The Digital Construction Awards attracted more than 120 entries, 63 of which have been shortlisted. Here, we detail the Best Use of Data shortlist.
This category recognises the use of data to enhance delivery of a project or improve a process within a construction organisation. Six entries made the shortlist:
51 Moorgate | Skanska UK
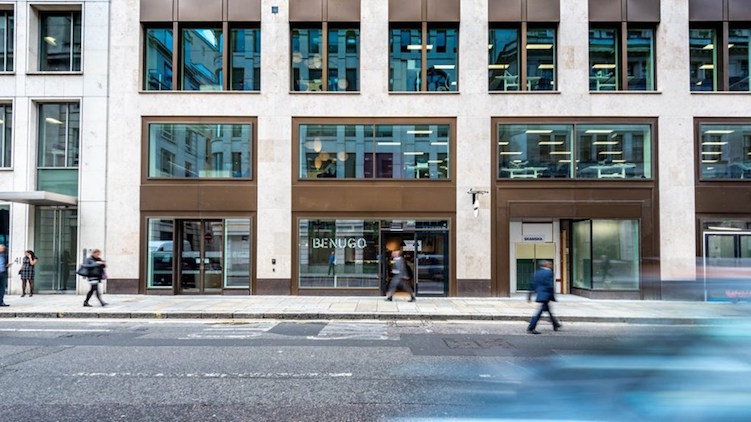
During 2020, Skanska developed its own intelligent buildings platform, which it deployed at its head office, 51 Moorgate in the City of London.
The platform collects and analyses real-time data to improve building performance, focusing on carbon and operational efficiency.
The technology allows Skanska to monitor and analyse the condition of the building and its assets. Through the platform, it can offer a service remotely to control all the assets that are monitored.
The platform integrates with other software including: Autodesk BIM 360 and Forge – for real-time models and specification data; Concept Evolution – for connecting to the building’s FM software; and Microsoft Azure – for hosting data and providing security measures.
Additionally, the platform connects to individual control systems, for example the BMS, and more than 140 IoT (Internet of Things) devices.
Since introducing the platform at 51 Moorgate, the building has seen an energy reduction of more than 40%, through using data to drive energy savings, and an 8% reduction in required FM labour.
Applying smart data connection at the HCA Cancer Care Hospital, Birmingham | Vinci Construction
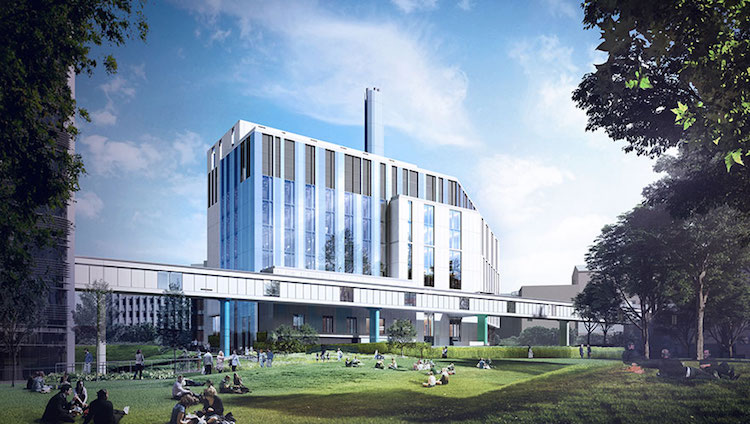
Vinci worked with US firm Openspace to introduce 360-degree data capture for recording site progress. After the initial implementation, Vinci looked at how it could link this data to the construction programme in real time.
On the HCA Cancer Care Hospital in Birmingham, Vinci used AI to convert 360-degree images into a measurable record of progress. The contractor then found other efficiencies from the technology.
The process for updating the programme is a weekly site inspection. Vinci wanted to increase the efficiency of this process and improve planning activities using the structured data captured.
In response, its digital team developed a ‘Smart Data Connection’ (SDC). This automates data entry from any structured data and connects this into a new ‘Digital Information Hub’, using Microsoft Azure software.
