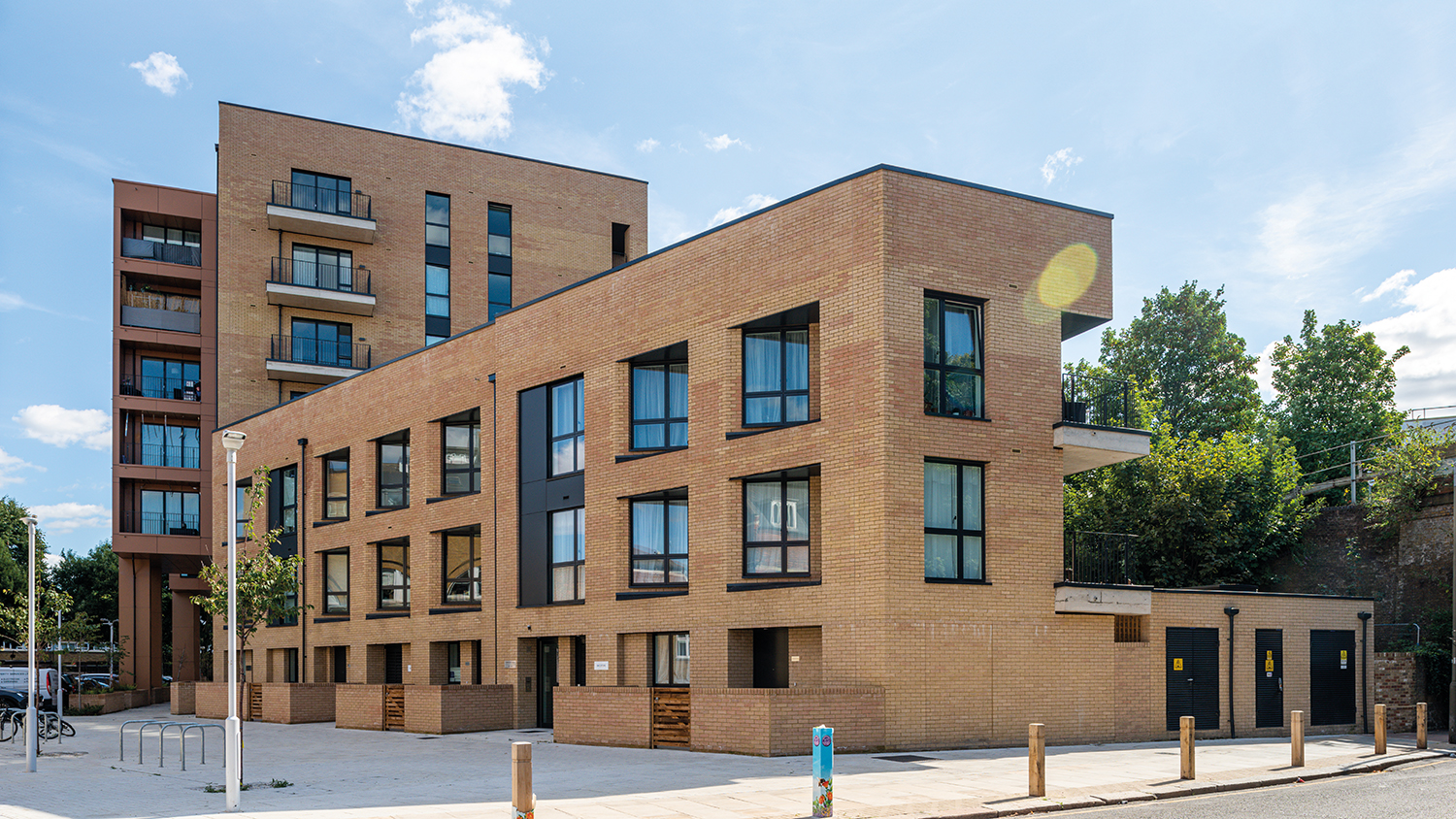
This CPD, in association with Keyfix, discusses the importance of non-combustible cavity trays in buildings. By John Duffin.
