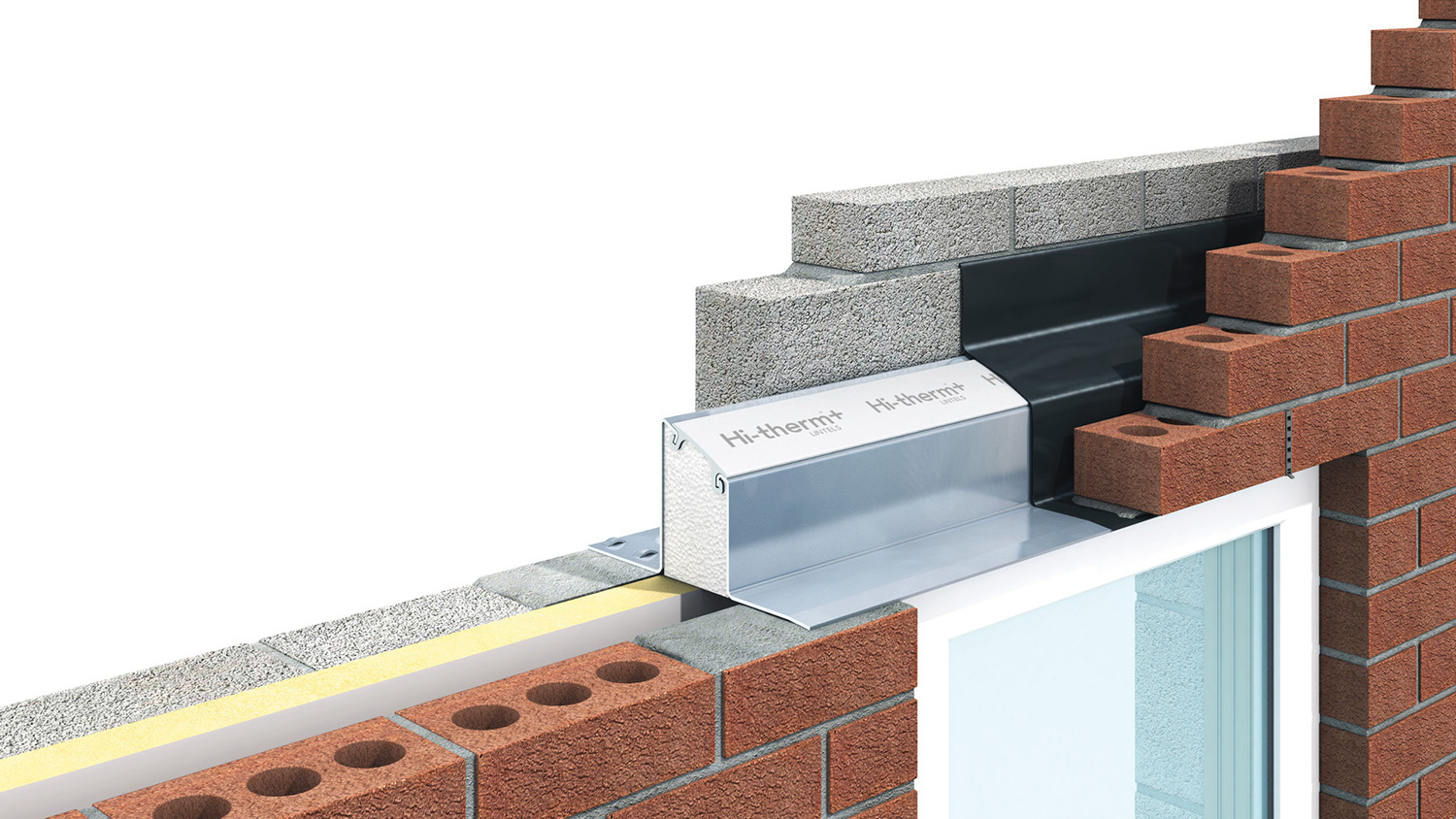
This CPD, in association with Keystone Lintels, discusses how correct lintel specifications can affect energy performance ratings and meet Part L requirements. By Ciarán McAliskey.
