The Digital Construction Awards attracted 165 entries this year, 84 of which have been shortlisted. Here, we detail the shortlisted entries for the Digital Collaboration of the Year award, sponsored by Bluebeam.
Digital Collaboration of the Year recognises the best use of digitalisation/digital methodologies and/or technologies to enhance collaboration between two or more organisations on a project, at any level of the supply chain. Six entrants – including Balfour Beatty, WSP and Accenture – made the shortlist.
EDF UK/Accenture/Dassault Systemes | Digital Twin Implementation at Hinkley Point C
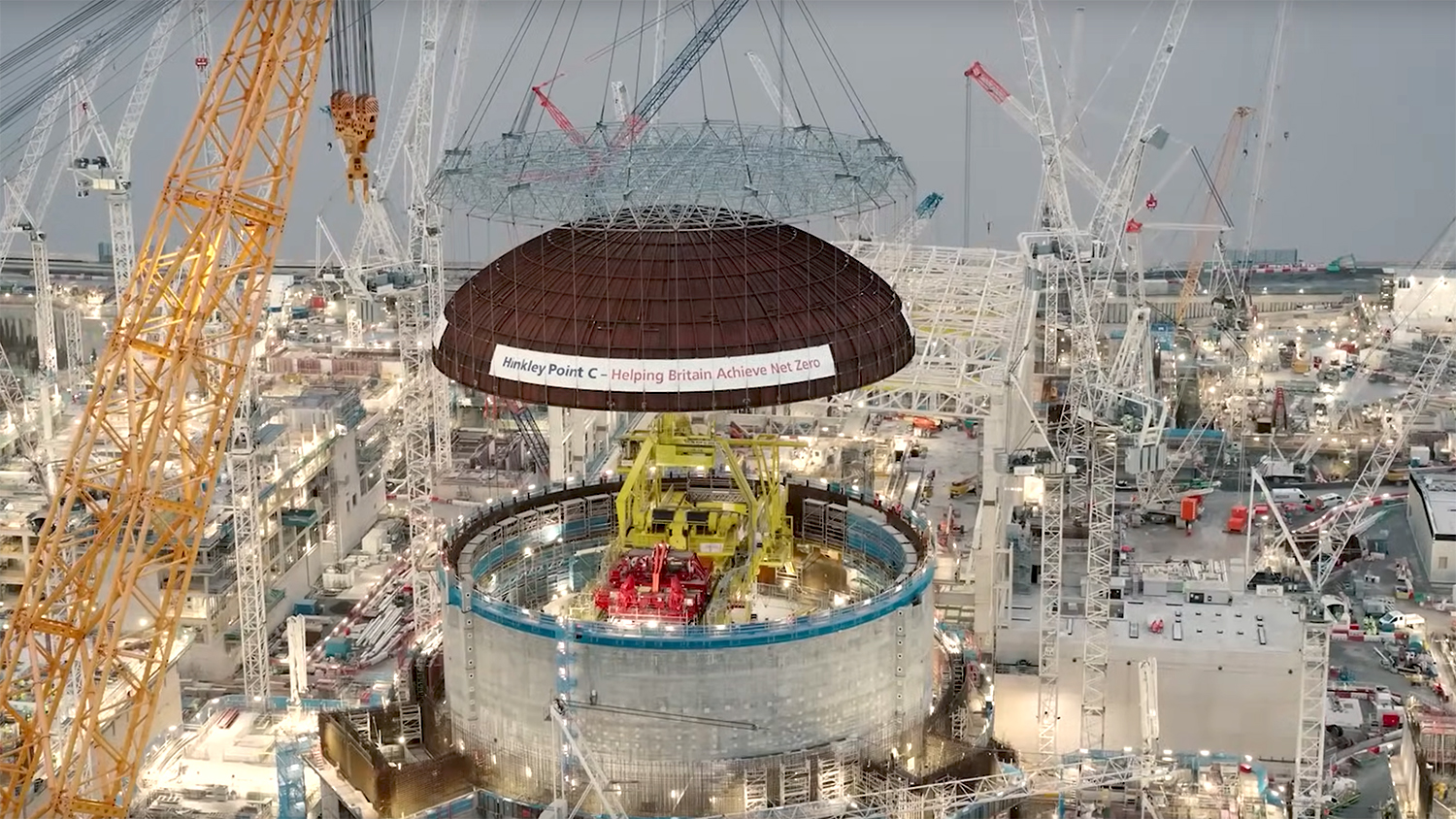
Hinkley Point C (HPC), Europe’s largest construction project, has been working with Accenture and software provider Dassault Systemes for more than three years to modernise end-to-end construction and engineering processes with the implementation of 3DExperience.
