If the construction supply chain is to decarbonise, it must embrace digital technology. That was the verdict of an expert panel from contractors, suppliers and academia, brought together by CM editor Will Mann.
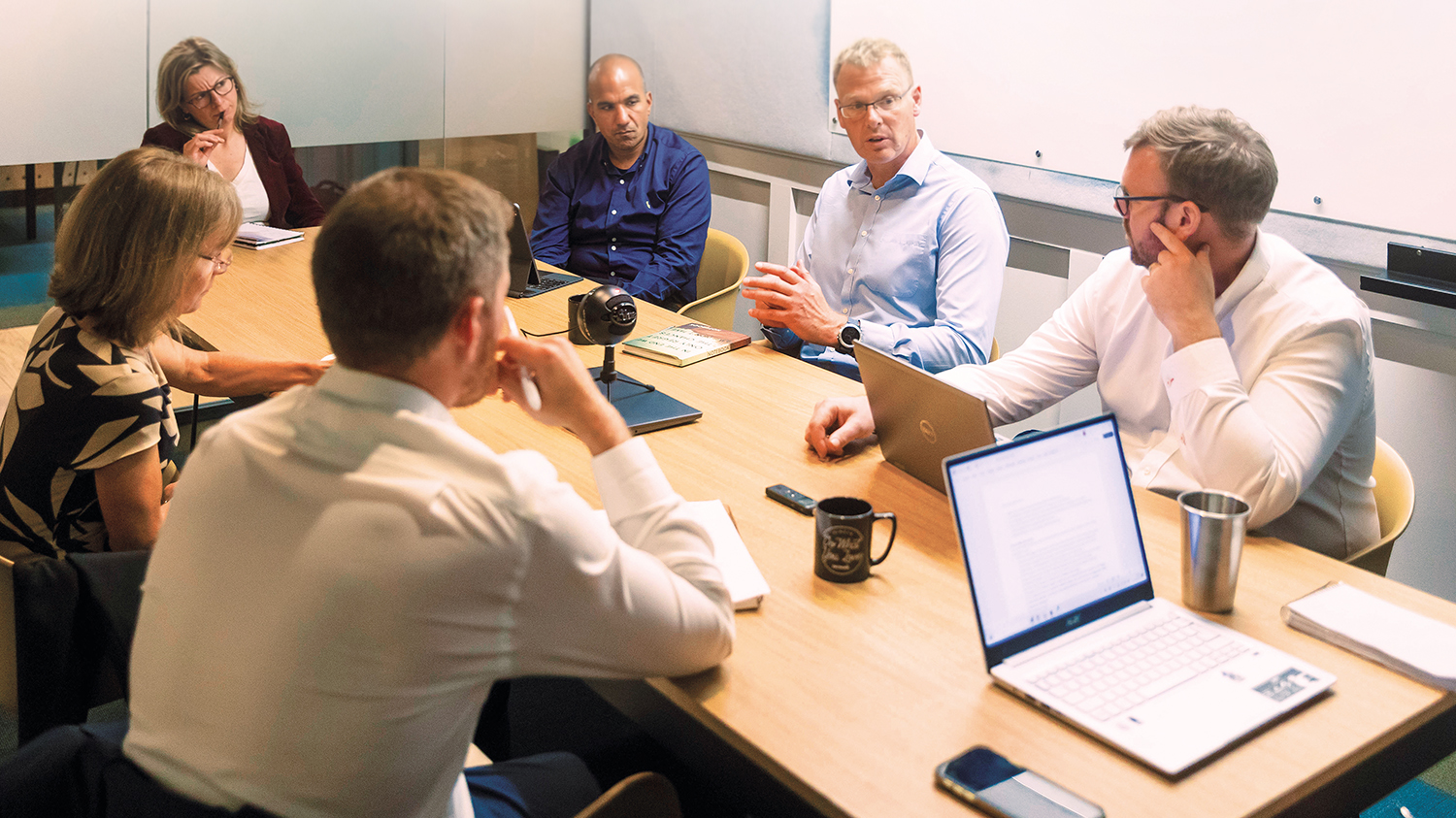
The panel
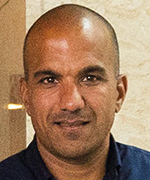
Arun Thaneja – Technical services and sustainability director, Winvic Construction
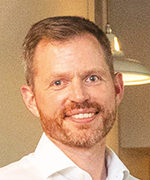
Michael Cross – National head of sustainability, Willmott Dixon
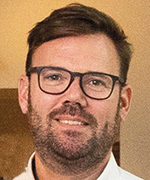
Thibaud Lefebvre – Vice-president, Hilti (Great Britain)
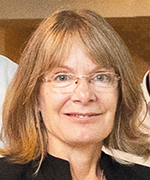
Carol Williams – Head of procurement, Laing O’Rourke
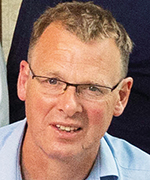
Chris Gorse – Head of CIOB Sustainability Panel and professor of construction engineering and management, Loughborough University
Chair: Will Mann – Editor, Construction Management magazine
Cristina Lago – Deputy editor, Construction Management magazine
Will Mann: What are the biggest challenges in reducing carbon emissions in the construction supply chain?