Making our future homes ‘zero-carbon ready’ will be essential if the UK wants to meet its net-zero target by 2050. An important first step is ensuring the fabric of our residential buildings is well designed. By paying careful attention to detailing and thermal bridging, we can eliminate some of the issues that create poorly performing dwellings.

What you will learn about in this CPD
- New UK regulations to make residential buildings net zero by 2050
- How heat loss of thermal bridging is calculated
- The role lintels play in thermal efficiency
The new Part L requirements of the Building Regulations will be seen as an important step towards the 2025 Future Homes Standard. There needs to be a clear emphasis on the design of a building’s envelope without the need for further retrofitting work. The new interim Part L uplift to energy efficiency requirements will mean all new homes will be expected to produce 31% fewer carbon emissions through a combination of fabric improvements, low-carbon heating technologies and PV panels.
The 31% reduction is the first step but, by 2025, new housing will be expected to produce 75-80% fewer carbon emissions compared to current standards. This is a potentially massive change for the industry.
Getting the fabric right in new housing
For new homes to meet these higher standards, one key area will be addressing the thermal performance of a building envelope through a fabric-first approach to building design. If the fabric is right and built as designed, it will go a long way to meeting our targets. It’s an approach that will enable us to meet and even exceed regulatory performance criteria, whether it is for large-scale social housing or a much smaller residential property.
Whilst a reduction in CO2 emissions is one consideration when designing thermally-efficient housing, an improvement in thermal comfort can also have a positive impact on its occupants’ wellbeing.
Thermal bridging and heat loss
A critical element of the fabric-first approach will be addressing the issue of thermal bridging, which research quoted by the Building Research Establishment states can be responsible for up to 30% of a dwelling’s heat loss.
This heat loss is quantified and calculated by an Energy/SAP/BRE assessor when designing a building, and they use a combination of U-values and Psi-values, which are thermal transmittance measurements.
- Psi-values: these are measurements used to determine the rate of heat loss through a specific junction. There are many of these junctions to consider when designing a dwelling. Collectively, these are known as thermal bridges. A thermal bridge is created when materials that are poor insulators come into contact with one another (such as a steel lintel within a masonry wall), allowing heat to flow through the path created.
- U-values: these are the sum of the thermal resistances of the layers that make up an entire building element. For example, the sum of the thermal resistances of all the layers that make up a wall (lintel + blockwork + insulation, etc). The U-value also includes adjustments for any fixings or air gaps.
Essentially, the lower the U-value or Psi-value, the more slowly heat will be able to transmit through the building element or junction, and so the better the dwelling will perform as an insulator.
SAP 10.2
SAP is The Government’s Standard Assessment Procedure for Energy Rating of Dwellings; with 10.2 being the latest version of the assessment. The Scope of SAP is to calculate energy use and similar metrics. It does not set any standards or limitations on data.
All Domestic New Builds Require a 3 – Stage SAP Calculation:
Stage 1 – Design Stage
Stage 2 – As-Built Stage
Stage 3 – Energy Performance Certificate (EPC)
Eliminating thermal bridging through smart design and product specification will be essential if we are to ensure we meet these new regulations.
In the past, builders or assessors may have looked to offset the use of inefficient building materials by hitting SAP targets with bolt-on technologies. It is sensible to reduce energy demand initially within the building fabric before replacing this with bolt-on technologies. This leads us to take a fabric-first approach, ensuring that the envelopes of our dwellings are designed with energy efficiency in mind.
Part L now also states that we use the actual thermal transmittance values for building products within the envelope of a dwelling, whereas in the past generic accredited construction detail (ACD) values were accepted within the SAP assessment. These values could vary rather substantially from the actual value of a specific product. By making this change, the Y-value obtained (which is the total amount of heat lost through thermal bridging in a dwelling) is now accurately represented within the BREL report.
