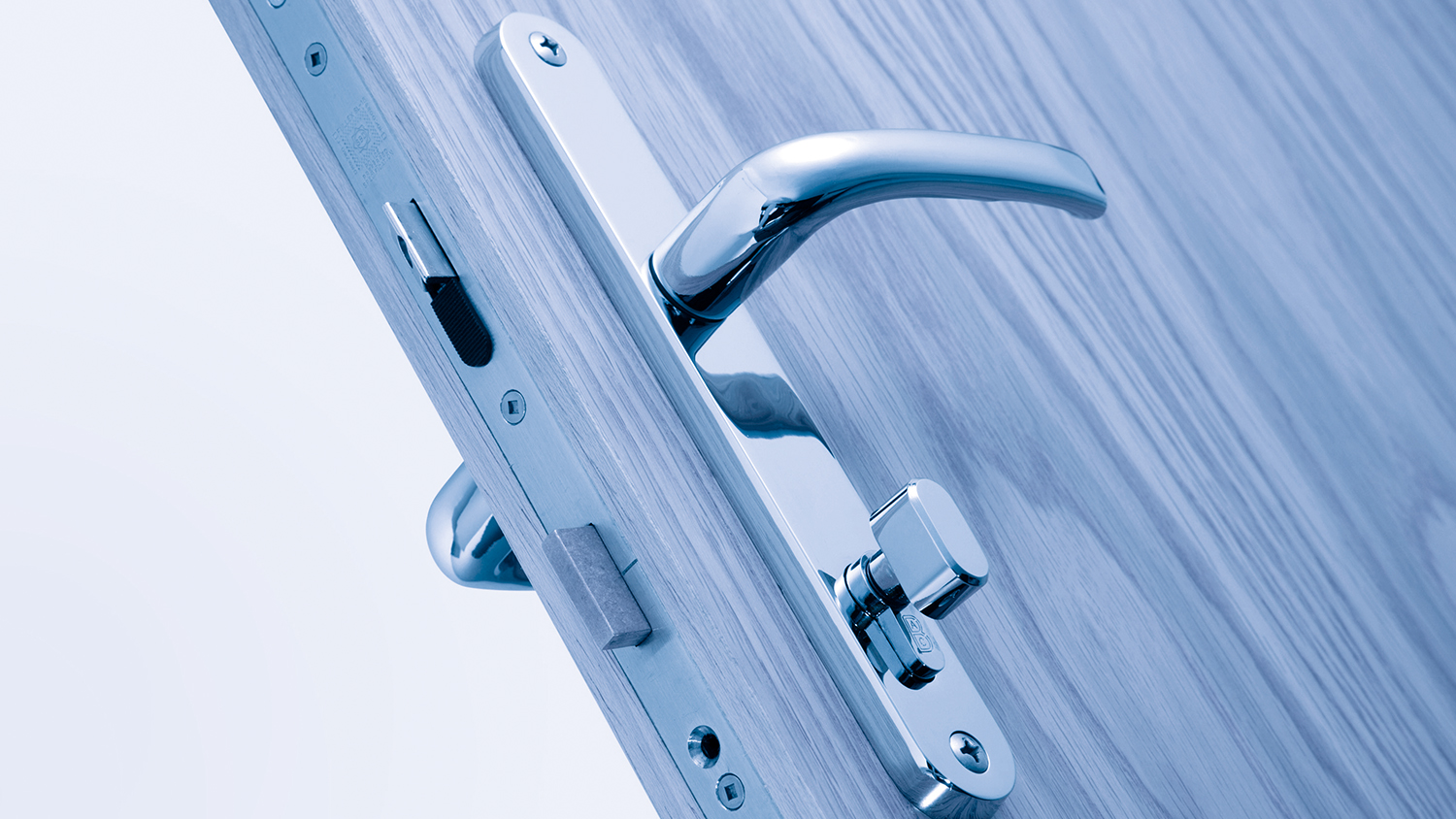
In this CPD, Jeld-Wen explains why testing, accessories, third-party accreditation, traceability and whole-life considerations play a critical role in selecting the right fire doorsets.
