The Digital Construction Awards attracted 170-plus entries this year, 85 of which have been shortlisted. Here, we detail the finalists for Digital Collaboration of the Year, sponsored by Bluebeam.
This category recognises the best use of digitalisation/digital methodologies and/or technologies to enhance collaboration between two or more organisations on a project, at any level of the supply chain. Six collaborations made the shortlist.
40 Charter Street, Canary Wharf | KPF/Canary Wharf Group/Aecom/Revizto/Dome Group/Disperse
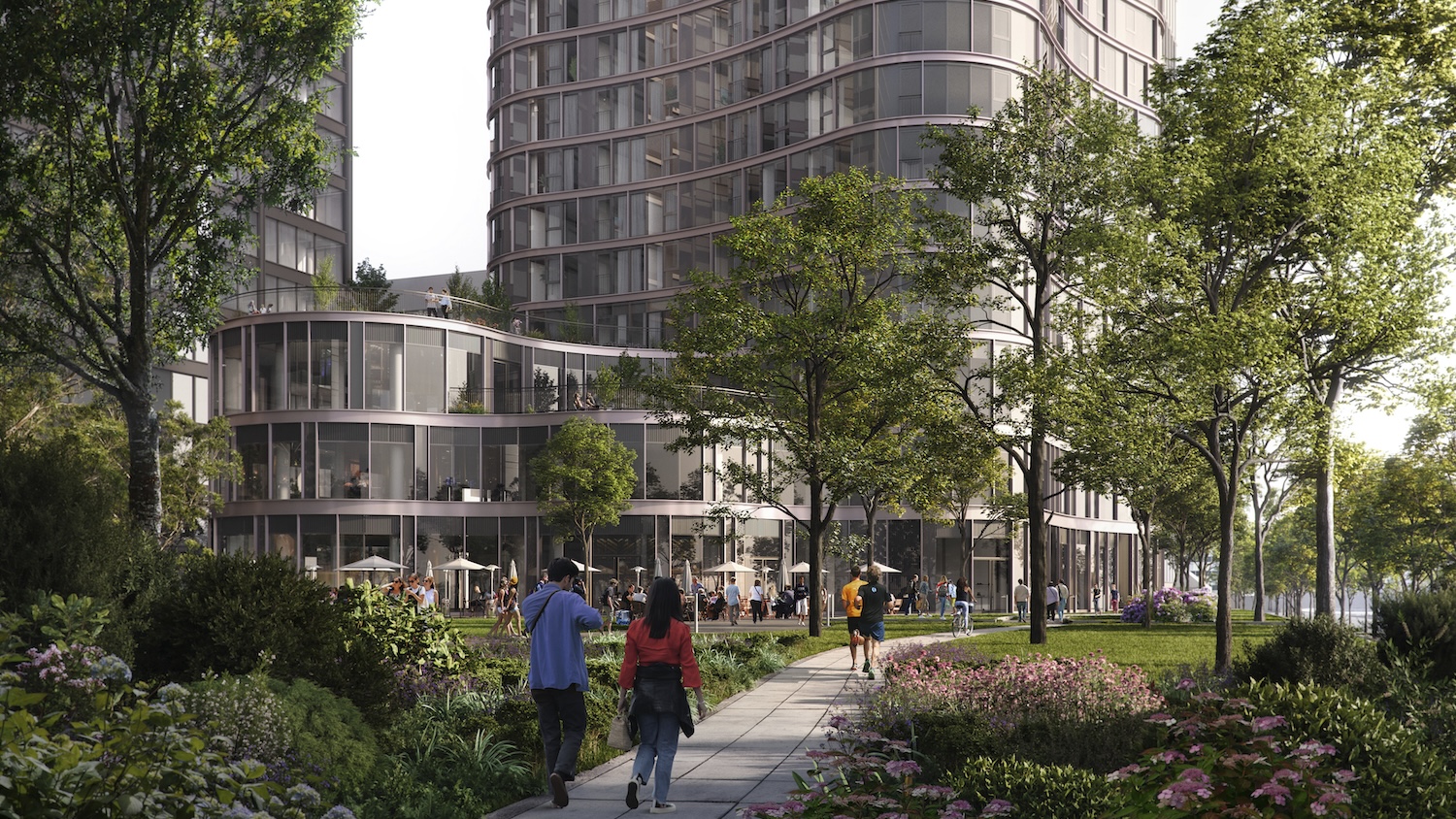
Canary Wharf Group’s (CWG) 40 Charter Street is a 52-storey, 552-unit residential tower within the Wood Wharf masterplan at Canary Wharf.