The team is aggregating data from siloed systems to create HPC’s golden thread of what it claims is the world’s first fully digital nuclear power plant. The solution has enduring capabilities for HPC’s entire plant lifecycle, with opportunities for replication at the Sizewell C nuclear power station, reducing cost and time to commission.
This technology has also increased data accessibility for the civil and mechanical electrical HVAC construction phases at HPC and will be fundamental to commissioning the nuclear plant. In the past year, Accenture has onboarded more than 2,500 users across HPC and the global supply chain (comprising more than 250 tier 1 suppliers), moving from multiple legacy systems to one way of working.
This transition required close collaboration across the business to challenge longstanding ways of working in the industry, moving users from document-centric to data-centric practices. A top-down approach to collaborative working with the supply chain in both the construction and commissioning phases resulted in meeting time and cost targets which can be replicated within future projects.
The suite of digital tools deployed at HPC has supported improved collaboration by promptly informing relevant stakeholders involved in the project and by driving process progression through the use of notifications and system workflows.
HS2/SCS JV/Queenswood | HS2 Mandeville Road Ventilation Shaft
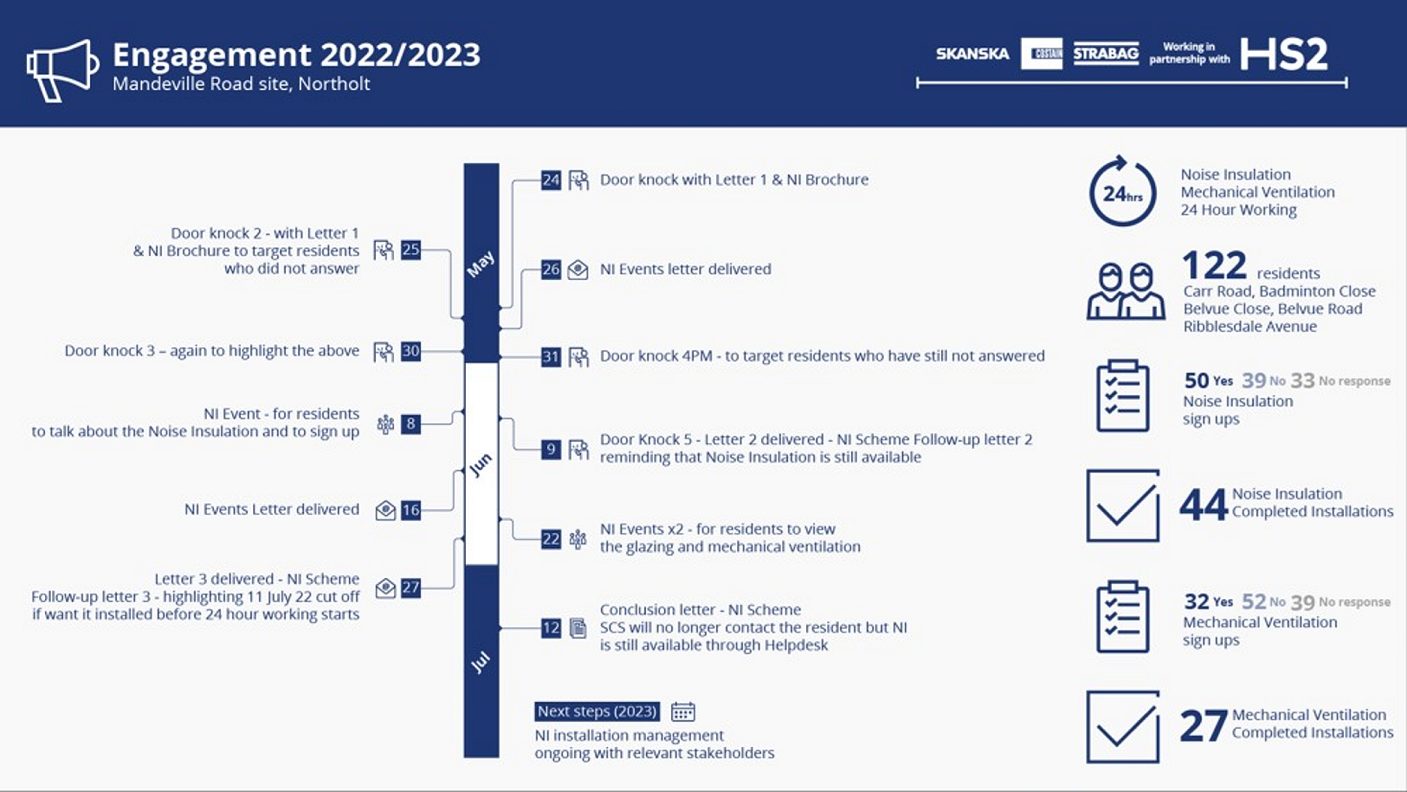
Queenswood was commissioned by the Skanska Costain Strabag JV (SCS) to help with local community and stakeholder engagement during the construction of a ventilation shaft on Mandeville Road near Northolt tube station in the London Borough of Ealing.