Fire doorsets are essential to a building’s fire safety strategy. But procuring them correctly means keeping pace with evolving regulations and changing industry attitudes.
Central to these shifts is the emphasis on long-term safety throughout the lifespan of a building, with legislation identifying key roles and responsibilities in the operation and maintenance phases. Meanwhile, cost remains a constant aspect of product specification and procurement.
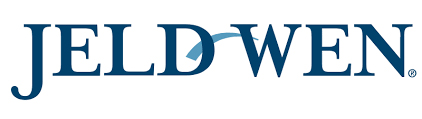
What you will learn in this CPD
- Which legislation and regulations affect doorsets
- How to test doorsets to current standards
- Why third-party accreditation is important
Here we examine the five key areas for improving long-term fire safety.
1. Testing to current standards – Understanding the testing landscape
There are many different situations in which fire doorsets can be used. Each application requires different performance characteristics, depending on the specific context of the individual building and its intended use. Relevant building regulations should therefore be the first port of call for checking the performance requirement. But how should that performance declaration be established?
For the Building Regulations in England, Appendix C of volumes 1 and 2 of Approved Document B deals exclusively with fire doorsets. It gives two routes by which fire doorset performance can be arrived at, plus a third that applies to lifts.
The first one is the national classification route and the second is the European classification route. As Approved Document B takes pains to point out, the two classifications do not necessarily equate and so performance determined under one route cannot be taken as a certain level of performance under the other route.
National classification route (BS)
This method involves testing to BS 476 part 22. It gauges a fire doorset’s fire integrity, while fire insulation performance, though less frequently mentioned, often emerges in commercial settings or by insurers’ demands. Following testing, fire doorsets are labelled with an FD (Fire Door) rating, indicating the achieved fire resistance duration, such as FD30 (30 minutes) or FD60 (60 minutes).
Terminology
Fire doorset
A door or shutter which, together with its frame and furniture as installed in a building, is intended (when closed) to resist the spread of fire and/or gaseous products of combustion and meets specified performance criteria to those ends.
Compartment (fire)
A building or part of a building, comprising one or more rooms, spaces or storeys, that is constructed to prevent the spread of fire to or from another part of the same building or an adjoining building.
European classification route (EN)
There are a series of important tests to be considered here. All fire doorsets should be classified in accordance with BS EN 13501-2, tested to the relevant European method from the following: BS EN 1634-1 and BS EN 1634-2 concern fire resistance while BS EN 1634-3 concerns smoke control.
In this system, the term ‘E’ represents integrity, indicating the duration of a product’s resilience during a fire test. Classifications are E30 (30 minutes), E60 (60 minutes), and so forth, with further letters added for other performance characteristics. For example, an E30 door will have been tested only for fire resistance for up to 30 minutes. These classifications are crucial in ensuring fire and smoke protection standards are met.
Consultation on national classification removal
In 2022, the UK government considered reforms to Approved Document B of the Building Regulations, suggesting a complete shift from the national to the European classification system, which already holds precedence. While this change may seem insignificant for products like fire doorsets that often undergo European testing, it presents potential challenges.
Many UK fire doorset manufacturers are prepping for this shift to EN (European Standards) testing, which might strain test laboratories and certification entities. The EN test, more demanding than its British counterpart, could need product adjustments to meet EN 1634 standards, potentially raising costs.
CE marking and UKCA marking
Presently, only external fire doorsets can carry the CE mark, excluding internal fire doorsets from both the CE and UKCA marks. However, related components, like hinges, must be CE/UKCA marked and rated for fire usage.