While CWG was simultaneously the project’s client, developer, contractor and estate manager, challenges around collaboration remained. CWG and its supply chain embraced a research-driven approach to technology with careful selection of technologies that inherently supported effective coordination.
It was important that any new software could integrate seamlessly with workflows already in operation using Asite as the project CDE and Autodesk Revit as the primary authoring tool.
The largest barrier to enabling effective collaboration is getting all the relevant parties to participate, either through lack of relevant skills or through not having access to the specific tool. To mitigate these risks, CWG incorporated several measures, including: the provision of software to all required stakeholders; ensuring equitable access to necessary tools; and targeted training programmes to equip users with the skills required to use the tools effectively.
Early resistance was encountered from some stakeholders accustomed to traditional methods. To address this, training and onboarding sessions were conducted to facilitate adoption and highlight the benefits of the new digital workflows. Integrating data across different platforms also posed an initial challenge, requiring customisation and API integration to ensure seamless interoperability between tools.
Despite these hurdles, the integration of the technologies exceeded expectations, leading to improved collaboration, reduced disputes and enhanced project transparency.
Heathrow’s When & Where Map | Costain/Heathrow
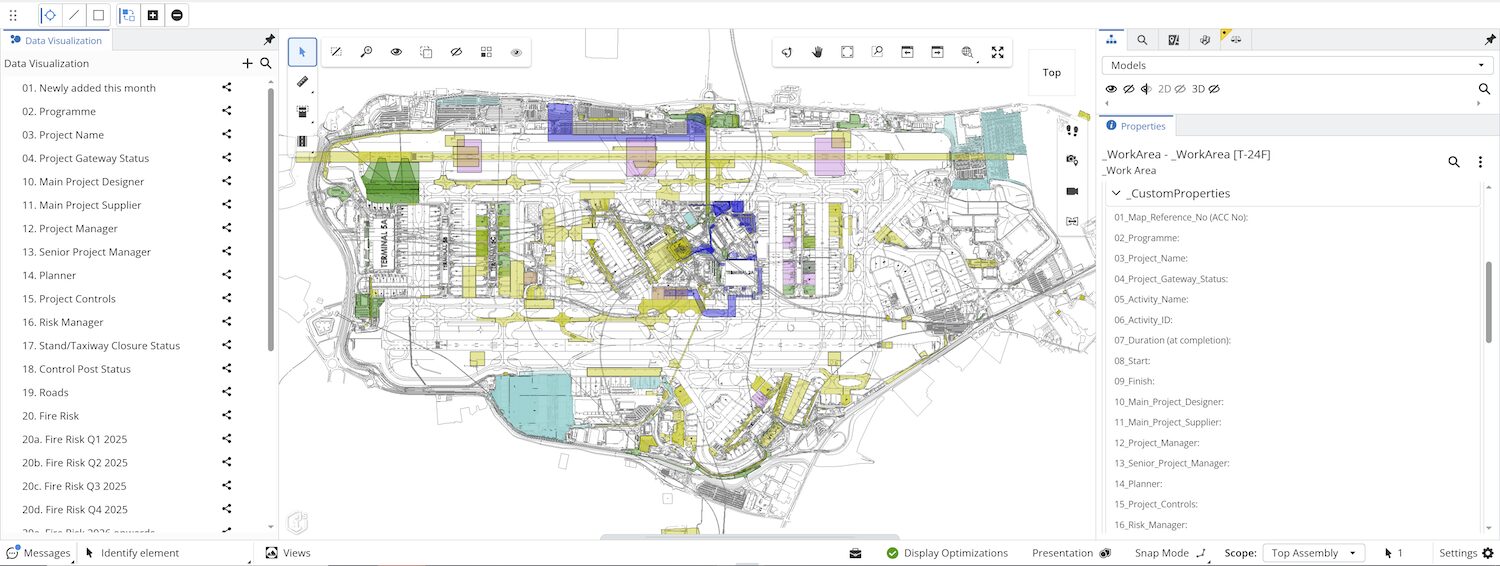
Costain has developed an interactive map with Heathrow, known as the When & Where Map. It allows Heathrow and its stakeholders and suppliers to see when and where construction work is planned throughout the airport. There are currently 160 projects showing their works in the When & Where Map, and more than 800 users.