The community and the local authority were particularly sensitive to the proposal because 24/7 working was not included as part of the HS2 Act.
SCS commissioned Queenswood to work closely with its suppliers (Selectaglaze and Adept) to help coordinate the rapid deployment of noise insulation (NI) and mechanical ventilation (MV) to affected properties surrounding the ventilation shaft construction site, which was to be impacted by 24/7 works.
The team led by Queenswood successfully engaged with the residents affected by working collaboratively and using digital communication tools to keep the local community fully appraised of the process. In addition to holding community engagement events at the local community centres, the team developed a visual digital model of the noise impacts.
Using EqMax noise modelling data, Queenswood reinterpreted the data over a typical 24-hour period to show a visual representation of the ebb and flow of noise to be expected, colour-coded in contours breathing in and out from the site, set against a noise scale of recognisable everyday items (such as a desk fan or a lawnmower) so residents could interpret what the colour meant to them when seeing the map of their street within the coloured noise contours. Residents could access the video via a QR code sent to them by letter.
This resulted in the installation of secondary glazing NI and MV in 50 properties without a single complaint and within the allotted Act of Parliament timescales. Additionally, there were no delays to the project.
Balfour Beatty/Sandwell and West Birmingham Hospitals NHS Trust/Arup/Gleeds/Stride Treglown | Midland Metropolitan University Hospital
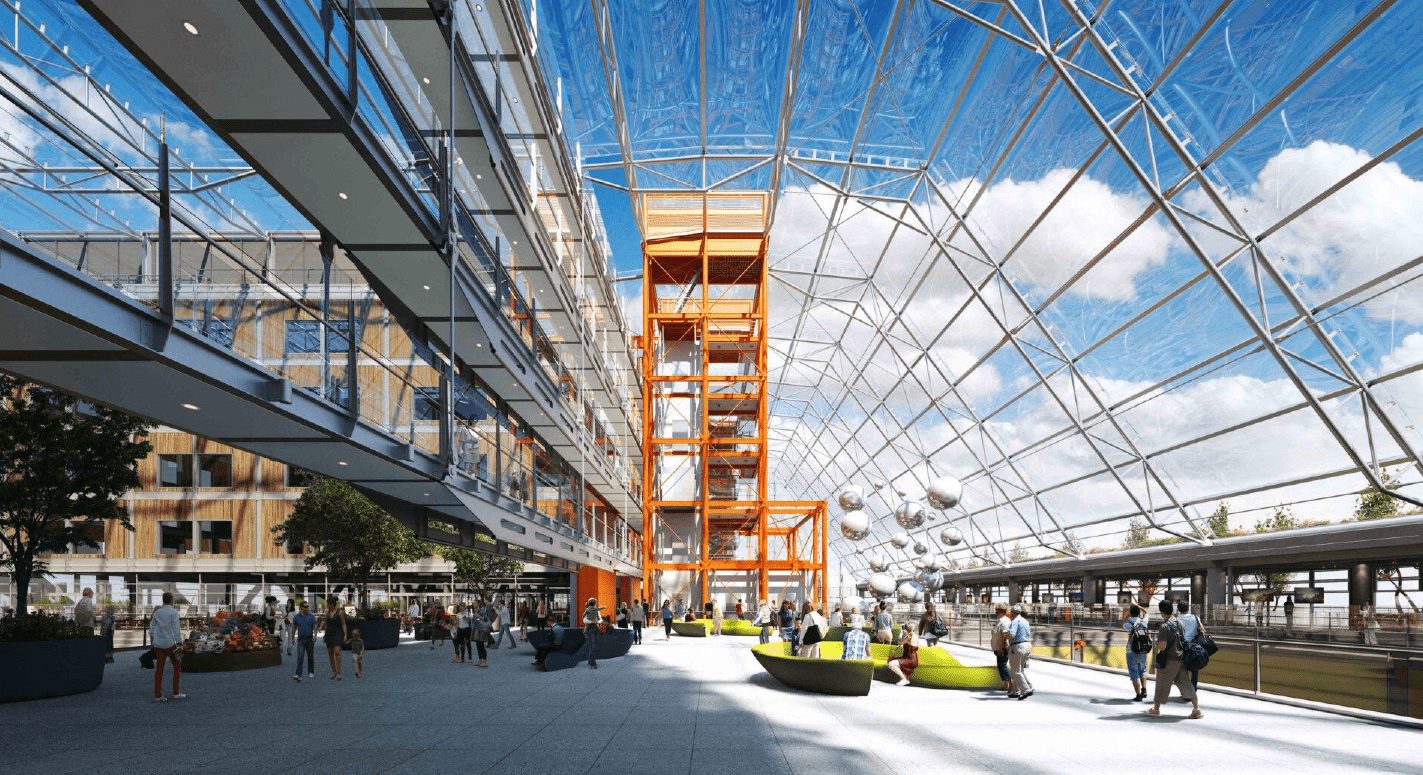
Balfour Beatty used its #DigitalByDesign digital strategy to facilitate and foster collaboration for the delivery of the complex Midland Metropolitan University Hospital.
The contractor was appointed to deliver the state-of-the-art hospital following Carillion’s collapse in 2019. At 85,924 sq m across 10 storeys, the building is the largest acute care hospital in the region and has a capacity of 675 beds and 13 theatres.
The implementation of Balfour’s #DigitalByDesign strategy supported the project completion, commissioning and handover stages, as well as helped create the golden thread for this complex facility. This strategy included the deployment of a data-centric approach and the use of software tools such as BIM 360 Field, Revit integration and OpenSpace for visual record keeping.
The use of digital tools as part of the wider contractor’s digital strategy resulted in teams collaborating more efficiently as they could story and find information easily without having to maintain spreadsheets. Automated reports were ready by the end of the day in time for the teams’ early morning meetings.
Balfour’s #DigitalByDesign strategy improved collaboration between teams, which in turn resulted in greater operational efficiency. The use of OpenSpace for visual record keeping also boosted collaboration between different stakeholders, especially between designers and trade contractors.