On 14 June 2017, the fire that broke out in the Grenfell Tower apartment building rapidly spread to other floors via the building’s exterior, tragically leading to the deaths of 72 people. The Grenfell Tower tragedy highlighted mistakes made by the industry and led to many regulatory changes.
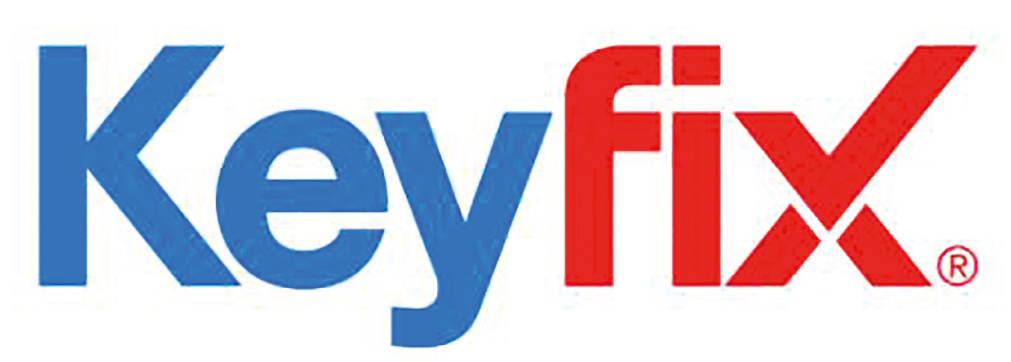
The Hackitt report identified failures within the construction sector that culminated in the Grenfell Tower fire. These findings were incorporated in the Building Safety Act with a view to resolving the systemic issues in the industry.
The fire rose due to the materials and fabrics which were housed in the cavity. But in this case it was also able to work its way down the cavity due to the presence of flaming droplets.
While reviews are ongoing and further legislation is expected to be introduced, the initial regulatory response came in the form of Building Regulations Approved Document B [ADB] (Fire Safety) 2019 edition, which banned combustible materials in the external wall of buildings over 18m. In 2022, the regulations became more stringent, banning combustible materials in the external wall of buildings over 11m.
