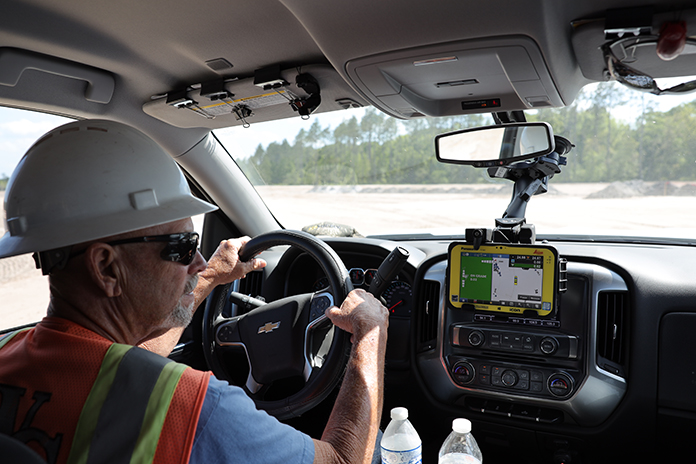
Accessing the digital model using the in-cab display
A ‘connected site’ concept unveiled at America’s biggest construction event could become the new model for infrastructure schemes. Peter Haddock explains.
In March this year at Conexpo 2020, America’s showcase event for the construction equipment sector in Las Vegas, the infrastructure site of the future was on display.
Hexagon, the parent company of surveying and machine control technology specialist Leica Geosystems, was displaying its ‘connected site’ concept. Digital tools on site, including tablets used by construction managers and machine control technology, connect with 3D models. Meanwhile augmented reality shows the actual worksite overlay and the levels achieved in the ‘as-built’ model.
Data capture and management
As work progresses, data is captured, structured and managed to create what is essentially a digital twin of a large civil engineering project.
Vice-president Holger Pietzsch says his company has been following a ‘real world’ project, the earthworks for a residential development in Florida, carried out by contractor Gardner.
“We worked with the Gardner team to provide all of the equipment needed to create a ‘digital twin’ of the site,” says Pietzsch. “We then followed the project from the planning stage, right the way through its earthworks construction phases, which included validation and the delivery of its ‘as-built’ final earthworks model to the client.
“We then took this information and mapped it against the digital workflows involved in its creation, so we could demonstrate how data was managed throughout the project.”
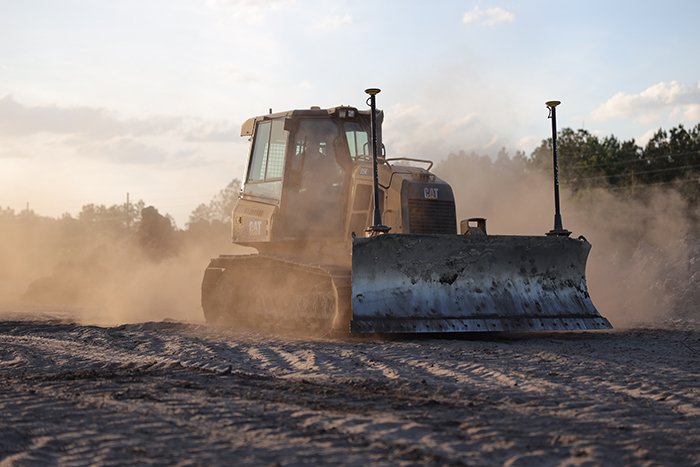
Sensors on the kit connect with GPS systems
At Conexpo, Hexagon created a scale model of the Florida site, plus tablets which visitors could use to access and understand the digital twin. “This allowed us to prove how technology can simplify the delivery of a project and that different sensor-led devices can work together,” says Pietzsch.
In the UK, the construction sector has been making steady strides towards the model unveiled by Hexagon at Conexpo.
“The level of adoption with connected assets is much further ahead of the US and the learning curve is sharper,” says Neil Williams, heavy construction director for Leica Geosystems.
“This adoption is also accelerating since Highways England recently has mandated the use of 3D machine control on all its projects and HS2 is looking closely at the connected site model.
“On projects like Hinkley C, data are making a productivity difference. For the construction manager, comes the ability to access information from any connected location and even to drive around the site and see progress against the model on a connected tablet.
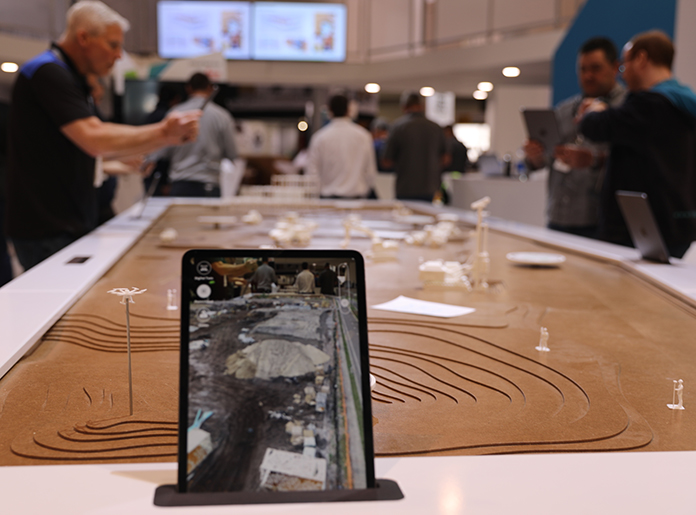
Conexpo visitors use tablets and a scale model to understand the digital twin on the Florida project
“This level of connectivity allows the individual to monitor different parts of a project, to determine progress against plan, and ensure every machine is working to the most up to date model, reducing errors and the reworks associated with them.
“For earthworks, this approach works not only for the big projects, it can work for all sites.”
Maintenance benefits
The digital twin offers numerous benefits for infrastructure projects. Data insights will allow maintenance to be planned and executed more effectively, such as repair of potholes using 3D as-built model data. Utility strikes will be a thing of the past. Lessons will be learnt and taken from one similar site to the next, supporting faster delivery.
But as Williams says: “A connected site is only as good as the connectivity available and the data that it depends on. So, what we now need to do is make sure data is correctly captured, validated and inputted into models much more swiftly and accurately.”