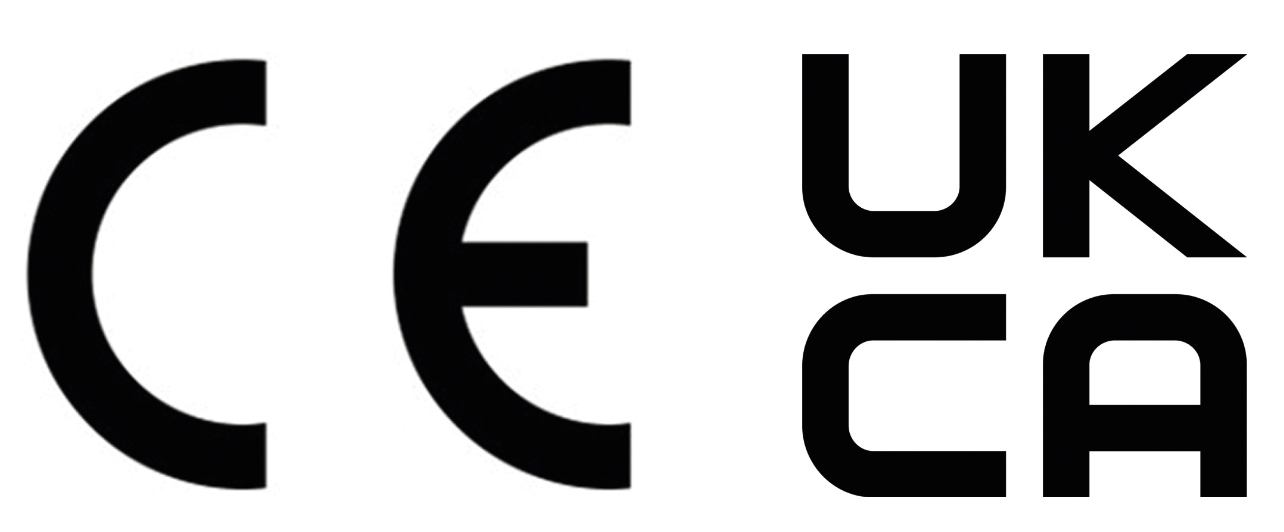
2. Correct components to form a fire doorset
A fire doorset is more than just the door leaf. Its performance depends on the door leaf being closed and the right hardware fitted. There are maximum allowable gaps between the door leaf, door frame and threshold. The gaps are needed for the doorset to operate in daily use but the correct distance also ensures components can function correctly when activated by heat.
The fire doorset relies on the correct hardware to be fitted in line with allowable limits as tested or specified in certificates. Hardware, in general, acts to ensure the door closes correctly and reliably and won’t contribute to the spread of fire. Different door constructions will have limitations on the hardware that can be fitted.
The anatomy of a fire doorset
A fire doorset’s effectiveness depends on its complete assembly, including the door leaf, frame and appropriate hardware. Specific allowable gaps ensure that components like intumescent function properly during a fire.
Key hardware components include:
- hinges
- seals
- handles
- glazing
- latches/locks
- letterplates
- drop seals
- overhead closers
Using a manufacturer-made and tested fire doorset streamlines the selection process, ensuring optimal compatibility and performance.
Fire doorset hardware and cost
While cost can tempt some when selecting hardware, it shouldn’t be the only determinant. Door leaves, with their varied materials, sizes and weights, require specific hardware. A mismatch can compromise an entire building’s fire safety strategy.
Moreover, smoke seals play a vital role in preventing lethal smoke transfer during fires. Proper installation and selection are vital for optimal protection.
3. Third-party accreditation
Third-party accreditation ensures that fire doorsets are:
- fit for purpose;
- compliant; and
- have been produced through a controlled and consistent process.
Third-party accreditation serves to comfort both specifiers and end users – whether tenants or owners. Beyond initial testing, it ensures that components and construction methods remain aligned with the original standards.