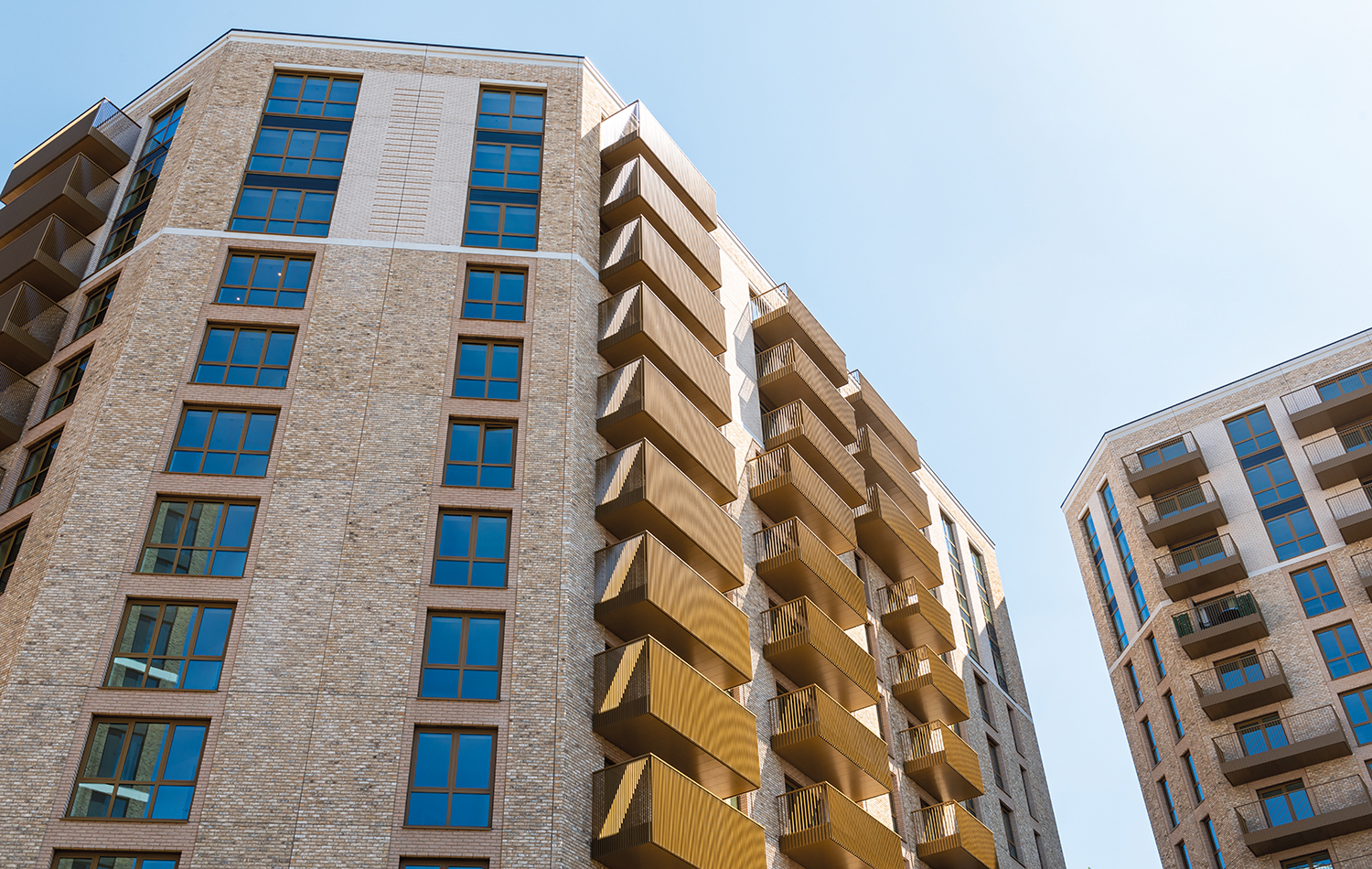
More recently, and alarmingly, there has been an update to the regulations which announced a temporary relaxation for cavity trays in June 2022 for 18 months. This exemption was based on a consultation in January 2020 when there were no viable alternatives available. The exemption was granted two and a half years later,
at a time when there was a variety of alternatives available.
Impact on housebuilders
Despite the exemption, warranty providers are calling for the use of non-combustible cavity tray systems to futureproof their stock.
There have been situations where properties cannot be sold or attain mortgages due to the use of poor materials in the external facade of the building. Therefore, correct specification is crucial to ensure that buildings built in the future exceed standards rather than meeting the minimum standards required at that particular time of the build.
