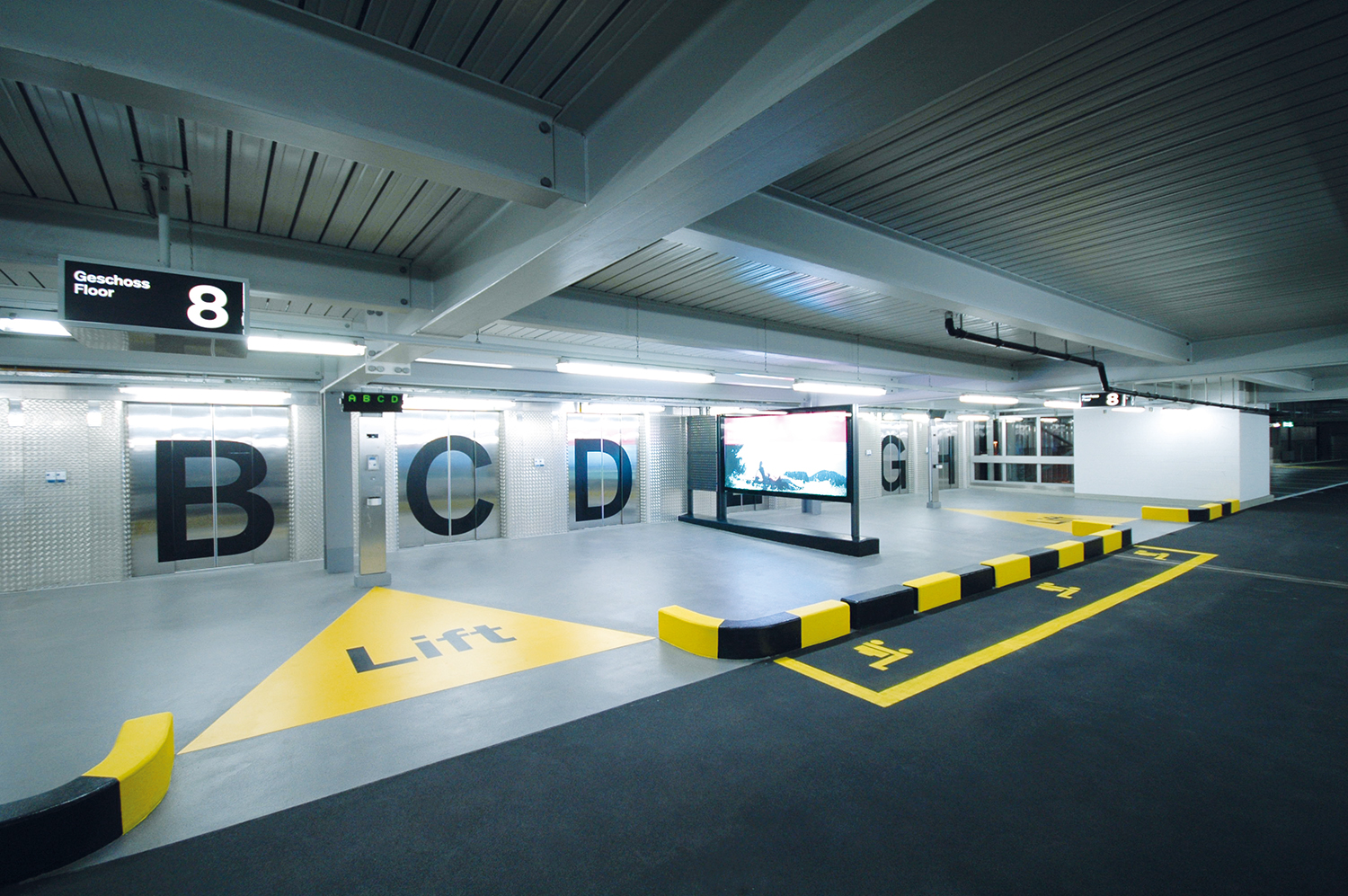
The UK has an ageing stock of multi-storey car parks (MSCPs), many of which were constructed from reinforced concrete in the 1960s and 1970s. A large number have exceeded their design life and require increasing levels of investment to operate.