Michael Cross: The fragmented and occasionally adversarial nature of the supply chain doesn’t help with creating a sense of collaboration, which could help begin to address some of the environmental issues our industry must deal with.
There needs to be more innovation in terms of the materials we use to build with, but innovation can in turn be limited by clients being cost conscious and risk averse, especially around things like fire safety, where strict controls have understandably been introduced in the wake of events such as Grenfell.
Properly understanding the issues around sustainability is important. Sustainable construction sounds complicated, but at its basic level it just makes good business sense.
Carol Williams: There can be unintended consequences when we adopt sustainable solutions without fully understanding what it will entail or what it leads to. For example, some people are switching back to fossil fuels because they aren’t getting what they expected from their investment in electrically powered equipment.
We need better data around how we can be more sustainable. And we need to research and invest in ‘whole life’ materials and products to help us deliver better outcomes. Yes, solar panels are good, but what happens to them at the end of their useful lives? If they are not reused in some way then there is the risk of creating a waste problem.
Arun Thaneja: Many engineers and architects in the industrial sector have done things the same ways for years and are reluctant to try new methods and use new materials because this may mean a project takes longer to deliver. This attitude needs to change.
Regarding the supply chain, we’ve worked with partners and helped them set baselines where they measure their efficiencies and carbon reduction targets. There will always be challenges, including cash flow, but everyone has got to want this for it to work.
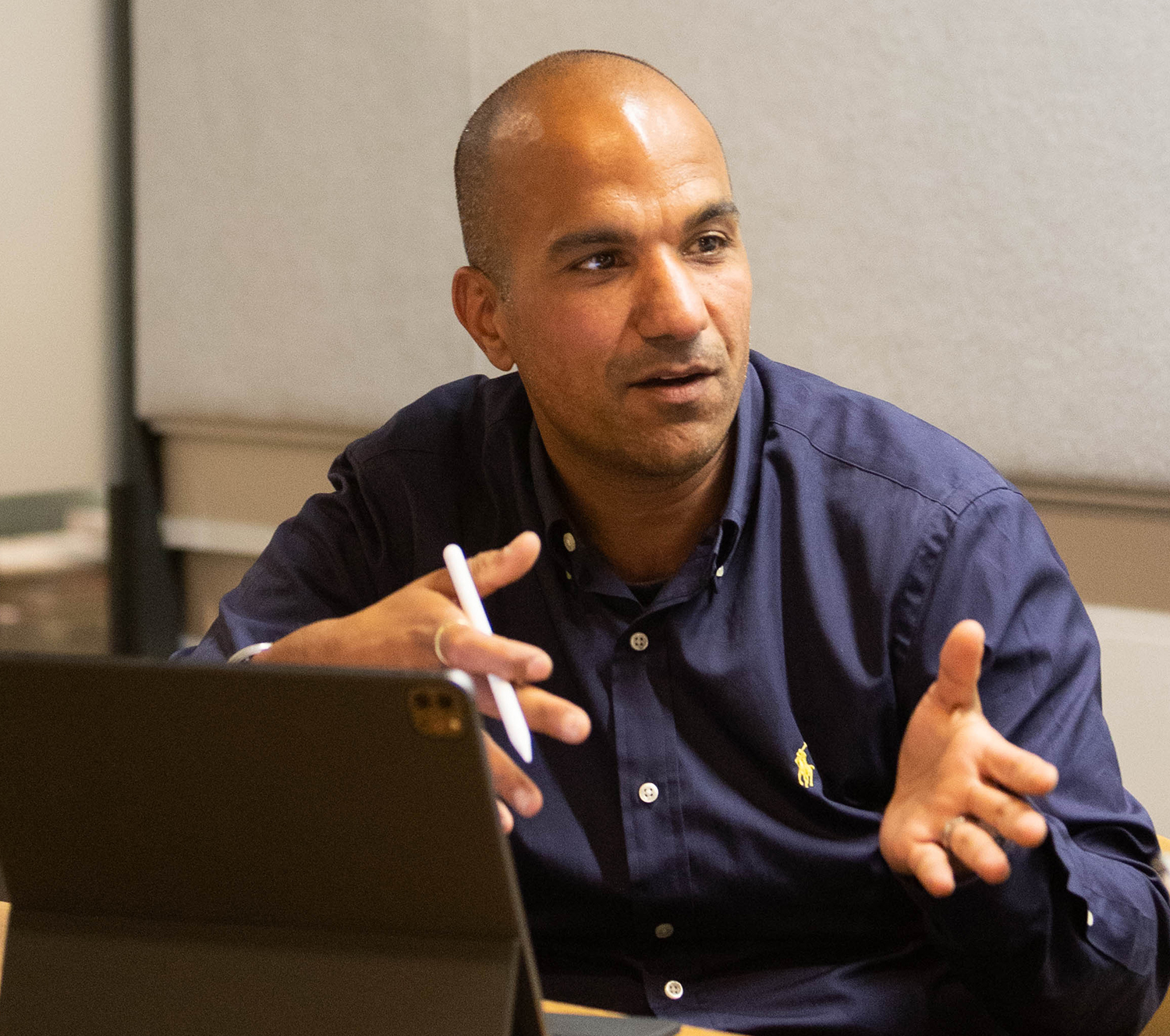
Chris Gorse: As an industry we work to tight deadlines and budgets, and we normally deliver quality buildings. We’re extremely skilled at delivering complex projects against all the odds. But we do have an issue around some of the information on products, services and what goes into certain materials.
