Construction firms are about to see compliance costs for dealing with non-recyclable plastic packaging skyrocket unless they start acting now, warns John Gummer.
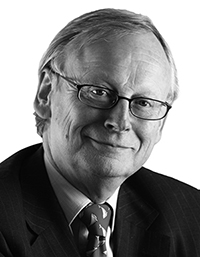
Chancellor Rishi Sunak announced in the spring Budget that a plastic packaging tax will come into force from April 2022. This will see businesses whose products have less than 30% recyclable material being charged £200 per tonne and forms only a part of the significant increase in the cost of plastics and packaging facing the construction industry.
Compliance costs, which have already increased by around seven times since 2017, are set to skyrocket further by 2023. Yet while a handful of construction and building companies are addressing this fundamental change in a meaningful way, many have yet to grasp the extent to which the costs and pressures associated with plastic packaging will fundamentally threaten their current business model.
So what do construction firms need to know?
Rising cost burden of current regulation
Packaging Recovery Note (PRN) charges are the compliance fees that companies must pay towards the collection and disposal of plastic packaging waste they put on the market. On its own, the per-tonne increase of plastic compliance – from an average of £50 in 2017 to over £400 in 2019 – is eye-catching enough. However, when these costs are modelled for large and mid-sized businesses it is calculated that for every £1,000 a company was spending on plastic compliance in 2017, they are now spending over £8,000. The cost of these PRNs has effectively risen from a level many businesses might have considered a manageable marginal cost of doing business, to a major cost centre.
New regulations will further increase costs
The Extended Producer Responsibility (EPR) rules, due to go live in less than three years’ time, will force producers and users of packaging to pay local authorities the full net cost of collecting, reprocessing and recycling packaging. By the government’s own calculations, EPR is set to increase the cost of packaging compliance fees by an estimated 21 times what businesses were paying in 2017. The chancellor’s plastic packaging tax will add to this but his rules will mean that businesses that reduce the amount of packaging they use, ensure it is made from the maximum recycled content, and insist that it’s universally recyclable will benefit significantly.
Supply chain and investor pressure
In the face of higher costs, the impact of commercial and consumer pressure on businesses to reduce the use of non-recyclable plastics, and the concerns of employees and the wider public – businesses are pressing their supply chains to reduce the use of plastic packaging. Initiatives from large construction firms who want their suppliers to remove or reduce packaging put product manufacturers unable to meet these targets at risk of delisting or reduced orders.
At the same time, with the growing power of Environment, Social and Governance (ESG) responsible investment, investors are increasingly aware of the impact of plastics and packaging on the future viability of businesses.
Construction companies need to work with suppliers immediately to minimise exposure to increasing packaging costs. As a sector which works on tight margins and uses a large amount of plastic packaging, builders and developers will need to engage with their suppliers to make sure they are working on solutions to reduce their financial exposure to PRN increases, EPR, and the plastics tax. If they do not take action, costs are likely to be passed on by suppliers.
This new operating environment demands that construction firms rethink their business model. They will need to move from one that takes little account of plastics and packaging, considering it no more than one of the costs of doing business to one that recognises this is a cost sufficiently important to repay real effort to minimise its incidence and more actively manage recycling and reuse.
These will be changes that need to be made to every construction business if it is to thrive sustainability and profitably.
The Rt Hon John Gummer, Lord Deben, was environment secretary from 1993 to 1997 and is chair of sustainability consultancy Sancroft
Direct action seems to be the only way to get the desired results