This CPD, in association with Sika, looks at the causes, indicators and solutions to structural defects in MSCPs.
Although there are examples of well-built, well-maintained car parks, many in the UK have structural defects due to issues with design, materials and workmanship. All of which have been exacerbated by years of neglect and the increased demands placed on them by owners and operators.
In many cases, the maintenance and repair approach for these structures has been to patch up visible damage as cheaply as possible and carry on, rather than adopting a whole-life maintenance strategy.
This reactive maintenance does not always ensure that car parks are maintained to a good state of repair and without treating the causes of the deterioration, can result in the need for much larger and more expensive interventions when maintenance issues snowball.
The cost of these repairs is exacerbated by the full or partial closures they entail, which have the knock-on effect of reducing footfall for surrounding businesses. The damage can be long lasting as valuable customers are lost to ‘competitor’ car parks.
Increased loads in car parks
The ongoing challenges of this legacy are compounded by the shift to electric vehicles (EVs), which are heavier than internal combustion (IC) engine vehicles due to their batteries, the armour required to protect them and the reinforced chassis and suspension required to support the battery weight.
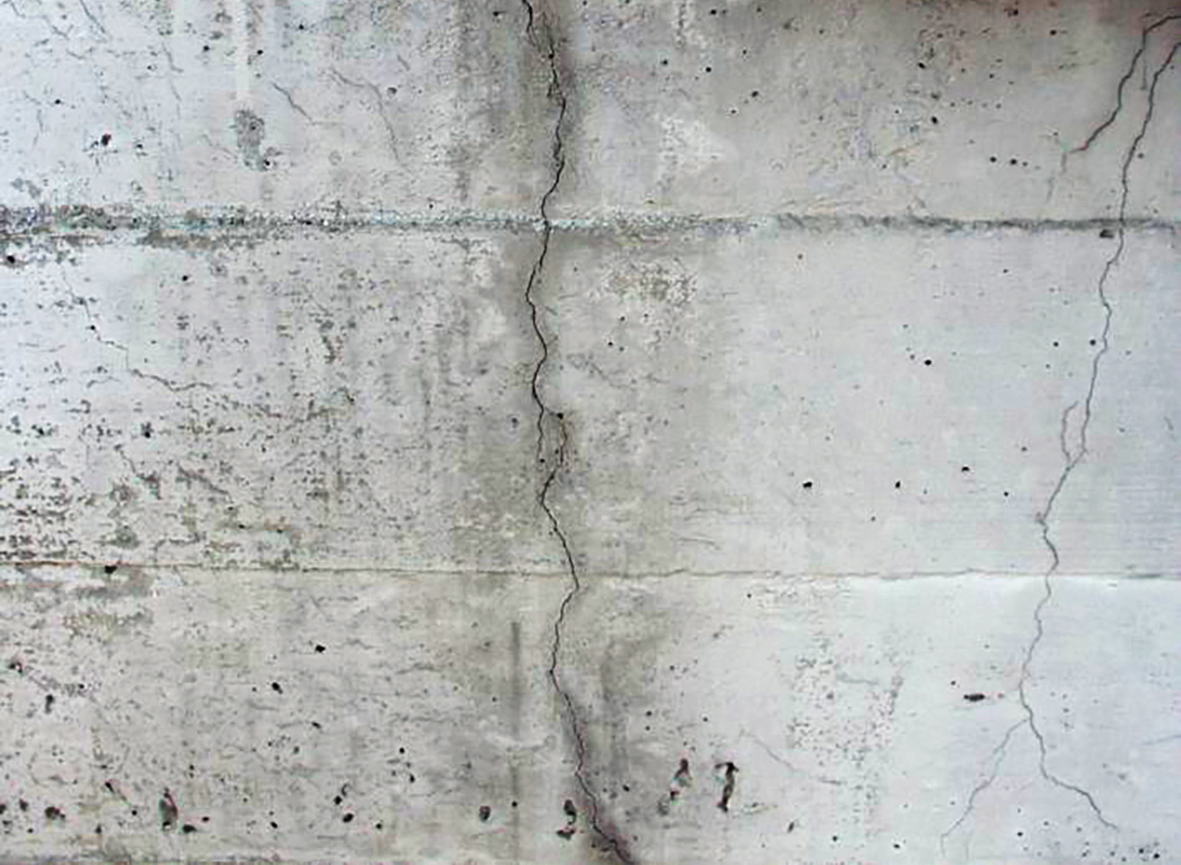
Many of the UK’s car parks were built when cars were significantly smaller and lighter than current models, even before factoring in the shift to electric vehicles. The increased load is significant – Sika’s research shows there is a 148% vehicle weight increase when comparing the top five selling cars of the 1960s with the top five selling EVs in 2021.
