The Digital Construction Awards attracted 165 entries this year, 84 of which have been shortlisted. Here, we detail the shortlisted entries for the Best Use of Data On A Project award.
The Best Use of Data On A Project recognises use of data and information to enhance design, construction processes or asset management on a building or infrastructure project. Seven entries have made the shortlist.
Skanska UK/National Highways | Delivering data-driven construction digital twins in highways
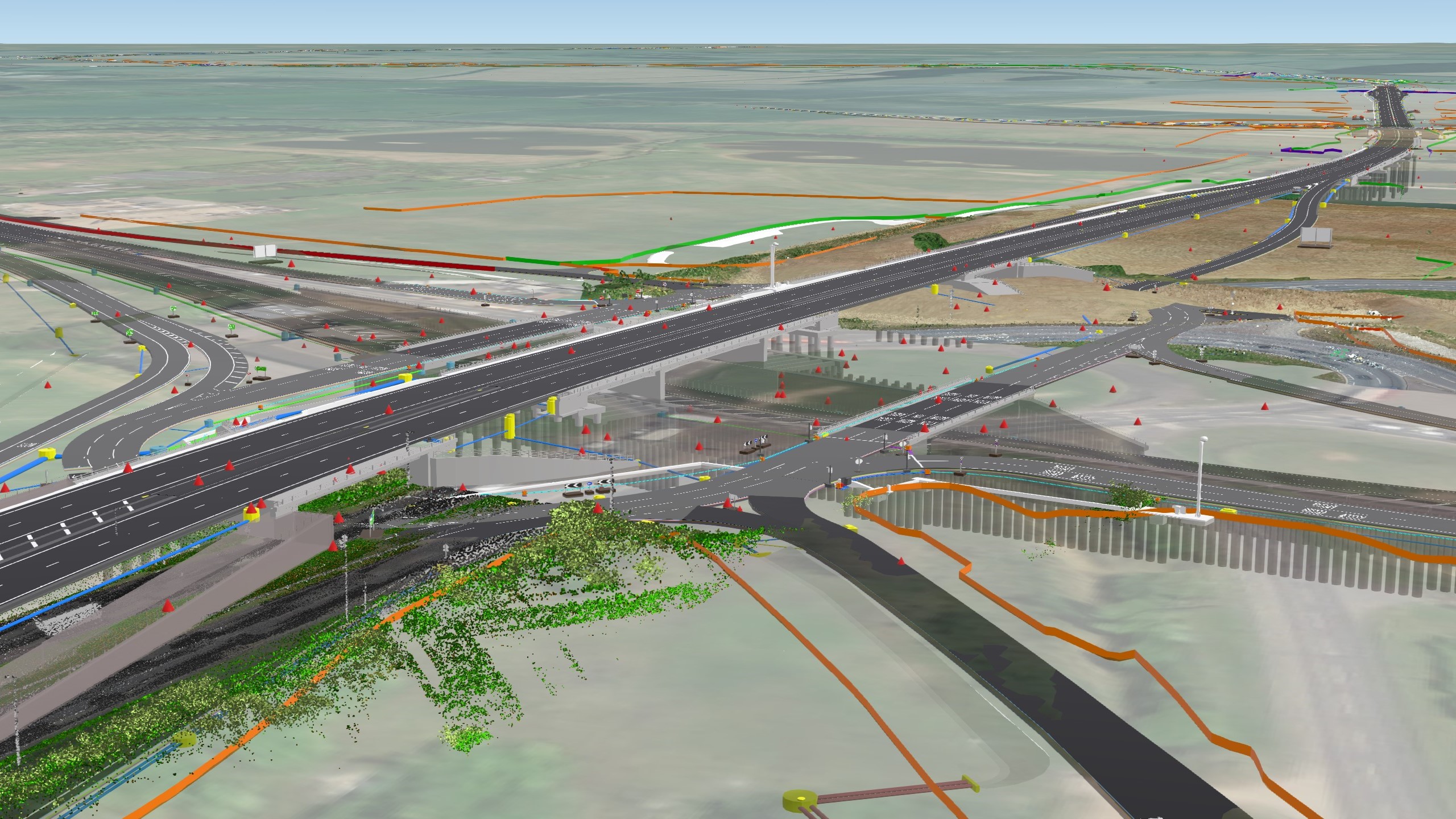
Skanska UK has developed an agnostic, data-intelligent construction digital twin to enhance productivity on a major National Highways project in Eastern England – the A428 Black Cat to Caxton Gibbet Improvement Scheme.
The engineering complexity and multiple stakeholders involved with this £1bn project, which will include a 10-mile dual carriageway from St Neots to Caxton Gibbet, convinced Skanska of the need for a strategic approach towards data-driven delivery.