NHS Lanarkshire/WSP Digital Services/Currie & Brown/Keppie Design | Monklands Replacement Project
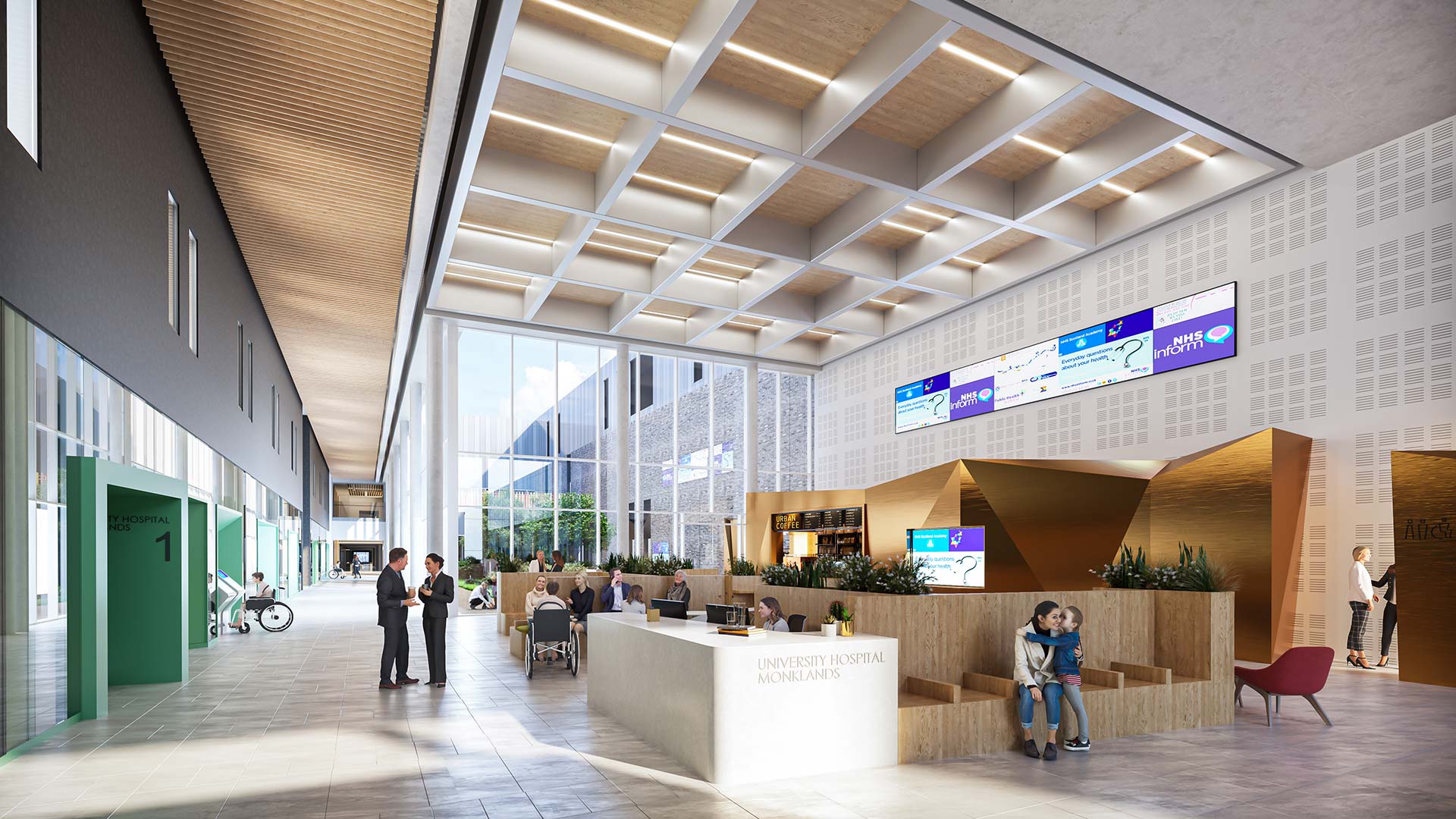
A team led by WSP Digital Services is using the BIM360 platform to enhance communication and collaboration at the Monklands Replacement Project – a scheme to replace the 1970s hospital with Scotland’s most advanced digital hospital.
WSP Digital Services worked with NHS Lanarkshire and the project delivery team to digitally transform the stakeholder review process, streamlining the approval of various departments and rooms as part of the RDD process.
A hybrid approach was adopted to address the challenge of maintaining a digitally auditable record for stakeholders while including non-digital clinical staff. This involved a digital platform with allowances for non-digital stakeholders. In-person workshops were linked to virtual participation, facilitated by the recording, and tracking of commentary within the digital process.
Collaborative workshops with the client, project management, and architectural teams were conducted to understand the current process and design a new electronic stakeholder review process using BIM360 features.
Follow-up meetings involved both digital and non-digital stakeholders to confirm acceptance, with two teams ensuring a comprehensive paper trail, aligning with NHS assurance policies. Digitisation enabled a rapid and well-executed turnaround time for reviews and completion of actions, which would have been impractical without this technological enhancement.
Throughout the design of the building, NHS Lanarkshire and the wider design team have used cloud-hosting models to allow for greater collaboration between the designers.