Prior to this tool, everything was held in P6 schedules viewed only by Heathrow planners with nothing to visualise where the planned work would take place.
Collaboration is at the heart of the map. Costain coordinated with more than 20 different suppliers to provide information about their planned works. Suppliers are now empowered to identify their own coordination issues and resolve them themselves without having to rely on Heathrow to lead coordination efforts.
Coordination issues are now identified much earlier in a project’s lifecycle, at the point where meaningful changes can be applied to reduce the impact on other projects, or on the airport’s operation.
A two-hour training course was developed, which was designed to be fun and relevant and included a series of scenarios that required participants to navigate the map.
Costain has iterated the map since its inception, embracing feedback from Heathrow and its partners. The map now holds information on the fire risk of planned works, aircraft stand closures, control post closures, road closures and diversions, as well as maintenance work. This has improved productivity as the map is a single source of truth.
Old Newton School Project | GS1 UK/Natural Building Systems/Circuland/OrcaScan
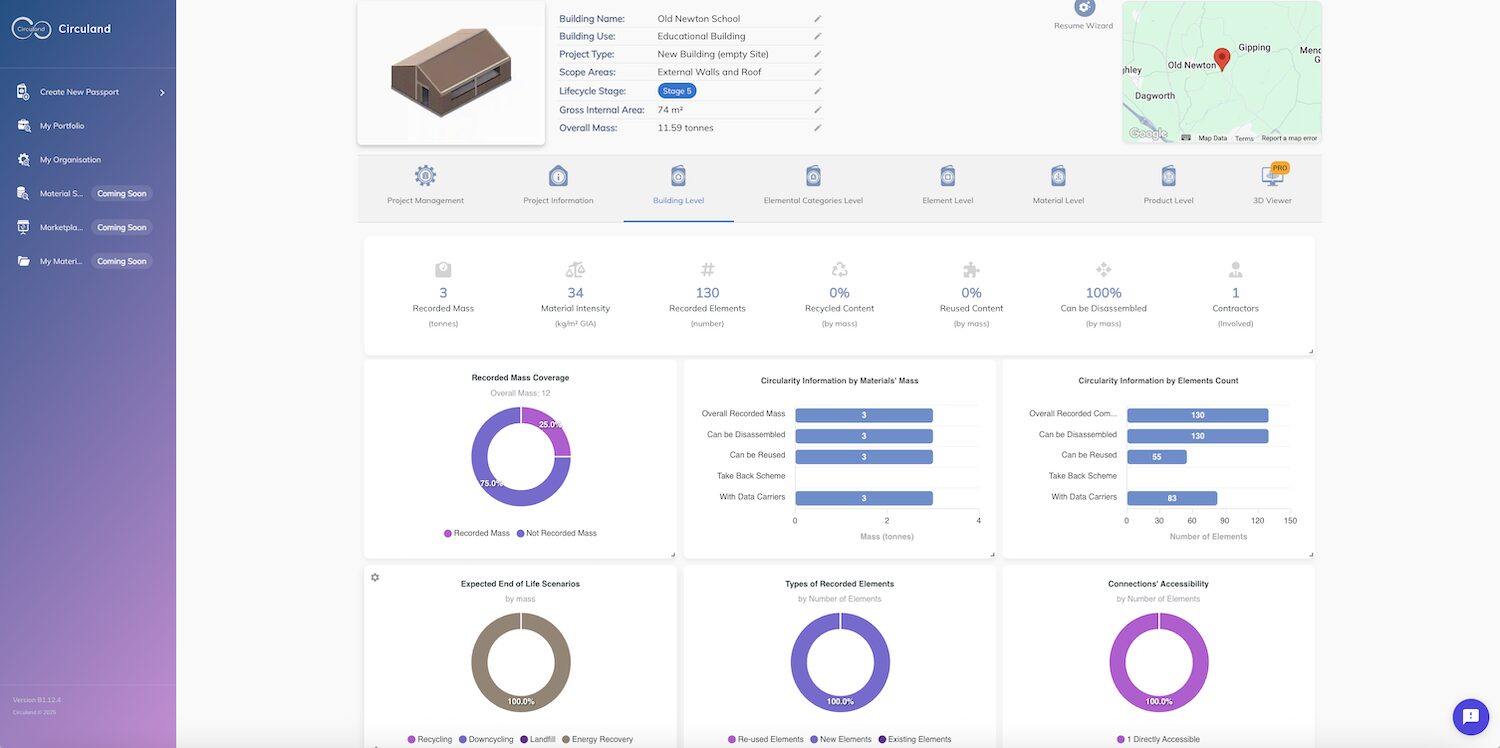
The new classroom at Old Newton School Project in Stowmarket needed a system to store and manage trusted data throughout its lifecycle. The school governors partnered with IF_DO Architects and Natural Building Systems to develop an offsite-manufactured solution aligned with their sustainability and health goals.
A key driver was ensuring excellent indoor air quality, free from VOCs and other contaminants, while also providing a long-lasting, flexible teaching space. Traditional and prefabricated methods were dismissed due to design limits, durability concerns, and air quality risks from petrochemical materials. Instead, a digital strategy was developed to enhance collaboration between designers, manufacturers and builders – ensuring real-time data accessibility and traceability.
A digital product passport (DPP) was created using the Circuland platform and GS1 GTIN (Global Trade Item Number) to uniquely identify materials. The project established an interoperable system for tracking materials, air quality and building performance, supporting seamless collaboration throughout the supply chain, from design to long-term use.