Its strategy set three core principles: data should be for the delivery teams; there should be a designated CDE; and data should enable construction decision-making. The strategy was created by a ‘data council’ that brought together representatives from across the project: construction, quality, health and safety, environment, client side, supply chain and digital.
Skanska’s digital and data strategy on the A428 is founded on the principle of agnosticity, which enables integration and a consistent flow of information across digital systems, including GIS and business intelligence, which are connected through the project’s CDE.
Creation of the construction digital twin of the project was founded on two information streams – BIM and GIS. The digital twin has driven decision-making through location-intelligent workflows: for example, automated clash detection of underground services such as utilities.
Benefits realised from the strategy include £1.5m in time and cost efficiencies to date from digitalisation, risk reduction and productivity gains. Skanska forecasts it will reduce the asset handover period from six to two months upon practical completion, resulting in more than £2m in savings.
iDEA | King’s College London Vantage Model
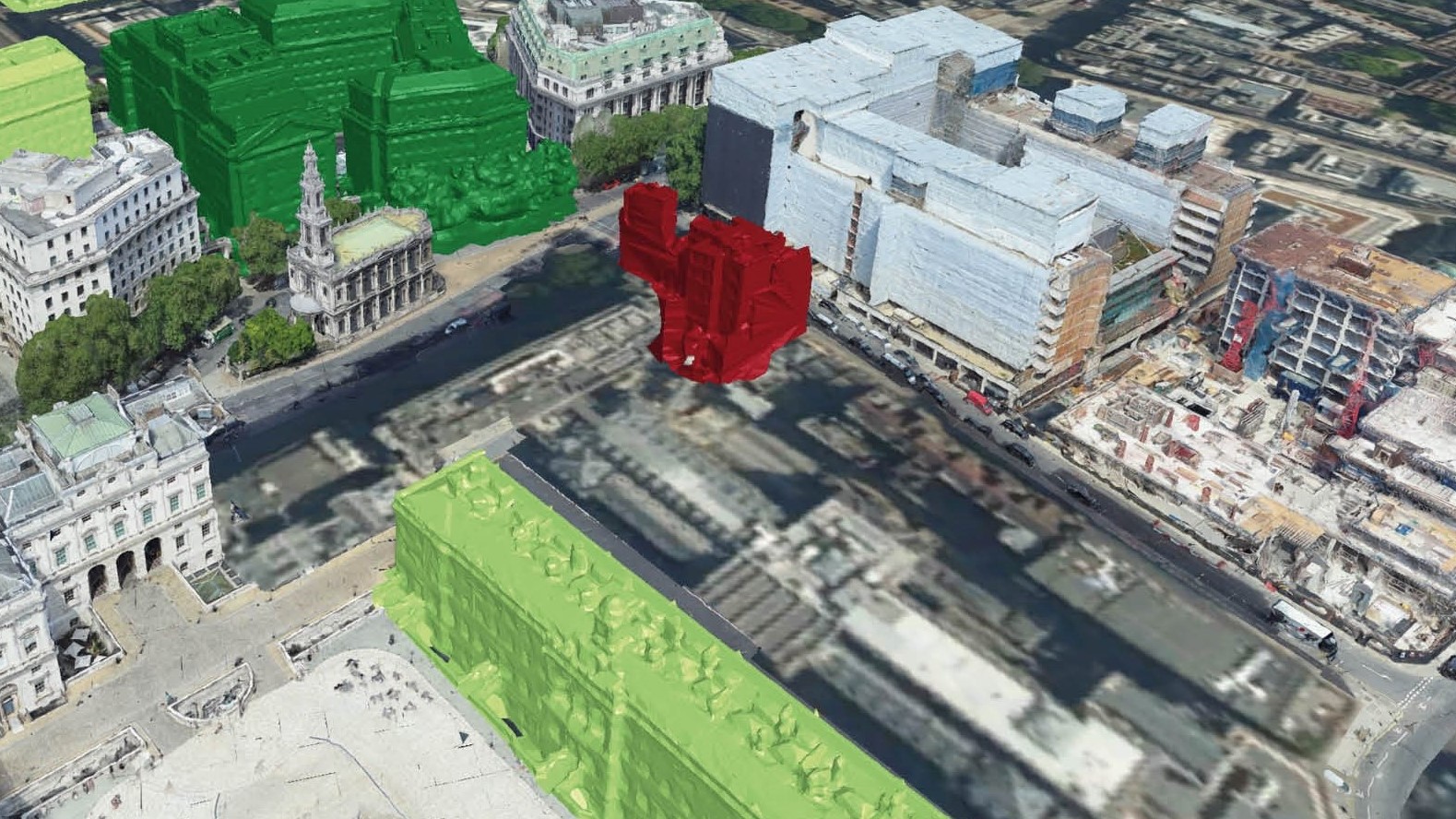
iDEA, a multi-disciplinary design consultancy, has been collaborating with King’s College London (KCL) for the past four years, exploring new digital technologies that could support the delivery of a long-term campus masterplan to improve and optimise a complex estate in central London.
