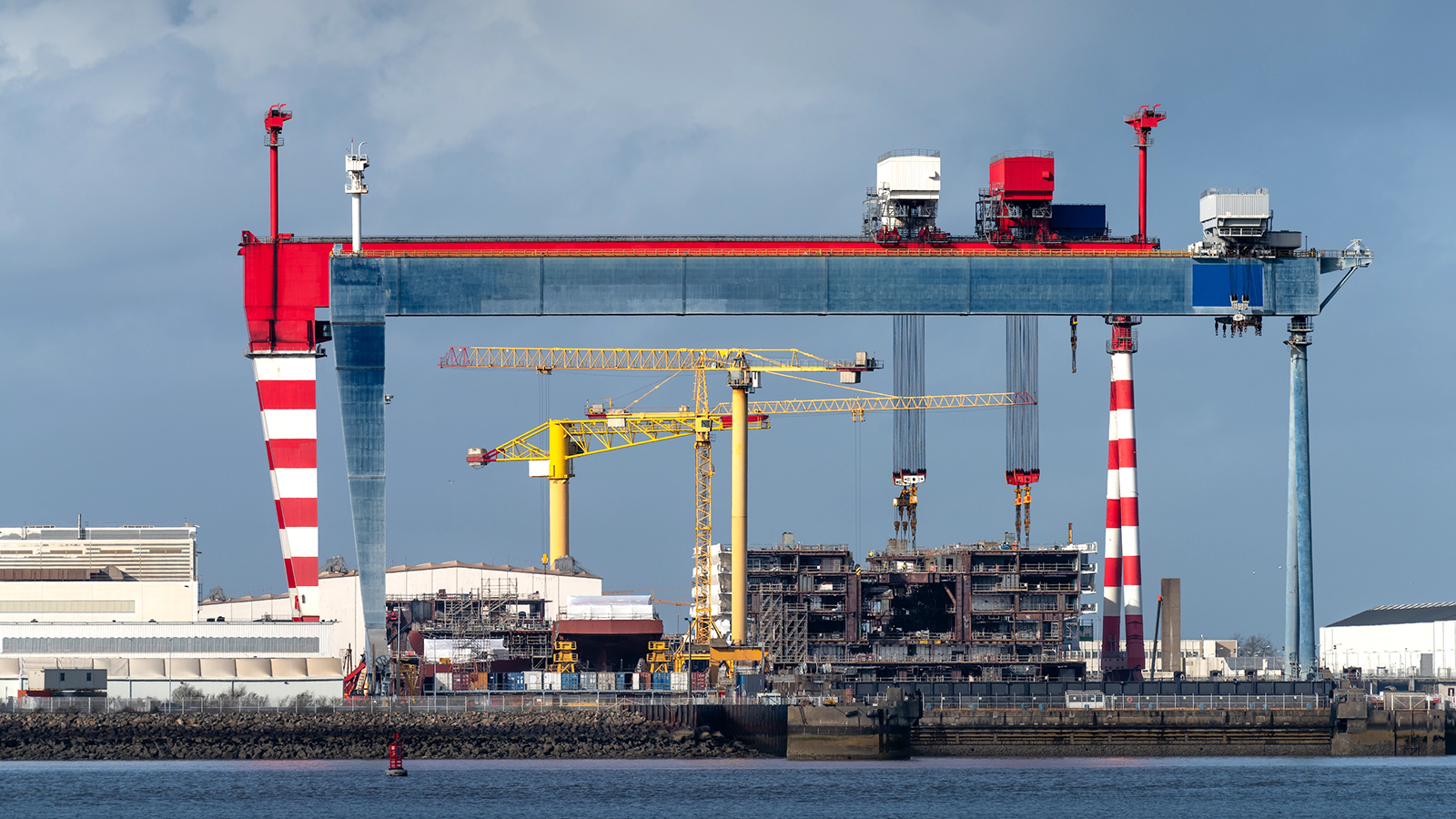
Experts at RNDV, a group of companies with a long-term experience in electrical installation, shipbuilding and complex construction management, say cutting costs for critical competences, such as project management, can lead to costly downtimes and unforeseen situations. It can inflate the budget, causing delays and, therefore, erosion of profits.