Inevitably, if you increase the weight of the vehicles using an MSCP, then both the dead/static loads (self-weight of the structural concrete elements, fixed items and parked cars) and live/dynamic loads (moving cars, people) increase and so do the corresponding stresses they place on the structure, even if the number of vehicles does not.
What to look for
The objective for any car park operator is to ensure that car park structures are safe, structurally sound and fit for purpose. This will involve taking stock of the asset in its current state, before looking at what needs to be done to strengthen and repair the structure. Once works are complete, there then needs to be a plan put in place to ensure that the asset is maintained into the future.
Visual indicators of structural deterioration can include:
- Water seepage: Water/rust staining of beam sides and deck soffits, often including the formation of stalactites, may indicate failed waterproofing, movement joints or drainage and may present an increased potential for corrosion damage and coating failures.
- Concrete cracking: There are myriad causes but cracking could indicate ongoing structural issues – and allows contaminated water to reach the steel easily. It can often be worsened by thermal expansion/contraction.
- Spalled concrete with exposed steel reinforcement: This arises from expansive corrosion products (rust) forcing the concrete cover to fail. The corrosion is caused by de-icing salt ingress (decks or wet areas) or carbonation (acidification) of the cover concrete, typically in drier areas.
- Deck coating wear and tear: Patches where coatings are delaminated or worn through due to application issues or tyre abrasion. Failed coatings lead to water ingress.
CFRP plates and wraps | Steel plates or beams |
PROS | PROS |
Lightweight with very little manual handling risk | More widely understood and remain the most common method, using common design codes |
Uniform application of strengthening (no bolts) | Lower material/fabrication costs |
Very little impact on headroom or column width | Simple surface preparation |
Will not corrode | CONS |
Straightforward and quick installation | Heavy to move into position and may need propping (which would cause closure of area below) |
Can be hidden behind mortars, renders or coatings | Adds significant static loads to structures |
CONS | Require ongoing painting and inspection/maintenance |
Higher initial cost | Point loads due to fixings and maximum length circa 5m |
Cannot be fixed through or to | Reduced ceiling heights (beams) and increases width of columns |
Fire resistance (only in certain circumstances) | Liable to corrosion |
Presenting the solution
Fortunately, there are a host of innovative products and systems to ensure that car park structures can be returned to a good state of repair, while also allowing them to cope with the increased weight of EVs. It is recommended that stakeholders follow a four-step process: assess, specify, repair, maintain.
1. Assess
Assess the structural performance of existing structures to reflect their current condition, current loadings and future loadings. This is typically carried out by a structural engineer.
Undertake a concrete condition assessment to quantify any damage and deterioration to structural elements, identify their causes and determine their extent and seriousness (usually a combination of chloride sampling/analysis, half-cell potential mapping, cover depth and carbonation depth surveys etc). This is typically carried out by a specialist surveying and testing contractor.