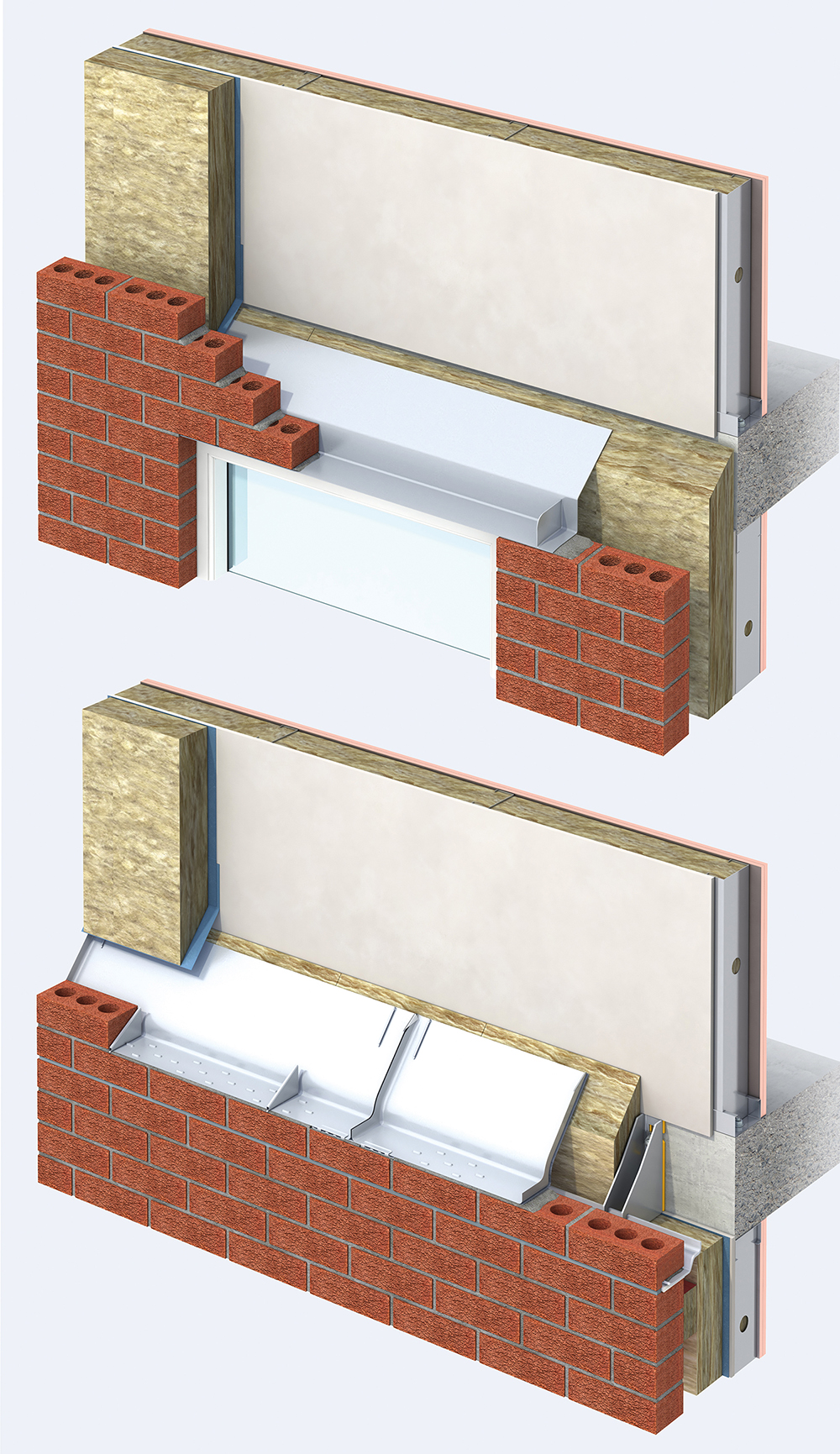
Warranty providers are now requesting that, where an alternative is available, all materials in the external cavity should achieve a minimum European Classification A2-s1, d0 or Class A1, classified in accordance with BS EN 13501-1:2007+A1:2009.
This outdated and fundamentally inaccurate exemption compromises fire safety standards and provides a significant risk to public safety. Moreover, the exemption has prompted confusion in the industry as it is being told to actively take a step back by installing combustible materials back into the cavity.
The National House Building Council (NHBC) and Premier Guarantee have issued a response saying they will only be warranting projects that continue to use non-combustible products in buildings 18m and above. Many major contractors and developers still plan to use non-combustible cavity trays going forward despite the temporary exemption.
Ensuring best practice
Keyfix firmly believes that manufacturers have an obligation to develop products that exceed standards as there is always the risk that those regulations could become outdated.
Therefore, when it developed the Keyfix Non-combustible Cavity Tray (NCCT) system, the company consulted and worked with leading architects and brickwork contractors in conjunction with the Building Research Establishment, British Board of Agrément (BBA), NHBC and Premier Guarantee to develop a unique non-combustible cavity tray system that meets the needs of regulators, insurers, developers and installers.