Going with the lowest bid might seem to be an attractive option. However, the saying “buy cheap, pay twice” could not be more true when it comes to construction projects.
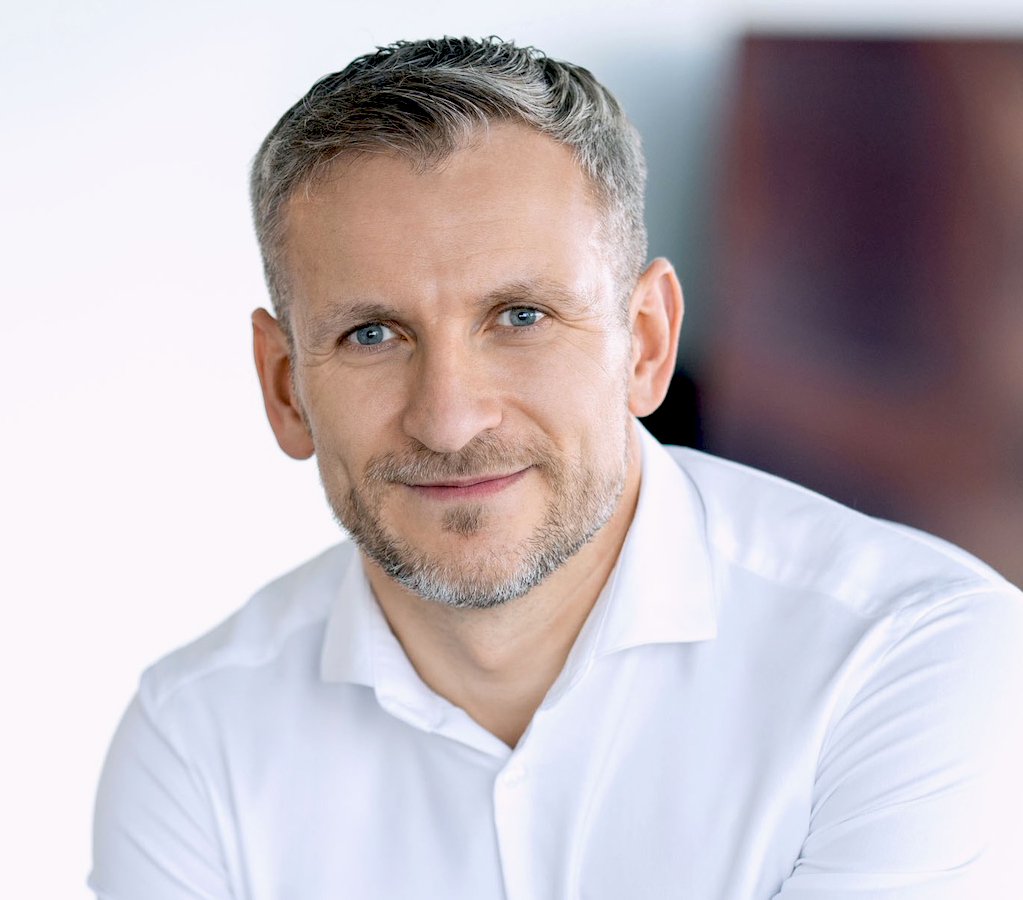
“Sometimes, to save money in the long run, you have to know where to invest.”
“Anyone with experience in construction knows that proceeding strictly as planned can be quite a challenge: unforeseen problems arise at building sites, shortages of materials occur and delays become inevitable,” says Evaldas Kaziulis, a director of sales at RNDV. These are among the top reasons that lead to the erosion of a project’s profit margins, he adds.