RFID tags were applied to building materials, leading to improved, accurate data sharing among stakeholders, enhancing decision-making and sustainability outcomes.
The DPP is accessed by scanning the GS1-powered QR code found on the material. These next generation QR codes, supplied by OrcaScan, have the GTIN embedded. The QR links to the DPP, showing key product and sustainability details.
By integrating digital tracking and standardised data sharing, this project sets a precedent for a more collaborative, transparent, and sustainable construction industry – creating a replicable model for the future.
Operational Delivery of a Golden Thread | Bouygues UK/Westminster City Council

The necessity for digitalisation on a significant, complex residential project arose from early engagement between the Bouygues UK BIM and digital construction team and Westminster City Council’s digital and FM team. The two teams collaboratively analysed the need for prioritised, structured, data-rich asset information to support FM and handover requirements.
Westminster City Council faces critical challenges managing its extensive property portfolio post-Grenfell, including comprehensive golden thread documentation.
This initiative brought together key partners across the asset lifecycle: Westminster City Council as client, consultant Digitize Consultants, Bouygues UK as the main contractor, MEP subcontractor HE Simm, and Activeplan, the O&M platform provider.
This collaborative ecosystem ensured seamless integration of asset data while aligning design, construction and FM requirements through a unified digital framework.
The research and development strategy involved systematic evaluation of existing workflows to identify improvement opportunities. Stakeholder workshops were undertaken to understand pain points and requirements, leading to the development of BIM and IFC-based workflows that automated data extraction. This approach significantly reduced dependency on error-prone manual data entry, while ensuring data accuracy and consistency.
The digital twin offers Westminster an opportunity to implement data-driven decision-making through comprehensive virtual representations of physical assets. This approach enables lifecycle optimisation, reduced operational costs and enhanced service delivery based on actual performance data rather than arbitrary timelines.