On the basis of the industry consultation, Keyfix concluded that the cavity tray should be:
- Fully non-combustible
- A1 fire rated
- Holding a lifespan of 125+ years
- Weather-tight with BBA testing
- Free of thermal transmission
- Free of issues associated with differential movement
- Free of condensation formation
- Slip plane resistant
- Accompanied by detailed installation drawing and component schedule
- Preformed without the need for tapes, sealants and mastics.
The Keyfix NCCT was manufactured using class A1 non-combustible grade 304 austenitic stainless steel, ensuring a lifespan of 125+ years for the entire system and making it the enduring, cost-effective and maintenance-free cavity tray solution.
The design of the Keyfix NCCT means that it requires no sealants or mastics. It is the only cavity tray of its type on the market with a mechanical dry seal at joints.
This means that it is not only designed to last, but the patented ribbed joint overlap eliminates the use of any sealants at joints, which also removes the possibility of installation errors caused by onsite conditions.
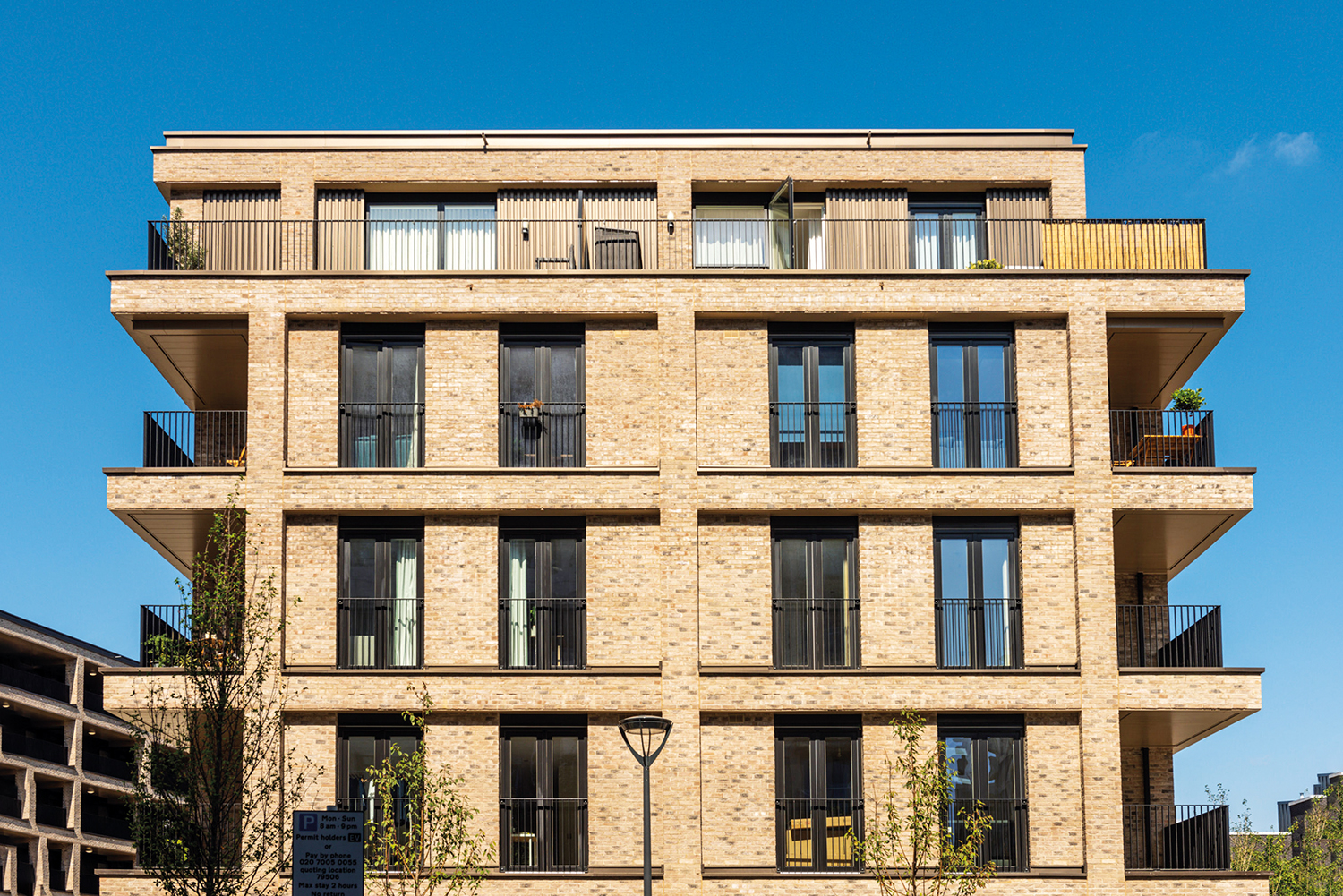
Self-supporting
Additionally, the Keyfix NCCT has rigid self-support. The design enables the stainless-steel tray to be self-supporting across the cavity and requires no support from the internal structure, eliminating clashes with other components.