One of the primary digital technologies that iDEA and KCL have been working with is Vantage, an estates visualisation platform that aggregates core campus data. Vantage is a multi-layered and 360-degree ‘command centre’, from which millions of combinations of data analysis can be achieved in one place at one time. Using Vantage, iDEA developed a digital campus platform, built in the Unity game engine.
This provides an interactive means of storytelling and data analysis, incorporating information such as: locations of campuses and buildings; building condition; functional suitability; construction date; and 3D representations of buildings.
iDEA has also developed a bespoke open-source API that allows data from associated tools such as Register (a timetable analysis tool) and Forecast (a spatial scenario planning tool) to connect with KCL’s existing Planon data, creating a single-source digital twin of the whole campus.
With a complete 3D build of KCL campuses, iDEA has provided access to all of the relevant occupier, work settings and occupancy data for whole university. The model is used by the KCL estates team as an engagement and communication tool, and to analyse the estate and scenario plan. Longer term, there is the possibility that KCL’s architecture and construction students could use iDEA’s tools to understand how carbon emissions from the built environment can be reduced.
Disperse/Canary Wharf Group – Wood Wharf Development
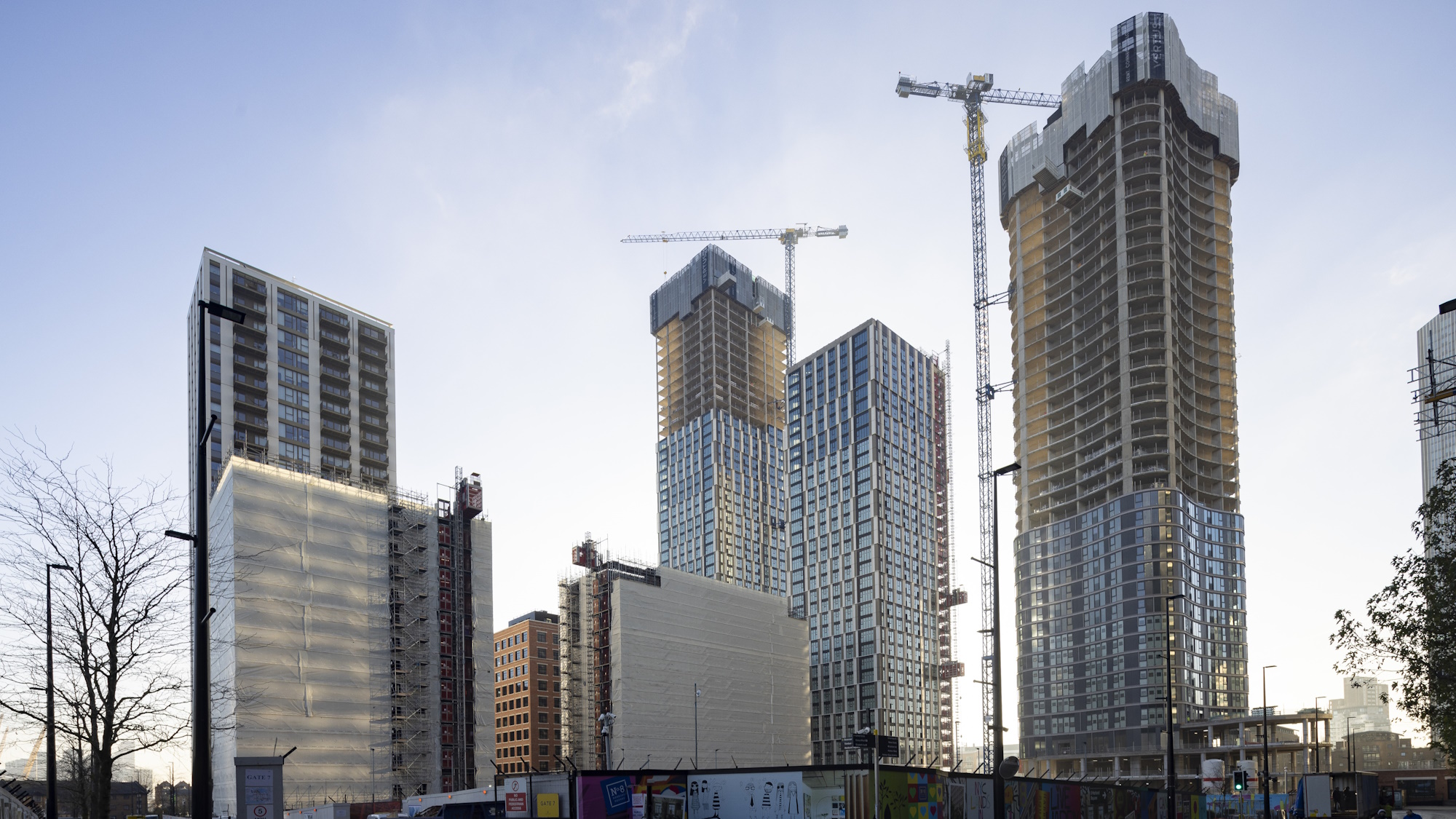
Canary Wharf Group appointed construction tech firm Disperse and its Impulse solution to manage data on the vast Wood Wharf Development, a 9ha site comprising seven residential towers, retail and office space.