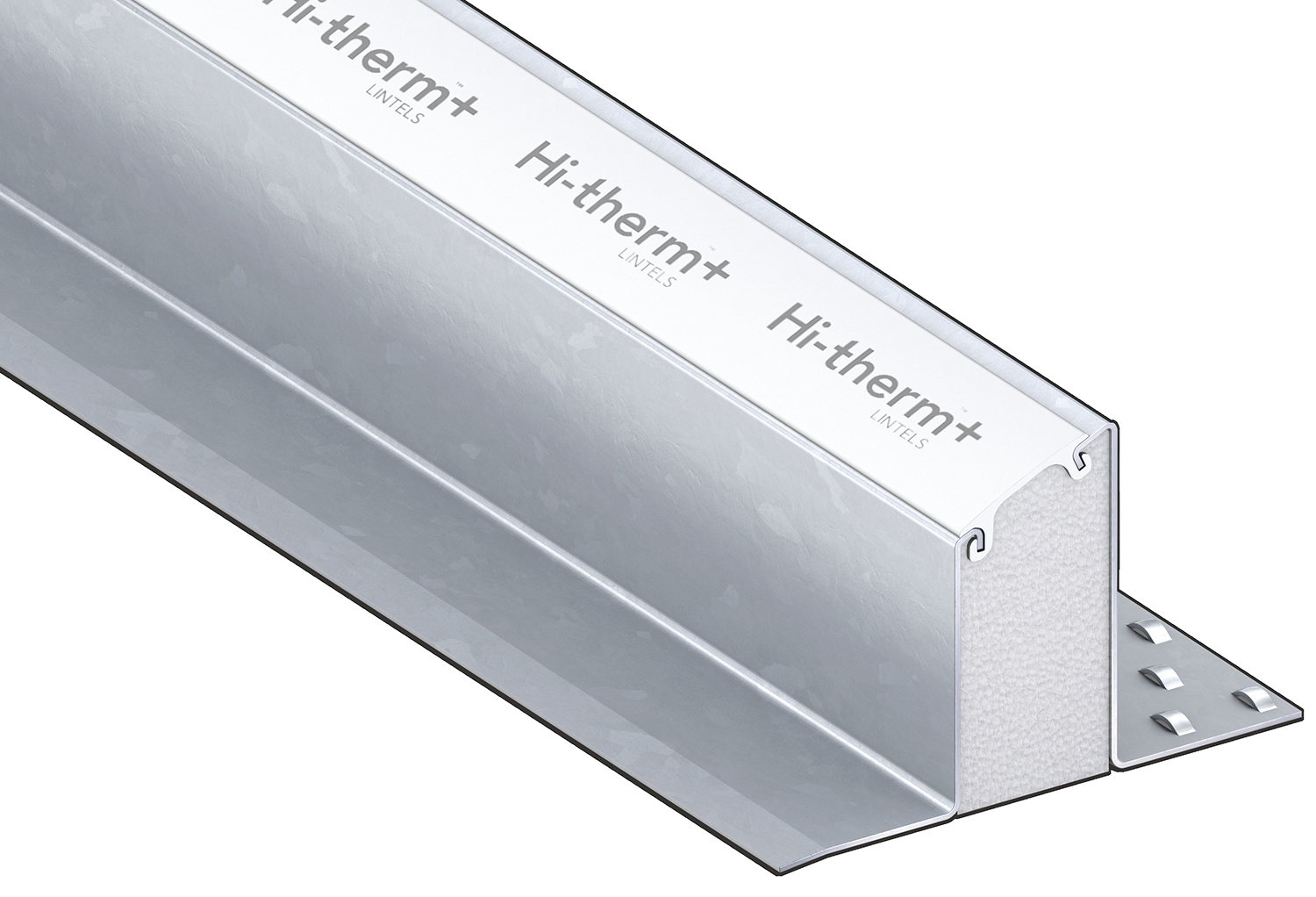
Moreover, due to the previous performance gap between the design and built stages that we have seen in the past, Part L has introduced the requirement for photographic evidence within the report. This helps overcome any inconsistencies with site workmanship or installation of a different product than was specified. These photographs are required at key junctions, at the relevant construction stage, for every new dwelling built.
To help with the fact that the photographs are plot-specific, geo-location technology is also required, so that there is clear evidence that all the photographs have not just come from one ‘perfect’ plot.
Collectively, these changes provide us with evidence that homes have been constructed from the same materials that they were designed from, ensuring properties run as efficiently as they were designed to run.
Regulatory standards
Building Regulations Conservation of Fuel and Power Part L
The new Part L – Conservation of Fuel and Power requirements of the Building Regulations was updated and came into force on 15th June 2022. It aims to reduce carbon emissions in new homes and non-residential buildings by 31% (compared to 2013 standards) in response to climate change.