We used to lead the way in terms of product development and testing, but we’ve forgotten some of the fundamental properties that we want in our buildings. Better data, along with better communication, can help us understand the properties of various materials and help us make better decisions. There are good systems out there, but we need to work with bigger institutions, bigger product suppliers, to get that specialised information to those that need it.
Thibaud Lefebvre: There is a marked lack of knowledge and education around how sustainability can work in the construction sector. As people have said, how do we assess where we are if we don’t have the data we need to make informed decisions about sustainability?
Along with better information, we also need more unified standards and frameworks, and better collaboration among various stakeholders. People look at the upfront cost of a material, but less so at the whole life of the product which those materials make. We need to look at that too.
WM: What changes in working practices and innovations do you think will do most to reduce carbon emissions?
MC: Two things will help. Greater use of modern methods of construction (MMC), helping to improve the way we deliver materials and put them together on site. And secondly, applying digital platform design solutions to more projects.
It’s a massive opportunity for some clients, particularly those delivering projects in education or healthcare, where a standardised approach makes sense in terms of carbon reduction and reduced costs.
It also allows for faster design, faster delivery, and makes your material use much more efficient, so that you’re not using more than you need, or spending valuable resources on stuff that is unnecessary.
CW: I agree. Take a hospital. We see a lot of bespoke design when what is needed are common facilities, eg operating theatres, wards. Standardising some elements, like these, will help enormously in terms of carbon reduction goals.
Meanwhile AI can help with design, analysing what is required, breaking it down to make it easier to fabricate off site in a modular, standardised way. Systems thinking is needed around the provenance of products and product data as standardisation becomes more widely used.