Challenges include ensuring effective communication among stakeholders, maintaining consistency and standardisation across different phases of the project, and managing the extensive amount of data generated, including the standardised photo capture sequence and early issues warning notifications.
Innovative features of the Impulse system include:
- Full site scanning. A standardised approach to capturing project progress through photos ensures consistency and comparability across different phases and locations.
- Progress tracking. This covers up to 670 task components, providing a holistic view of the entire development process, so stakeholders have a comprehensive understanding of the project’s status at any given time.
- Reporting. Progress tracking is documented and delivered to Canary Wharf Group every week, presenting details of actual progress vs planned progress for each trade at unit, floor, and building levels.
- Issue detection. The system alerts stakeholders to deviations from the planned schedule or budget in real-time and enables swift action to address potential issues before they escalate.
The implementation of Impulse has reduced the turnaround time for progress reports for the site from a week to 48 hours. The incorporation of 360-degree images in Impulse streamlines the creation of progress baselines, facilitating more efficient handovers to new contractors.
The weekly insights provided give a clear understanding of project dynamics and the context behind numerical data. Construction accuracy has improved, risks diminished, and significant time and cost savings were realised for Canary Wharf Group.
GMI Construction | ProjectData
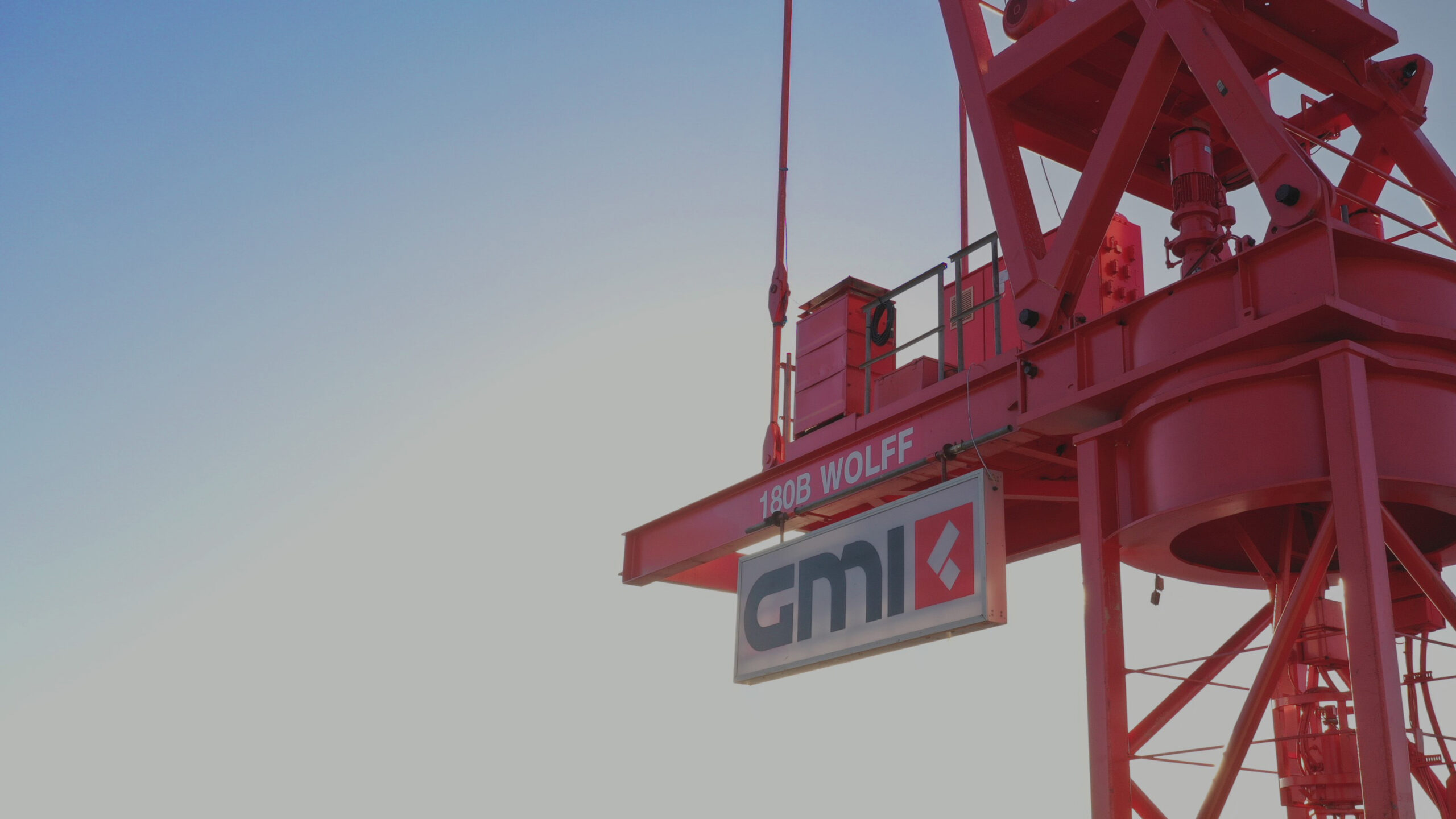
ProjectData is a new app developed and launched by SME contractor GMI Construction, which aims to collate data from across the business and help optimise the management of its projects.