Scottish Water’s Digital Leadership Hub | Scottish Water/Caledonia Water Alliance/RSE/ESD/George Leslie/Morrison Water Services/WGM Engineering/Galliford Try
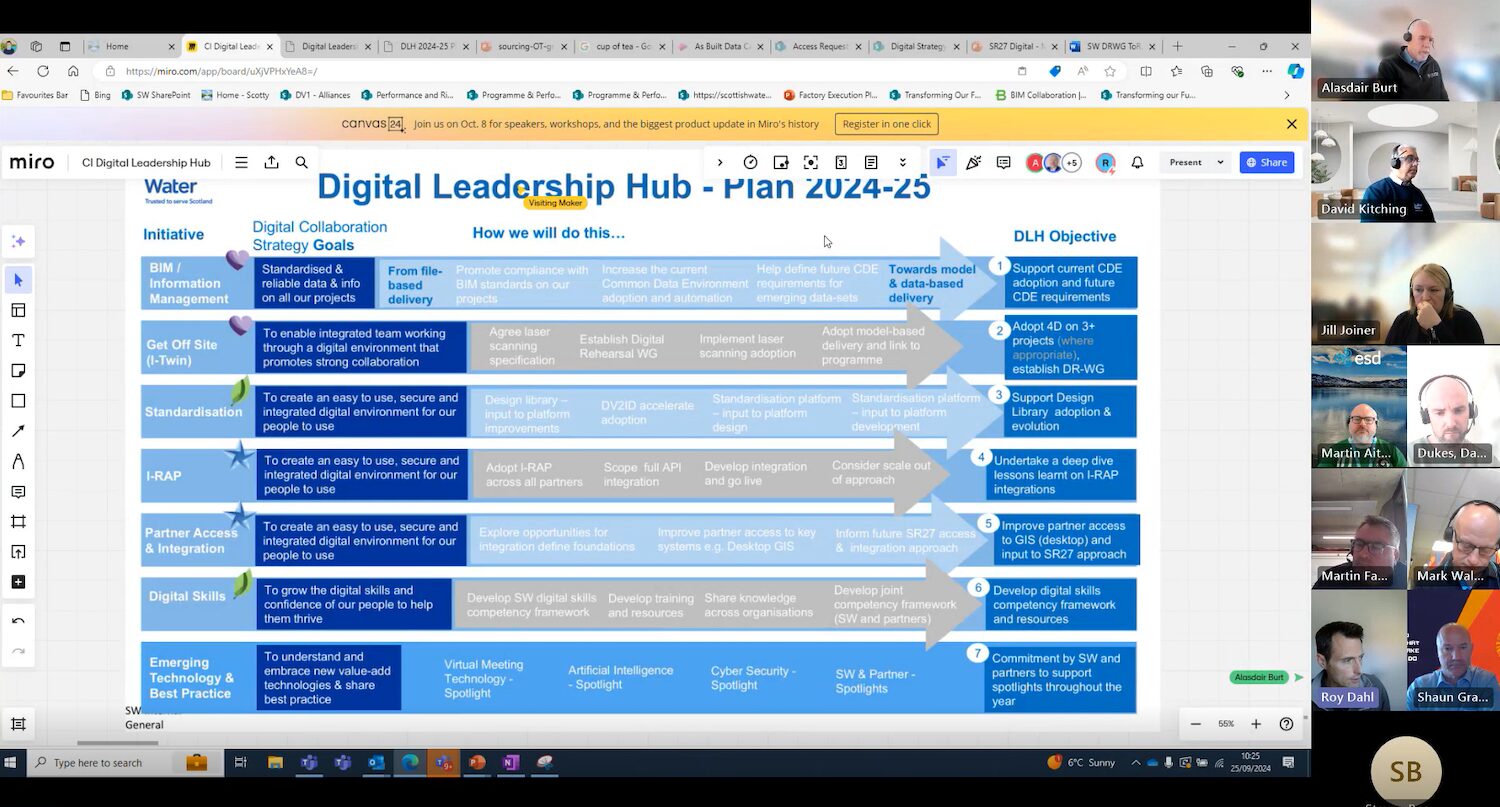
Scottish Water identified a previously fragmented approach to digital transformation across its delivery partners and realised that a step change in collaboration was needed.
The solution was the establishment of a digital leadership hub to set direction, share knowledge and deploy best practices, serving as a collective guiding mind across the digital transformation of Scottish Water and its supply chain.