The Keyfix NCCT has also been subjected to rigorous third-party testing and is BBA certified.
The infamous ‘gap between design and build’ is constantly in discussion throughout the industry, and the use of combustible or low-fire-rated products is one prominent example.
Keyfix has worked to close this gap with its NCCT, which is made evident by its employment on the Verdo – Kew Bridge high-rise residential development in west London, where it helped to simultaneously meet and exceed regulatory requirements.
Located close to the River Thames in Brentford, this new mixed-use development, designed by Broadway Malyan and built by developer EcoWorld, forms part of a major new regeneration scheme that includes the new community stadium for Brentford FC. In order to safeguard the future of the development, Keyfix supplied 765m of Keyfix NCCTs to the development.
One of the key challenges for Keyfix was the tight brickwork build programme. Working to a tight schedule, the offsite fabrication and preforming of bespoke Non-combustible Cavity Tray units in line with the brickwork set-out drawings saved time for the installation team at brickwork contractor DWG.
No additional fixings
The Keyfix stainless steel NCCT was specified due to its self-supporting system. It requires no additional fixings, sealants or onsite fabrication by the brickwork contractor. Therefore, installation of the trays did not impede the speed of bricklaying even when compared to a traditional damp proof course (DPC).
Installed in the outer leaf, with no connection with the inner skin, this system does not create a thermal bridge and eliminates all issues associated with differential movement.
Furthermore, the NCCT is manufactured with integral Stop Ends on each cavity tray to ensure water is trapped and channelled outwards via a Keyfix Non-combustible Weep.
With a lifespan of over 125 years, it is the only non-combustible cavity tray system that does not rely on tapes and mastics to make watertight joints, therefore eliminating one of the main reasons for product failure.