Previously, GMI didn’t have the processes, systems or structure in place to collate high-level data and needed a solution that worked for more than 250 employees and 30 live construction sites at any given time.
The business looked at how global brands gather data, attending key technology events such as the Microsoft Business Applications Summit in Atlanta, USA, looking at data visualisation and analytics tools.
Following this process, GMI decided to develop a system through Microsoft Power BI, which presented greater integration opportunities. The new system implements and livestreams data from third-party systems used by the business, including Workwallet, Viewpoint/Trimble, Biosite, Microsoft and Elecosoft.
ProjectData was introduced into the business late in 2023, being trialled in the offices initially and then rolled out to each of the contractor’s projects. It pulls together a range of data, including project programmes, cashflow, health and safety, quality assurance, sustainability, and even monitors GMI’s Considerate Constructors Scheme scoring.
The system is customised to work on individual construction sites, with the goal of pushing project teams to maintain and improve programme efficiencies while forecasting and maintaining budget.
GMI has invested more than £5m on the development and rollout of ProjectData, primarily through the technology process improvement and upskilling its workforce.
Integrated Health Projects/Buildots | Royal Bournemouth Hospital
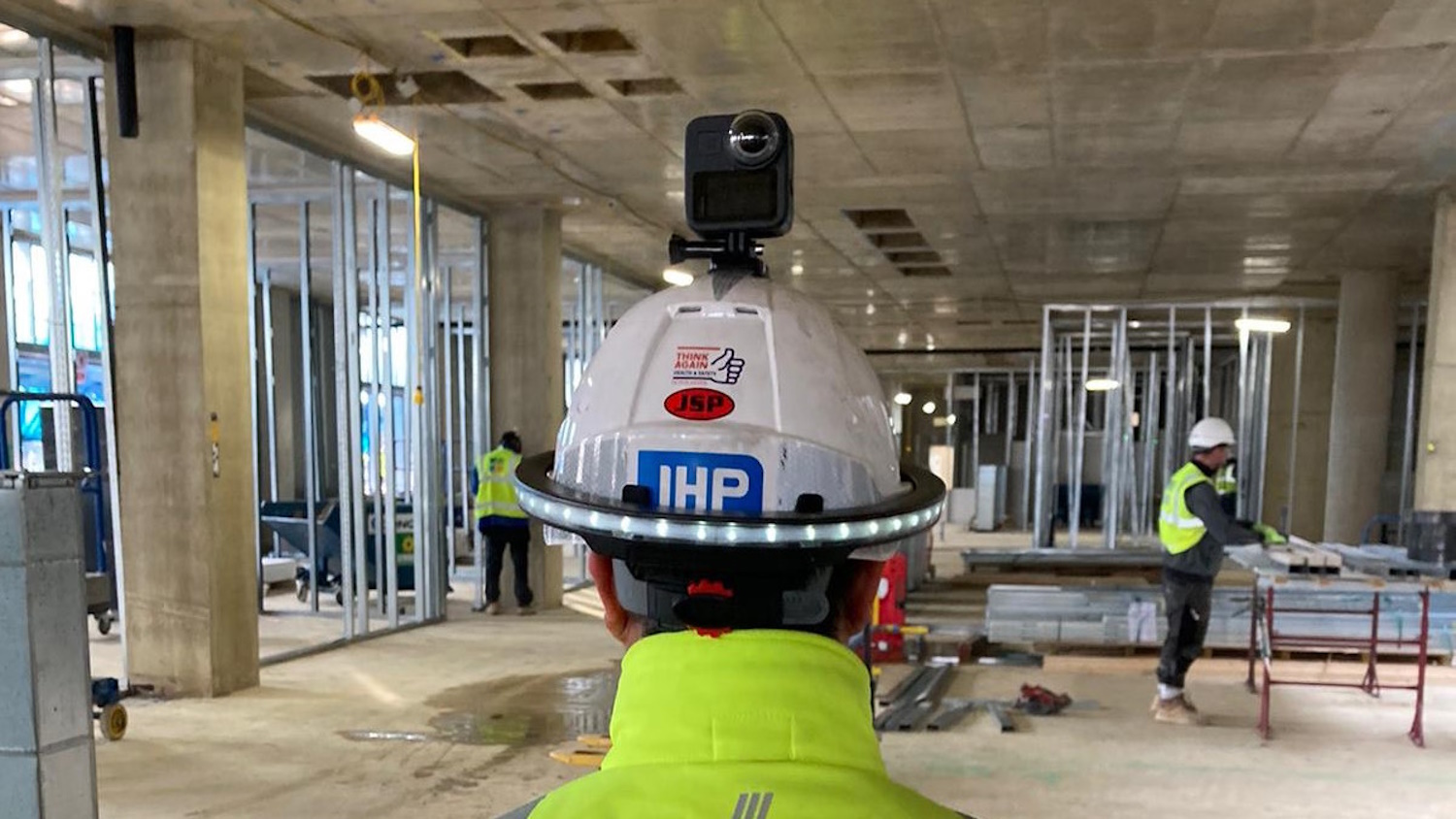
Integrated Health Projects (IHP) – the Sir Robert McAlpine and Vinci JV – is pioneering the application of Buildots’ AI technology at Royal Bournemouth Hospital for University Hospitals Dorset NHS Foundation Trust.