A pivotal aspect of the strategy was proactive engagement with the supply chain, where Scottish Water shared its digital strategies and sought feedback. By facilitating open discussions about successful practices and the challenges encountered, Scottish Water gained invaluable insights that shaped its decision-making process.
Scottish Water prioritised breaking down silos across the delivery teams. By eliminating barriers from the supply chain, it encouraged the integration of diverse perspectives, which led to more innovative solutions and a unified approach to digital transformation.
To further refine its strategic planning, Scottish Water organised a series of workshop sessions aimed at developing a cohesive solution architecture. These workshops brought together stakeholders from various teams, enabling the brainstorming and design of scalable solutions. This participatory approach not only fostered buy-in from all participants, but ensured that the solutions were practical and directly informed by the organisation’s needs.
Digital access to existing utilities allows for instant data retrieval across the supply chain. Integrating clients’ GIS data enhances spatial analysis and decision-making. Streamlining data capture processes ensures accuracy, while standardising laser scanning specifications promotes consistency in asset capture.
A key achievement has been the enhanced accessibility to the client’s asset data, which facilitated more informed design decisions. This improvement translated into a remarkable reduction in project costs, estimated at around 15%.
Smart Motorways Programme Alliance | Fluor/Jacobs/WSP/Costain/Balfour Beatty/BAM Nuttall-Morgan Sindall JV/National Highways
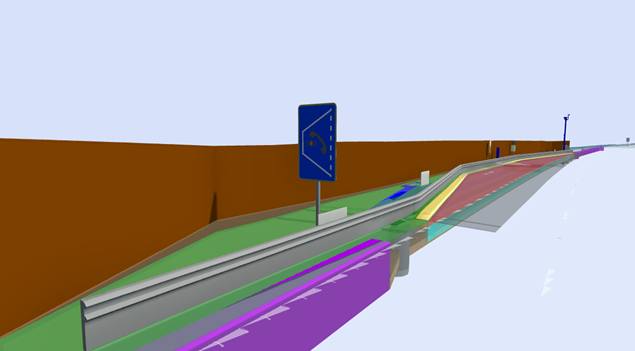
The Smart Motorways Programme Alliance operates on Project 13 principles and comprises National Highways as the client, Fluor responsible for production management, Jacobs and WSP handling digitally-enabled design, and Balfour Beatty, Costain and the BAM Nuttall-Morgan Sindall JV as onsite assembly partners. Collectively, they work with more than 100 suppliers, ranging from SMEs to global players.
Their challenges included:
- facilitating secure, collaborative sharing and information management;
- integrating the UK BIM Framework across the seven alliance partners and the many varied programmes;
- overcoming different legacy systems/corporate policies and levels of digital maturity;
- fostering a culture of unprecedented integrated collaboration, communication and transparency that promotes data-led insights and decision-making for greater productivity/efficiencies, along with enhanced quality and unified governance; and
- encouraging innovation and programmatic approaches for successful delivery while driving safer, more efficient, greener solutions that simultaneously maximise road user benefits.
These challenges were addressed by digital engineering and information management specialists drawn from the alliance partners, operating as one team.
They developed the Alliance Information Management System, a business management platform where processes are centrally referenced, including a common coding standard for documents, geometrical and alphanumerical data.
Effective communication was key, achieved through an information execution plan and a technology stack, which guided the implementation of current and new technology while ensuring standards compliance. The Alliance M365 Collaboration Environment underpins this strategy, providing a secure, neutral/agnostic platform for information/data sharing.
As of January 2025, SMP Alliance had realised £97.43m assured efficiencies (with forecast of £144.14m) on programmes totalling £1.2bn. Digital solutions helped reduce pre-construction times by up to 60%.
Celebrate with the best
The winners will be revealed at the gala dinner on 1 July at the Brewery in London.
You can join the shortlisted entrants by booking your seats at the awards. There is an early bird discount for those who book tables before 16 May.
The Digital Construction Awards are organised by Digital Construction Week, Construction Management and the Chartered Institute of Building. The first sponsor to be announced is Bluebeam.
To find out more about the Awards, visit digitalconstructionawards.co.uk.