The implementation of SDC at the HCA scheme resulted in a 60% efficiency improvement in time taken for site inspections. Vinci also reduced the programme from 113 weeks to 110 weeks.
ARC – automated cable routing management system | Bryden Wood with Transport for London
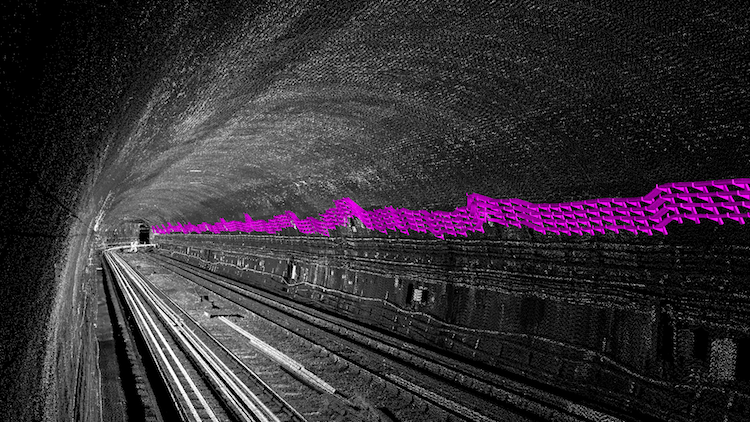
Upgrading cabling in London Underground tunnels used to be time-consuming and labour-intensive. Bryden Wood, working with Transport for London (TfL), has developed ARC: data-driven design automation technology for underground signal upgrades that makes cable routing faster, safer and smarter.
The ARC process starts with collation of as many input variables as possible to establish machine-readable rules. Then comes a point cloud survey of the tunnel, which is analysed. The rules then recommend the optimal routing of cables. ARC also outputs 3D models offering various options for cable installation.
Bryden Wood and TfL successfully tested the process on sections of tunnel, before the software was handed over to TfL.
Cable routing design typically takes months or even years. Results from ARC’s tests show that once the point cloud survey is complete, TfL can provide design outputs in less than two days. ARC also reduces network disruption and safety risks for the workforce.
360 real-time reporting | Multiplex
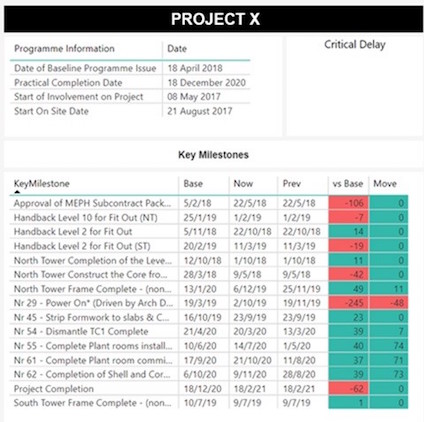
Internal analysis showed Multiplex that its people were spending 60% of their working week generating monthly project performance reports in Excel, which often contained out-of-date information. Realising the inefficiencies of this, the company decided to develop a 360 real-time data analysis tool.
This initially meant an extensive R&D process, which included creation of a ‘data dictionary’ and identification of the best storage method and schema for project data.
Multiplex’s data was historically managed in third party tools or Excel, and the designers of the 360 tool ensured the data vault modelling integrated with existing in-house data entry apps. They also designed the data ingestion processes to be fluid and editable so they could react to the business’s changing requirements.
The new 360 tool has resulted in reduced reporting time of up to 40 hours a month on each Multiplex project. The system also identifies trends across projects and its real-time capability allows project leaders to take decisive action before issues turn into bigger problems.