Before using Buildots, IHP project teams spent considerable time manually updating data. IHP’s team wanted a slicker information management process for the 22,650 sq m BEACH (Births, Emergency and Critical Care, Children’s Health) building. It needed to maximise quality control, enhance forecasting capabilities, and streamline early error detection.
The introduction of Buildots transformed the approach to the project’s development. The technology automatically analyses data captured on site via helmet-mounted 360-degree cameras. The platform then generates true-to-life progress reports supported by visuals, providing managers and stakeholders with accurate, objective data and in-depth analysis, improving efficiency.
IHP worked closely with Buildots to develop a solution tailored to its specific needs and develop a 4D BIM sequencing environment for the project. It was important for any new technologies to work in tandem with existing platforms, and Buildots integrates with other key software tools, including MS Project, Revit, Powerproject and BIM360.
Using Buildots’ technology, the project team can now capture full 360-degree photogrammetry of the project. By comparing detailed 3D models with 360-degree site-walk videos, the IHP team can demonstrate the status of the project at any given time.
The online interface allows instant access to 2,300 rooms and spaces. Data is centralised on one platform, fostering a culture of transparency and trust. The 3D models facilitate early identification and resolution of potential design conflicts, significantly reducing rework, which has improved programme and cost prediction.
DMRC | Allo on HS2