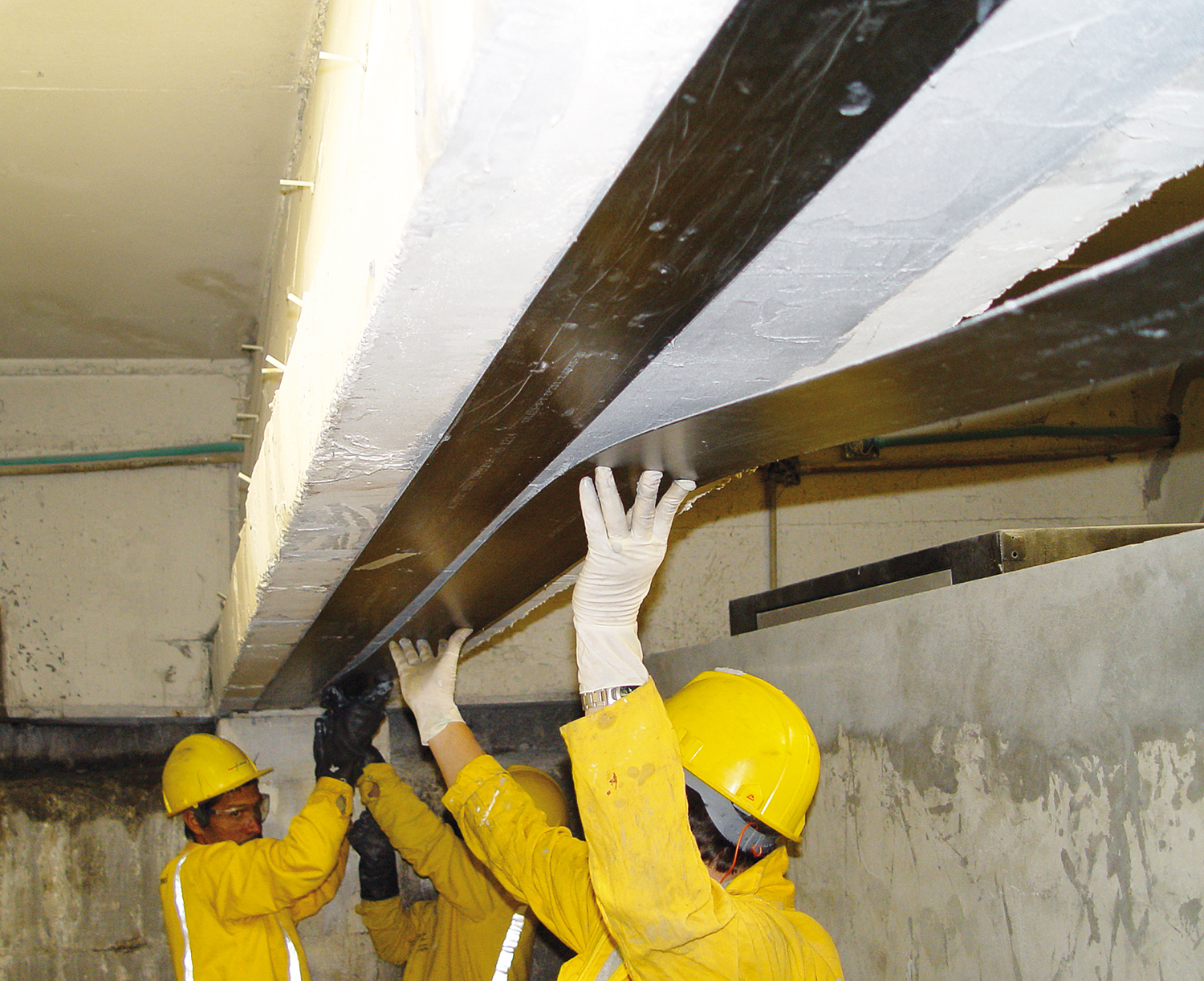
This initial testing will allow the specifying engineer to determine any issues to be addressed. The results will also allow for prioritisation, to ensure that ‘big ticket’ items critical to the car park remaining open are addressed as a priority.
2. Specify
It is therefore essential that the responsible engineers engage with materials manufacturers and suppliers to ensure that the correct products and product systems are specified for the project.
When this is done successfully, the products and systems will address most, if not all, of the issues raised by the testing and surveys carried out. This ensures that the repairs have the longest possible lifespan and therefore represent a sound return on investment.