QFlow on SCS Railways | SCS Railways and Q Flow with HS2
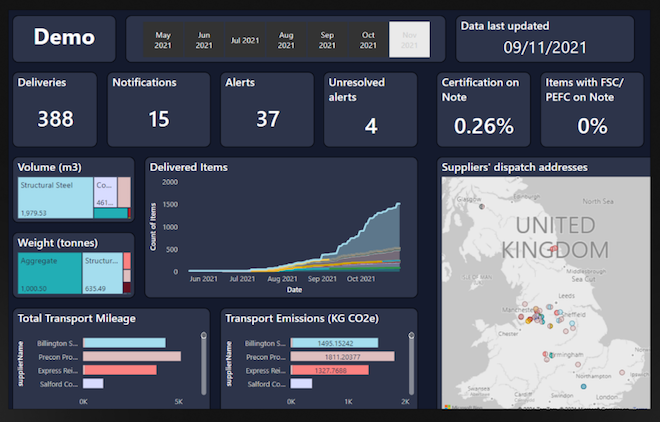
Construction teams on HS2 must report against tough environmental, sustainability and quality requirements – meaning collation and analysis of vast quantities of data. The SCS Railways JV (Skanska, Costain and Strabag) had already used Qflow on its enabling works contract to automate waste transfer data collection and identify non-compliance.
On its London tunnels contract, SCS used Qflow to address other time-consuming issues. These included linking the sustainability data collated with certificates and connecting the reporting through a public API with other SCS systems, including Microsoft Power BI, SCS’s main tool for reporting.
Further developments Qflow is looking at include benchmarking performance against Environment Agency data and identifying key product groups with disproportionately high carbon impact
Implementing and developing Qflow on just one third of the contract has resulted in benefits including: 65%-80% efficiency gains for collecting and digitising data across eight sites; capturing more than 70% of waste movements compared to less than 30% previously (these can now be incorporated in the logistics waste movements tracker); and £108,000 in direct cost savings per year.
The Forge | Sir Robert McAlpine, Mace, Landsec, Bryden Wood
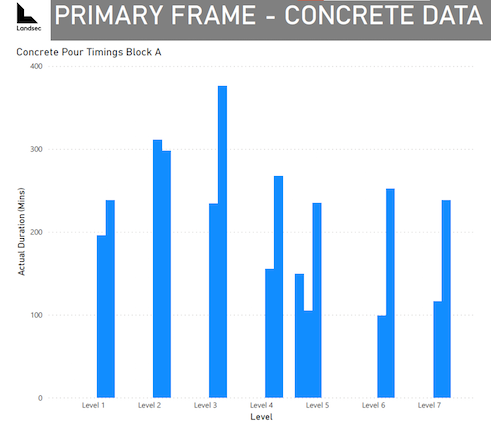
Data was key to the platform DfMA (design for manufacture and assembly) strategy on this 139,000 sq ft office development in Southwark, London.
Sir Robert McAlpine (SRM) and Mace worked with client Landsec and architect Bryden Wood to collect and analyse data across a range of platform DfMA packages.
Data sets collected included concrete pour times and strength monitoring, facade install times, tower crane performance, waste management and delivery times. This was all crucial to calculate productivity and carbon measurements.
The team created a centralised reporting hub using Power BI to combine all the various data streams in 10 dashboards.
With this data, SRM and Mace were able to drive productivity gains across the project. For example, the use of Converge software to monitor concrete strength, using live data from wireless sensors monitored by AI, resulted in reduced strike times. Disperse 360-degree photo capture and automated AI progress-reporting speeded up site inspections and helped the team analyse the project’s progression.
Awards ceremony
The winners of the Best Use of Data category, alongside the victors of the other 11 categories, will be revealed at the awards dinner on 12 July at the Brewery in London.
You can join them by booking your places at the awards. There is an early bird discount of 20% for those who book tables before 5pm on 20 May.
The Digital Construction Awards celebrate best practice and reward innovation in the application of BIM and digital technology in the built environment sector.
The awards are run by Digital Construction Week, the Chartered Institute of Building, and media titles Construction Management and BIMplus.
Awards sponsors include Revizto, Bluebeam, Procore, Autodesk, Solibri and the Association for Project Safety.
Don’t miss out on BIM and digital construction news: sign up to receive the BIMplus newsletter.