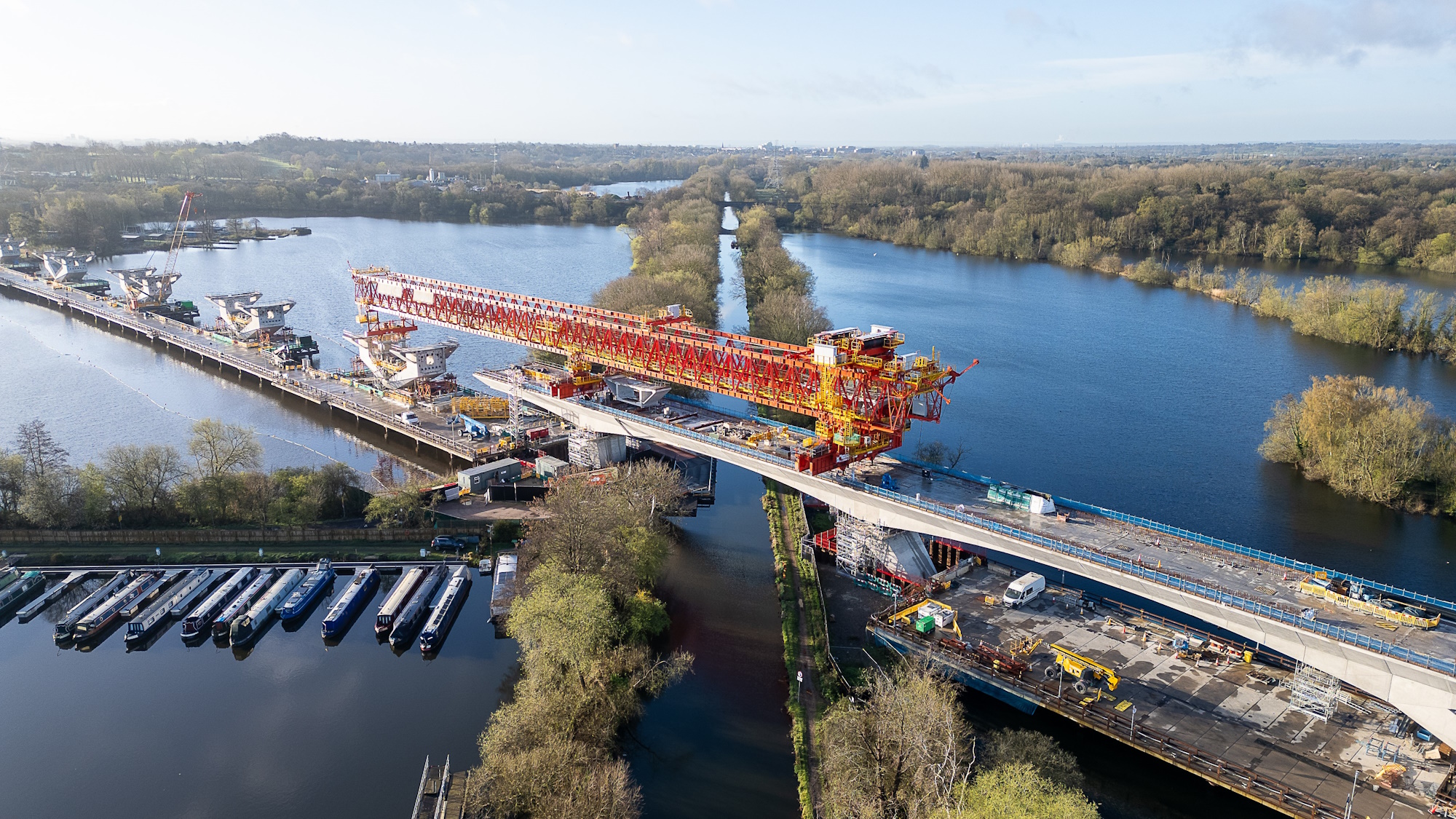
The Eiffage Kier Ferrovial BAM Nuttall (EKFB) JV faced several challenges with resource management in its construction operations on HS2. The manual process of daily resource and cost allocation data led to inefficient use of time, with supervisors spending up to 30 minutes each day filling in Excel sheets, while cost reporting would often be up to 10 weeks out of date.
After identifying these issues, EFKB worked with tech firm DMRC Technologies to deploy Allo, a resource management software package tailored to the construction industry. It facilitates the centralisation of resource allocation, providing data and real-time insights on utilisation. It also offers a cloud-based SaaS platform, enabling the capture, tracking, and management of personnel, plant, material, and environmental data in near real-time.
The package includes a mobile app, which allows on-the-go data capture and offers features such as roles and permissions. To facilitate payroll, Allo has enabled integrations with Coins. It also connects to existing datasets via SharePoint and enables natural language reporting through Metamesh, another DMRC solution.
EKFB reports numerous benefits from the introduction of Allo. There has been an 80% reduction in errors associated with manual data entry. Improved reporting has led to better management of resources such as personnel, plant, or materials, increasing utilisation and productivity.
The JV estimates more than 32,000 hours have been saved by using Allo for resource allocation. This has resulted in a cost saving of more than £5m, which is projected to rise to £35m by the end of EKFB’s work on the HS2 project.