United Utilities/MWH Treatment, Stantec, J Murphy & Sons | Oswestry Water Treatment Works
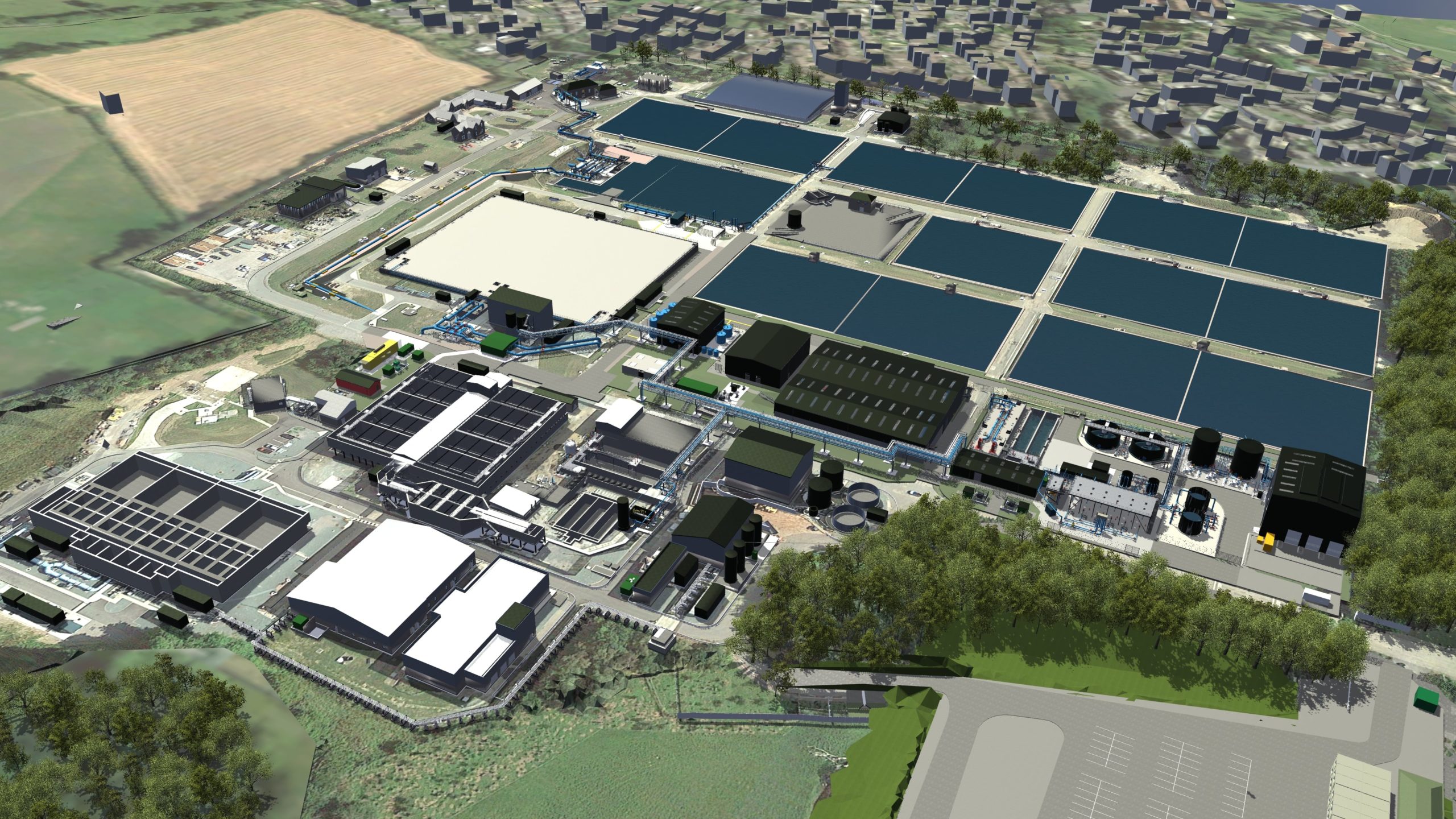
The team at Oswestry Water Treatment Works faced a significant challenge to deliver a £145m capital investment project in 33 months while maintaining a live existing site with uninterrupted supply to United Utilities customers.
The team tackled this head-on by adopting a digital first approach and fostering full collaboration across a complex project and network of more than 20 subcontractors, the client and suppliers. In addition, the project has also adopted a ‘one team culture’ among all parties.