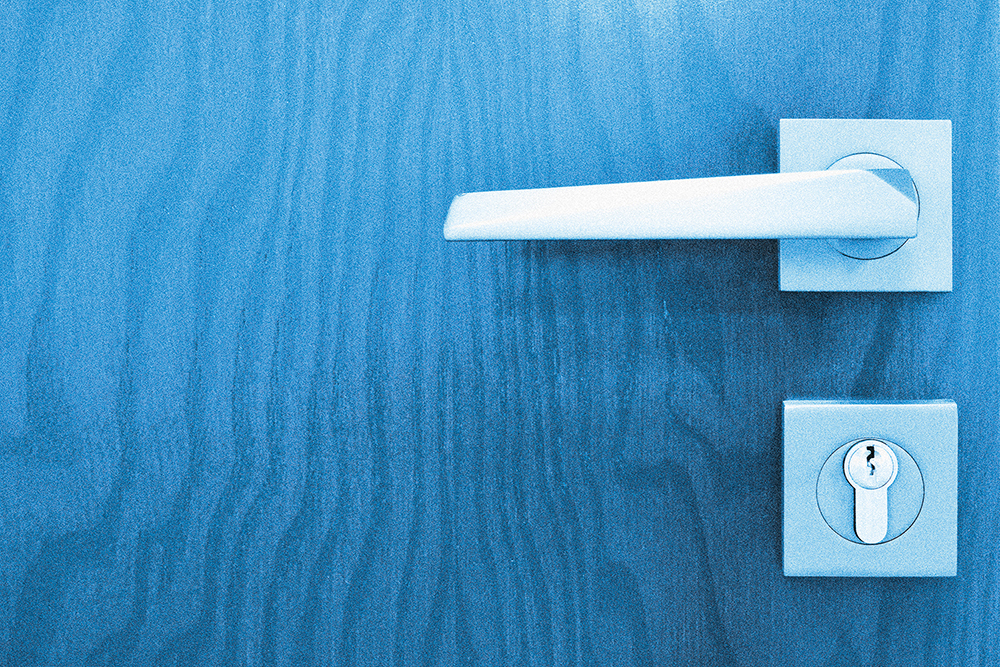
In addition, independent assessment confirms that fire doorsets are produced consistently, are compliant and fit their intended purpose. Accreditation schemes should be overseen by UKAS-registered organisations, ensuring they meet rigorous standards. As part of this, fire doorsets undergo testing at a UKAS-approved facility, following either the national or European classification routes.
What does third-party accreditation evaluate?
Third-party accreditation evaluates:
- factory processes and procedures;
- production consistency; and
- ongoing auditing.
Beyond testing the product, third-party schemes verify that the fire doorset manufacturer’s processes and procedures are consistently upheld. This ensures manufacturers can’t simply produce one compliant door for testing while distributing inferior products – every fire doorset from the facility must match the declared specifications.
Mandatory audits are integral to the process. They occur at timed intervals or after a number of units have been sold (depending on the certification scheme), ensuring no more than five years between checks.
Accreditation schemes spotlight
The British Woodworking Federation’s (BWF’s) Certifire scheme stands as a premier third-party accreditation for fire doorsets. Under this scheme any performance falling short of its declared rating requires investigation and rectification. Failing to address a performance that is even a minute less can jeopardise certification.
If a fire doorset’s resistance falls below 85% of its stated period, its certification is instantly put on hold. Furthermore, any design alteration triggers the need for retesting, ensuring the Certifire certification remains up to date. This encompasses both the components and the fire door’s construction methods.
Dual-purpose certification
Greater value can be had from working with a manufacturer that offers dual-purpose certification. These credentials not only attest to fire resistance but also other industry standards, such as PAS24 enhanced security. This reassures consumers that both fire and security aspects have undergone stringent evaluation.