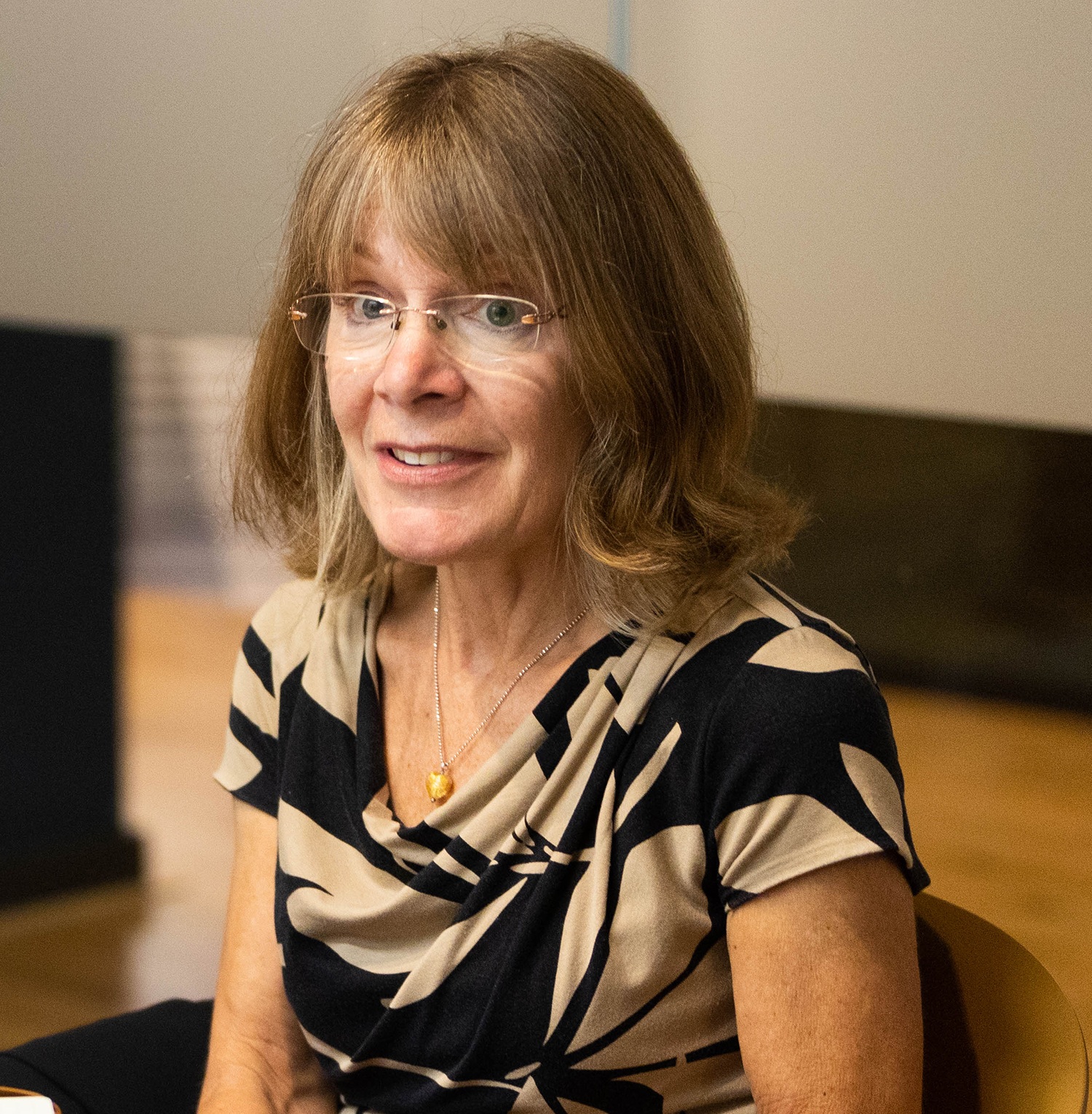
Public expenditure will make a lot of difference to how this progresses, which is why we have to work with government to enable the industry to invest.
AT: Transporting material to site is another issue which can be addressed. We’ve acquired bigger articulated trailers that can carry more steel and therefore cut down the number of deliveries that are necessary. We’re also addressing waste and how we can reduce this.
But these remedies can impact the bottom line, so we need to assess what works best to start with and work from there.
We’re also linking BIM to carbon calculators, so we’re automatically plugging carbon factors into the BIM model. This can be useful when, as often happens, a client changes their mind about something. The use of digital technology is going to be a key factor in helping us reduce carbon.
CG: Standardisation, MMC and prefabrication play an important role for those wanting both repeatable and bespoke structures. But the circular economy argument falls off a cliff if you can’t return a product to the supplier for reuse. If you can argue the case for that, and commercialise that process, you’ve got a powerful argument for the circular economy.
Also, we shouldn’t fear technologies like AI. Yes, the data needs to be spot on, but we’ve got the skills to assess whether a particular design will work, what materials will or won’t be suitable and how we assemble them to make the project work. As an industry we’re dealing with some pretty complex problems. We might not be moving as quickly as some clients would like, but we’re getting there.