3. Repair
The standard that governs the assessment and repair of concrete structures is the BS EN 1504 series: Products and Systems for the Protection Repair of Concrete Structures. This sets out the principles to be followed for a high-quality durable repair and should be the basis of any repair intervention.
Broadly, the techniques and products used to structurally repair a car park structure fall into three categories: Reinstate lost strength, protect against future deterioration and increase strength.
Reinstate lost strength
There are myriad product categories that can be used to reinstate the strength of a car park structure which has been lost through corrosion damage, structural movements and excessive loading.
These include reinforcement primers, structural repair mortars and grouts, resin anchors and crack injection resins. These repairs may require new reinforcement to be installed to replace bars damaged by reinforcement corrosion.
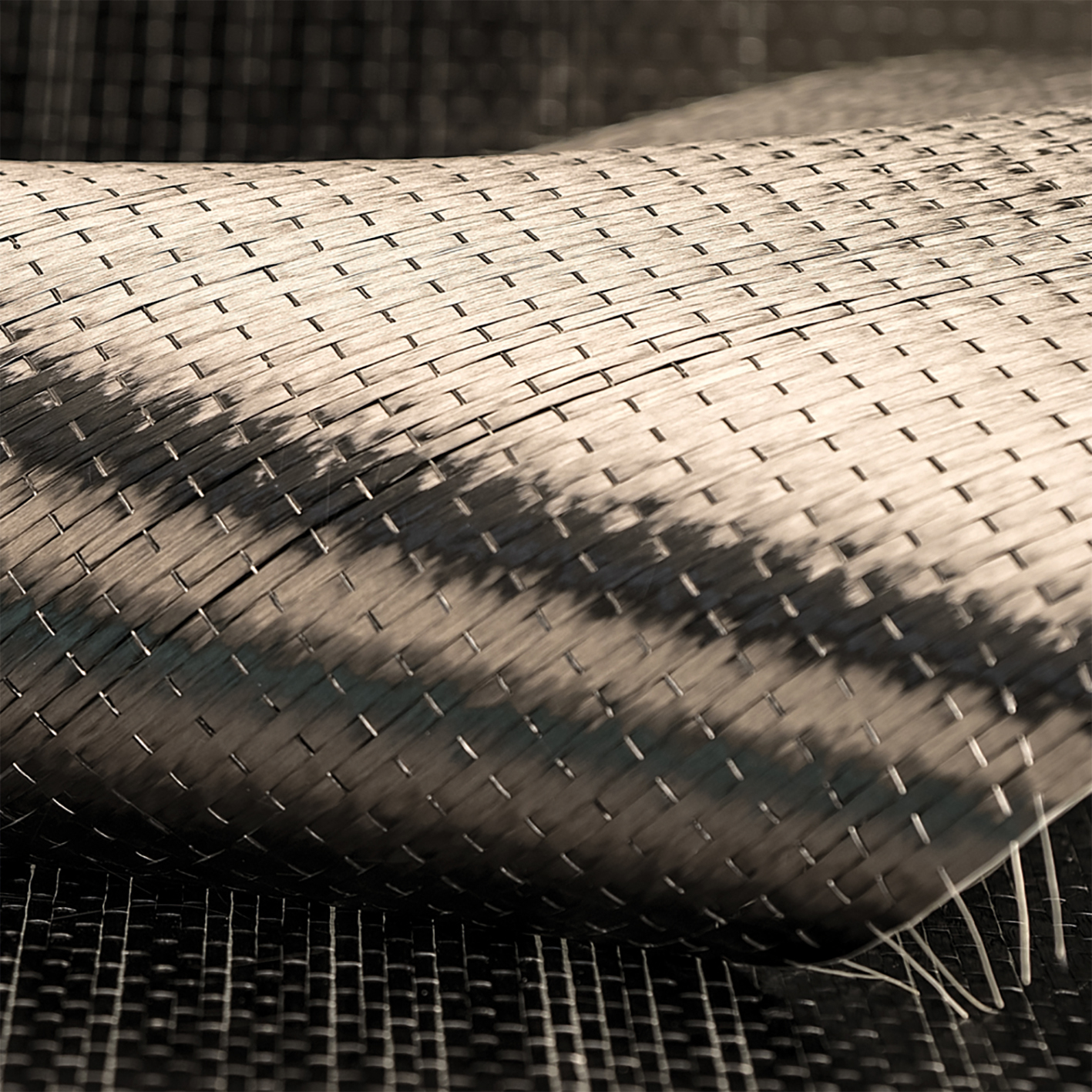
The idea behind these kinds of repairs is that defective concrete is replaced by a durable material that is at least as strong as the existing concrete. This allows load paths to be reinstated and further deterioration to be stopped.