AtkinsRéalis | Sizewell C
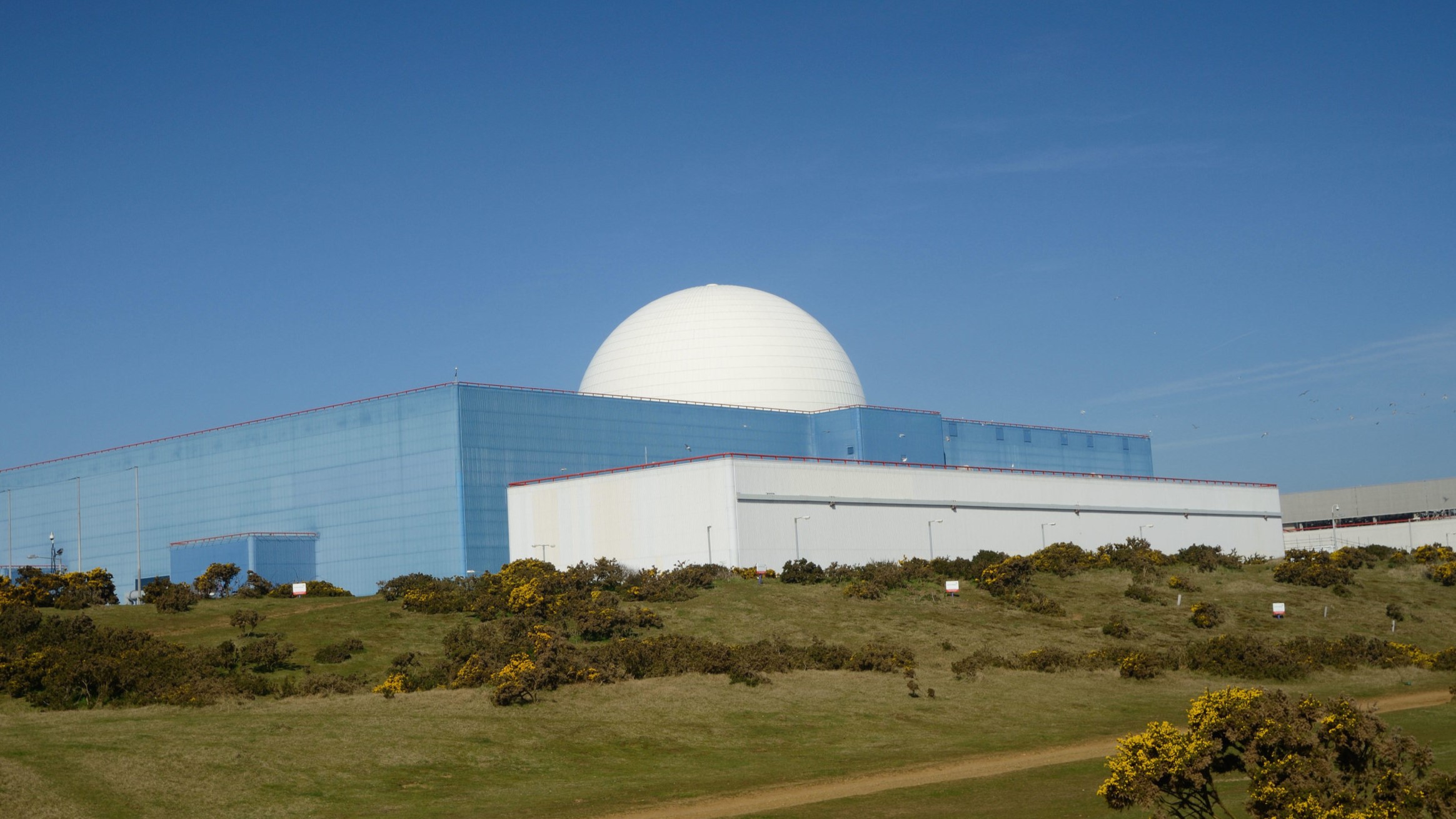
AtkinsRéalis is using automation and digitalisation in the design delivery phase of Sizewell C, the new 3.2GW nuclear plant planned for Suffolk, generating valuable data for driving design efficiency.
This is a huge project with tens of thousands of different modelled objects across multiple different disciplines, so having a coherent data strategy is critical for delivery.
AtkinsRéalis is driving the implementation of a model object data dictionary (MODD) to deliver a data-enabled Sizewell C. The MODD was developed based on industry standards and plays a crucial role in detailed design delivery. It defines every attribute required for all elements within AtkinsRealis’s design scope, providing the design teams with a standardised approach to data across all disciplines.
To date, more than 100,000 elements have been modelled. Automated tools were developed to allow teams to append data quickly and accurately. Working within Civil3D, the tools extract data to populate all MODD requirements for that object – a combination of calculated values from Civil3D properties, entry fields for the user via input or Excel, and directly reading data from the project CDE.
One area of particular benefit from improved data handling is the ‘mass balances’. This concept, borrowed from process engineering, is used on Sizewell C to describe demand and supply profiles across technical disciplines. These include the number of workers on site, earthwork volumes and HGV deliveries.
For these demand calculations, unpivoted datasets, which are not typically used in technical delivery, have been implemented, enhancing data granularity and enabling better decisions. For example, by analysing the granular workforce data, AtkinsRéalis identified an overprovision of desks for office staff, but a shortfall of lockers for site workers, and site welfare was improved in response.
AtkinsRéalis says the project’s successes demonstrate the potential for combined model and data-driven solutions, and how the adoption of MODD can improve the overall efficiency and productivity of projects.
Celebrate with the best
The winners of the Best Use of Data category, alongside the victors of the other 12 categories, will be revealed at the awards dinner on 2 July at the Brewery in London. You can join them by booking your places at the awards.
The Digital Construction Awards celebrate best practice and reward innovation in the application of information management and digital technology in the built environment sector.
The awards are run by Digital Construction Week, the Chartered Institute of Building (CIOB), and Construction Management and BIMplus. Awards sponsors include Bluebeam, Procore, Revizto and the CIOB.
Don’t miss out on BIM and digital construction news: sign up to receive the BIMplus newsletter.