TL: It’s clear that embracing digital ways of working is a no-brainer. Also, doing more with less. The principles of circularity should be integrated into every aspect of a project, where possible.
The electrification of job sites also needs to go further. We want to not only reduce CO2 emitted during the production of our tools, but look at how we reduce the CO2 emissions of the tools during their lifetime.
If you can combine sustainability with safety and productivity, and keep costs down, then people will buy into that. It’s challenging, but we are on the right track.
WM: Focusing on digital, what tools can help with decarbonisation at all stages of the project process?
MC: Implementing digital platforms, integrating them with one’s supply chain, which can in turn lead to a project being delivered more quickly than traditional methods.
We should also be looking at how other industries, such as automotive, have taken technologies on board and adopted them. Then there’s reuse. As an industry we should be much better at identifying materials that have been used and look at how they can be used elsewhere, in other projects, when the structure where they were originally installed is being torn down.
CG: As has been said, looking at how other sectors use technology can be enormously helpful. We need to move closer to the example of aerospace, especially when maintaining the operability and condition of products.
In the aerospace sector, engineers would work on different iterations of a design, and learn about what worked and what didn’t as it progressed. In construction, where projects last a lot longer, that opportunity to learn as much as our colleagues in aerospace isn’t there.
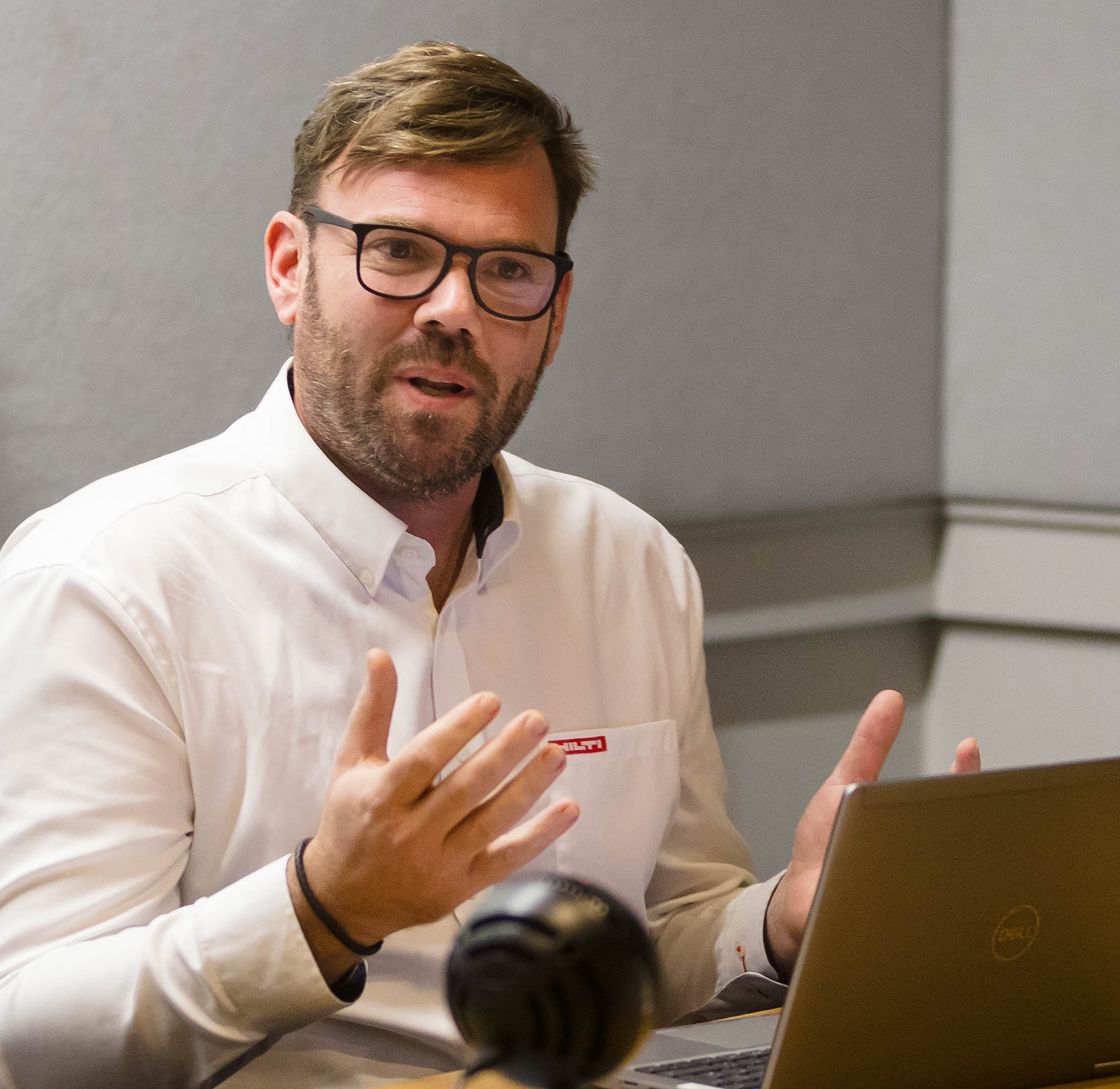
Then there’s data. The Building Safety Act requires the storage and updating of a baseline of data, but I’m not sure how that will play out. In construction there have been too many ways to get around putting in the correct solution.