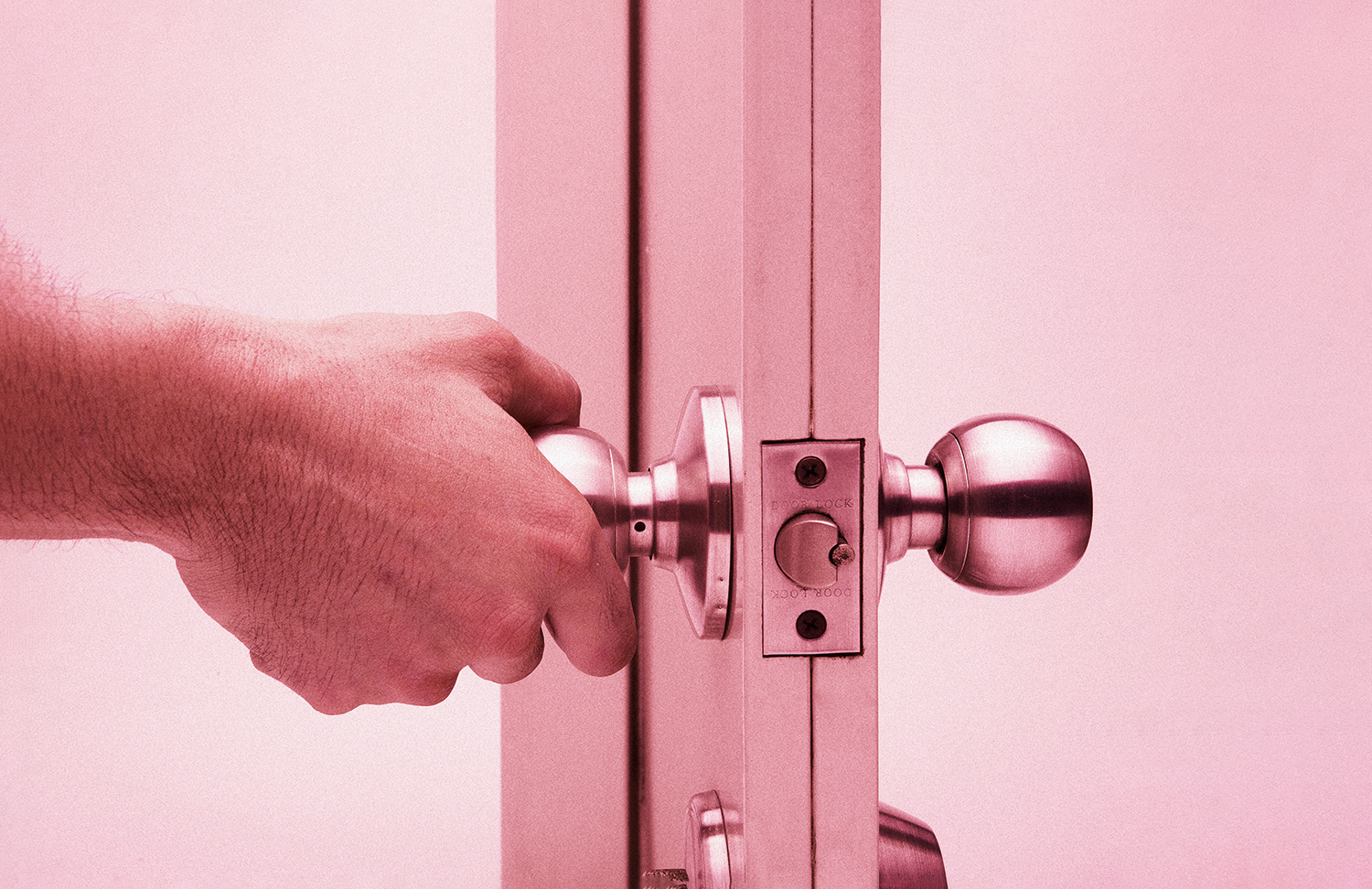
4. Product traceability
Currently, the requirement for a ‘golden thread’ of building safety information applies only to higher-risk buildings – that is, residential buildings exceeding 18m in height, or those that have at least seven storeys and at least two residential units. Care homes and hospitals meet the same height threshold during design and construction, but not during occupation. Over time, experts expect the range of buildings under this requirement will expand.