There are subsets of products within these categories that are particularly useful in car park repair works. Fast-set, rapid strength gain products, usually but not always based on epoxy technology, can ensure a return to trafficable surfaces within a few hours post-repair.
Protect against future deterioration
Concrete protection in some form is often required in MSCPs to ensure the longevity of the structural concrete, including any repairs that have been made. These products generally fall into one of two categories:
- Corrosion control, to mitigate the risk posed by chloride ions in the concrete. Cathodic protection and prevention techniques use activated zinc, hybrid or impressed current anodes to relocate the corrosion reaction to the anode and prevent reinforcement corrosion. In addition, corrosion inhibitors can be used to stop or prevent corrosion.
- Ingress prevention, to prevent water penetrating into the concrete. On the car park decks and column bases, high-strength, waterproof and wear-resistant coatings prevent water laden with chloride salts from penetrating the concrete and causing reinforcement corrosion. On the columns, beams and soffits, coatings can prevent moisture from entering, and also prevent carbonation of the concrete, a process which leads to reinforcement corrosion. Hydrophobic impregnants are another class of material which line the pores of the concrete, preventing water ingress. These can be applied to the concrete surface in either liquid or cream form.
Increase strength
To ensure that the various elements of the car park can withstand current and future loads, it may be necessary to supplement their strength and load-bearing capacity. Traditionally, this has been done using various forms of steel to supplement the reinforcement already buried in the concrete: for example steel plates, steel reinforcement in a concrete ‘jacket’ around columns, or by adding supplemental beams to the soffit.
While these techniques, when properly designed, undoubtedly achieve the aims of the strengthening, they increase the self-weight and therefore static load on the car park. Also, as they all contain ferrous materials, they represent a corrosion risk. This must be mitigated by coatings and regular inspection and maintenance.