CW: When the construction sector delivers a hospital or a school, or rail infrastructure or a nuclear power station, we follow an architectural process. But when it comes to operations and data and technology enablers, things are less clear. Where is the design to optimise the use of materials? How can we optimise our use of plant machinery so that we don’t have more than we need at any one time?
We ask ourselves: “What is the technological architecture that this industry needs?”, but in practice it’s different stakeholders using different apps. If we create a technology strategy across the industry, and if we were able to better collaborate with the supply chain in that space, it would make a massive difference to both productivity and reducing our environmental impact.
AT: You can’t consider the circular economy without the availability of appropriate data. A supplier could say they have a sustainable product, but can they prove that when we try and track that product back through the years? Have you recorded lifecycle assessments?
I can order a robot that on paper claims to be the most efficient, sustainable piece of equipment, but if there’s no data to back that up, you’ve got nothing.
One of the biggest issues we’re seeing right now is around the validity of data for carbon assessments, so anything that can improve our data collection and analysis can only be a good thing.
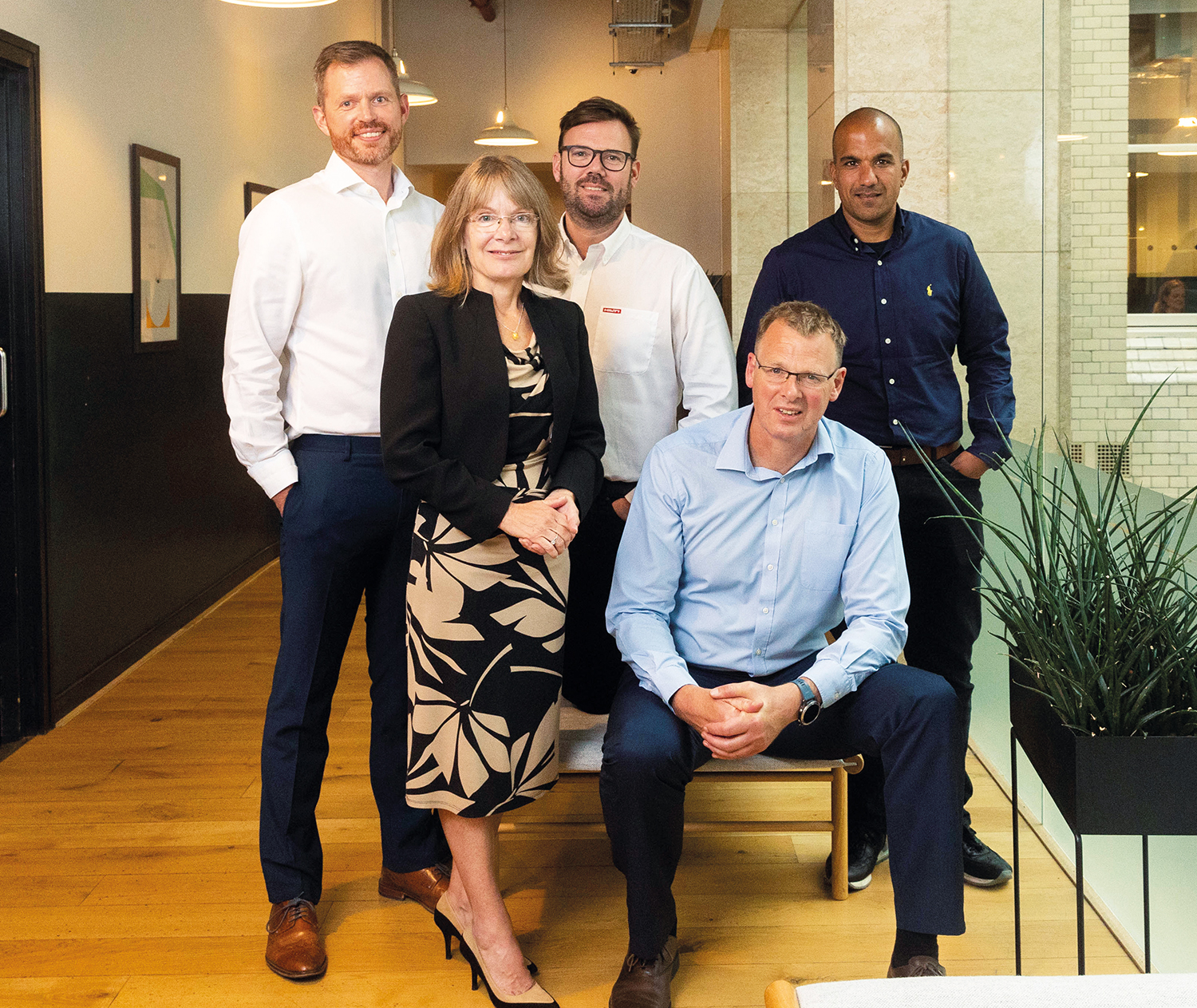
TL: There is a lack of awareness around how to make sustainable decisions. And part of that is due to the lack of available data. As I mentioned earlier: how do we know where we’re at if we don’t have access to reliable, actionable information to hand? It comes down to the sort of technology and data-gathering techniques being used, and these need to be more robust.
CG: When it comes digital platforms, our customers still struggle. One of the main issues is the lack of an integrated solution. If different software platforms don’t or can’t speak to each other there will be
a duplication of effort. It’s better than nothing, but it’s inefficient. When it comes to materials, such as combustible products, and what we can use and where, BIM comes into its own.
We have to take a lead on working out which products and services work and why they don’t. And if we get the building design right, get the right construction processes in place, partner with asset managers or digital platform people, we can get into predictive maintenance and controls where we take some responsibility from facility managers and building operators – then we’ll be better positioned to benefit from the front-end investment.
This article has been produced by Construction Management in association with Hilti
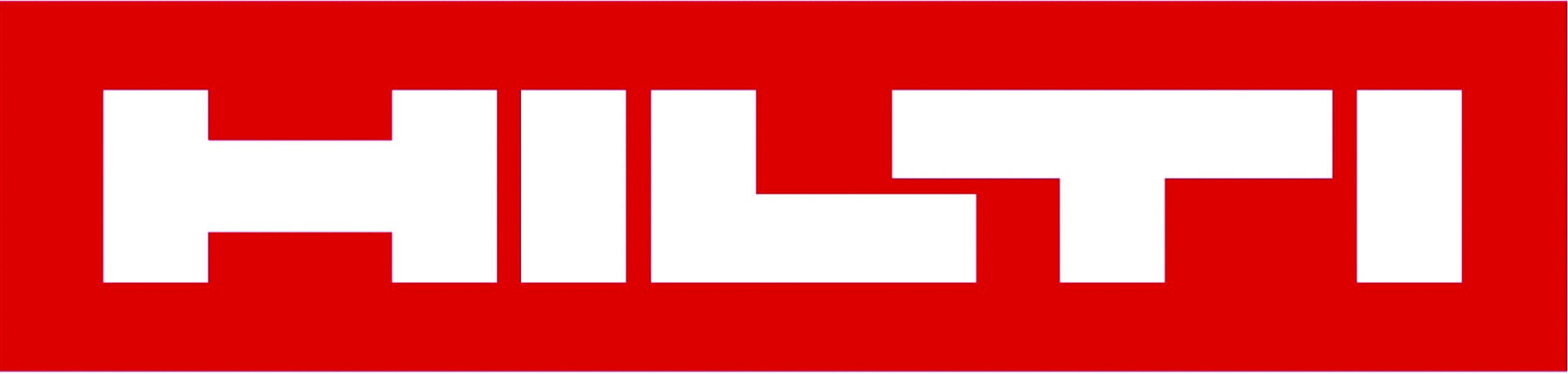