The golden thread:
- currently applies to higher-risk buildings;
- is expected to be expanded in scope over time; and
- records the original design intent and any changes made after.
The golden thread isn’t just about building safety – it’s about how information is stored in and used by digital tools and systems. It should record the original design intent and any changes. It ensures information availability at the right time and to the right people – including the newly created roles of dutyholders and accountable persons.
Responsibility for the golden thread transitions between the design and construction phase and the operation and management phase. Through these roles, the industry should witness a culture shift. Residents of higher-risk buildings should feel safer, and a ‘single source of truth’ for building safety-related information should emerge.
How can manufacturers support the golden thread?
As construction adapts to the golden thread, manufacturers are likely to introduce traceability initiatives, where products bear a unique code allowing the original product specification to be checked.
Fire doorsets are no exception. Engaging with manufacturers to learn about plans to implement ‘tag and track’ systems is crucial. Such features might not immediately impact work, but will assist installers and building managers later when making repair and maintenance decisions.
5. Whole-life considerations beyond manufacturing
Part of procurement involves assessing whether a product can be properly installed on site and determining its maintenance frequency to ensure consistent performance over its lifespan.
A manufacturer’s commitment to testing, accreditation and providing current information only matters if the fire doorset is installed correctly. Currently, no qualification exists for fire doorset installers – nor a requirement for one. This lack of standardisation means inconsistent training, potentially leading to errors even by competent installers.
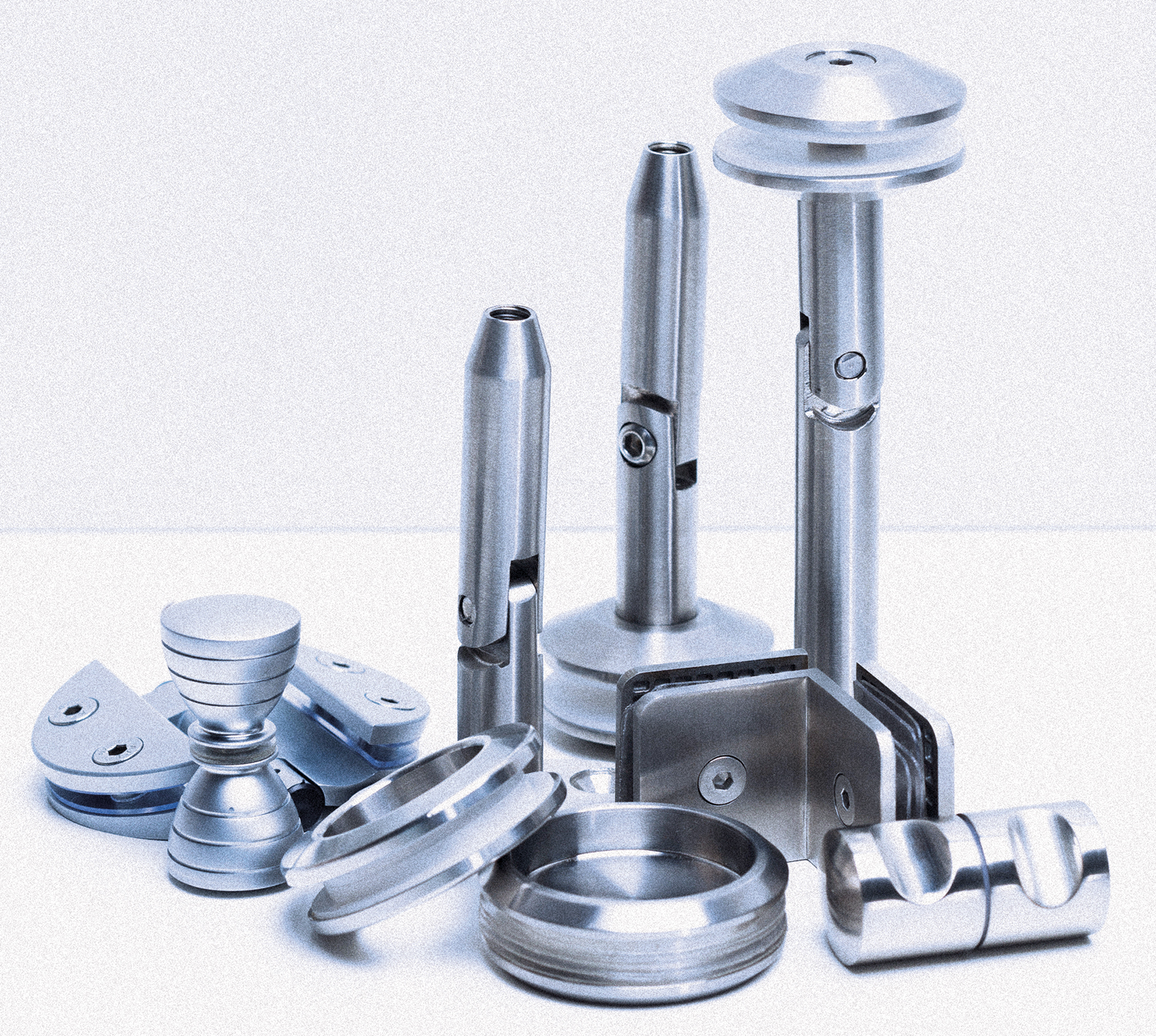
Reputable manufacturers offer installation guidance and are open to discussions should installers need further interpretation of standards.
All fire door fittings should adhere to BS 8214:2016. The key takeaway is that reputable manufacturers will not endorse any installation that doesn’t strictly follow their guidelines. Any deviation from these instructions jeopardises the fire safety strategy.