These regulations form a series of Approved Documents that provide guidance on different aspects of a building’s design and construction.
High-performance lintel
Often overlooked when it comes to thermal efficiency are steel lintels but the importance of lintels should not be understated. Considering that steel lintels are typically present in traditional build dwellings throughout the UK and Ireland, they can play a significant contributing factor to the 30% of heat loss through thermal bridging in a typical dwelling.
While steel has numerous advantageous properties such as structural performance and life expectancy, it is a highly thermally conductive material and, as such, will transfer heat from the inside to the outside of a dwelling. That heat loss will require energy to replace it and generating that energy will produce carbon emissions as a result. However, there are solutions to address this.
For instance, the Hi-therm+ lintel has set a new standard for thermal efficiency in steel lintels. It incorporates a central thermal break and is up to five times more thermally efficient than a standard lintel – with a thermal transmittance value of 0.03-0.06 W/mk. Hi-therm+ is a very cost-effective solution, particularly if we look beyond the unit price, as getting the fabric right will save energy throughout the entire life span of the dwelling.
The Hi-therm+ lintel has made a significant impact on the thermal efficiency of homes and is specified on many housebuilder projects across the UK and Ireland due to its low cost and improved performance in lowering carbon emissions within SAP, especially when compared to some other popular alternatives.
Arron Ross is specification manager (UK) at Keystone Lintels.
Case study – Redrow Homes
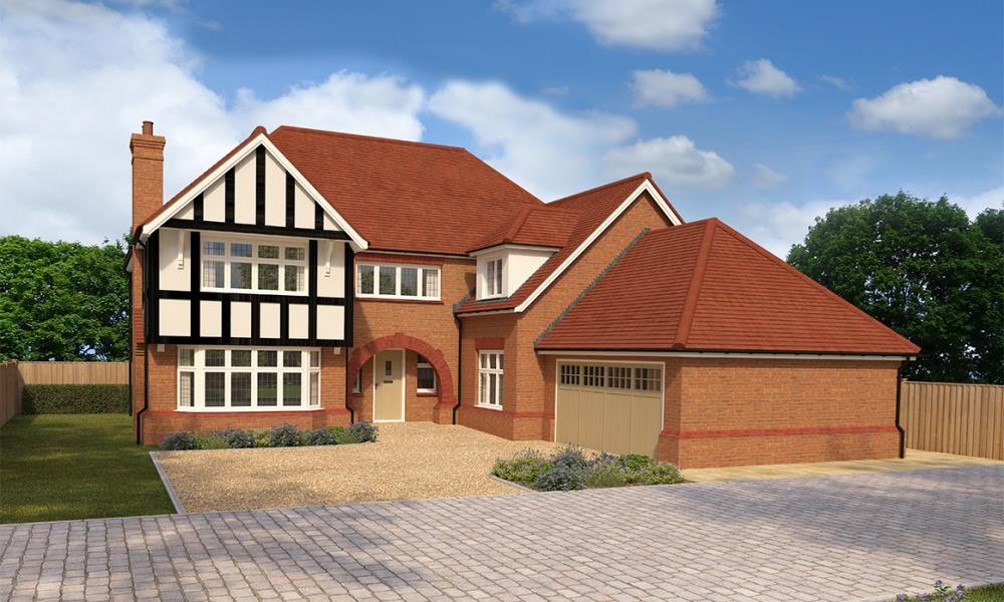
Redrow Homes is using Hi-therm+ lintel to help achieve energy performance requirements whilst simultaneously providing considerable build cost savings. The housebuilder has committed to the Hi-therm+ going forward, saving £200 per plot. Based on 5,800 plots built last year, this would equate to a cost saving of £1,160,000.
Jonathan Moss, head of group technical at Redrow Homes, said: “By including low psi value Hi-therm+ Lintels into our group specification, the improved performance within SAP calculations allowed us to achieve overall significant cost savings by reviewing the ground floor insulation specification whilst still meeting the requirements of Part L Regulations.
The Hi-therm+ lintel has proven to be a cost-effective solution to tackle concentrated areas of heat loss and contribute to the energy performance of our group house type range.”
Further reading