“This is in addition to instances of inaccurate technical drawings or documentation, or where there is a lack of labour and appropriate planning. This is why meticulous planning and a flexible, competent team capable of solving issues on site are crucial for a project to be successful: investing in prevention is more profitable than paying for the consequences.”
Kaziulis continues: “Sometimes, to save money in the long run, you have to know where to invest. Once our new clients have had the opportunity to learn about the benefits of having a proper project management team, they very rarely want to try to cut these costs again. This is because it not only saves money, but gives more stability, certainty and, therefore, peace of mind.”
A 20% to 30% increase in costs
According to Giedrius Grėbliūnas, RNDV’s chief project officer, downtime rates, common in the industry, can be in the range of 20% to 30%. When downtimes are caused by issues such as delayed delivery of materials or errors in technical drawings, contractors typically claim additional payments. This leaves the client with two options: decline and potentially lose a contractor for future projects; or negotiate regarding the size of the claim and increase the project’s costs.
“In other words, when efficiency drops by 20%, the costs are likely to rise accordingly,” says Grėbliūnas.
To illustrate the point, he gives an example of two companies that are working on identical projects. “Let’s say the first company includes a project management team, maintaining 100% efficiency and keeping the project cost fixed at €1m. In contrast, the second company chooses a slightly cheaper option, pricing their project at €900,000, but without a project management team. Due to a 20% drop in efficiency, their final project cost increases to €1,080,000, leading to an €80,000 loss.”
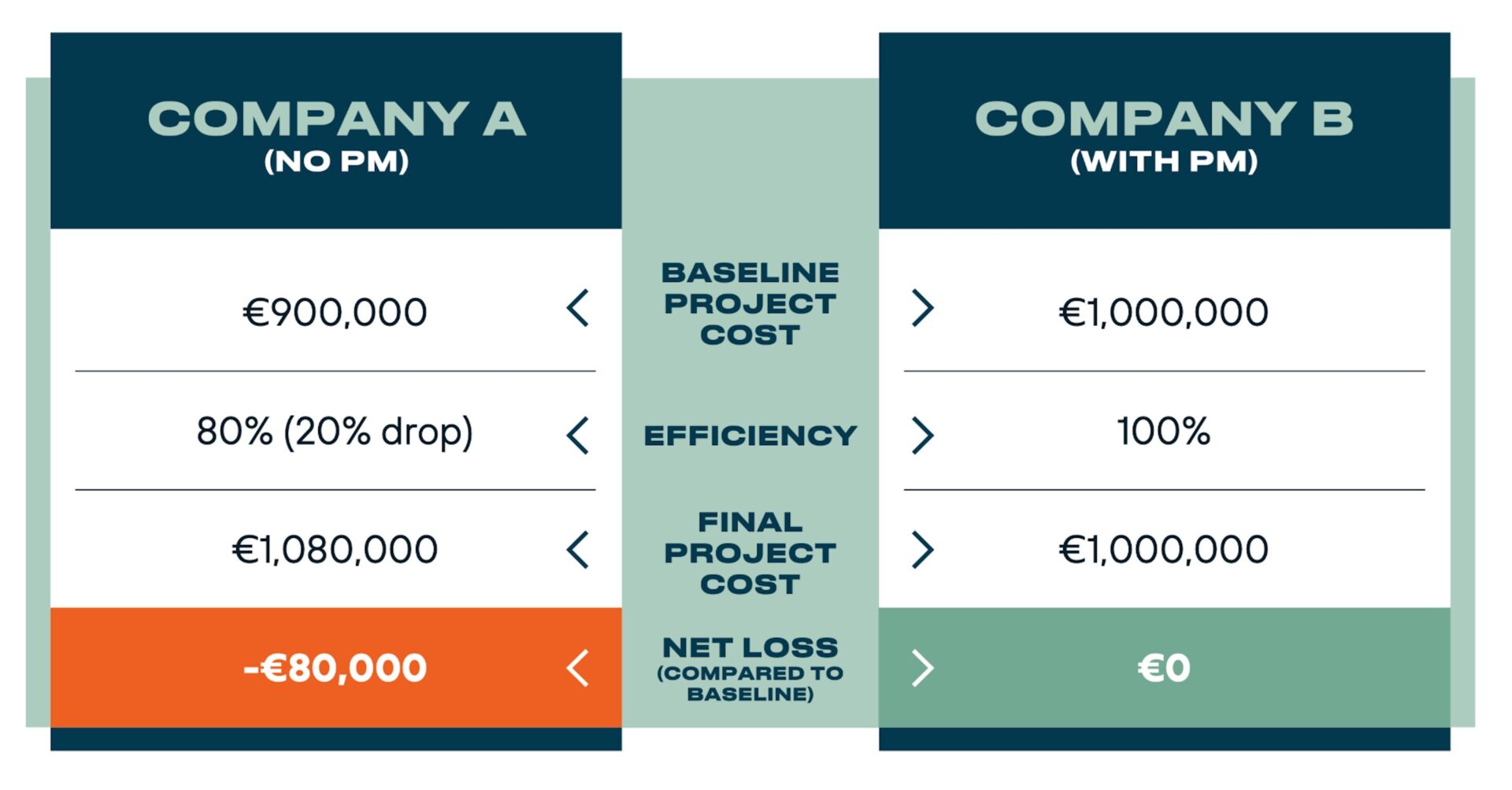
Efficiency made standard
Making 100% efficiency its standard, RNDV aims to eliminate waste in construction projects by implementing the ‘full-kit’ methodology. This significantly improves a project’s execution by ensuring that all necessary resources, materials and instructions are available before any work begins.
“This approach eliminates delays caused by missing components or incomplete guidance, fostering a seamless and uninterrupted workflow. By enabling workers to focus solely on task execution rather than sourcing materials or seeking clarifications, a full-kit approach improves operational efficiency,” says Grėbliūnas.