Common maintenance issues include damaged seals, excessive gaps, faulty hinges, damaged doors and propped-open fire doors.
The importance of understanding how even minor changes to a fire doorset can affect its fire-resistance capability cannot be understated. These include instances where doors have had modifications such as new paint coats or trimming to accommodate new flooring.
Though fire doorsets should be inspected at least every six months, there is no legal mandate to action any identified remedial requirements. Issues like damaged seals or large gaps between the door leaf and frame can be avoided by following the manufacturer’s guidelines. Damage due to vandalism or doors propped open for extended periods is not something manufacturers or contractors can control.
If manufacturers and contractors collaborate to provide better information to building managers and accountable persons, restoring fire doorset specifications to their original performance becomes feasible. Simple actions, like not propping door leaves open, make a significant difference.
Conclusion
The new building and fire legislation is enhancing fire safety standards in the industry. While roles such as ‘competent person’, ‘dutyholder’, and ‘accountable person’ are now clearer, success hinges on improved industry collaboration. Fire doorsets require the right framework of specification, installation, inspection and maintenance to function optimally.
There is still room for improvement in the standardisation of fire doorsets across the UK. Currently, there is no legal obligation for them to be third-party certified. But opting for fire doorsets with independent accreditation assures hardware specifications and consistent performance. Manufacturers offering product tagging further enhance project transparency.
While the industry awaits a UKAS-accredited certification scheme for fire doorset installers, buyers can safeguard their interests by sourcing fire door components from BWF-approved Fire Door Centres or firms listed in the BWF-Certifire Fire Door and Doorset Scheme Directory. Additionally, the BWF provides invaluable information and materials to facilitate installation, inspection and maintenance.
Useful references
GOV.UK Fire safety: Approved Document B
HSE.gov.uk New roles and responsibilities – Building safety
HSE.gov.uk Storing your building’s information – the golden thread