This approach was achieved by adopting key digital initiatives to better engage with client operations, internal teams and supply chain delivery teams, and by creating a digitally inclusive space that fosters communication and open collaboration.
The technology used by the project team includes 3D models; design for manufacture and assembly; virtual reality; digital rehearsals, 4D modelling and digital RAMs; Pix4D; mView+ interactive site induction; digital site quality control records using inspection test plans and field management tools; Pix4D for photogrammetry capture for production controls and underground services; and Hilti tracker for asset registration and delivery assurance.
The digital rehearsals and 4D modelling hosted by the project team were one of the most important tools to advance collaboration. They promoted consideration of constructability and potential clashes between disciplines and helped identify programme risks and sequences that mitigate those risks.
The digital-first approach at Oswestry has resulted in successful interoperability and a collaborative ecosystem between the client, contractors, subcontractors and the supply chain that has been driving tangible benefits to this complex project and which will allow the team to achieve the challenging timescale to deliver it in 33 months.
Network Rail/Method Grid | The Digital PACE Framework
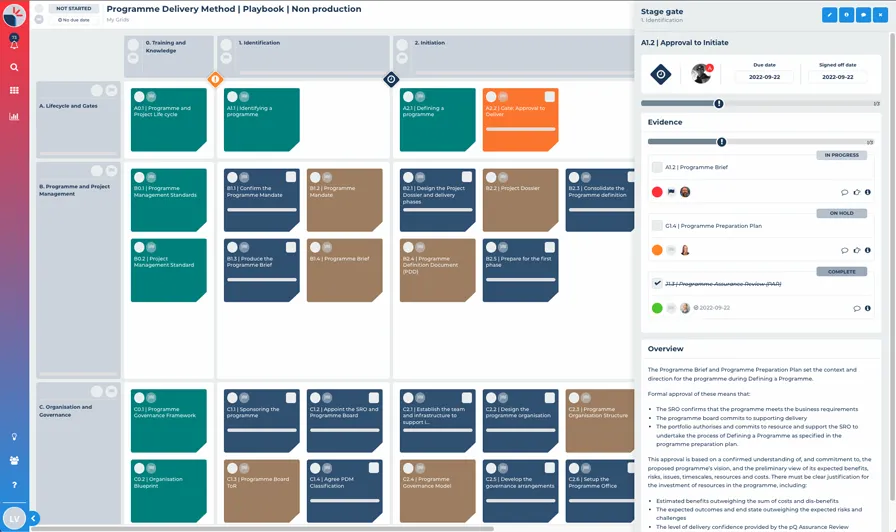
Method Grid and Network Rail collaborated throughout 2023 and into 2024 on building the Digital PACE (Project Acceleration in a Controlled Environment) Framework to improve how Network Rail delivers projects.
This digital resource – as deployed on the Method Grid AI-powered knowledge and project management platform – is now publicly available to all rail project management professionals in the UK.
The use of this technology radically enabled the entire UK rail industry to collaborate effectively in the delivery of the ambitious Control Period 7 construction investment plan (£43.1bn over five years) by enabling genuine, multi-supplier collaboration on one of the country’s most critical, strategic programmes of work.
Method Grid’s collaboration with Network Rail involved integrating existing PACE standards, products and guidance resources into the new digital playbook. The platform’s AI empowerment further enabled the joint team to build and enhance this deep, quality knowledge resource in a few months – expediting the ‘speed to value’ aspect of such work.
Method Grid claims that this empowerment expedited the time to quality outcome by a factor of five (i.e. five times as fast as conventional, fully manual renditions of a complex playbook build).
The project was also a vanguard of digital innovation in the context of other UK public bodies facing the comparable challenge of harnessing technology to genuinely ‘force multiply’ all actors across their construction supply chain.
Celebrate with the best
The winners of the Digital Collaboration of the Year category, alongside the victors of the other 12 categories, will be revealed at the awards dinner on 2 July at the Brewery in London.
You can join them by booking your places at the awards.
The Digital Construction Awards celebrate best practice and reward innovation in the application of information management and digital technology in the built environment sector.
The awards are run by Digital Construction Week, the Chartered Institute of Building (CIOB), and Construction Management and BIMplus.
Awards sponsors include Bluebeam, Procore, Revizto and the CIOB.