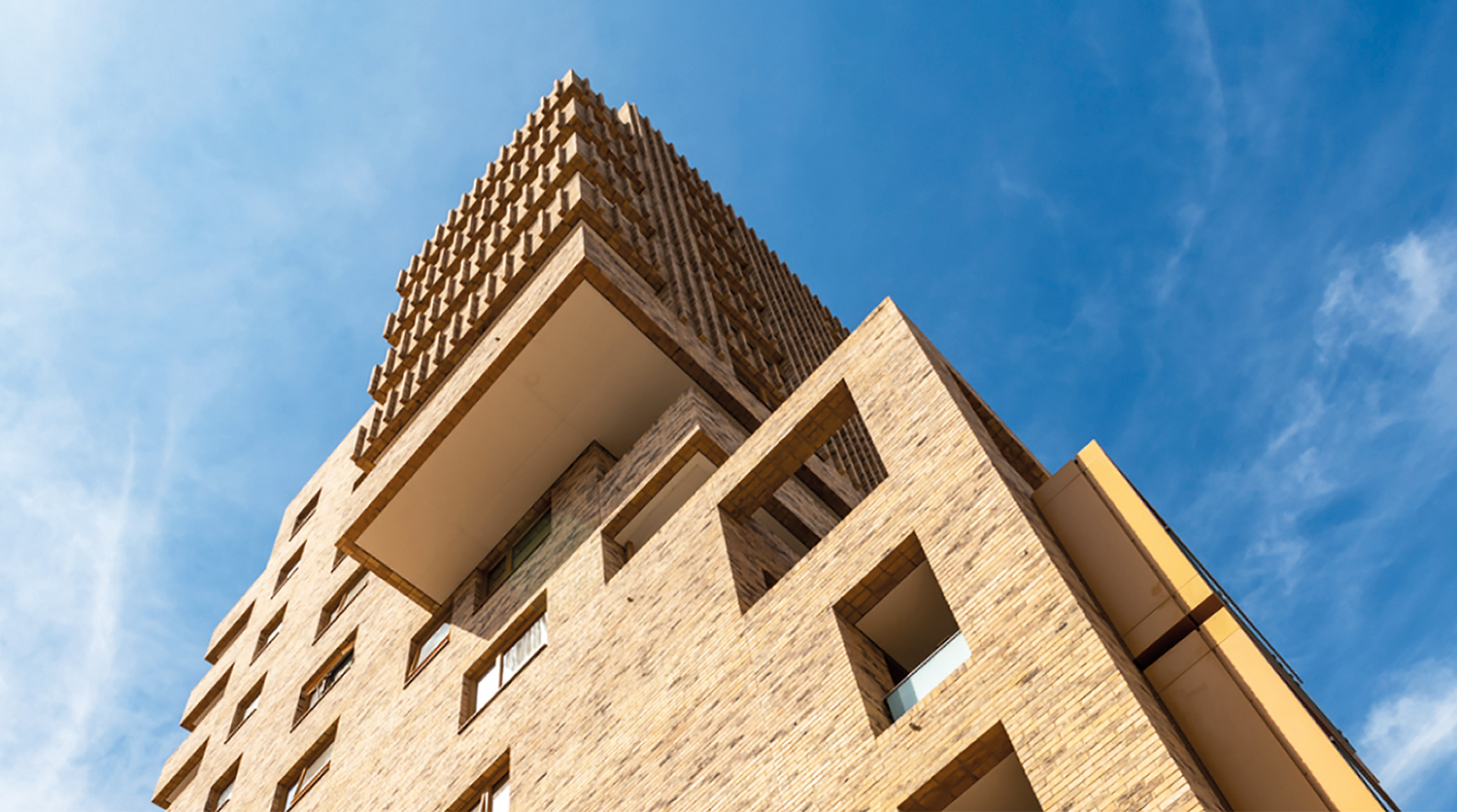
Commenting on the project, Kieran Coyle, general manager at Keyfix, says: “Verdo – Kew Bridge was the first project in which we created and used a component schedule and this is now the same component schedule template we use on every project. It allows installers to use new component codes to identify the different components and install the system to its full integrity.”
Holding an A1 fire rating, the Keyfix NCCT solution exceeds the minimum standards set out in ADB, while ensuring this major new development meets and exceeds the latest regulations.
If the regulations become stricter, it will also be futureproof, maximising the whole-life value of the development. Verdo – Kew Bridge is now complete, with the Keyfix NCCT meeting contractors’ requirements and enabling the creation of a development that has safety built in.
Best practice in fire safety
Ultimately, the industry must not cut corners as there is no place for second best in our built environment. Our buildings must be robust and resilient – and this starts with the correct specification of materials.
Keyfix does not believe that the target for product development should be the minimum allowable standard, as this does not allow for any ‘onsite tolerances’.
If a system is designed to achieve the minimum allowable standard and then encounters conditions on site that further challenge its performance, it can easily drop below the minimum required standard. This results in a return to the ‘gap’ between what has been designed and what has been built, which has dominated the headlines for the last few years.
Keyfix’s external cavity wall solutions provide full assurance that the entire system has been designed and tested to achieve the highest industry standards.
John Duffin is managing director of Keyfix.
This article has been produced by Construction Management in association with Keyfix