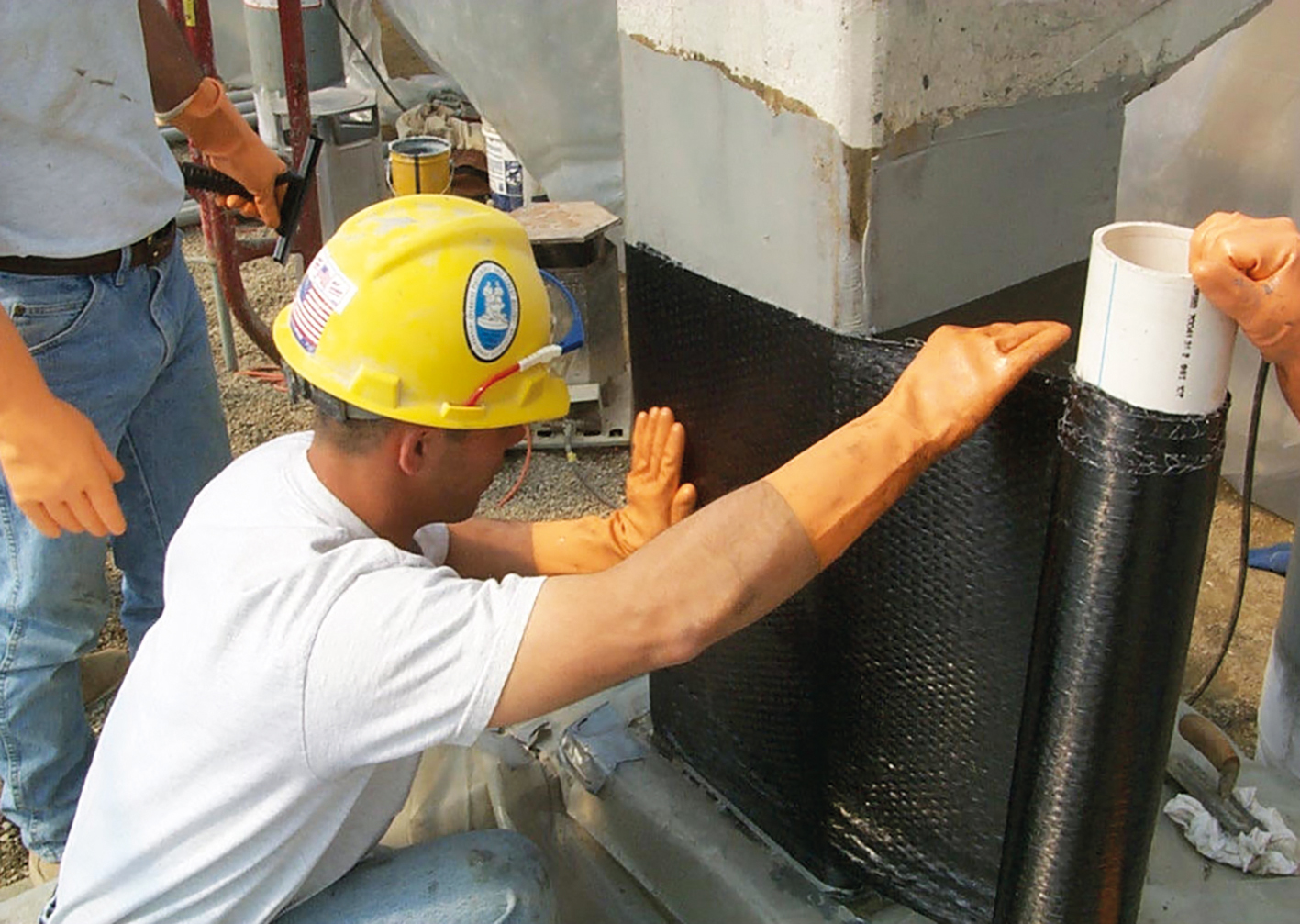
A proven alternative, carbon fibre reinforced polymer (CFRP) products, have been successfully employed for 30 years or more to strengthen reinforced concrete structures. These materials generally come in the form of pultruded plates or as uni- or multi-directional fibres. These are then combined with an epoxy resin or adhesive on site to create a composite strengthening system.
The incredibly high strength of the carbon fibres, along with their low weight, means that much less material is required to achieve the same level of strengthening as steel. A steel plate 10mm+ in thickness, weighing 100kg+, can be replaced by a ~1mm thick plate of CFRP weighing only a few kg. Similarly, a reinforced concrete column jacket 150mm thick can be replaced by several wraps of a CFRP fabric which might total just 10mm.
The weight reduction alone reduces the risks around manual handling and the amount of labour required on site, and removes the need for lifting/propping equipment. In addition, it is possible to apply lengths of up to 50m in one go and there is no risk of corrosion.
4. Maintain
Once repairs and strengthening are complete, it is important to maintain the structure to prolong its operational lifetime. Car park owners can refurbish their existing assets for a fraction of the cost of new build, while also preventing the carbon footprint associated with constructing a new facility, including through construction methods and embodied carbon of building materials.
Further reading
Recommendations for the Inspection, Maintenance & Management of Car Park Structures (2nd edition), published by the Institution of Civil Engineers.
Advice on concrete repair (including materials and CFRP) can be obtained from The Structural Concrete Alliance, which is formed of the CRA, SPA and the CPA.
This CPD has been produced by Construction Management in association with Sika.
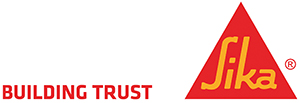