“Additionally, it reduces the likelihood of errors stemming from missing or inaccurate data, promoting consistency and reliability in task completion. This structured approach contributes to more accurate project timelines and greater predictability throughout a project’s lifecycle.”
A proper team is the key to success
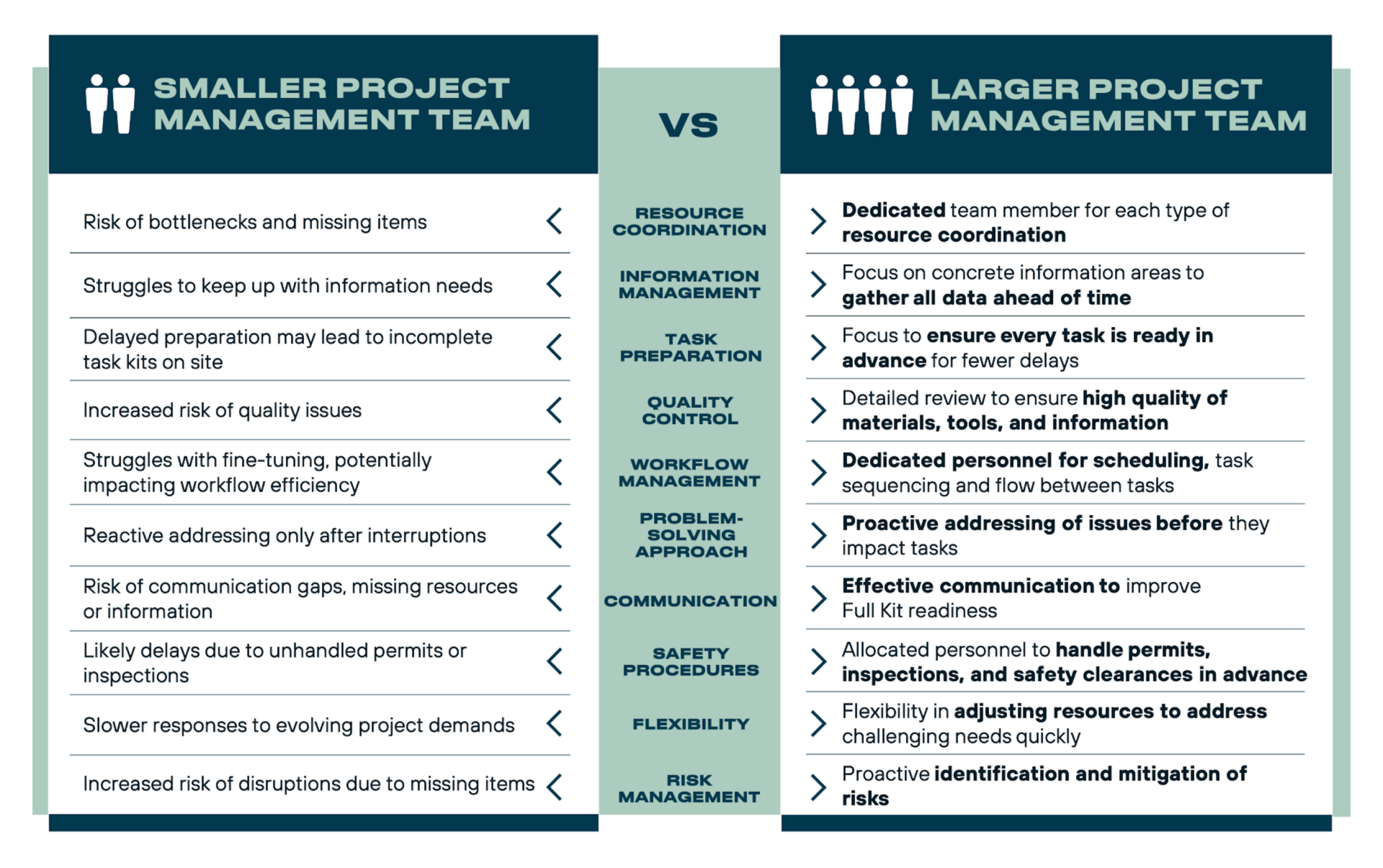
This is why having a comprehensive team with a project manager, site manager, site foremen and team leaders is crucial – and something that is still often overlooked.
“A well-built contractor’s project management team is necessary to make sure that the full-kit principle functions properly. In this way it can significantly contribute not only to sustaining, but even increasing profits. Unfortunately, many players in the industry still overlook it, leading to significant losses of both money and time,” remarks Grėbliūnas.
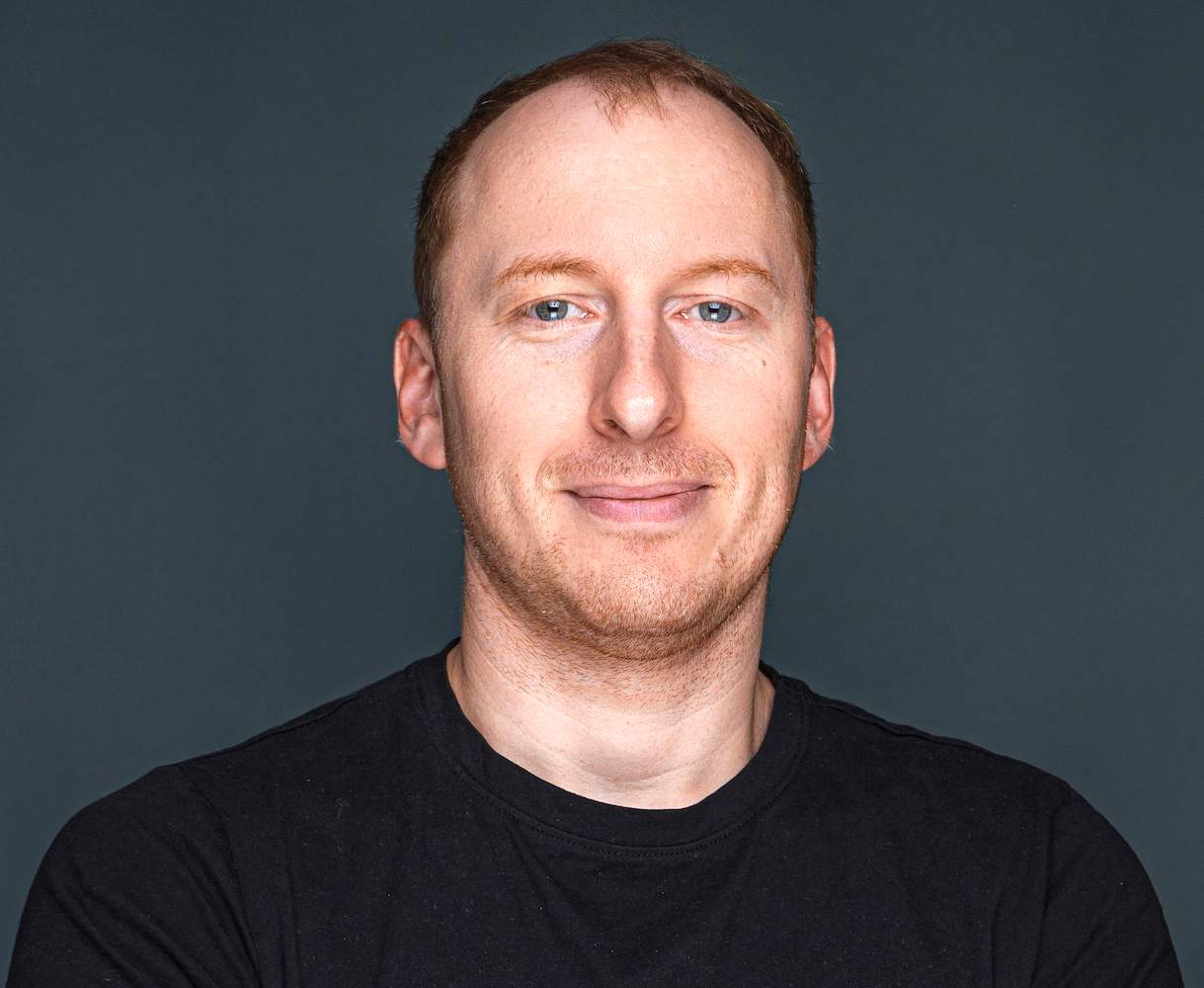
“A proper project management team ensures that a project is carried out at 100% efficiency. This means transparency, cost-effectiveness and predictability.”
The size of the project management team required to effectively implement the full-kit methodology largely depends on the project’s scale, complexity and the diversity of its resources.
“A well-structured team should be adequately staffed to ensure meticulous planning and resource coordination, in addition to timely communication. For larger or more complex projects, this may necessitate specialised roles, such as procurement managers, engineers, quality managers and more, who manage the comprehensive preparation process,” Grėbliūnas notes.
However, more is not always better, and overstaffing can also lead to inefficiencies. It is therefore essential to strike a balance such that the project management team is large enough to handle the workload without having any redundancy within the team. “A proper project management team ensures that a project is carried out at 100% efficiency. This means transparency, cost-effectiveness and predictability,” concludes Grėbliūnas.
About RNDV
The RNDV group of companies has been operating since 2007 and has grown rapidly and now has a team of more than 1,866 employees in 23 countries. Primarily focused on Western Europe, RNDV has increased its revenue by executing a wide range of electrical installation projects, including work on data centres, shipbuilding and repair, electromechanics, scaffolding and technical insulation, as well as renewable energy initiatives. The group’s revenue grew by 20% last year, reaching €126.5m.